The switching power supply electromagnetic interference filter is a passive network with bidirectional suppression performance. Inserting it between the AC power grid and the power supply is equivalent to adding a blocking barrier between the EMI noise of the two. Such a simple passive filter plays a role in bidirectional noise suppression, thus gaining wide application in various electronic devices.
Switching power supplies are widely used in various electronic devices such as computers and communications due to their low power consumption, high efficiency, small size, light weight, wide voltage regulation range, and flexible circuit form. However, with the miniaturization of switching power supplies, the switch must be high-frequency. This high frequency, the fundamental wave itself constitutes an interference source, emitting a stronger conducted interference wave. In addition, while achieving high frequency by improving components, a stray signal exceeding the standard value will also be caused by radiated interference waves. These signals constitute electromagnetic interference (EMI), and the interfered object is radio communication. In order to prevent radio waves from being affected by electromagnetic interference, measures must be taken to limit this electromagnetic interference so that it complies with relevant electromagnetic compatibility (EMC) standards or specifications. This has become an issue that electronic product designers are increasingly concerned about.
Characteristics of Switching Power Supply Electromagnetic Interference (EMI)
The switching frequency of power semiconductor devices in the power converter of the switching power supply is usually high. The power switching devices will inevitably generate strong electromagnetic interference during the on and off process at high frequency. Compared with digital circuits, the EMI of the switching power supply presents distinct characteristics: a. The location of the EMI interference source of the switching power supply is relatively clear, mainly concentrated on the power switching devices, diodes, and the heat sink and high-frequency transformer connected thereto. b. As an energy conversion device working in the switching state, the voltage and current change rate of the switching power supply is very high, and the EMI noise signal it generates has both a wide frequency range and a certain intensity. c. Improper wiring of the printed circuit board is also the main cause of electromagnetic interference. These interferences interfere with other electronic equipment through conduction and radiation.
Any conducted interference signal on the power line can be represented by differential mode and common mode signals. In general, the differential mode interference has a small amplitude and low frequency, so the interference caused is small; the common mode interference has a large amplitude and high frequency, and can also radiate through the wire, causing greater interference. Therefore, in order to weaken the conducted interference and control the EMI signal below the limit level specified by the relevant EMC standards, the most effective method is to install electromagnetic interference filters in the input and output circuits of the switching power supply. Design of electromagnetic interference filters
(1) EMI filter design principles
The design and selection of electromagnetic interference filters should be comprehensively considered based on the characteristics of the interference source, frequency range, voltage, impedance and other parameters and load characteristics. Usually, the following issues should be considered:
1) The electromagnetic interference filter is required to meet the attenuation characteristics required by the load within the corresponding working frequency band. If the attenuation of one filter cannot meet the requirements, a multi-stage cascade can be used to obtain a higher attenuation than a single stage. Different filter cascades can obtain good attenuation characteristics in a wide frequency band.
2) To meet the requirements of the load circuit operating frequency and the frequency to be suppressed, if the frequency to be suppressed is very close to the useful signal frequency, an EMI filter with a very steep frequency characteristic is required.
3) At the required frequency, the impedance of the filter must match the impedance of the interference source and the load impedance connected to it. If the load is high impedance, the output impedance of the EMI filter should be low impedance; if the power supply or interference source impedance is low impedance, the output impedance of the EMI filter should be high impedance; if the power supply impedance or interference source impedance is unknown or varies within a large range, it is difficult to obtain stable filtering characteristics. In order to make the EMI filter obtain good filtering characteristics, a fixed resistor should be connected in parallel at both its input and output ends.
4) The electromagnetic interference filter must have a certain voltage resistance. The filter should be selected according to the rated voltage of the power supply and the interference source. It should have a high enough rated voltage to ensure that it can work reliably under all expected working conditions and withstand the impact of instantaneous high voltage input.
5) The current allowed to pass through the filter should be consistent with the rated current of the circuit in continuous operation. If the current is set too high, the size and weight of the filter will increase; if the current is set too low, the reliability of the filter will be reduced.
6) The filter should have sufficient mechanical strength, simple structure, light weight, small size, easy installation, safety and reliability.
(2) Circuit structure and parameter selection of electromagnetic interference filter
Figure 1 is the circuit of the switching power supply EMI filter. Among them, L1 and L2 are common mode chokes, and their structure is shown in Figure 2. Since the number of turns of its two coils is equal, the magnetic flux generated by these two inductors for the differential mode current and the main current is opposite in direction and cancels each other, so it has no effect; while for the common mode interference signal, a large inductance can be obtained to present high impedance to obtain the maximum filtering effect, so it has a good suppression effect on it. However, due to various reasons, such as the material of the magnetic ring cannot be absolutely uniform, and the winding of the two coils cannot be completely symmetrical, the inductance of L1 and L2 is not equal, so (L1-L2) forms a differential mode inductor, which, together with the independent differential mode suppression inductor formed by L3 and L4 and the Cx capacitor, forms a low-pass filter between the independent ports of L-N, which is used to suppress the differential mode interference signal existing on the power line.
When selecting filter components, it is important to ensure that the input filter resonant frequency is lower than the operating frequency of the switching power supply. As the operating frequency of the power supply increases, the filter will be easier to suppress the operating noise, so in the design, attention should be paid to the suppression effect of the filter at low operating frequencies.
The CX capacitor is used to attenuate differential mode interference, CY is used to attenuate common mode interference, and R is used to eliminate static electricity accumulation that may occur in the filter. If the capacitance of the capacitor is greater than 0.1 μF, the resistance of the discharge resistor should be
R = t /(2.21C)
Where, t = 1 s; C is the sum of the two CX values. In the circuit shown in Figure 1, the parameters of each component are selected within the following range:
CX is 0.1~2 μF; CY is 2200 pF~0.033 μF; L1 and L2 are several to tens of millihenries; different parameters are selected according to different working currents.
The magnetic cores used in common mode chokes are ring-shaped, E-shaped, and U-shaped, and are generally made of ferrite materials. Ring-shaped magnetic cores are suitable for large currents and small inductances. Their magnetic circuits are longer than those of E-shaped and U-shaped magnetic cores, and they have no gaps. They can obtain larger inductances with fewer turns. Due to these characteristics, they have better frequency characteristics. The coil leakage flux of the E-shaped magnetic core is small, so when the inductor leakage flux may affect other circuits or other circuits have magnetic coupling with the common mode inductor, and the required noise attenuation effect cannot be obtained, the E-shaped magnetic core should be considered as the common mode inductor.
L3 and L4 generally use metal powder pressed cores. Since the applicable frequency range of powder pressed cores is relatively low, at tens of kilohertz to several megahertz, their DC superposition characteristics are good, and the inductance will not drop significantly when large currents are used, they are most suitable for differential mode inductors.
The differential mode capacitor CX is connected to both ends of the AC incoming line. In addition to the rated AC voltage, it will also be superimposed with various EMI peak voltages between the AC incoming lines. Therefore, the performance requirements of the capacitor's withstand voltage and transient peak voltage resistance are relatively high; at the same time, it is required that after the capacitor fails, it cannot endanger the subsequent circuit and personal safety. The safety level of CX capacitors is divided into two categories: X1 and X2. Category X1 is suitable for general occasions, and category X2 is suitable for applications where high noise peak voltages will appear. Therefore, it is necessary to correctly select capacitors with appropriate safety levels based on the application of the EMI filter and the possible peak values of the EMI signal.
Common mode capacitors CY are connected between the AC power line and the chassis ground. They are required to have a large enough safety margin in terms of electrical and mechanical performance. In case of breakdown and short circuit, the equipment chassis will be charged with AC. If the insulation or grounding protection of the equipment fails, the operator may suffer an electric shock or even endanger personal safety. Therefore, the capacity of the CY capacitor should be limited so that its leakage current is less than the safety specification value at the rated frequency voltage. In addition, it is required to have sufficient withstand voltage and withstand transient high peak voltage margin, and in case of voltage breakdown, it should be in an open circuit state without charging the equipment chassis.
Since the filter works in a high voltage, high current, and harsh electromagnetic interference environment, the safety performance of the inductor and capacitor used must be considered when designing and selecting the filter. For the inductor coil, the material of the magnetic core and winding, the insulation material and insulation distance, and the temperature rise of the coil should all be taken into consideration. For the capacitor, the type of capacitor, withstand voltage, safety level, capacity, and leakage should all be given priority, and it is especially required to select products that have been certified by international safety agencies.
Installation of EMI Filters
To achieve good results, the filter must be installed properly. Generally, the following points should be considered.
1) The filter should be installed as close to the equipment entrance as possible, and the AC line that does not pass through the filter in the equipment should be as short as possible. It is best to install it at the outlet of the interference source, and then completely shield the interference source and the filter. If the space inside the interference source is limited, it should be installed near the outside of the power line outlet of the interference source, and the filter housing should be well overlapped with the interference source housing.
2) The input and output lines of the filter must be separated to prevent the input and output lines from coupling and reducing the filtering characteristics. The filter is usually fixed with a partition or chassis. If the isolation method cannot be implemented, use shielded leads.
3) The capacitor wires in the filter should be as short as possible to prevent the inductive reactance and capacitive reactance from resonating at a certain frequency.
4) There is a large short-circuit current on the filter grounding wire, which can radiate electromagnetic interference and requires good shielding.
5) Each wire soldered to the same socket must be filtered, otherwise the filtering attenuation characteristics will be completely lost.
6) The tubular filter must be installed completely coaxially so that the electromagnetic interference current flows through the filter in a radial manner.
Previous article:Design of EMI filter for switching power supply based on synthetic choke
Next article:The basic working principle of switching power supply
Recommended ReadingLatest update time:2024-11-16 16:30
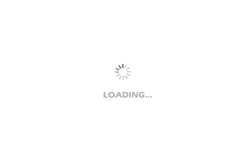
- MathWorks and NXP Collaborate to Launch Model-Based Design Toolbox for Battery Management Systems
- STMicroelectronics' advanced galvanically isolated gate driver STGAP3S provides flexible protection for IGBTs and SiC MOSFETs
- New diaphragm-free solid-state lithium battery technology is launched: the distance between the positive and negative electrodes is less than 0.000001 meters
- [“Source” Observe the Autumn Series] Application and testing of the next generation of semiconductor gallium oxide device photodetectors
- 采用自主设计封装,绝缘电阻显著提高!ROHM开发出更高电压xEV系统的SiC肖特基势垒二极管
- Will GaN replace SiC? PI's disruptive 1700V InnoMux2 is here to demonstrate
- From Isolation to the Third and a Half Generation: Understanding Naxinwei's Gate Driver IC in One Article
- The appeal of 48 V technology: importance, benefits and key factors in system-level applications
- Important breakthrough in recycling of used lithium-ion batteries
- Innolux's intelligent steer-by-wire solution makes cars smarter and safer
- 8051 MCU - Parity Check
- How to efficiently balance the sensitivity of tactile sensing interfaces
- What should I do if the servo motor shakes? What causes the servo motor to shake quickly?
- 【Brushless Motor】Analysis of three-phase BLDC motor and sharing of two popular development boards
- Midea Industrial Technology's subsidiaries Clou Electronics and Hekang New Energy jointly appeared at the Munich Battery Energy Storage Exhibition and Solar Energy Exhibition
- Guoxin Sichen | Application of ferroelectric memory PB85RS2MC in power battery management, with a capacity of 2M
- Analysis of common faults of frequency converter
- In a head-on competition with Qualcomm, what kind of cockpit products has Intel come up with?
- Dalian Rongke's all-vanadium liquid flow battery energy storage equipment industrialization project has entered the sprint stage before production
- Allegro MicroSystems Introduces Advanced Magnetic and Inductive Position Sensing Solutions at Electronica 2024
- Car key in the left hand, liveness detection radar in the right hand, UWB is imperative for cars!
- After a decade of rapid development, domestic CIS has entered the market
- Aegis Dagger Battery + Thor EM-i Super Hybrid, Geely New Energy has thrown out two "king bombs"
- A brief discussion on functional safety - fault, error, and failure
- In the smart car 2.0 cycle, these core industry chains are facing major opportunities!
- The United States and Japan are developing new batteries. CATL faces challenges? How should China's new energy battery industry respond?
- Murata launches high-precision 6-axis inertial sensor for automobiles
- Ford patents pre-charge alarm to help save costs and respond to emergencies
- New real-time microcontroller system from Texas Instruments enables smarter processing in automotive and industrial applications
- Playing with Zynq Serial 39——[ex58] XADC acquisition control example based on Zynq
- [AD21] How to solve the error Board Clearance Constraint
- Can anyone make a 433M remote control?
- 【DFRobot Wireless Communication Module】+ DFRobot Gravity: UART A6 GSM & GPRS Wireless Communication Module Review
- Creative PCB display
- LPC2478 Timer 2 and Timer 3 enable
- Design and implementation of optical transceiver UART interface based on FPGA.pdf
- MicroPython official new wiki
- Is this setting OK?
- Daisy chain communication