LED (Light Emitting Diode), also known as light-emitting diode, uses solid semiconductor chips as light-emitting materials. When a forward voltage is applied to both ends, the carriers in the semiconductor recombine, releasing excess energy and causing photon emission to produce visible light.
2. What are the advantages of LED?
★High efficiency and energy saving, only a few kWh of electricity is consumed in one thousand hours (ordinary 60W incandescent lamp consumes 1 kWh of electricity in seventeen hours, ordinary 10W energy-saving lamp consumes 1 kWh of electricity in one hundred hours)
★Super long life semiconductor chip light, no filament, no glass bulb, not afraid of vibration, not easy to break, the service life can reach 50,000 hours (the service life of ordinary incandescent lamp is only 1,000 hours, and the service life of ordinary energy-saving lamp is only 8,000 hours)
★ Healthy light does not contain ultraviolet and infrared rays, and does not produce radiation (ordinary light contains ultraviolet and infrared rays)
★ Green and environmentally friendly, does not contain harmful elements such as mercury and xenon, is conducive to recycling and utilization, and does not generate electromagnetic interference (ordinary lamps contain elements such as mercury and lead, and the electronic ballast in energy-saving lamps will generate electromagnetic interference)
★ Protect eyesight DC drive , no flicker (ordinary lights are AC driven, which will inevitably produce flicker)
★ High light efficiency , low heat generation: 90% of the electrical energy is converted into visible light (for ordinary incandescent lamps, 80% of the electrical energy is converted into heat energy, and only 20% of the electrical energy is converted into light energy)
★ High safety factor, small voltage and current required, low heat generation, no potential safety hazard, can be used in dangerous places such as mines
★ Huge market potential Low voltage, DC power supply, battery, solar power supply is sufficient, can be used in remote mountainous areas and outdoor lighting and other places where there is a lack of electricity or insufficient electricity.
3. Authoritative prediction
Semiconductor lighting will replace existing traditional light sources in the next 5-10 years.
"In the future, white light LEDs will be cheaper and the overall market capacity will grow rapidly." Xu Zhipeng optimistically pointed out that according to the US Department of Energy's forecast, around 2010, 55% of incandescent and fluorescent lamps in the United States will be replaced by LEDs, which may form a $50 billion industry. Japan has proposed that LEDs will replace traditional incandescent lamps on a large scale this year. Japan, the United States, Europe, South Korea and other countries have officially launched LED lighting strategic plans.
The U.S. Department of Energy predicts that by around 2010, 55% of incandescent and fluorescent lamps in the United States will be replaced by semiconductor lamps, which are luminous bodies embedded in chips. Japan plans to replace 50% of traditional lighting fixtures with such semiconductor lamps by 2008. Scientists have found that at the same brightness , LEDs consume only 1/10 of the power of incandescent lamps, and their lifespan is 100 times that of incandescent lamps. Experts call LEDs another leap forward in the history of human lighting after incandescent and fluorescent lamps, due to their advantages of energy saving, environmental protection, long life, and small size. According to the U.S. Department of Energy (DOE), the complete replacement of traditional lighting devices will start in 2010, but many LED suppliers hope to bring this start time forward by one to two years.
4. Following Australia, the EU wants to ban incandescent bulbs within two years
On March 9, 2007, strings of colorful lights flickered on the streets of London, England. The EU summit that just ended passed a series of measures aimed at improving energy efficiency. The EU spring summit that ended on the 9th has reached an agreement that within two years, European countries will gradually replace old-fashioned incandescent bulbs with energy-saving fluorescent lamps to reduce greenhouse gas emissions. Prior to this, Australia had taken the lead in passing a law to stop using incandescent bulbs.
5. LED lighting output value will exceed 100 billion US dollars, Tongfangzheng is making efforts
Sun Min, vice president and secretary of Tongfang Co., Ltd., recently revealed to reporters that the company's high-brightness LED lighting project has basically achieved industrialization. Currently, 20 production lines have been put into production. Its industrialization technology has reached the world's advanced level. It is planned that by the end of 2008, the number of production lines will reach 50, forming a scale effect of green lighting. It is estimated that the scale of China's application market will reach 54 billion yuan in 2008. By 2010, the output value of China's semiconductor lighting and related industries will exceed 100 billion US dollars, of which the domestic growth rate of high-brightness chips will be as high as 100%.
6. Seoul Semiconductor Expects to capture a $100 billion share of the global lighting market.
Seoul Semiconductor of South Korea is now planning to replace traditional lighting lamps with LEDs. The current Acrylic brightness of 60 lumens /watt will be increased by 50% to 80 lumens/watt in the fourth quarter of 2007, with each module having 250 lumens; and to 120 lumens/watt in the fourth quarter of 2008, with each module having 400 lumens. It hopes to gain a share of the $100 billion global lighting market.
7. Australia and New Zealand will be the first to stop using incandescent light bulbs
The Australian government recently announced that in order to reduce greenhouse gas emissions, Australia will ban the use of incandescent lamps except for medical purposes. By 2012, Australia will reduce greenhouse gas emissions by 4 million tons.
According to a report in The Dominion Post on February 21, 2007, New Zealand Energy Minister David Parker suggested that New Zealand should also follow Australia's practice and ban the use of ordinary incandescent light bulbs in the next two to three years and replace them with energy-saving and environmentally friendly fluorescent bulbs (Florescent Eco Bulb). Australian Environment Minister Malcolm Turnbull said that Australia will implement new civil lighting standards in 2010, and through the implementation of the new standards, greenhouse gas emissions can be reduced by 4 million tons in 2012.
It is reported that this new fluorescent bulb is mainly imported from China.
8. Why LED is the first choice for corridor lights
1. At present, the price of LED is still relatively high. Corridor lights are shared facilities, so everyone can accept it if they share the cost.
2. Incandescent lamps are now commonly used in corridor lamps. If they are replaced with LED lamps , the energy saving effect will be particularly obvious.
3. The corridor lights are off during the day. They are frequently turned on and off at night. Not to mention energy-saving lamps, even incandescent lamps will be worn out very quickly. However, LED lamps are not afraid of this because their light-emitting mechanism is different from that of incandescent lamps and energy-saving lamps. They are very suitable for high-speed switching working conditions and will never be damaged for this reason.
4. The life of LED lamps is very long, which eliminates the embarrassing situation that corridor lights often need maintenance.
5. The property management pays for the electricity for the corridor lights. The investment is a one-time one. Saving 80% of the electricity bill is a long-term benefit, which is the most cost-effective for the property management department.
9. Can LED lights directly replace the current corridor lights?
No. Since the corridor lights that everyone uses now are incandescent lamps, they cannot be replaced by LED lamps or energy-saving lamps. Therefore, if you want to replace LED lamps, you must also replace them with sound and light control switches. Now there are special integrated LED sound and light control corridor lights, which directly use 220V mains electricity and are very convenient to use. We will strongly recommend that the voltage of corridor lights be DC 24V. We will introduce its benefits and reasons in another article. With the development of technology and the reduction of costs, it is inevitable that LED lamps will replace energy-saving lamps.
10. Classification and characteristics of LED driver power supply
1. According to the driving mode, it can be divided into two categories:
(1) Constant current type:
a. The output current of the constant current drive circuit is constant, but the output DC voltage varies within a certain range with the size of the load resistance. The smaller the load resistance, the lower the output voltage, and the larger the load resistance, the higher the output voltage.
b. The constant current circuit is not afraid of load short circuit, but it is strictly forbidden to have a completely open load.
c. Constant current drive circuit is ideal for driving LED, but the price is relatively high.
d. Pay attention to the maximum current and voltage used, which limits the number of LEDs used;
(2) Voltage stabilization type:
a. When the parameters in the voltage stabilization circuit are determined, the output voltage is fixed, but the output current changes with the increase or decrease of the load;
b. The voltage stabilizing circuit is not afraid of open-circuit load, but it is strictly forbidden to completely short-circuit the load.
c. Use a voltage-stabilizing drive circuit to drive the LED. Each string needs to be added with a suitable resistor to make each string of LEDs display an even brightness;
d. Brightness will be affected by changes in voltage from rectification.
2. Classification by circuit structure
(1) Resistor and capacitor voltage reduction method: When using capacitors to reduce voltage, the instantaneous current passing through the LED is extremely large due to the effect of charging and discharging, which can easily damage the chip. It is easily affected by grid voltage fluctuations, and the power supply efficiency and reliability are low.
(2) Resistor step-down method: The voltage is stepped down by resistors, which is greatly affected by the voltage changes of the power grid. It is not easy to make a voltage-stabilized power supply. The voltage-stepping resistor consumes a large part of the energy. Therefore, the power efficiency of this power supply method is very low, and the reliability of the system is also low.
(3) Conventional transformer step-down method: The power supply is small in size, heavy in weight, and has a low power efficiency, generally only 45% to 60%, so it is rarely used and has low reliability.
(4) Electronic transformer step-down method: The power supply efficiency is low, the voltage range is not wide, generally 180~240V, and the ripple interference is large.
(5) RCC step-down method Switching power supply : The voltage regulation range is relatively wide and the power efficiency is relatively high, generally reaching 70% to 80%, and it is widely used. Since the oscillation frequency of this control method is discontinuous, the switching frequency is not easy to control, the load voltage ripple coefficient is also relatively large, and the adaptability to abnormal loads is poor.
(6) PWM control switching power supply: It mainly consists of four parts, input rectification and filtering part, output rectification and filtering part, PWM voltage regulation control part, and switch energy conversion part. The basic working principle of PWM switching voltage regulation is that when the input voltage, internal parameters and external load change, the control circuit performs closed-loop feedback through the difference between the controlled signal and the reference signal, adjusts the pulse width of the main circuit switch device, and makes the output voltage or current of the switching power supply stable (that is, the corresponding voltage-regulated power supply or constant current power supply). The power supply efficiency is extremely high, generally 80% to 90%, and the output voltage and current are stable. Generally, this circuit has perfect protection measures and is a high-reliability power supply.
From the above introduction, it can be seen that the LED power supply designed by PWM control method is a relatively ideal LED power supply. At present, the "Jinxing" brand LED switching power supply produced by Zhuhai Nanyuxing Electronics Co., Ltd. is a switching power supply with PWM control technology. This type of LED power supply has been reported by users to have a very good effect.
1. High start-up costs
Lighting costs involve not only the initial cost of the lamp, but also the energy cost consumed by the lamp, the labor cost required to replace the lamp when the lamp does not work properly, and the average frequency of lamp replacement. From this concept, it is easy to understand why the market for LED traffic lights began to take off when the price of LED light sources was about 50 times that of incandescent light sources, and when it reached 28 times, it had already formed a new industry. At present, semiconductor lighting is mainly based on light color lighting and special lighting, and will expand to general lighting in the future. Specifically, in recent years, the semiconductor lighting market will be widely used in various signal lights, landscape lighting, window lighting, architectural lighting, beautification of squares and streets, home decorative lighting, beautification of public entertainment venues and stage effect lighting. In fact, it can be seen everywhere around us: computer display lights, backlight sources of mobile phone buttons and screens, car taillights, building lights, traffic lights... and so on.
2. Problems caused by inconsistency:
In theory, all LEDs are the same, they are all diodes that can emit light, but in reality, the electrical properties of all LEDs are different, and many manufacturers are competing to meet production schedules and meet quantity requirements; the production processes of each manufacturer are inconsistent, and even vary greatly, even the processes of the same manufacturer at different times are different; the purity requirements of semiconductor materials used to produce light-emitting diodes are very high, and the purity of semiconductor raw materials used by different manufacturers is different, which makes the LED's luminous intensity and driving current not completely the same, or very different, and the difference in overcurrent resistance and heat generation is naturally different; due to the differences in packaging processes and packaging materials, the overall heat dissipation capacity is different, and all manufacturers are researching and developing new materials to solve the problems of thermal expansion and heat dissipation of combined materials. It is not difficult to see that there are still great differences between individual LEDs in the short term. If each lamp uses only one LED, it is very easy to control and has a truly long life, such as the power indicator light on a TV or DVD. When we use LEDs to make lighting fixtures, we do not use a single LED, but multiple, or hundreds or thousands of LEDs arranged in an array to connect to the circuit. Moreover, the required brightness is not what an indicator light can achieve, and the brightness will be reduced if the current is too large or too small, and the life span will be greatly reduced, and even broken before leaving the factory. Because the differences of LEDs always exist, in a connection composed of multiple LEDs, when several are broken (usually short-circuited), the current will increase and damage other LEDs. This is the result of the inconsistency band, and it is also one of the factors that restrict its development.
3. The driving circuit is complex, costly and has a high failure rate
a. In terms of voltage matching, LEDs are not like ordinary incandescent bulbs that can be directly connected to 220V AC power. LEDs are driven by a low voltage of 2-3 volts, so complex conversion circuits must be designed. Different LED lamps for different purposes must be equipped with different power adapters.
b. In terms of current supply, the normal working current of LED is 15mA-18mA. When the supply current is less than 15mA, the luminous intensity of LED is not enough. When it is greater than 20mA, the luminous intensity will also weaken, and the heat will increase greatly, aging will accelerate, and the life will be shortened. When it exceeds 40mA, it will be damaged quickly. In order to extend the service life of LED lighting, simple power supply cannot be used, and commonly used integrated circuit power supply, electronic transformer, separation component power supply, etc., but they all need to design constant current source circuit and constant voltage source circuit power supply mode. When driving with large current, it is necessary to match high power tube or thyristor device, plus protection circuit, so that the power supply circuit of LED is very complicated and the failure rate increases. Component cost, production cost and service cost will all increase. At present, the cost of LED itself is high, plus the cost of power supply, which greatly limits the market competitiveness and purchasing group, and the advantages of LED lighting are greatly reduced. This is also another key issue restricting its development and popularization.
4. Solutions to the problem and feasibility analysis:
The solution to the problem is to use a self-resetting overcurrent protector WHPTC element
If the WHPTC overcurrent protector is used for protection, it will be another result. From the principle, it can be known that when the current of the circuit exceeds the specified value, it will automatically protect quickly, and automatically reset after the fault is eliminated, without manual replacement. For LEDs, voltage changes are not the direct cause of LED damage, but the increase in current is the real killer of LEDs. Obviously, using this feature of WHPTC has an absolute advantage in LED circuit protection, making simple power supply a reality. Practice has proved that it can effectively protect the LED circuit before it fails. This advantage is particularly prominent in simple power supplies. As can be seen from the analysis of the following 3 figures, with WHPTC, constant current and constant voltage circuits can be omitted, and the quality of LEDs is also improved. Device costs, production costs, failure rates, service costs, etc. are greatly reduced. It also greatly increases the market competitiveness of products. So whoever uses WHPTC first will occupy the market first.
Comparison of topological structures before and after using WHPTC
A brief discussion on LED product aging When we use LED, we often encounter this kind of problem. When the LED is welded on the product, it works normally at the beginning, but after lighting for a period of time, it will appear dim light, flicker, malfunction, intermittent light, etc., causing serious damage to the product. The reasons for this phenomenon are roughly:
1. When applying the product, there are problems with the welding process, such as too high welding temperature, too long welding time, and failure to do a good job of anti-static work. More than 95% of these problems are caused by the packaging process.
2. The quality of the LED itself or the production process. Prevention methods include:
1. Control the welding process well.
2. Perform aging test on the product .
Aging is an important guarantee for the reliability of electronic products and is the last essential step in product production. LED products can improve their performance after aging, and help stabilize their performance in later use. LED aging test is a very important link in product quality control, but it is often overlooked and cannot be properly and effectively aged. LED aging test is a countermeasure taken based on the characteristics of the product's failure rate curve, namely the bathtub curve, to improve product reliability, but this method is not necessary. After all, aging test is at the expense of the life of a single LED product.
LED aging methods include constant current aging and constant voltage aging. A constant current source means that the current is constant at any time. If there is a frequency problem, it is not a constant current. It is an AC or pulsating current. An AC or pulsating current source can be designed to have a constant effective value, but this power source cannot be called a "constant current source". Constant current aging is the most consistent with the current working characteristics of LEDs. Overcurrent impact aging is also a new aging method adopted by manufacturers. By using a constant current source with adjustable frequency and current for this type of aging, the quality and expected life of the LED can be judged in a short time, and many hidden dangers that cannot be picked out by conventional aging can be picked out. Effectively prevent high temperature failure-PTC thermistor used as LED current limiter In recent years, the development of light-emitting diodes (LEDs) has made great progress: from being used purely as indicator lights to high-power LEDs with a light output of more than 100 lumens . Soon, the cost of LED lighting will drop to a level similar to that of traditional cold cathode fluorescent lamps ( CCFLs ). This has led to a growing interest in LEDs for automotive lighting, LED light sources inside and outside buildings, and backlighting for laptop or TV LCD screens. The development of high-power LED technology has increased the requirements for heat dissipation during the design phase. Like all other semiconductors, LEDs must not overheat, lest their output degrades rapidly or, in the worst case, fail completely. Although high-power LEDs have a higher efficiency than incandescent lamps, a significant portion of the input power is converted into heat rather than light. Reliable operation therefore requires good heat dissipation and requires that high temperatures be considered during the design phase. Temperature must also be taken into account when dimensioning the LED driver circuit : its forward current must be chosen so that the LED chip does not overheat even at the maximum ambient temperature. As the temperature rises, it is necessary to reduce the temperature by reducing the maximum allowable current, i.e., by derating the rated value. LED manufacturers include derating curves in their product specifications. Such curves are shown in Figure 1.
Figure 1 LED frequency reduction curve
There are drawbacks to operating LEDs with a power supply that is not temperature-dependent: in the high temperature region, the LEDs operate outside the specification range. In addition, when in the low temperature region, the lighting source is powered by a current that is significantly lower than the maximum allowable current (see the red curve in Figure 1). As shown in the green curve in Figure 1, controlling the LED current through a positive temperature coefficient thermistor (PTC thermistor for short) in the LED driver circuit is a major improvement. This can bring at least the following benefits:
* Increased forward current at room temperature, thereby increasing light output
*Because the number of LEDs used can be reduced, a lower-priced driver integrated circuit (IC) or even a driver circuit without temperature management can be used to save costs
*Realize the design of driving circuit without IC control, this circuit can also make the LED current change with temperature
*Can use cheaper LEDs with higher derating values and smaller safety margins
* Overheat protection function improves reliability
*Thermomechanical design with heat sink is simpler
Most LED drive circuits have one thing in common: the forward current flowing through the LED is set by a fixed resistor (see Figure 2). Generally speaking, the current flowing through the LED ILED depends on Rout, that is, ILED ~ 1/Rout. Since Rout does not change with temperature, the LED current is also not affected by temperature.
Temperature management of the LED current can be achieved by replacing the fixed resistor with a temperature-dependent circuit. The following diagram illustrates how a standard circuit can be improved using a PTC thermistor.
Example 1: Constant Current Source with Feedback Loop
Circuit 1 in Figure 2 is a commonly used drive circuit. Its constant current source includes a feedback loop. When the feedback voltage across the regulating resistor reaches VFB, which varies depending on the IC, the LED current remains unchanged. The LED current is thus stabilized at ILED = VFB/Rout.
Figure 2 Traditional LED driving method
Figure 3 shows an improved version of the previous circuit: This circuit uses a PTC thermistor to generate a temperature-dependent LED current. By properly selecting the PTC thermistor, Rseries, and RparallEL, this circuit matches the dedicated driver IC and LED combination. The LED current can be calculated using the following equation:
The circuit shown in Figure 3 illustrates the temperature dependence of the LED current (see Figure 3). Compared to a constant current source designed for a maximum operating temperature of 60 degrees, the LED current can be increased by up to 40% between 0 and 40 degrees by using a PTC thermistor, and the LED brightness can be increased by the same percentage.
Figure 3 Temperature monitoring and current frequency reduction using PTC thermistors
Example 2: Constant current source with no series connection between resistor and LED
Circuit 2, Figure 2, is another common constant current source circuit: the current is determined by the resistor connected to the driver IC. In this case, however, the adjustment resistor is not connected in series with the LED. The ratio between Rset and ILED is determined by the IC specifications. Therefore, with a 20KΩ series resistor and a TLE4241G driver IC, the resulting LED current is 30mA. Figure 4 shows a modification of the standard circuit, which also includes a PTC thermistor, although a WHPTC thermistor is used here. In sensing temperature, the component resistance can reach 4.7KΩ, and the permissible error value is ±5℃ (standard series) or ±3℃ (precision series with permissible error value).
Figure 4 shows the LED current as a function of the ambient temperature. The fixed resistor Rseries has a small tolerance and dominates the total resistance at low temperatures. Only at about 15 K below the sensing temperature of the PTC thermistor does the current begin to decrease as the resistance of the PTC thermistor begins to increase. The current is about 23 mA at the sensing temperature (total resistance = Rseries + RPTC = 19.5 KΩ + 4.7 KΩ = 24.2 KΩ). The PTC resistance rises sharply at higher temperatures, quickly causing a short circuit, thus avoiding failure due to overtemperature.
Figure 4 Temperature recording without shunt measurement
Example 3: Simple driver circuit without IC
As shown in Figure 2, circuit 3, the LED can also operate without a driver IC. The circuit shown is to drive a single 200mA LED from a car battery. The regulator generates a stable supply voltage Vstab of 5 V to avoid fluctuations in the supply voltage. The LED operates at Vstab and the current is determined by the resistor element Rout in series with the LED. In this type of circuit, the temperature-independent forward current can be calculated by the following equation, where VDiode is the forward voltage of an LED:
Another approach is to combine a radial lead PTC thermistor of WHPTC and two fixed resistors to replace the above fixed resistors, as shown in the figure.
Since the majority of the LED current flows through the PTC thermistor itself, a larger radial leaded component needs to be selected. The PTC will heat up due to the current flowing through the resistor itself, and will therefore always reduce the current, regardless of the ambient temperature (see Figure 5). Connecting two or more chip PTC thermistors in parallel will split the current, but this solution still has limitations.
Figure 5 Temperature compensation drive circuit without IC
The current value is mainly set by the appropriate choice of two fixed resistors. These two resistors also play an important role in improving the circuit because they keep the tolerance of the generated LED forward current to a low level. This is especially important in the normal operating temperature range, where the resistance tolerance of the PTC thermistor itself is still high. The second parallel fixed resistor also ensures that the PTC does not completely shut down the LED in extremely high temperature conditions, so the current does not drop below the value calculated by the following equation:
This performance is extremely important in applications such as automotive electronics , where safety requirements do not allow the lights to be completely switched off.
Background information: Temperature dependence of LEDs
Like all semiconductors, the maximum permissible junction temperature of LEDs must not be exceeded to avoid premature aging or complete failure. If the junction temperature is to be kept below a critical value, the maximum permissible forward current must decrease as the ambient temperature increases. However, if a heat sink is used, the forward current can be increased at a specific ambient temperature. The light output of LEDs decreases as the chip junction temperature increases. This is mainly the case for red and yellow LEDs, while white LEDs are less temperature-dependent. The luminous efficiency and forward current increase in tandem, but the high thermal resistivity of the LED mounted between the junction and the environment can reduce or even reverse this effect, because the emitted light decreases as the junction temperature increases.
In addition, when the junction temperature rises and the LED forward voltage keeps increasing in sync with the temperature, the main wavelength of the emitted light will increase at a typical rate of +0.1 nm/K. Evaluation of various white light LED drive circuit characteristics In 1996, after Mr. Nakamura of Nichia Chemical discovered blue light LED , white light LED was regarded as the component with the most development potential for lighting sources. Therefore, the improvement of white light LED performance and commercial application immediately became the focus of research in various countries. At present, white light LEDs have been used in public place sidewalk lights, automotive lighting, traffic signs, portable electronic products, liquid crystal displays and other fields. Since white light LEDs also have the characteristics of rich three primary colors, color temperature and high luminous efficiency, they are generally considered to be very suitable for backlighting sources of liquid crystal displays. Therefore, various manufacturers have successively launched white light LED dedicated drive circuits and related components. In view of this, this article briefly explains the characteristics of LED dedicated drive circuits and future development trends. 1 Reasons for constant current drive
1.1 The luminosity of white LEDs is regulated by forward current
The forward voltage of white light LEDs is usually regulated to a minimum of 3.0V and a maximum of 4.0V at 20mA. That is, if a certain forward voltage is simply applied, the forward current will vary over a wide range.
Figure 1 shows the results of testing the forward voltage and forward current characteristics of three types of white light LED samples randomly selected from the products of LED companies A and B. According to the test results, if the six types of white light LEDs are driven by a forward voltage of 3.4V, the forward current will vary greatly within the range of 10~44mA. Table 1 shows the electrical and optical characteristics of white light LEDs.
Since the luminosity and chromaticity of white light LEDs are measured using a constant current method, they are usually driven with a constant current to obtain the expected brightness and chromaticity.
Table 2 shows the ranks of optical coordinates (IF=25mA, Ta=250C).
1.2 Avoid forward current exceeding the allowable current value
To ensure the reliability of white light LEDs, it is basically necessary to try to prevent the forward current from exceeding the absolute maximum design value (rated value) of the white light LED.
In Figure 2, the maximum forward current of a white light LED is 30mA. As the ambient temperature rises, the allowable forward current continues to decrease. If the ambient temperature is 50°C, the forward current cannot exceed 20mA. In addition, it is difficult to control the current value flowing into the LED using a constant voltage drive method, so the reliability of the LED cannot be maintained.
2. Driving method of white light LED
Figure 3 shows four commonly used power supply circuits for driving white light LEDs ; Figure 4 shows the Regulation accuracy characteristics of the above six randomly sampled white light LEDs after stabilization.
The test results in Figure 4 show that the load characteristics of the ReguLator appear at the VF corner of the white light LED, that is, the intersection point in the figure is the stable operating point of each white light LED.
2.1 How to drive the voltage regulator
The circuit in Figure 3 (a) uses a voltage regulator and a BaLLast resistor to control the LED current. The advantage of this circuit is that there are many types of voltage regulators, the designer has more freedom to choose, and there is only one point of contact between the voltage regulator and the LED. The disadvantage is that the power loss caused by the BaLLast will lead to deterioration of efficiency. In addition, the forward current of the LED cannot be precisely controlled.
As can be seen in Figure 4 (a), the forward current of six randomly sampled white light LEDs has a wide distribution range from 14.2mA to 18.4mA, so the (average) forward current of the LED of manufacturer A is as high as 2.0mA. In contrast, although the ReguLator used in the circuit of Figure 4 (b) has the advantages of small size and low cost, its disadvantage is that it may not meet the requirements of performance and reliability, which means that the practicality of this circuit is relatively weak.
2.2 Voltage Regulator drive method using constant current output
Although the circuit in Figure 3 (b) can stabilize all currents flowing into the LEDs, a group of BaLLast resistors are specially set in the circuit to match the electrical characteristics of each LED.
The MAX1910 in Figure 3 (b) is a constant current output type voltage regulator. Although this circuit uses white light LEDs from the same manufacturer and the same lot number (Lot), it has achieved excellent matching. However, when using LEDs from different manufacturers and lots, there will be a large difference in the distribution of characteristics. This current regulator uses a similar method to Figure 3 (a) to control the drive current, but it can reduce the power consumption of the Ballast resistor by about half.
The test results in Figure 4 (b) show that the current flowing into the six randomly sampled white light LEDs varies greatly from 15.4mA to 19.6mA. Therefore, the LEDs of both manufacturers A and B are driven with an average current of 17.5mA. The disadvantages of this circuit are that the power loss caused by the BaLLast resistor may remain, and the matching of the LED current cannot be achieved; however, overall, this circuit has both action characteristics and simplicity, so it has considerable use value.
2.3 Driving method using output type MuLti PuLL current regulator
The circuit of Figure 3 (c) can stabilize the current flowing into the LEDs, so there is no need to use a Ballast resistor, and the accuracy and matching of the current ReguLator are dominated by the respective current ReguLator.
The MAX1570 IC in Figure 3(c) can achieve the above current regulation to achieve the current accuracy of 2% standard and the current matching of 0.3% standard.
The current regulator composed of MAX1570 IC is a low drop-out type, so its operation efficiency is very high. The test results of Figure 4 (c) show that when the driving circuit of Figure 3 (c) is used, the current flowing into the six randomly sampled white light LEDs is stabilized to 17.5mA.
Although four connection terminals are required between the ReguLator and the LED, this circuit does not require a Ballast resistor, so the package area can be effectively suppressed. This makes it very suitable for applications such as small LCD panels where the package space is extremely narrow .
2.4 Using boost current regulator drive method
The circuit in Figure 3 (d) uses an inductor that can stabilize the current to form a so-called high-efficiency step-up converter. The biggest feature of this circuit is the Feed Back ThreshoLd voltage, which can reduce the power loss of the current detection resistor. In addition, the LEDs are connected in series, so the current flowing into the white light LED can be fully matched with the LED even under various requirements. The accuracy of the current basically depends on the Feed Back ThreshoLd accuracy of the Regu-Lator, so it will not be affected by the forward voltage of the LED.
The efficiency (PLED/PIN) of the current regulator composed of MAX1848 and MAX1561 ICs is: three LEDs + MAX1848, 87%; six LEDs + MAX-1561, 84%.
Another advantage of the Step Up Converter is that two connection terminals are required between the Regu-Lator and the LED, and the number of LEDs used will not be affected by the type of Step Up Converter, which means that designers will have more choices. Therefore, the Step Up Converter is widely used in LCD panels of various sizes; the disadvantages of the circuit are the height of the inductor, the high cost of the components, and EMI radiation interference.
3 Conclusion
The above introduces the commonly used driving circuits for white light LEDs, and explores the advantages, disadvantages and characteristics of each circuit in actual operation through experiments. Due to the limitations of LED structure, there are problems such as difficulty in controlling wavelength and driving current accuracy. With the increasing demand for white light LED backlight modules , how to improve the above wavelength and current accuracy problems and reduce the production cost of driving circuits have become problems that must be overcome.
Previous article:Digital LED-driven street lighting system
Next article:A new LED energy-saving street light control solution
Recommended ReadingLatest update time:2024-11-17 03:28
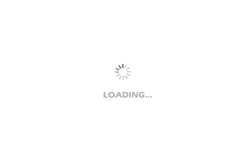
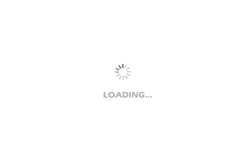
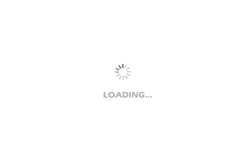
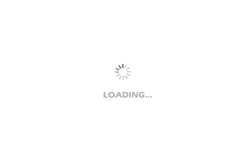
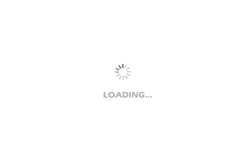
- Popular Resources
- Popular amplifiers
- MathWorks and NXP Collaborate to Launch Model-Based Design Toolbox for Battery Management Systems
- STMicroelectronics' advanced galvanically isolated gate driver STGAP3S provides flexible protection for IGBTs and SiC MOSFETs
- New diaphragm-free solid-state lithium battery technology is launched: the distance between the positive and negative electrodes is less than 0.000001 meters
- [“Source” Observe the Autumn Series] Application and testing of the next generation of semiconductor gallium oxide device photodetectors
- 采用自主设计封装,绝缘电阻显著提高!ROHM开发出更高电压xEV系统的SiC肖特基势垒二极管
- Will GaN replace SiC? PI's disruptive 1700V InnoMux2 is here to demonstrate
- From Isolation to the Third and a Half Generation: Understanding Naxinwei's Gate Driver IC in One Article
- The appeal of 48 V technology: importance, benefits and key factors in system-level applications
- Important breakthrough in recycling of used lithium-ion batteries
- Innolux's intelligent steer-by-wire solution makes cars smarter and safer
- 8051 MCU - Parity Check
- How to efficiently balance the sensitivity of tactile sensing interfaces
- What should I do if the servo motor shakes? What causes the servo motor to shake quickly?
- 【Brushless Motor】Analysis of three-phase BLDC motor and sharing of two popular development boards
- Midea Industrial Technology's subsidiaries Clou Electronics and Hekang New Energy jointly appeared at the Munich Battery Energy Storage Exhibition and Solar Energy Exhibition
- Guoxin Sichen | Application of ferroelectric memory PB85RS2MC in power battery management, with a capacity of 2M
- Analysis of common faults of frequency converter
- In a head-on competition with Qualcomm, what kind of cockpit products has Intel come up with?
- Dalian Rongke's all-vanadium liquid flow battery energy storage equipment industrialization project has entered the sprint stage before production
- Allegro MicroSystems Introduces Advanced Magnetic and Inductive Position Sensing Solutions at Electronica 2024
- Car key in the left hand, liveness detection radar in the right hand, UWB is imperative for cars!
- After a decade of rapid development, domestic CIS has entered the market
- Aegis Dagger Battery + Thor EM-i Super Hybrid, Geely New Energy has thrown out two "king bombs"
- A brief discussion on functional safety - fault, error, and failure
- In the smart car 2.0 cycle, these core industry chains are facing major opportunities!
- Rambus Launches Industry's First HBM 4 Controller IP: What Are the Technical Details Behind It?
- The United States and Japan are developing new batteries. CATL faces challenges? How should China's new energy battery industry respond?
- Murata launches high-precision 6-axis inertial sensor for automobiles
- Ford patents pre-charge alarm to help save costs and respond to emergencies
- Double-layer board, PCB charges?
- Power Development Tutorial: Summary of topology transformation calculation formulas
- Switching Power Supply Interest Group 15th Task
- Omron E6A2
- ADI Think Tank Secrets New Release丨High Speed Circuit Design Guide is now available for download
- undefined reference to `cv_bridge::toCvShare
- [ESP32-S2-Kaluga-1 Review] MQTT component connection to OneNet
- Review summary: RTT & Renesas high-performance CPK-RA6M4 development board
- Two methods of chip unpacking
- MSP430FR25x2 Capacitive Touch Sensing Mixed-Signal Microcontrollers