In early October, BOE's 8.5-generation LCD (liquid crystal display) production line and TCL-controlled Huaxing Optoelectronics' 8.5-generation LCD line announced mass production. Just as the companies were singing "breaking the monopoly of foreign high-generation panel industry", Japanese and Korean companies had already shifted their investment focus to OLED (organic light-emitting display) production lines.
OLED panels are generally considered by the industry to be innovators in the next generation of TV technology because of their bright colors, small thickness, and fast response speed.
From May to June this year, Samsung announced its 5.5-generation and 8-generation AM-OLED production line plans. LG also postponed its original plan to invest in the 8.5-generation LCD production line in Guangzhou twice, and increased its investment in OLED production lines in South Korea. However, few domestic color TV giants have announced plans to put OLED production lines into production. An industry insider told this newspaper that the cost recovery period for investing in large-size LCD production lines abroad is generally 5-6 years, while domestic LCD production lines have basically not recovered their costs.
Late and loss-making mass production
"In October, CSOT will only produce a few thousand glass substrates, and in December it will produce nearly 20,000. By the end of 2012, we will successfully achieve the goal of producing 100,000 pieces per month," Chen Liyi, executive vice president of CSOT, told reporters.
CSOT, which just announced its production on August 8, created a historical record of only two months from production to mass production, while Japanese and Korean companies need half a year to a year to achieve this interval. There are other reasons for being so anxious to start mass production. "CSOT has a large loan amount and the project cannot be postponed. Because the financial interest is several million every day, in order to reduce the risk, we must shorten the construction period," said Chen Liyi. The registered capital of CSOT's 8.5-generation line project is 10 billion yuan, with TCL Group and Shenzhen Super Technology each contributing 5 billion yuan, and the remaining 14.5 billion yuan will be solved through bank loans or other financing methods. Samsung acquired 15% of CSOT's equity for 1.5 billion yuan.
Even if the production is put into operation earlier, and TCL and its investor Samsung will absorb the production capacity for CSOT, the industry rule of initial losses cannot be changed. On August 8, TCL Chairman Li Dongsheng told reporters that CSOT's budget loss this year is 200 million yuan, and TCL, which holds a 55% stake, will suffer a loss of more than 100 million yuan, "but this is a process that must be experienced during project construction."
When will Huaxing Optoelectronics be able to recover its costs, TCL's top management is unwilling to respond. Industry insiders told this newspaper, "In the business plans of domestic LCD projects, the static payback period is generally 6-8 years, but in fact, after the production line is put into operation, no project can recover its costs, at least this is the case with BOE." "On the one hand, it is because the profit margin of LCD itself is low, and now more production lines are invested, which will inevitably lower the profit margin; on the other hand, the fixed investment is large and the payback time is long. Before the payback period, we have to invest in higher-generation lines, otherwise we will fall behind. At present, the global LCD industry is in oversupply, and in 2010, all global LCD production lines were loss-making." The above-mentioned person revealed.
Data from BOE shows that the company suffered another loss of 670 million yuan in the first quarter of 2011, and the industry expects that its full-year loss may exceed the 2 billion yuan in 2010. Li Dongsheng said, "I believe that since the country is so vigorously supporting China's own LCD panel industry, it will also support LCD panel companies in terms of budget in terms of relevant national economic policies."
Speed of transformation
At a time when the government and enterprises are advocating independent innovation but struggling with the capacity and profit and loss of LCD production line investment, Japanese and Korean companies are seizing the opportunity to enter the OLED market and seize the technological commanding heights of OLED.
On May 31, Samsung announced that its 5.5-generation OLED panel production line, which it invested $2.1 billion to build in South Korea, had entered mass production two months ahead of schedule. On June 2, Samsung announced that its 8th-generation AM-OLED panel pilot line will be put into operation in May next year.
At present, OLED has become relatively mature in the field of small-size PMOLED. There are currently more than 10 PMOLED production lines in the world, mainly in the hands of companies such as Taiwan's ReTone, Japan's Pioneer, China's mainland Visionox, and Taiwan's WiseChip Optoelectronics.
Currently, only Samsung in South Korea has achieved mass production of AM-OLED. The immature technology and limited production capacity will inevitably lead to high prices.
LG Display has once again postponed its 8.5-generation LCD production line and plans to invest approximately US$2.83 billion (approximately RMB 18 billion) in mass production of OLED panels.
A media outlet quoted a research report from Taiwan's Industrial Technology Research Institute, which pointed out that "once Samsung's 8th-generation OLED production line goes into production, Taiwan's LCD panel industry will face a catastrophe. An industry with a total output value of over one trillion yuan and employing hundreds of thousands of people will be wiped out, and precision equipment costing hundreds of billions of yuan will suddenly become scrap metal. In addition, hundreds of billions of yuan in bank loans will become bad debts."
The pain of transformation
It will take until the second half of 2012 for the high-generation LCD panel production lines in mainland China to be fully operational, and it will take another 6-7 years for the assets to be depreciated. Once a breakthrough is made in large-size OLED panel technology, the pressure on the domestic panel industry can be imagined.
It is understood that Rainbow, Truly and Changhong are all planning to build small-size OLED production lines, but there is basically no output at present. At the same time, Rainbow, Changhong, BOE, Tianma and others all have plans to build large-size OLED production lines, but due to technical bottlenecks, the progress is not smooth.
Traditional TV giants such as TCL and Skyworth are following OLED technology, but it is still in the early stages. He Chengming, senior vice president of TCL Group and CEO of CSOT, said that TCL currently has a team tracking the latest OLED technology and has its own OLED experimental line, "but it does not mean that we will focus our main efforts on OLED. Our 8.5-generation line, which we invested 24.5 billion yuan in, is still the most important thing at present."
Yang Dongwen, vice president of Skyworth Group and president of the color TV business unit, told the newspaper that Skyworth Group cooperated with South China University of Technology to develop OLED technology three years ago, and the production line is still in the pilot stage.
Yang Dongwen admitted to reporters that companies are responding to the trend and want to make a good transformation, but now is the early stage of development of China's home appliance companies, with annual profit margins hovering between 2% and 3%, and most companies are still struggling on the poverty line.
Regarding the development of OLED in China, Wan Boquan, former deputy secretary-general of the China Liquid Crystal Association and consultant of Visionox, told this newspaper that technology plays a decisive role in the field of OLED, and there is no ready-made technology to introduce to the OLED industry. Wan Boquan said that the OLED industry is in the early stages of industrial development and is still in the technology-led stage, which provides my country with a very rare opportunity for breakthroughs. Due to the need for huge capital investment, the country must concentrate its efforts to support qualified enterprises in the development and industrialization of key technologies so that enterprises can expand their scale as soon as possible.
Previous article:Design of inductive capacitive touch control system from the perspective of controller
Next article:Design of non-isolated negative voltage DC/DC switching power supply
Recommended ReadingLatest update time:2024-11-16 16:55
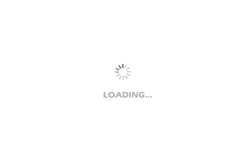
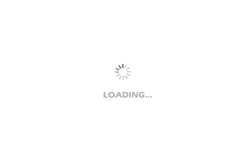
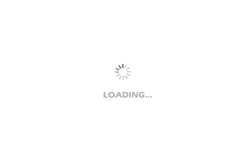
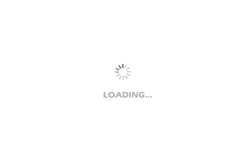
- Popular Resources
- Popular amplifiers
- MathWorks and NXP Collaborate to Launch Model-Based Design Toolbox for Battery Management Systems
- STMicroelectronics' advanced galvanically isolated gate driver STGAP3S provides flexible protection for IGBTs and SiC MOSFETs
- New diaphragm-free solid-state lithium battery technology is launched: the distance between the positive and negative electrodes is less than 0.000001 meters
- [“Source” Observe the Autumn Series] Application and testing of the next generation of semiconductor gallium oxide device photodetectors
- 采用自主设计封装,绝缘电阻显著提高!ROHM开发出更高电压xEV系统的SiC肖特基势垒二极管
- Will GaN replace SiC? PI's disruptive 1700V InnoMux2 is here to demonstrate
- From Isolation to the Third and a Half Generation: Understanding Naxinwei's Gate Driver IC in One Article
- The appeal of 48 V technology: importance, benefits and key factors in system-level applications
- Important breakthrough in recycling of used lithium-ion batteries
- Innolux's intelligent steer-by-wire solution makes cars smarter and safer
- 8051 MCU - Parity Check
- How to efficiently balance the sensitivity of tactile sensing interfaces
- What should I do if the servo motor shakes? What causes the servo motor to shake quickly?
- 【Brushless Motor】Analysis of three-phase BLDC motor and sharing of two popular development boards
- Midea Industrial Technology's subsidiaries Clou Electronics and Hekang New Energy jointly appeared at the Munich Battery Energy Storage Exhibition and Solar Energy Exhibition
- Guoxin Sichen | Application of ferroelectric memory PB85RS2MC in power battery management, with a capacity of 2M
- Analysis of common faults of frequency converter
- In a head-on competition with Qualcomm, what kind of cockpit products has Intel come up with?
- Dalian Rongke's all-vanadium liquid flow battery energy storage equipment industrialization project has entered the sprint stage before production
- Allegro MicroSystems Introduces Advanced Magnetic and Inductive Position Sensing Solutions at Electronica 2024
- Car key in the left hand, liveness detection radar in the right hand, UWB is imperative for cars!
- After a decade of rapid development, domestic CIS has entered the market
- Aegis Dagger Battery + Thor EM-i Super Hybrid, Geely New Energy has thrown out two "king bombs"
- A brief discussion on functional safety - fault, error, and failure
- In the smart car 2.0 cycle, these core industry chains are facing major opportunities!
- The United States and Japan are developing new batteries. CATL faces challenges? How should China's new energy battery industry respond?
- Murata launches high-precision 6-axis inertial sensor for automobiles
- Ford patents pre-charge alarm to help save costs and respond to emergencies
- New real-time microcontroller system from Texas Instruments enables smarter processing in automotive and industrial applications
- Improving the efficiency of microcontroller code execution
- Correctly understand the amplification region, saturation region, and cutoff region of the transistor
- [Analog Electronics Course Selection Test] + Operational Amplifier Type Application
- Detailed schematic of LTC2380-24 (preferably single-ended input to differential)
- What is the power-off mode? Generally, to save power, you just need to put it in standby mode. To exit the power-off mode, you can only do a hardware reset...
- CircuitPython 5.4.0 Beta 0 released
- Chip Manufacturing 1-Semiconductor Manufacturing Process
- ptpython A better Python REPL
- HPM6750 CAN and GPIO parallel data reading test, not implemented
- How to analyze this circuit