The mobile phone batteries required by today's technology must not only be able to provide a stable power supply for a long time,
In addition, small size and light weight are also key. How can we reduce the circuit board area, increase the power supply time and reduce the cost at the same time? Integrating many power management components on a single chip will be the best way to solve the problem.Early mobile phones were either bulky or had to be bound by car batteries, but after a long period of development, today's mobile phones have become very light and can do many things besides calling functions. The new 3.xG smartphones combine traditional 2G mobile phones with many other functions, including PDAs , digital cameras, music players ( MP3 ) and global positioning systems ( GPS ). Such a variety of functions requires many parts, most of which have different power supply voltages and increasing current requirements, making them require more power. (Figure 1) is an estimated value of the increase in power requirements after upgrading from 2G voice phones to 3G video phones.
Figure 1 Power consumption
At the same time, consumers want more compact phones. This article introduces two power management systems that can help smartphone designers balance conflicting goals, such as minimizing packaging while supporting greater power requirements; achieving optimal efficiency to maximize battery life; and reducing power supply noise and ripple to acceptable levels to support the next generation of mobile phones. Battery Selection
Selecting
a rechargeable battery is one of the first tasks in power management system design, and nickel-metal hydride batteries and lithium-ion batteries are currently the only two practical choices. The unit volume storage capacity of lithium-ion batteries is 270 to 300Wh/l, and the unit weight storage capacity is 110 to 130Wh/kg, both higher than the 220 to 300Wh/l and 75 to 100Wh/kg of nickel-metal hydride batteries. Therefore, at the same storage capacity, the volume and weight of lithium-ion batteries are smaller than nickel-metal hydride batteries. In addition, the 3.6V operating voltage of lithium-ion batteries is also higher than the 1.2V of nickel-metal hydride batteries. Most of the power consumption of mobile phones comes from 1.2V and 3.3V power supplies. To maximize the efficiency of switching power converters, the more effective method is usually to convert from high voltage to low voltage rather than from low voltage to high voltage, so lithium-ion batteries are the best choice.
To maximize the use time of rechargeable batteries, proper battery management and control are particularly important. Battery management includes three parts: charging control, battery monitoring and battery protection. From linear controllers using external pass elements to switching controllers with built-in switching elements and higher efficiency, charging control components have made great progress. Battery chargers must handle currents in the range of 500mA to 1500mA to provide fast charging cycle times. Battery monitoring and protection components are usually packaged with the battery. Battery monitoring components can be simple "charge meters" (coulomb counters) that are responsible for calculating the remaining battery power by the central processor, or they can be battery power measurement components (gas gauges) with built-in microcontrollers. It directly provides information such as remaining power, remaining power time, battery voltage, temperature, and average current measurements through a simple interface between the DSP and the processor.
Power Topology
Next, the design engineer must decide on the type of power conversion component. It may be an inductor-based switching power converter with built-in FET switches, an inductor-free switching power converter (charge pump), or a linear regulator. Each of these converters has its own advantages. In terms of efficiency, inductor-based converters have the highest overall efficiency, followed by charge pumps, and finally linear regulators. Cost is usually inversely proportional to efficiency, so linear regulators are the lowest cost, followed by charge pumps, and finally inductor-based converters. Linear regulators have no output ripple, charge pumps have some output ripple, and switching regulators have the highest output ripple among the three. In terms of the volume of the entire solution, linear regulators are the smallest and usually only require input and output capacitors. Charge pumps require one or two "flying" capacitors in addition to input and output capacitors, and switching regulators require inductors, so their package volumes vary greatly.
2G phones offer almost no functional integration, whether it is digital components such as DSPs or analog-to-digital converters, or analog components such as power management systems. When developing power management systems, system designers usually prioritize cost and volume rather than conversion efficiency. Linear regulators can only convert input voltages to lower output voltages, so the battery voltage must be higher than 3.3V. At this time, low-current or medium-current linear regulators can be used for voltage conversion to provide power to other power requirements in the 2.8V range. In 3G chipsets, baseband processors now include DSPs, microprocessors/microcontrollers, analog-to-digital converters, and digital-to-analog converters to control RF signals and audio signal processing. The core voltage of the processor has dropped to 1.2V or lower, and the I/O and peripheral voltages have also begun to decrease to the 2.5V to 3.0V range. Since the current requirements of 3.xG phones are generally higher than those of 2.G phones, 3.xG designers need DC power converters that are more efficient than linear regulators to provide longer battery life. To further extend battery life, many designers must use the power of the lithium-ion battery until its voltage drops to a minimum; in this process, how to generate 3.3V becomes a challenge. On the surface, if designers can continue to use the battery to 2.7V and use a positive supply buck-boost converter or SEPIC converter to provide 3.3V, the battery life of the portable device will be greatly extended. However, a simple analysis of a 600mAh battery (Table 1) shows that this is not the case, because there is almost no difference in the power supply time between using a more efficient buck converter and using the battery to 3.3V or using a converter such as SEPIC and completely draining the battery.
Table 1 60mAh battery analysis
In addition, whether it is a SEPIC
converter
using two inductors
or some newer positive supply buck-boost converters that are more efficient, they are more expensive. Therefore, when making an overall evaluation, it is more efficient and may be a more attractive option to use only battery power above 3.3V and then use a high-efficiency switching power converter to provide 3.3V power. The discrete solution introduced below uses a buck converter to provide 3.3V power, while the integrated solution uses a SEPIC converter.
System Overview
Different smartphone components have different power requirements. (Figure 2) is a simple block diagram of the main components that require power in a mobile phone. For example, the voltage-controlled oscillator (VCO) and phase-locked loop (PLL) of the RF unit require extremely low noise and high power rejection ratio power to ensure that they provide the highest transmission and reception performance. Therefore, although the efficiency of linear regulators is not high, they are the best choice for this type of power supply because they have no output ripple; it is also important to keep the switching frequency of the DC converter and their second-order and third-order harmonics outside the intermediate frequency band. As the core voltage of DSP and CPU has dropped to about 1V, the high-efficiency switching buck converter based on inductor is an ideal choice. As for the white light diode used in screen backlighting, its power supply can come from charge pump or inductive boost/buck converter.
Figure 2 Smartphone power supply block diagram
Dynamic Voltage Scaling
As shown in Figure 1, the two components with the highest power requirements are in the RF unit, namely the transmitter's power amplifier and baseband processor. Depending on the distance between the phone and the base station, the power amplifier consumes up to 75% of the total power during a call and only 30% in standby mode. Older GSM phone transmitters that use nonlinear power amplifiers typically operate at about 50% efficiency, but newer standards such as WCDMA require both amplitude and phase modulation, which can only be provided by linear amplifiers with an efficiency of between 25% and 35%. In addition, the normal baseband processor load requirements of CDMA2000 1x phones are in the 60 to 120mA range, so it is extremely important to provide the most efficient power to the power amplifier and processor.
Dynamic/Adaptive Voltage Scaling (DVS/AVS) is similar to the method used by highly integrated components. It connects the processor and regulator in a closed-loop system and dynamically adjusts the output voltage of the digital power supply to the minimum value while ensuring normal system operation. The power amplifier will be optimized to have the highest efficiency at the maximum transmission power. Since most mobile phones work near the base station, the radio function of the mobile phone will reduce the transmission power to the lowest level while maintaining the communication quality. When the power amplifier works at a lower power level, its efficiency will be affected. As can be seen from (Figure 3), using dynamic voltage adjustment technology to adjust the voltage of the power amplifier, its working efficiency will increase by 10% to 20%.
Figure 3 Power amplifier efficiency
The power consumption of digital processors is proportional to the square of the voltage, so the CPU can also use dynamic voltage adjustment technology; when the CPU enters standby mode or other function-reduced mode, it can work at a lower frequency. At this time, the processor voltage can be reduced to reduce power consumption, improve work efficiency, and extend battery life. Take OMAP1510 as an example. Assuming that its power supply is supplied by TPS62200 and uses a 1 ampere-hour 3.6V lithium-ion battery input, other features include: ● Sleep mode (TPS62200 uses PFM modulation) without dynamic voltage adjustment: Vout = 1.5 V @ 300 µA; efficiency = 93% ● Normal working mode (TPS62200 uses PWM modulation): Vout = 1.5 V @ 100 mA; efficiency = 96%
Assuming that this component is in sleep mode 95% of the time and in normal working mode 5% of the time, it can be seen from the relationship between output power and time that using dynamic voltage adjustment technology in sleep mode can extend battery life by up to 9 hours.
The discrete solution
(Figure 4) is a power management system implemented using discrete components, with the battery voltage limited to 3.3V.
Figure 4: Power management system implemented using discrete components
In this solution, the high-efficiency TPS62200 buck converter operating in 100% duty cycle mode can still provide 3.3V I/O voltage even if the lithium-ion battery drops to about 3.3V. All of the above parts are packaged in SOT-23 packages, except for the bq24020 battery charger component, TPS61020 boost converter, and TPS61042 white light diode driver component, which are packaged in 3×3 square centimeters QFN package. TPS61040 and TPS61042 also have built-in top FET transistors, and only one external diode is required for each component. The bq24020, TPS622xx, TPS61020 and linear regulator components all have built-in FET transistors, and the dynamic voltage adjustment technology used in the power amplifier and CPU power supply can improve the efficiency of each component, thereby helping to reduce power consumption.
Integrated Solutions
The latest process technology makes it easier for engineers to combine, quickly modify and/or utilize existing discrete component designs to provide semiconductor chips with different levels of integration. For example, general-purpose dual-channel switching converters and dual-channel linear regulators with high power rejection ratio and low noise, power supplies for special-application white light diodes, and multi-power management solutions for mobile phones, PDAs and digital cameras are now available. Power components specifically supporting terminal equipment will have built-in peripherals ranging from ringers and buzzers for mobile phones to general-purpose I/O pins for PDAs, such as the TPS65010 used in the integrated solution in Figure 4.
Figure 5 Integrated solution
In this solution, the 3.3VI/O power is provided by a SEPIC converter, which allows the application system to fully utilize the power of the lithium-ion battery until the battery voltage drops to a minimum level (about 2.7V). Like the discrete solution, the regulator output also comes from the 3.3V input power supply to improve operating efficiency. The TPS65010 uses a 48-pin QFN package, and these components all have built-in FET transistors. The TPS61130 SEPIC converter uses a 4×4 square cm QFN package and has built-in FET transistors, with an efficiency of up to 90%, and the TPS5100 is a three-channel output controller specifically used to provide power to the display. The dynamic voltage adjustment technology used in the power amplifier and CPU power supply can improve the efficiency of each component, thereby helping to reduce power consumption.
Discrete or integrated?
How to choose between discrete or integrated solutions? Generally speaking, the cost of integrated components is lower than that of multiple discrete parts of the same level. In addition, as shown in the circuit board layout of (Figure 6), the TPS65010 and its matching passive components require less circuit board space than multiple discrete parts that perform the same function, mainly because additional space is required between discrete parts to accommodate signal lines. Since the TPS65010 also includes other functions originally provided by discrete parts, such as power supply sequencing, oscillators, and diode driver components, the integrated solution can save more circuit board area.
Figure 6. PCB layout comparison between TPS65010 and discrete solutions of the same level
Integrated devices used to support special applications and were not very flexible, so they could not be significantly changed later in the design process. However, new process technologies, including integrated EEPROM that supports programmable output voltage and post-package adjustment, allow engineers to repeat simple modifications to existing devices (that is, devices with different fixed output voltages) more easily and quickly at a lower cost. On the other hand, there is usually only one supplier of integrated devices, which may force manufacturers to use discrete solutions.
Future Challenges
Consumers want smartphones that last longer. New semiconductor process technologies have been developed to reduce leakage current and impedance (sometimes through copper coatings), making FET transistors have lower quiescent current and smaller on-resistance. However, unlike semiconductor technology, which continues to improve, battery technology has not made any major progress to extend the battery life without increasing the size of the battery.
Some advances in capacitor technology have blurred the line between rechargeable batteries and capacitors. Many portable products have begun to use high-energy supercapacitors as a temporary power source when consumers replace batteries. In addition, high-energy and high-power ultra capacitors can also provide large currents in a short period of time, so that the battery does not need to supply huge power instantly, which can extend the battery life. These ultra capacitors are integrated into the battery package and charged with a small current when the system power demand is not high. Fuel cells are a hot topic recently, but the widespread application of fuel cells is affected by the lack of standardization of the appearance packaging, and the commercialization process is not smooth. The transient response of the output of fuel cells is also poor, so at least in the initial stage, fuel cells will only serve as a supplement to ordinary batteries and cannot completely replace ordinary batteries.
Consumers also want products to be smaller and more powerful. Innovative power management component design and advances in packaging and process technology can help achieve this goal. Increasingly sophisticated process technology can produce smaller and smaller FET transistors, making the size of the die and package smaller, the operating voltage lower, the gate capacitance less, and the switching speed of the transistor faster
- for inductor-based switching power supplies, faster switching speed means smaller inductance. New packaging technology can accommodate more functions in a smaller package and withstand greater power consumption. For example, the bq24010, a lithium-ion battery linear charging component with a built-in FET switch, uses a 3×3 square centimeter QFN package. It can withstand up to 1.5W of power consumption at room temperature. To provide more powerful functions at lower
operating voltages, the tolerance requirements of the power management unit and low-noise layout will usually become more stringent. For example, if the system requires the error of the 1.2V power supply to be less than ±3%, it means that the output voltage fluctuation cannot exceed ±36mV; in contrast, using a 3.3V power supply means that under the same ±3% error limit, it can tolerate voltage fluctuations of up to ±99mV. As supply voltages continue to decrease, the need for DC power converters with lower tolerances, higher currents, higher efficiency, and very low EMI will increase in the coming years. In addition, as packages shrink, the area available for heat dissipation will also decrease, making thermal management of these high-power components a difficult challenge.
The Power of Integration
The power solutions described in this article use power components with different levels of integration. Integrating some or all of the analog power components with digital parts such as baseband processors has many advantages, including saving more board area and reducing overall cost. One of the obstacles to achieving higher-level integration of digital and analog components in the past is that each part of a complex electronic system has different requirements. For example, the digital baseband unit requires a high-density process to support digital signal processing, and the analog baseband and power functions require higher voltage components. The RF unit, especially the phase-locked loop, requires BiCMOS components that are best suited to support high-frequency operation. Traditionally, process development has been managed by digital designers, who usually only push for high-density process development. If the circuit requires high-voltage components, it must use a different process, which means that they need separate digital components. Semiconductor manufacturers have not only begun to develop BiCMOS processes with shorter "minimum gate lengths" to provide high component density and operating speed, but also higher voltage drain extended devices, which have been used in more analog and power applications. Many analog and digital functions, including power management, will eventually be integrated into a single chip.
Conclusion
Different levels of component integration are simplifying portable power design, especially for system designers of portable products. They no longer have to worry about managing the power requirements of components. Power management components with different levels of integration can help them maximize battery power supply time while minimizing circuit board area and cost.
Previous article:Mobile phone charger solution that meets 30mW standby power consumption requirement
Next article:Detailed explanation of wireless charging on the charging stand
Recommended ReadingLatest update time:2024-11-16 16:38
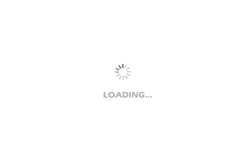
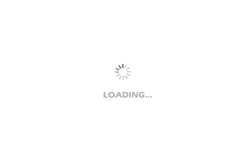
- MathWorks and NXP Collaborate to Launch Model-Based Design Toolbox for Battery Management Systems
- STMicroelectronics' advanced galvanically isolated gate driver STGAP3S provides flexible protection for IGBTs and SiC MOSFETs
- New diaphragm-free solid-state lithium battery technology is launched: the distance between the positive and negative electrodes is less than 0.000001 meters
- [“Source” Observe the Autumn Series] Application and testing of the next generation of semiconductor gallium oxide device photodetectors
- 采用自主设计封装,绝缘电阻显著提高!ROHM开发出更高电压xEV系统的SiC肖特基势垒二极管
- Will GaN replace SiC? PI's disruptive 1700V InnoMux2 is here to demonstrate
- From Isolation to the Third and a Half Generation: Understanding Naxinwei's Gate Driver IC in One Article
- The appeal of 48 V technology: importance, benefits and key factors in system-level applications
- Important breakthrough in recycling of used lithium-ion batteries
- Innolux's intelligent steer-by-wire solution makes cars smarter and safer
- 8051 MCU - Parity Check
- How to efficiently balance the sensitivity of tactile sensing interfaces
- What should I do if the servo motor shakes? What causes the servo motor to shake quickly?
- 【Brushless Motor】Analysis of three-phase BLDC motor and sharing of two popular development boards
- Midea Industrial Technology's subsidiaries Clou Electronics and Hekang New Energy jointly appeared at the Munich Battery Energy Storage Exhibition and Solar Energy Exhibition
- Guoxin Sichen | Application of ferroelectric memory PB85RS2MC in power battery management, with a capacity of 2M
- Analysis of common faults of frequency converter
- In a head-on competition with Qualcomm, what kind of cockpit products has Intel come up with?
- Dalian Rongke's all-vanadium liquid flow battery energy storage equipment industrialization project has entered the sprint stage before production
- Allegro MicroSystems Introduces Advanced Magnetic and Inductive Position Sensing Solutions at Electronica 2024
- Car key in the left hand, liveness detection radar in the right hand, UWB is imperative for cars!
- After a decade of rapid development, domestic CIS has entered the market
- Aegis Dagger Battery + Thor EM-i Super Hybrid, Geely New Energy has thrown out two "king bombs"
- A brief discussion on functional safety - fault, error, and failure
- In the smart car 2.0 cycle, these core industry chains are facing major opportunities!
- The United States and Japan are developing new batteries. CATL faces challenges? How should China's new energy battery industry respond?
- Murata launches high-precision 6-axis inertial sensor for automobiles
- Ford patents pre-charge alarm to help save costs and respond to emergencies
- New real-time microcontroller system from Texas Instruments enables smarter processing in automotive and industrial applications
- Solution to MotionFX getting stuck when executing MotionFX_initialize(); function
- W806 Lianshengde 9.9 yuan development board experience 4 --- SDK surprise discovery
- A Complete List of "English Abbreviations" in Hardware Schematics
- A little skill can satisfy high return income. Let's share a product repair with super high click rate
- Why use ultrasonic testing for flow meters?
- How KiCAD schematics and PCB interact
- About Power
- Usage of $test$plusargs
- Amplifier Expert Design Experience
- Flathead RVB2601 board-web playback