This article introduces a driver reference design for AR111 LED lamps in a 2-in-parallel-5-in-series (5S2P) configuration.
Overview
This reference design uses the MAX16819 as the main controller to provide a buck-boost driver solution for the 5S2P AR111 LED lamp. Figure 1 is the circuit schematic, and Figure 2 shows the design layout.
The electrical input requirements and output characteristics are as follows:
VIN:12VAC ±10%
PWM input: Not applicable
VLED configuration: 5S2P, 3VDC to 3.8VDC per LED (19VDC per string, maximum), 500mA per string
The following is a detailed discussion of this reference design, analyzing its main circuit blocks and design specifications.
Figure 1. LED driver schematic
Figure 2. LED driver layout
Design Analysis
The AR111 LED lamp reference design can drive a total of 10 LEDs—2 parallel strings of 5 LEDs each. The input voltage is 12VAC with a tolerance of ±10%. Schottky diodes D1 to D4 form a full-wave rectifier circuit, and capacitors C1 to C8 are used for voltage filtering. Depending on the requirements for LED flicker, some filter capacitors can be removed to reduce costs. These capacitors include a tantalum capacitor, which has good temperature characteristics.
Because the LEDs are arranged in 5S2P, it is impossible to achieve a completely matched current. Assuming that the LED lamps have good matching, the current difference is minimized. Controlling the number of LEDs in each string and the number of lamps in the hybrid architecture can help mitigate the impact of current matching.
The MAX16819 is designed to be used as a buck regulator, but can also be set up in buck-boost mode. However, this configuration sacrifices some current accuracy.
Inductor Selection
Calculate the LED current as follows:
Where IL is the inductor current. The above formula shows that the LED current is equal to the inductor current after the input and output voltages are corrected. The fluctuation of VIN (120Hz ripple) will cause the LED current to fluctuate accordingly.
Use the following formula to calculate the inductor current:
In this design, the average LED current is 1A, the average VIN is 13V, and the average VLED is 19V. Therefore, the required inductor current is:
The inductor current can be adjusted using an 80mΩ current-sense resistor. When the input voltage is low (assuming about 10V), the LED current drops to about 850mA; when the input voltage reaches 16V, the LED current can reach about 1.12A.
The inductor L1 operates at a switching frequency of 250kHz, with an average current of 2.46A and a peak current of 2.83A. The Coilcraft® inductor MSS1260-393ML can be selected, with an inductance of 39µH, a rated continuous current of 2.6A (40°C temperature rise), and a saturation current of 3.08A (10% decrease in inductance).
Overvoltage protection
When the load is open circuit, R7, R8 and Q2 can provide overvoltage (OV) protection. Without the overvoltage protection circuit, the LED in the open circuit state will cause the output voltage to run away and damage the device. The overvoltage protection threshold is about 30V.
Thermal Management
R2, R4, R5, R6, and U2 provide foldback thermal management. R4 is a 100kΩ negative temperature coefficient thermistor (constant B = 4250). When the temperature reaches 50 degrees Celsius, the resistance of resistor R4 decreases, which increases the voltage at the control pin of U2, causing some current to flow through R6 and R2. This current reduces the voltage at the input current sense resistor R1, thereby reducing the current in the inductor and LED. As the temperature rises, the voltage across R2 increases further, further reducing the LED current. Finally, as the LED current decreases, the temperature returns to the normal range and the system is balanced. The foldback thermal management architecture allows LED lamps to be used in applications where air circulation is limited without concern for overheating. Thermal management may slightly affect the brightness of the lamp, but still maintain an acceptable lighting level.
Q1 (STN3NF06L) is a 60V, 0.07Ω, logic-level controlled MOSFET in a SOT223 package. This MOSFET has a small total gate charge (Qg = 9nC, maximum) to keep switching losses to a minimum. The device losses are approximately: 400mW (conduction losses) and 500mW (switching losses), for a total of 900mW. The package thermal resistance is 38°C/W, which will cause the die temperature to be 34°C higher than the PCB temperature. Possible error factors must also be considered to retain more margin.
PCB Layout
In PCB design, all components are placed on the top layer of the circuit board, and the bottom layer is reserved for ground. In actual applications, the circuit is installed on an aluminum structure, which can provide better grounding and heat dissipation performance. The top layer design uses a larger copper area to improve the thermal conductivity between the aluminum structure.
Previous article:On Semi NCP1219 Universal AC Input Non-Isolated 6W Electric Meter Step-Down Power Supply Solution
Next article:Design of timing light-controlled LED street light control
Recommended ReadingLatest update time:2024-11-16 16:30
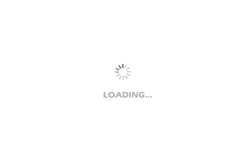
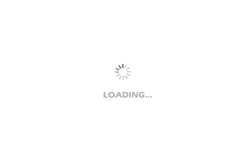
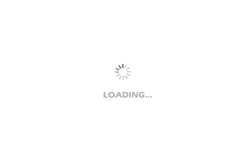
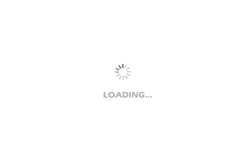
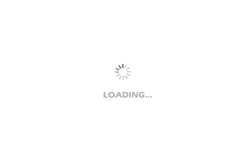
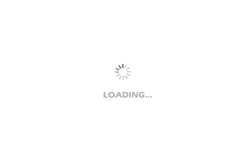
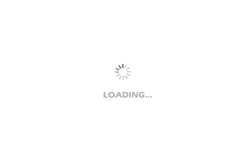
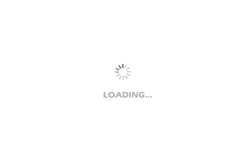
- Popular Resources
- Popular amplifiers
-
Siemens Motion Control Technology and Engineering Applications (Tongxue, edited by Wu Xiaojun)
-
Modern Product Design Guide
-
Modern arc welding power supply and its control
-
Small AC Servo Motor Control Circuit Design (by Masaru Ishijima; translated by Xue Liang and Zhu Jianjun, by Masaru Ishijima, Xue Liang, and Zhu Jianjun)
- MathWorks and NXP Collaborate to Launch Model-Based Design Toolbox for Battery Management Systems
- STMicroelectronics' advanced galvanically isolated gate driver STGAP3S provides flexible protection for IGBTs and SiC MOSFETs
- New diaphragm-free solid-state lithium battery technology is launched: the distance between the positive and negative electrodes is less than 0.000001 meters
- [“Source” Observe the Autumn Series] Application and testing of the next generation of semiconductor gallium oxide device photodetectors
- 采用自主设计封装,绝缘电阻显著提高!ROHM开发出更高电压xEV系统的SiC肖特基势垒二极管
- Will GaN replace SiC? PI's disruptive 1700V InnoMux2 is here to demonstrate
- From Isolation to the Third and a Half Generation: Understanding Naxinwei's Gate Driver IC in One Article
- The appeal of 48 V technology: importance, benefits and key factors in system-level applications
- Important breakthrough in recycling of used lithium-ion batteries
- Innolux's intelligent steer-by-wire solution makes cars smarter and safer
- 8051 MCU - Parity Check
- How to efficiently balance the sensitivity of tactile sensing interfaces
- What should I do if the servo motor shakes? What causes the servo motor to shake quickly?
- 【Brushless Motor】Analysis of three-phase BLDC motor and sharing of two popular development boards
- Midea Industrial Technology's subsidiaries Clou Electronics and Hekang New Energy jointly appeared at the Munich Battery Energy Storage Exhibition and Solar Energy Exhibition
- Guoxin Sichen | Application of ferroelectric memory PB85RS2MC in power battery management, with a capacity of 2M
- Analysis of common faults of frequency converter
- In a head-on competition with Qualcomm, what kind of cockpit products has Intel come up with?
- Dalian Rongke's all-vanadium liquid flow battery energy storage equipment industrialization project has entered the sprint stage before production
- Allegro MicroSystems Introduces Advanced Magnetic and Inductive Position Sensing Solutions at Electronica 2024
- Car key in the left hand, liveness detection radar in the right hand, UWB is imperative for cars!
- After a decade of rapid development, domestic CIS has entered the market
- Aegis Dagger Battery + Thor EM-i Super Hybrid, Geely New Energy has thrown out two "king bombs"
- A brief discussion on functional safety - fault, error, and failure
- In the smart car 2.0 cycle, these core industry chains are facing major opportunities!
- The United States and Japan are developing new batteries. CATL faces challenges? How should China's new energy battery industry respond?
- Murata launches high-precision 6-axis inertial sensor for automobiles
- Ford patents pre-charge alarm to help save costs and respond to emergencies
- New real-time microcontroller system from Texas Instruments enables smarter processing in automotive and industrial applications
- 【GD32E231 DIY】Use of TIMER
- Wireless technology behind the "next-day delivery" of Double 11 express delivery
- HyperLynx High-Speed Circuit Design and Simulation (X) Transmission Line (Microstrip and Stripline) Exploration
- How Bluetooth 5 maximizes the range of Bluetooth low energy connections
- Fan modification based on RSL10
- FAQ Analog Front End and Sensors
- Embedded uboot learning
- Disassembly of an eight-year-old laptop battery!
- Design of greenhouse temperature and humidity monitoring and alarm system based on zigbee
- Keysight Material Dielectric Constant Test Method - Just Read the Content