Have you spent a long time on failure analysis of circuit boards? Have you spent a lot of energy on sample debugging? Have you ever doubted your original correct design?
Perhaps many hardware engineers have had similar psychological conversations. Data shows that 78% of hardware failures are caused by poor welding and incorrect material placement. This causes engineers to spend a lot of time and energy on sample debugging and analysis, delaying the project progress. If the cause of the failure cannot be found for a while, the engineer will doubt his original correct design, causing himself to go astray in the incorrect direction of thinking. When actually debugging the hardware, engineers often consider many profound potential causes, but are reluctant to doubt whether the welding is reliable enough, but often "the safest place is the most dangerous place." Engineers will habitually think that something as simple as welding will not cause many seemingly complex problems. Once such a problem occurs, they will also habitually consider the robustness of the software and the rationality of the hardware circuit design. For example,
Case 1: Due to a poor solder joint in a certain signal of the DDR high-speed signal part, the system seemed to work normally when transmitting a small amount of data. However, when performing a burst operation with a large amount of data, such as playing a high-definition movie or loading an operating system, errors would often be reported. This was often mistakenly believed to be a software problem, and the software engineer spent a long time checking the code to no avail.
Case 2: Due to improper time and temperature control during welding, the plastic structure inside connectors such as LCD and USB melted and deformed due to high temperature, causing a certain signal to be accidentally disconnected, resulting in no LCD display and no USB communication, which was mistakenly believed to be a software driver problem.
Case 3: There are a lot of decoupling capacitors densely distributed next to the CPU power supply . Due to the excess solder during the welding process, one of the capacitors short-circuited, resulting in the hardware engineer spending a lot of time to check the cause of the short circuit one by one.
Case 4: High-speed signal interface connector. Due to a signal solder joint failure, the system can work at a lower bus frequency. Once the bus speed is increased, the system immediately reports an error. The cause of this problem is basically difficult to locate.
Case 5: Due to poor welding of the inductor , the PWM dimming function of the LED failed. Engineers spent a lot of time to confirm whether it was a software or hardware problem.
Welding, seemingly simple, is also made up of many work details and steps, and these links are closely linked to each other. Any mistake in any link will lead to the final problem. The China Southern Electronics Industry Association, in collaboration with Massembly Technology, established a service organization specializing in sample patch welding in Shenzhen Nanshan High-tech Park, aiming to provide effective and reliable sample patch services for the majority of R&D electronic technology companies, and improve the speed of R&D and product launch. It has creatively added its own 3Q quality inspection links in the overall patch workflow, such as material selection, marking, printing, patch, and furnace passing, which effectively reduces the possibility of hardware failure.
Therefore, during the hardware debugging process, it is recommended that engineers first observe the welding quality of your prototype: 1. Is the material correct? 2. Is the pin position correct? 3. Is there any solder joint, empty solder joint, or cold solder joint? 4. Is the solder paste full and reflective after passing through the furnace? 5. Is the PCB board browned? 6. Does the structural part of the connector melt under high temperature? 7. Does the chip position correspond to the silk screen?
After checking the “simple” items above, focus your energy on those “advanced” issues!
Previous article:Briefly describe the design and implementation of remote power safety measurement and control system
Next article:Design of AVR microcontroller timer-counter based on PWM function
Recommended ReadingLatest update time:2024-11-16 22:37
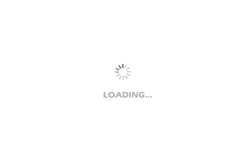
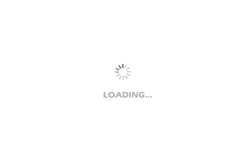
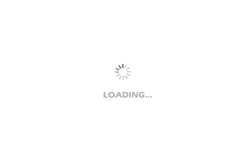
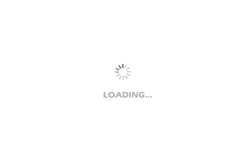
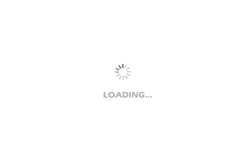
- MathWorks and NXP Collaborate to Launch Model-Based Design Toolbox for Battery Management Systems
- STMicroelectronics' advanced galvanically isolated gate driver STGAP3S provides flexible protection for IGBTs and SiC MOSFETs
- New diaphragm-free solid-state lithium battery technology is launched: the distance between the positive and negative electrodes is less than 0.000001 meters
- [“Source” Observe the Autumn Series] Application and testing of the next generation of semiconductor gallium oxide device photodetectors
- 采用自主设计封装,绝缘电阻显著提高!ROHM开发出更高电压xEV系统的SiC肖特基势垒二极管
- Will GaN replace SiC? PI's disruptive 1700V InnoMux2 is here to demonstrate
- From Isolation to the Third and a Half Generation: Understanding Naxinwei's Gate Driver IC in One Article
- The appeal of 48 V technology: importance, benefits and key factors in system-level applications
- Important breakthrough in recycling of used lithium-ion batteries
- Innolux's intelligent steer-by-wire solution makes cars smarter and safer
- 8051 MCU - Parity Check
- How to efficiently balance the sensitivity of tactile sensing interfaces
- What should I do if the servo motor shakes? What causes the servo motor to shake quickly?
- 【Brushless Motor】Analysis of three-phase BLDC motor and sharing of two popular development boards
- Midea Industrial Technology's subsidiaries Clou Electronics and Hekang New Energy jointly appeared at the Munich Battery Energy Storage Exhibition and Solar Energy Exhibition
- Guoxin Sichen | Application of ferroelectric memory PB85RS2MC in power battery management, with a capacity of 2M
- Analysis of common faults of frequency converter
- In a head-on competition with Qualcomm, what kind of cockpit products has Intel come up with?
- Dalian Rongke's all-vanadium liquid flow battery energy storage equipment industrialization project has entered the sprint stage before production
- Allegro MicroSystems Introduces Advanced Magnetic and Inductive Position Sensing Solutions at Electronica 2024
- Car key in the left hand, liveness detection radar in the right hand, UWB is imperative for cars!
- After a decade of rapid development, domestic CIS has entered the market
- Aegis Dagger Battery + Thor EM-i Super Hybrid, Geely New Energy has thrown out two "king bombs"
- A brief discussion on functional safety - fault, error, and failure
- In the smart car 2.0 cycle, these core industry chains are facing major opportunities!
- The United States and Japan are developing new batteries. CATL faces challenges? How should China's new energy battery industry respond?
- Murata launches high-precision 6-axis inertial sensor for automobiles
- Ford patents pre-charge alarm to help save costs and respond to emergencies
- New real-time microcontroller system from Texas Instruments enables smarter processing in automotive and industrial applications
- Analysis of the role of terminal resistance in CAN bus
- Download the information and watch the video to win a prize | Tektronix HDMI 2.1 test solution is now available for download, and you can also watch the supporting video
- Things to note when using C/C++ to write programs based on TMS320 series DSP
- Generate sine wave data using microcontroller DAC and C language
- RISC-V RVB2601 First Experience--Section 4--Sensor Module Interface
- Easy to use, LiChuang EDA. Haha!
- [Start at 10:30] Interpretation of TI's latest smart lock, visual doorbell, and network camera solutions, and recommendations for its core components
- C6678 multi-core DSP development - connected domain marking of vlib application
- Nanjing MIIT certified enterprise [urgently hiring IC engineers with high salary]
- CCS 6 New TMS320F2812 Project