1 Introduction
Power adapters are power supply conversion devices for small portable electronic devices and electronic appliances. With the rapid increase in the number of users of portable devices such as cellular phones and laptops, low-voltage and low-power power adapters are becoming more and more widely used. Researchers and businesses continue to launch power supply design solutions and products with lower costs, smaller size, lighter weight and higher efficiency [1]. In order to further improve the performance of the power supply, the ON Semiconductor full current mode controller NCP1014 is used, and the flyback transformer is designed using the critical current method based on the characteristics of the continuous and discontinuous working modes of the flyback transformer, maximizing the performance of the transformer in both modes. The designed 5W constant current constant voltage (CCCV) power supply system has the advantages of dynamic self-power supply, fault self-detection, no audio noise in intermittent mode, high-efficiency operation in wide voltage mode, and low cost. The power supply system is simulated using OrCAD/PSpice 10.5, and relevant settings are made for the non-convergence of the system transient analysis [2]. The simulation results are consistent with the results of actual measurement and theoretical analysis.
2 Analysis of 5W CCCV power adapter circuit based on NCP1014
2.1 5W CCCV power system circuit diagram
The NCP101X series is a fixed frequency (65khz -100khz -130khz) current mode controller produced by ON Semiconductor. It has a built-in 700V MOSFET and uses PDIP-7 or SOT-223 packages. It has the advantages of soft start, cycle skipping, dynamic self-supply, etc., and can provide everything needed for low-cost power supply. This article uses NCP1014ST100T3 (four-pin, fixed output frequency 100khz) [3], and the simulation model can be obtained from the ON Semiconductor website. The rectifier module uses D2SB60, the flyback transformer uses the system's own XFRM_LINER to replace the flyback transformer, the optocoupler uses PS2501, and the voltage regulator diode uses D1N5229. A 5W CCCV power supply system is established in PSPICE 10.5. The circuit diagram is shown in Figure 1.
Figure 1 5W CCCV power system circuit diagram
2.2 Working Principle
The effective value range of the input AC voltage is (100~250) VAC. After being rectified by D1 and filtered by the filter composed of C1-A, C1-B, and L1, it becomes a DC voltage. R1 is a resistor to limit the surge current. After the DC voltage is chopped by the built-in MOSFET of NCP1014 and transformed by the flyback transformer, a high-frequency rectangular wave voltage is obtained at the secondary side. Finally, it is rectified, filtered, and stabilized by D3, C4, and D4 on the secondary side to obtain the required DC voltage at the output end [4]. The DC output voltage is fed back to the FB pin of NCP1014 through the sampling circuit and the optocoupler PS2501. The controller automatically adjusts the output pulse so that the power system is in an efficient and stable mode in all states [5].
When the power supply starts, NCP1014 charges the C4 capacitor through the built-in bias current source. Once VC4 reaches VCCoff (typical value 8.5V), the current source is turned off, and the pulse is transmitted through the output stage to activate the built-in MOSFET. When the voltage of C4 drops to VCCon (typical value 7.5V), the internal current source is activated and the voltage is pulled up to 8.5V. Under normal conditions, the voltage VCC fluctuates between 7.5V and 8.5V, and the typical value of C4 is 10μF.
When the detection circuit detects a light load, the NCP1014 automatically adjusts the output pulse and skips unnecessary conversion cycles, which greatly reduces the power consumption under light load.
When a circuit fault occurs (such as the optocoupler is short-circuited or damaged), the circuit will enter fault mode, NCP1014 will stop outputting pulses, and the voltage VCC will remain between 4.7V and 8.5V until the circuit returns to normal and the circuit attempts a new startup.
2.3 Flyback Transformer Design
The flyback switching power supply transformer has two working modes: incomplete energy transfer and complete energy transfer. Large changes in the input grid voltage or output current will inevitably cause the transformer to cross the continuous and discontinuous working states. Therefore, when designing a transformer, the key is to make it work efficiently and stably in both states [6,7,8]. In this paper, the critical current state method is used to design the flyback transformer so that it has good performance in both states.
Figure 2 Primary and secondary current waveforms of a current continuous mode transformer: (a) primary current waveform; (b) secondary current waveform
In the figure, Irp and Irs are the primary and secondary pulsating currents, Ipp and Ips are the primary and secondary peak currents, and Ton and Toff* are the on and off times of the switch tube. Formula (1) is satisfied in the continuous and critical states.
Ton + Toff*=1 Formula (1)
When the loss is not considered, the transformer always satisfies equation (2).
Us∙Is =Iavg∙Udc Formula (2)
Assuming that the output power remains unchanged, the primary voltage Udc increases, the primary average current Iavg will decrease, and Irp and Ipp will also decrease accordingly. When Irp just reaches zero, the transformer enters the critical mode. When Udc continues to increase, the circuit enters the discontinuous state, and Ton and Toff* satisfy equation (3).
Ton + Toff*<1 Formula (3)
Based on the above discussion, the transformer can be designed so that it reaches a critical state at a specific voltage. Below this voltage, the transformer enters a continuous mode, and above this voltage, the transformer enters a discontinuous state. In this way, the performance of the transformer in both modes can be maximized[9].
The transformer in this article should meet the following parameters: AC input voltage Uin = (100~250) VAC or Udc = (140~350) VDC, efficiency η = 0.80, output voltage Uo = 5.1V, output current Io = 1A, operating frequency Fsw = 100kHz, maximum duty cycle Dmax = 0.4, transformer secondary voltage Us = Uo + Uf = 9V, Uf is the secondary voltage drop, and the secondary side voltage is set to reach the critical state at 200V, that is, the secondary side calculated current Is = 0.7A.
The structural parameters of the transformer are designed as follows.
(1) The transformer core is designed using the following relationship: Wa∙Ae=Po∙104/K∙J∙B∙F≈0.045cm4. Where: K is the window utilization factor, which is 0.3 for the flyback transformer;
J is the current density, which is 300A/cm2;
B is the operating magnetic induction intensity, which is 0.22T;
F is the operating frequency, which is 100kHz.
The E_16_8_5 core is selected: Wa∙Ae=726mm4, Ae=19.3mm2, effective magnetic path length MPL=37.6mm, and magnetic permeability μ=2300.
(2) Transformer turns ratio: N = (Udc∙Dmax)/[Us∙(1-Dmax)] ≈10.
(3) Transformer primary and secondary inductance [9]: Ips = 2∙ Is / (1-Dmax) ≈ 2.3A, Ls = Us∙ (1-Dmax)∙ T/Ips ≈ 23.48μH, Lp ≈ 2.348mH
(4) Number of primary and secondary turns of transformer: Np = 134, Ns ≈ 13.
(5) Air gap length: Lg = (0.4∙π∙N p2 ∙Ae∙10-8/Lp)-MPL/μ≈0.015cm, where Ae unit: cm2; MPL unit: cm.
3 Power System Simulation
Before simulation, the following settings are made to achieve better system convergence [10]:
Figure 3 Simulation convergence settings
The simulation time is set to 60ms, the transformer primary inductance Lp=2.34mH, the secondary inductance Ls=0.0234mH, and the coupling coefficient COUPLING=0.99. Figure 4 shows the comparison between the measured MOSFET drain waveform and the simulated waveform under 120VAC and 75% load. Figure 5 shows the VCC voltage and load voltage and current waveforms under 220VAC and 80% load. Figure 6 shows the scanning waveform of the primary current of the transformer under the three states of discontinuous, critical, and continuous. The simulated waveform is consistent with the theoretical analysis and the measured waveform. I believe that as the model accuracy becomes higher and higher, the simulation results will become more and more accurate.
Figure 4 MOSFET drain waveform at 120VAC 75% load: (a) measured waveform; (b) simulated waveform
Figure 5 VCC voltage and load voltage and current waveforms under 80% load Figure 6 Secondary current graphs of transformer in three states
4 Conclusion
The self-contained monolithic converter NCP1014 can realize the efficient and stable operation of the power supply system. The 5W CCCV power adapter designed by the critical current method meets the design requirements. The flyback transformer has stable performance in two modes. Under normal operation, the load voltage ripple is less than 0.05V, the current ripple is less than 0.015A, and the efficiency is more than 80%, which can provide a reference for the design of low-cost power adapters. The power supply system was simulated using OrCAD/PSpice 10.5, and settings were made for the non-convergence of transient analysis. The simulation results are consistent with the theoretical values and measured values, providing a good basis for the design of the power supply system. OrCAD/PSpice can be applied to the design of power supplies.
References
[1] Cao Fengwen, Deng Yan, He Xiangning. Design and research of low voltage and low power power adapter [J]. Television Technology, 2001, 6: 55-59.
[2] Wang Fuchun, Liu Mingshan, Chi Haitao, et al. Learning OrCAD from Examples[M]. Beijing: Machinery Industry Press, 2006.
[3] NCP1014 Data Sheet [M]. Wuhan Information Technology Co., Ltd. Wuhan: 2006.
[4] Wu Guoping, Yang Rengang, Du Haijiang. Research on the design of a flyback switching power supply based on NCP1014[J]. Power Electronics Technology, 2010, 44(1):78-80.
[5] Xi Hui, Ma Lihua. Design of switching power supply based on NCP1014 chip[J]. Journal of Shanghai Institute of Technology, 2007, 7(2): 91-93
[6] Xu Qiang, Dong Wei, Tian Junjie, et al. Design of flyback switching power supply transformer [J]. China Testing, 2009, 35(3): 74-77.
[7] Lenk, J.; Wang Zhengshi, Zhang Junming, translators. Practical Switching Power Supply Design[M]. Beijing: Posts and Telecommunications Press, 2006.4.
[8] Chen Yongzhen, Meng Linan. Design and production of high efficiency switching power supply[M]. Beijing: China Electric Power Press, 2008.
[9] Jin Wenhui, Fan Panguo, Yan Shaoxiong, et al. Research on an improved design method for a flyback switching power supply transformer [J]. Power Electronics Technology, 2009, 43(1): 62-63.
[10] Wang Fuchun. Electronic Circuit CAD and OrCAD Tutorial[M]. Beijing: Machinery Industry Press, 2004.7.
About the Author
Gao Faliang (1984-), male, from Linyi, Shandong, master's degree candidate, research direction: high-efficiency power conversion
Previous article:NXPTEA1713150W All-in-one PC Adapter Solution
Next article:High-accuracy frequency measurement system
Recommended ReadingLatest update time:2024-11-16 15:34
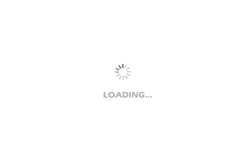
- Popular Resources
- Popular amplifiers
- MathWorks and NXP Collaborate to Launch Model-Based Design Toolbox for Battery Management Systems
- STMicroelectronics' advanced galvanically isolated gate driver STGAP3S provides flexible protection for IGBTs and SiC MOSFETs
- New diaphragm-free solid-state lithium battery technology is launched: the distance between the positive and negative electrodes is less than 0.000001 meters
- [“Source” Observe the Autumn Series] Application and testing of the next generation of semiconductor gallium oxide device photodetectors
- 采用自主设计封装,绝缘电阻显著提高!ROHM开发出更高电压xEV系统的SiC肖特基势垒二极管
- Will GaN replace SiC? PI's disruptive 1700V InnoMux2 is here to demonstrate
- From Isolation to the Third and a Half Generation: Understanding Naxinwei's Gate Driver IC in One Article
- The appeal of 48 V technology: importance, benefits and key factors in system-level applications
- Important breakthrough in recycling of used lithium-ion batteries
- Innolux's intelligent steer-by-wire solution makes cars smarter and safer
- 8051 MCU - Parity Check
- How to efficiently balance the sensitivity of tactile sensing interfaces
- What should I do if the servo motor shakes? What causes the servo motor to shake quickly?
- 【Brushless Motor】Analysis of three-phase BLDC motor and sharing of two popular development boards
- Midea Industrial Technology's subsidiaries Clou Electronics and Hekang New Energy jointly appeared at the Munich Battery Energy Storage Exhibition and Solar Energy Exhibition
- Guoxin Sichen | Application of ferroelectric memory PB85RS2MC in power battery management, with a capacity of 2M
- Analysis of common faults of frequency converter
- In a head-on competition with Qualcomm, what kind of cockpit products has Intel come up with?
- Dalian Rongke's all-vanadium liquid flow battery energy storage equipment industrialization project has entered the sprint stage before production
- Allegro MicroSystems Introduces Advanced Magnetic and Inductive Position Sensing Solutions at Electronica 2024
- Car key in the left hand, liveness detection radar in the right hand, UWB is imperative for cars!
- After a decade of rapid development, domestic CIS has entered the market
- Aegis Dagger Battery + Thor EM-i Super Hybrid, Geely New Energy has thrown out two "king bombs"
- A brief discussion on functional safety - fault, error, and failure
- In the smart car 2.0 cycle, these core industry chains are facing major opportunities!
- The United States and Japan are developing new batteries. CATL faces challenges? How should China's new energy battery industry respond?
- Murata launches high-precision 6-axis inertial sensor for automobiles
- Ford patents pre-charge alarm to help save costs and respond to emergencies
- New real-time microcontroller system from Texas Instruments enables smarter processing in automotive and industrial applications
- EEWORLD University Hall----Live Replay: CAN SIC signal improvement function
- TMS570 learning 2-bootload jump experiment
- Playing with Zynq Serial 2——GPIO peripherals of Zynq PS
- Ask the big guy, about the problem of DS1302
- EEWORLD University Hall----Application of IoT sensing technology
- [micropython] STM32 branch improves support for wiznet5k
- MSP430 MCU Development Record (18)
- Oscilloscope probe compensation principle - explain the fundamental reason for oscilloscope probe compensation calibration
- About c0_init_calib_complete of ddr4
- MSP430F5529 generates PWM waves with CCS