1 Introduction
To ensure that power electronic components are reliably protected from the effects of non-permissible operating conditions, fast and reliable error detection and effective protection measures are required. In the power module, error management can be provided by the system controller or by the IGBT driver. The system controller is suitable for reacting to slow failure modes, such as overheating caused by overtemperature. In contrast, drive electronics are required to detect and respond to sudden errors. Various drivers are available on the market today, with different suitability, efficiency and reliability.
2 Failure of the power conversion system
Fast errors in power conversion systems include short circuits and circuit-induced overvoltages. Short circuits are the fastest errors.
When power electronic systems are put into service, connection and isolation errors are often the cause of short circuits, while in field applications, short circuits can be attributed to faulty components.
If a short circuit occurs in the load path or in the bridge bypass, the collector current of the IGBT increases completely, causing the transistor to saturate. The IGBT modules on the market today are only short-circuit-proof for a short time. In order to prevent the IGBT from being destroyed by the thermal load, it is crucial to detect the short circuit within the safe time and reliably shut down the IGBT.
The driver electronics can detect a short circuit by measuring di/dt or by monitoring VCE.
Figure 1 (a) di/dt detection circuit diagram; (b) VCE monitoring circuit diagram
The di/dt detection circuit is shown in Figure 1 (a), where the driver measures the rate of change of the current in the IGBT through an electronic circuit. The voltage drop across the stray inductance between the auxiliary and power emitters is proportional to the rate of change of the collector current (di/dt). By comparing the voltage with a reference voltage, fast short circuits can be detected. To monitor slow short circuits, this method uses resistive elements in the bond wires and internal busbars between the power and auxiliary emitters. However, this method also depends on screw connections for the power connection. These show a certain contact resistance characteristic distribution and must be considered in series with other resistive elements. This requires precise adaptation to the given system. In general, di/dt detection can only be used for IGBT modules with auxiliary emitter outputs.
VCesat monitoring (Figure 1b) is achieved by means of a collector current versus on-state voltage curve. To this end, the collector-emitter voltage is measured and compared with a reference voltage via a comparator. If the voltage reading exceeds the reference voltage, the driver electronics automatically switches off the transistor. Due to the rapid increase in transistor voltage, Vce monitoring is a reliable short-circuit detection method. The advantage of Vce monitoring is that short-circuits can be detected quickly and are suitable for any standard IGBT.
If the load carries a higher current during a short circuit, such as on the power supply side, the collector current rises more slowly. In this case, the Vce threshold must be adjusted accordingly. In order to be able to use the Vce method for overcurrent detection, multi-stage Vce monitoring can be used. In this case, several trip thresholds with given reference times are defined. However, the disadvantage of this method is that different temperatures can lead to completely different measurement results and the factors involved in adjusting each stage for a given system are very complex. In general, a more effective and reliable method for detecting slow overcurrents is to use integrated current sensors.
In addition to fast error detection, an effective and reliable response to short circuits is also crucial. If the drive is used in a multi-level application or is used to drive a synchronous motor, the main controller should be responsible for shutting down the system. In this case, the drive only sends an isolated error signal to the controller and waits for instructions. For example, in a multi-level application, if the drive directly switches off the power semiconductor device and then sends a signal to the controller, the entire DC link voltage may be applied to an IGBT during the entire signal transmission and response time. This will cause damage to the module. However, in most applications, it is safer to let the driver switch off the power module directly. The driver can respond more quickly because it does not have to wait for the signal transmission process to complete and can switch off the module independently from the secondary side. The driver can ensure that voltage spikes are avoided when switching off the short-circuit current, which is achieved by means of a soft shutdown or secondary shutdown function. In this case, the driver will switch off the IGBT with a larger gate resistance more slowly, which protects the module from exceeding the safe operating area (SOA).
The second fast error mode is caused by circuit-induced overvoltage. The overvoltage generated during the turn-off process must be detected and reduced quickly to prevent the IGBT module from being damaged. Switching surges are caused by stray inductance in the power circuit, such as the busbar. Externally induced overvoltages are slow and can be controlled more effectively by monitoring the DC link voltage.
3 IGBT driver protection
The driver electronics can control overvoltages directly via active clamping or use IntelliOff, a feature designed to reduce critical voltage spikes.
Active clamping allows the IGBT to switch back on as soon as an overvoltage occurs. The gate charging process is essentially controlled by a central unit between collector and gate to reduce the overvoltage.
Figure 2 Active clamp circuit diagram
Here, the maximum value of the overvoltage corresponds to the Zener voltage. The transistor operates again in the safe operating area, but converts the energy stored in Lk into heat. In the process, a large amount of additional losses are generated inside the IGBT in a very short time. These losses accelerate the aging process of the components and limit the reliability of the converter system.
One way to prevent overvoltages from occurring is to use the IntelliOff shutdown function. IntelliOff offers optimized shutdown capabilities combined with the advantages of a soft shutdown with an almost instantaneous switching response. The shutdown process itself is optimized by IntelliOff thanks to the different speeds of gate discharge. First, the driver starts the IGBT shutdown process as fast as possible. As soon as the shutdown process enters the overvoltage phase, the driver slows down the shutdown process and actively reacts to the overvoltage in this case. Finally, the IGBT driver shuts down the module safely and reliably.
Figure 3 IntelliOff, proactive overvoltage protection
只要关断信号到来,驱动器产生负的栅极电荷。栅极集电极和发射极电容的放电过程开始,栅极电流达到其负峰值(period 0)。由于米勒效应,其描述了电容容抗在关断时的反馈过程,栅极发射极电压在特定的时间(period 1)内保持较高的电平。得益于小阻值的关断电阻,IntelliOff缩短了放电时间,并允许该过程加速。在period 2,大阻值电阻减慢关断过程,这样做避免了电路引起的电压尖峰(period 2)。如果没有IntelliOff,在有源箝位的情况下,这一阶段可能会出现过压,产生额外的损耗。如果不采取合适的保护措施,最终可能会导致模块的损坏。一旦危险的电压尖峰时间过去了,驱动器通过IntelliOff功能实现关断电阻的并联,确保IGBT被安全有效地关断。得益于大小关断电阻间的可调时间常数,简单的调整是可能的。
The new generation of IGBTs, in particular, has very fast and hard switching characteristics. The IntelliOff function ensures fast shutdown without the risk of dangerous voltage spikes and thus helps ensure optimal performance of the new IGBT modules. In contrast, alternative protection concepts limit the performance of the IGBT module in exchange for protection, which incurs additional losses.
4 Conclusion
The ideal protection for a gate driver depends on the specific application. However, in general, it is wise to investigate and analyze the error mechanisms during the system dimensioning phase. Using a gate driver to permanently compensate for non-permitted conditions is not an effective solution and will also reduce reliability. A more effective overvoltage protection method is to use the IntelliOff function to prevent voltage spikes from occurring in the first place. VCE monitoring is a reliable short-circuit detection method that has many advantages over di/dt detection because it is adaptable and applicable to any standard module.
There are many different drive protection solutions on the market today, ranging from standard protection functions to highly complex drive solutions. However, with simple drive solutions, users must integrate the protection functions themselves and provide drive protection for the entire system. This can be quite expensive and drive protection is often underestimated. In contrast, highly complex drive solutions often have disadvantages, the system implementation is quite complex and the service life is often limited. An optimal drive solution must meet the reliability requirements of the system, but the price for mass production applications should also be considered as an important factor.
About the Author
Johannes Krapp, Product Manager for Drive Electronics at Semikron.
Previous article:Analysis of operational amplifier capacitive load driving
Next article:Highly Efficient 28 V, 3.3 A LED Driver Design for LED Street Light Applications
Recommended ReadingLatest update time:2024-11-16 17:32
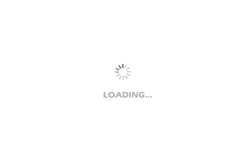
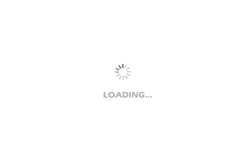
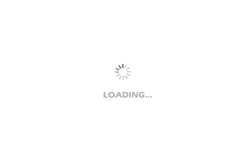
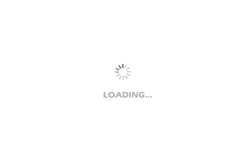
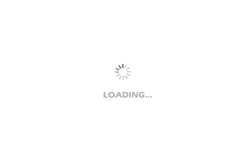
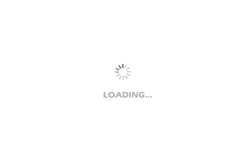
- Popular Resources
- Popular amplifiers
-
Siemens Motion Control Technology and Engineering Applications (Tongxue, edited by Wu Xiaojun)
-
Modern Product Design Guide
-
Modern arc welding power supply and its control
-
Small AC Servo Motor Control Circuit Design (by Masaru Ishijima; translated by Xue Liang and Zhu Jianjun, by Masaru Ishijima, Xue Liang, and Zhu Jianjun)
- MathWorks and NXP Collaborate to Launch Model-Based Design Toolbox for Battery Management Systems
- STMicroelectronics' advanced galvanically isolated gate driver STGAP3S provides flexible protection for IGBTs and SiC MOSFETs
- New diaphragm-free solid-state lithium battery technology is launched: the distance between the positive and negative electrodes is less than 0.000001 meters
- [“Source” Observe the Autumn Series] Application and testing of the next generation of semiconductor gallium oxide device photodetectors
- 采用自主设计封装,绝缘电阻显著提高!ROHM开发出更高电压xEV系统的SiC肖特基势垒二极管
- Will GaN replace SiC? PI's disruptive 1700V InnoMux2 is here to demonstrate
- From Isolation to the Third and a Half Generation: Understanding Naxinwei's Gate Driver IC in One Article
- The appeal of 48 V technology: importance, benefits and key factors in system-level applications
- Important breakthrough in recycling of used lithium-ion batteries
- Innolux's intelligent steer-by-wire solution makes cars smarter and safer
- 8051 MCU - Parity Check
- How to efficiently balance the sensitivity of tactile sensing interfaces
- What should I do if the servo motor shakes? What causes the servo motor to shake quickly?
- 【Brushless Motor】Analysis of three-phase BLDC motor and sharing of two popular development boards
- Midea Industrial Technology's subsidiaries Clou Electronics and Hekang New Energy jointly appeared at the Munich Battery Energy Storage Exhibition and Solar Energy Exhibition
- Guoxin Sichen | Application of ferroelectric memory PB85RS2MC in power battery management, with a capacity of 2M
- Analysis of common faults of frequency converter
- In a head-on competition with Qualcomm, what kind of cockpit products has Intel come up with?
- Dalian Rongke's all-vanadium liquid flow battery energy storage equipment industrialization project has entered the sprint stage before production
- Allegro MicroSystems Introduces Advanced Magnetic and Inductive Position Sensing Solutions at Electronica 2024
- Car key in the left hand, liveness detection radar in the right hand, UWB is imperative for cars!
- After a decade of rapid development, domestic CIS has entered the market
- Aegis Dagger Battery + Thor EM-i Super Hybrid, Geely New Energy has thrown out two "king bombs"
- A brief discussion on functional safety - fault, error, and failure
- In the smart car 2.0 cycle, these core industry chains are facing major opportunities!
- The United States and Japan are developing new batteries. CATL faces challenges? How should China's new energy battery industry respond?
- Murata launches high-precision 6-axis inertial sensor for automobiles
- Ford patents pre-charge alarm to help save costs and respond to emergencies
- New real-time microcontroller system from Texas Instruments enables smarter processing in automotive and industrial applications
- Does anyone know how to drive the LCD screen on the GD32F450z_EVAL development board?
- What are the options for isolated DAC/ADC? APC & PAC chips
- Simple analysis of the difference between STM32 and 51
- A senior project used a digital tube, a three-pin inductor, and a three-pin capacitor.
- The role of parallel resistance on the capacitor of the integration circuit
- Practical sharing: The harm of Miller effect to MOSFET switching process
- Last day! Free review of Beetle ESP32-C3, hurry up and get it
- SVPWM principle, implementation, simulation analysis
- Why is the waveform of LM324 distorted?
- Answer the questions to win prizes | TDK special reports are waiting for you