In addition to being used for motor driving, PWM (Pulse Width Modulation) is also widely used in power conversion of power supplies such as DC/DC converters and AC/DC converters, and is widely used in many fields. In principle, PWM is a method of sending the required power by turning pulses on and off. The size and period of the pulse are constant, and the power to be sent is controlled by adjusting the pulse width (time) when it is turned on. The output voltage is the average size corresponding to the ratio of the time of conduction and pulse period = duty cycle.
Below is a schematic diagram of the PWM drive principle of a brushed DC motor.
The motor is represented by a motor symbol and resistance R + inductance L + induced voltage Ec. When voltage is applied, the motor voltage Ea is applied to both ends of the motor and the motor current Ia flows. When OFF, both ends of the motor pin will be short-circuited. In this state, current regeneration will occur. Since the inductance of the coil plays a role in maintaining the current, when the voltage is repeatedly applied in a cycle that is short enough relative to the time constant of the inductance L and the resistance R and the motor ends are repeatedly short-circuited, a constant current will flow.
The process is represented by an H-bridge as follows:
When voltage is applied, SW1 and SW4 are turned on, SW2 and SW3 are turned off, and the direction of motor current Ia is shown by the gray dotted line. When turned off = short-circuited across the motor, SW2 and SW4 are turned on, and SW1 and SW3 are turned off.
The voltage and current waveforms in this case are as follows:
The voltage waveform shows that the motor voltage Ea is applied during the on period with a constant repetitive cycle, but not during the off period (regeneration due to short circuiting of both ends of the motor). The current enters a stable state by repeatedly performing the "cycle of increasing when on and decreasing when off". The average current Iave at this time is the value obtained by multiplying the applied voltage Ea by the duty cycle m and dividing by the resistance R. As a simple example, assuming Ea = 12V and m is 0.5 (duty cycle 50%), 6V is applied to the motor. Because current is supplied from the power supply only when voltage is applied, the power consumption of the power supply will be reduced.
In the previous article, we discussed the off state (current regeneration) by short-circuiting the motor terminals. In fact, there are other current regeneration methods, each with different considerations. The next article will introduce other current regeneration methods in PWM drive of brushed DC motors.
Previous article:Current regeneration method based on motor PWM output
Next article:Linear Current Drive of Brushed DC Motors Using BTL Amplifiers
Recommended ReadingLatest update time:2024-11-16 10:41
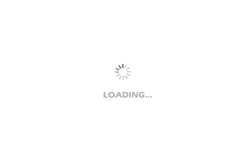
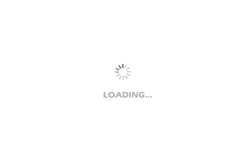
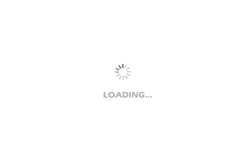
- Popular Resources
- Popular amplifiers
-
西门子S7-12001500 PLC SCL语言编程从入门到精通 (北岛李工)
-
Small AC Servo Motor Control Circuit Design (by Masaru Ishijima; translated by Xue Liang and Zhu Jianjun, by Masaru Ishijima, Xue Liang, and Zhu Jianjun)
-
Intelligent Control Technology of Permanent Magnet Synchronous Motor (Written by Wang Jun)
-
100 Examples of Microcontroller C Language Applications (with CD-ROM, 3rd Edition) (Wang Huiliang, Wang Dongfeng, Dong Guanqiang)
- Huawei's Strategic Department Director Gai Gang: The cumulative installed base of open source Euler operating system exceeds 10 million sets
- Analysis of the application of several common contact parts in high-voltage connectors of new energy vehicles
- Wiring harness durability test and contact voltage drop test method
- Sn-doped CuO nanostructure-based ethanol gas sensor for real-time drunk driving detection in vehicles
- Design considerations for automotive battery wiring harness
- Do you know all the various motors commonly used in automotive electronics?
- What are the functions of the Internet of Vehicles? What are the uses and benefits of the Internet of Vehicles?
- Power Inverter - A critical safety system for electric vehicles
- Analysis of the information security mechanism of AUTOSAR, the automotive embedded software framework
Professor at Beihang University, dedicated to promoting microcontrollers and embedded systems for over 20 years.
- Innolux's intelligent steer-by-wire solution makes cars smarter and safer
- 8051 MCU - Parity Check
- How to efficiently balance the sensitivity of tactile sensing interfaces
- What should I do if the servo motor shakes? What causes the servo motor to shake quickly?
- 【Brushless Motor】Analysis of three-phase BLDC motor and sharing of two popular development boards
- Midea Industrial Technology's subsidiaries Clou Electronics and Hekang New Energy jointly appeared at the Munich Battery Energy Storage Exhibition and Solar Energy Exhibition
- Guoxin Sichen | Application of ferroelectric memory PB85RS2MC in power battery management, with a capacity of 2M
- Analysis of common faults of frequency converter
- In a head-on competition with Qualcomm, what kind of cockpit products has Intel come up with?
- Dalian Rongke's all-vanadium liquid flow battery energy storage equipment industrialization project has entered the sprint stage before production
- Allegro MicroSystems Introduces Advanced Magnetic and Inductive Position Sensing Solutions at Electronica 2024
- Car key in the left hand, liveness detection radar in the right hand, UWB is imperative for cars!
- After a decade of rapid development, domestic CIS has entered the market
- Aegis Dagger Battery + Thor EM-i Super Hybrid, Geely New Energy has thrown out two "king bombs"
- A brief discussion on functional safety - fault, error, and failure
- In the smart car 2.0 cycle, these core industry chains are facing major opportunities!
- The United States and Japan are developing new batteries. CATL faces challenges? How should China's new energy battery industry respond?
- Murata launches high-precision 6-axis inertial sensor for automobiles
- Ford patents pre-charge alarm to help save costs and respond to emergencies
- New real-time microcontroller system from Texas Instruments enables smarter processing in automotive and industrial applications
- Is there something wrong with the application of this Zener diode?
- Protel 99 SE and AD have copper holes and copper grooves
- [RISC-V MCU CH32V103 Review] ---Advancing Wiki---RTC
- Dual-machine piezoelectric strapdown inertial navigation system based on MCU and DSP
- [AT-START-F403A Evaluation] Part 1 FreeRTOS System IAR Environment Construction
- Things you have to know about FPGA
- STM32CubeIDE imports the STM32 project automatically generated by Gizwits Online (based on the MDK environment
- Clear (set) CCS5.5 eclipse workspace record
- MSP430F5529 key interrupt scanning and pwm program
- FPGA_100 Days Journey_PS2 Design