In the past, LED manufacturers have developed large-size LED chips to achieve their desired goals in order to obtain sufficient white light LED beams. However, in reality, when the applied power of white light LEDs exceeds 1W, the beam will decrease, and the luminous efficiency will decrease by 20~30%. In other words, if the brightness of white light LEDs is to be several times greater than that of traditional LEDs and the power consumption characteristics are to exceed those of fluorescent lamps, the following four major issues must be overcome: suppressing temperature rise, ensuring service life, improving luminous efficiency, and equalizing luminous characteristics.
The solution to the temperature rise problem is to reduce the thermal impedance of the package; the way to maintain the service life of the LED is to improve the chip shape and use small chips; the way to improve the luminous efficiency of the LED is to improve the chip structure and use small chips; as for the way to uniformize the luminous characteristics, it is to improve the LED packaging method. These methods have been developed one after another.
Solving the heat dissipation problem of packaging is the fundamental solution
Since increasing power will cause the thermal impedance of the package to drop sharply below 10K/W, foreign companies have developed high-temperature resistant white light LEDs in an attempt to improve the above problem. However, in fact, the heat generated by high-power LEDs is more than ten times higher than that of low-power LEDs, and the temperature rise will also cause a significant drop in luminous efficiency. Even if the packaging technology allows high heat, the junction temperature of the LED chip may exceed the allowable value. Finally, the industry finally realized that solving the heat dissipation problem of the package is the fundamental solution.
Regarding the service life of LEDs, for example, the use of silicon packaging materials and ceramic packaging materials can increase the service life of LEDs by single digits. In particular, the emission spectrum of white light LEDs contains short-wavelength light with a wavelength below 450nm. Traditional epoxy resin packaging materials are easily damaged by short-wavelength light. The large amount of light from high-power white light LEDs accelerates the degradation of packaging materials. According to industry test results, the brightness of high-power white light LEDs has been reduced by more than half if the lighting is continuously turned on for less than 10,000 hours, which cannot meet the basic requirement of long life of lighting sources.
Regarding the luminous efficiency of LEDs, improving the chip structure and packaging structure can achieve the same level as low-power white light LEDs. The main reason is that when the current density is increased by more than 2 times, it is not only difficult to extract light from large chips, but the result is that the luminous efficiency is not as good as low-power white light LEDs. If the electrode structure of the chip is improved, the above light extraction problem can be solved in theory.
Try to reduce thermal impedance and improve heat dissipation
Regarding the uniformity of luminous properties, it is generally believed that the above problems can be overcome by improving the uniformity of the concentration of the phosphor material of the white light LED and the manufacturing technology of the phosphor. As mentioned above, while increasing the applied power, it is necessary to find ways to reduce thermal impedance and improve heat dissipation. The specific contents are: reducing the thermal impedance from the chip to the package, suppressing the thermal impedance from the package to the printed circuit board, and improving the heat dissipation smoothness of the chip.
In order to reduce thermal impedance, many foreign LED manufacturers place LED chips on the surface of heat sinks made of copper and ceramic materials, and then use welding to connect the heat dissipation wires of the printed circuit board to the heat sink that uses a cooling fan to force air cooling. According to the experimental results of OSRAM Opto Semiconductors Gmb in Germany, the thermal impedance of the LED chip to the welding point of the above structure can be reduced by 9K/W, which is about 1/6 of the traditional LED. When 2W of power is applied to the packaged LED, the junction temperature of the LED chip is 18K higher than the welding point. Even if the temperature of the printed circuit board rises to 50℃, the junction temperature is only about 70℃ at most; in contrast, once the thermal impedance is reduced, the junction temperature of the LED chip will be affected by the temperature of the printed circuit board. Therefore, it is necessary to try to reduce the temperature of the LED chip. In other words, reducing the thermal impedance from the LED chip to the welding point can effectively reduce the burden of the cooling effect of the LED chip. On the other hand, even if the white light LED has a structure that suppresses thermal impedance, if the heat cannot be transferred from the package to the printed circuit board, the result of the LED temperature rise will still cause a sharp drop in luminous efficiency. Therefore, Panasonic Electric has developed a technology to integrate printed circuit boards and packaging. The company packaged 1mm square blue light LEDs on a ceramic substrate in a flip chip manner, and then pasted the ceramic substrate on the surface of a copper printed circuit board. According to Panasonic, the thermal impedance of the entire module including the printed circuit board is about 15K/W.
Various industry players demonstrate their thermal design skills
Since the compactness between the heat sink and the printed circuit board directly affects the heat conduction effect, the design of the printed circuit board becomes very complicated. In view of this, lighting equipment and LED packaging manufacturers such as Lumileds in the United States and CITIZEN in Japan have successively developed simple heat dissipation technology for high-power LEDs. CITIZEN began to manufacture white light LED sample packaging in 2004, which can directly discharge the heat of the heat sink of about 2~3mm thickness to the outside without special bonding technology. According to the CITIZEN report, although the 30K/W thermal impedance from the junction of the LED chip to the heat sink is larger than the 9K/W of OSRAM, and the room temperature in a general environment will increase the thermal impedance by about 1W, even if the traditional printed circuit board is forced to cool without a cooling fan, the white light LED module can be used continuously.
Lumileds began to manufacture high-power LED chips in 2005, with a junction allowable temperature of up to +185°C, 60°C higher than other companies' products of the same level. When using traditional RF 4 printed circuit board packaging, a current equivalent to 1.5W of power (about 400mA) can be input within an ambient temperature range of 40°C. Therefore, Lumileds and CITIZEN have adopted the approach of increasing the junction allowable temperature, while Germany's OSRAM has set the LED chip on the surface of the heat sink, achieving an ultra-low thermal impedance record of 9K/W, which is 40% lower than the thermal impedance of OSRAM's previous products of the same level. It is worth mentioning that the LED module is packaged using the same flip chip method as the traditional method, but when the LED module is bonded to the heat sink, the closest to the LED chip's light-emitting layer is selected as the bonding surface, so that the heat of the light-emitting layer can be conducted and discharged at the shortest distance.
In 2003, Toshiba Lighting once laid a 60lm/W low thermal impedance white light LED on a 400mm square aluminum alloy surface, and trial-produced an LED module with a beam of 300lm without any special heat dissipation components such as cooling fans. As Toshiba Lighting has rich trial production experience, the company said that due to the advancement of simulation analysis technology, white light LEDs exceeding 60lm/W after 2006 can easily use lamps and frames to improve thermal conductivity, or use cooling fans to force air cooling to design the heat dissipation of lighting equipment. White light LEDs can also be used in module structures that do not require special heat dissipation technology.
Changing the packaging material to reduce the rate of material degradation and light transmittance reduction
Regarding the longevity of LEDs, the current countermeasures taken by LED manufacturers are to change the packaging materials and disperse the fluorescent materials in the packaging materials. In particular, the silicon packaging materials can more effectively suppress the degradation of materials and the speed of light transmittance reduction than the epoxy resin packaging materials on the traditional blue light and near-ultraviolet light LED chips. Since the percentage of epoxy resin absorbing light with a wavelength of 400~450nm is as high as 45%, while the silicon packaging material is less than 1%, the time for epoxy resin to halve the brightness is less than 10,000 hours, while the silicon packaging material can be extended to about 40,000 hours, which is almost the same as the design life of the lighting equipment. This means that the white light LED does not need to be replaced during the use of the lighting equipment. However, silicon resin is a highly elastic and soft material, and the production technology that will not scratch the surface of the silicon resin must be used during processing. In addition, silicon resin is very easy to adhere to dust during processing, so it is necessary to develop technologies that can improve surface properties in the future.
Although silicon packaging materials can ensure the service life of LEDs for 40,000 hours, lighting equipment manufacturers have different opinions. The main debate is that the service life of traditional incandescent lamps and fluorescent lamps is defined as "the brightness drops below 30%." The LED with a brightness halving time of 40,000 hours, if converted to a brightness drop below 30%, only has about 20,000 hours left. There are currently two countermeasures to extend the service life of components, namely, suppressing the overall temperature rise of white light LEDs and stopping the use of resin packaging.
It is generally believed that if the above two life extension measures are thoroughly implemented, the requirement of 40,000 hours at 30% brightness can be achieved. The temperature rise of white light LEDs can be suppressed by cooling the LED package printed circuit board. The main reason is that the package resin will deteriorate rapidly when it is exposed to strong light under high temperature. According to the Arrhenius law, the life will be extended by 2 times if the temperature is reduced by 10°C. Stopping the use of resin packaging can completely eliminate the degradation factors, because the light generated by the LED is reflected in the package resin. If a resin reflector that can change the direction of light on the side of the chip is used, the reflector will absorb the light, causing the amount of light extracted to drop sharply. This is also the main reason why LED manufacturers consistently use ceramic and metal packaging materials.
Previous article:Discussion on LED Packaging Technology
Next article:Design of single-stage CrM TRIAC dimming LED driver based on NCL30000
Recommended ReadingLatest update time:2024-11-17 02:25
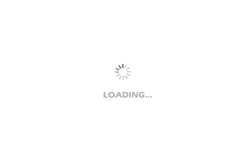
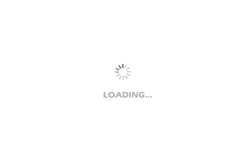
- Popular Resources
- Popular amplifiers
- MathWorks and NXP Collaborate to Launch Model-Based Design Toolbox for Battery Management Systems
- STMicroelectronics' advanced galvanically isolated gate driver STGAP3S provides flexible protection for IGBTs and SiC MOSFETs
- New diaphragm-free solid-state lithium battery technology is launched: the distance between the positive and negative electrodes is less than 0.000001 meters
- [“Source” Observe the Autumn Series] Application and testing of the next generation of semiconductor gallium oxide device photodetectors
- 采用自主设计封装,绝缘电阻显著提高!ROHM开发出更高电压xEV系统的SiC肖特基势垒二极管
- Will GaN replace SiC? PI's disruptive 1700V InnoMux2 is here to demonstrate
- From Isolation to the Third and a Half Generation: Understanding Naxinwei's Gate Driver IC in One Article
- The appeal of 48 V technology: importance, benefits and key factors in system-level applications
- Important breakthrough in recycling of used lithium-ion batteries
- Innolux's intelligent steer-by-wire solution makes cars smarter and safer
- 8051 MCU - Parity Check
- How to efficiently balance the sensitivity of tactile sensing interfaces
- What should I do if the servo motor shakes? What causes the servo motor to shake quickly?
- 【Brushless Motor】Analysis of three-phase BLDC motor and sharing of two popular development boards
- Midea Industrial Technology's subsidiaries Clou Electronics and Hekang New Energy jointly appeared at the Munich Battery Energy Storage Exhibition and Solar Energy Exhibition
- Guoxin Sichen | Application of ferroelectric memory PB85RS2MC in power battery management, with a capacity of 2M
- Analysis of common faults of frequency converter
- In a head-on competition with Qualcomm, what kind of cockpit products has Intel come up with?
- Dalian Rongke's all-vanadium liquid flow battery energy storage equipment industrialization project has entered the sprint stage before production
- Allegro MicroSystems Introduces Advanced Magnetic and Inductive Position Sensing Solutions at Electronica 2024
- Car key in the left hand, liveness detection radar in the right hand, UWB is imperative for cars!
- After a decade of rapid development, domestic CIS has entered the market
- Aegis Dagger Battery + Thor EM-i Super Hybrid, Geely New Energy has thrown out two "king bombs"
- A brief discussion on functional safety - fault, error, and failure
- In the smart car 2.0 cycle, these core industry chains are facing major opportunities!
- Rambus Launches Industry's First HBM 4 Controller IP: What Are the Technical Details Behind It?
- The United States and Japan are developing new batteries. CATL faces challenges? How should China's new energy battery industry respond?
- Murata launches high-precision 6-axis inertial sensor for automobiles
- Ford patents pre-charge alarm to help save costs and respond to emergencies
- RGB565
- EEWORLD University - Analysis and Design of Analog Integrated Circuits
- Has anyone tried the GD32E230 board?
- Let's talk about the technical difficulties of electric vehicles. It turns out that the electric motor is not the core
- [Liquid Level Sensor Evaluation] Capacitive-non-contact sensor response to container media
- Recruiting antenna RF part-time teacher
- Very detailed introductory article FPGA_SOPC_starter.pdf
- The era of UWB is coming, are you ready?
- [Perf-V Evaluation] Development of Hummingbird Timer Interrupt Based on Perf-V Development Board
- 485 Communication abnormality