1. What is pressure?
Pressure is the force exerted by a fluid on its surroundings per unit area. For example, pressure P is a function of force F and area A.
A container filled with gas contains countless atoms and molecules that are constantly hitting the walls of the container. The pressure is the average of the forces per unit area of the container wall from these atoms and molecules. Furthermore, pressure does not have to be measured along the walls of the container; it can be measured as the force per unit area on any flat surface. For example, air pressure is a function of the weight of air pressing down on the ground. Therefore, the higher the altitude, the lower the pressure. Similarly, the deeper a diver or submarine goes into the ocean, the greater the pressure.
The SI unit of pressure is the Pascal (N/m2), but other common pressure units include pounds per square inch (PSI), atmospheres (atm), bar, inches of mercury (in Hg), and millimeters of mercury (mm Hg).
Pressure measurements can be classified as static or dynamic. Static pressure is the pressure when there is no motion. Examples of static pressure include the pressure inside a balloon or the pressure of water in a basin. Often, the movement of a fluid changes the forces it exerts on its surroundings. This type of pressure measurement is called dynamic pressure measurement. For example, the pressure inside a balloon or at the bottom of a basin will change as you release the air from the balloon or pour out the water from the basin.
Pressure head (pressure head) measures the static pressure of a liquid in a tank or pipe. The pressure head P is a function of the height h and weight density w of the liquid being measured, as shown in Figure 1.

Figure 1. Pressure head measurement
The pressure experienced by a diver in the ocean is equal to the diver's depth multiplied by the weight of the ocean (64 pounds per cubic foot). A diver diving 33 feet deep is experiencing 2,112 pounds of water per square foot of his body, which equals 14.7 PSI. Interestingly, the atmospheric pressure at sea level is also 14.7 PSI or 1 atm. Therefore, 33 feet of water creates the same pressure as 5 miles of air! The total pressure experienced by a diver diving 33 feet deep is equal to the weight of the air plus the pressure created by the water, which is 29.4 PSI or 2 atm.
Pressure measurements can be further described by the type of measurement being made. There are three types of pressure measurements: absolute, gauge, and differential. Absolute pressure is the pressure in a vacuum (Figure 2). Absolute pressure is often described using the abbreviations PAA (Pascals Absolute) or PSIA (Pounds per Square Inch Absolute).

Figure 2. Absolute pressure sensor [3]
Gage pressure is the pressure relative to the ambient atmospheric pressure (Figure 3). Similar to absolute pressure, gauge pressure is often described using the acronyms PAG (Pascals Gauge) or PSIG (pounds per square inch gauge).

Figure 3. Gauge pressure sensor [3]
Differential pressure is similar to gauge pressure, but instead of measuring ambient atmospheric pressure, it measures a specific reference pressure (Figure 4). Differential pressure is often described using the acronyms PAD (Pascals Differential) or PSID (Pounds per Square Inch Differential).
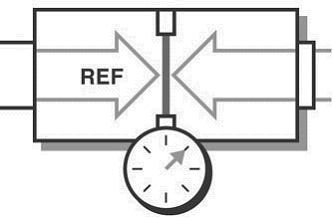
Figure 4. Differential pressure sensor [3]
Back to top
2. Pressure sensor
There are many different types of pressure sensor designs because of the wide variety of conditions, ranges, and materials that must be measured for pressure. Pressure is usually converted to some intermediate form, such as displacement. The sensor then converts the displacement into an electrical output, such as voltage or current. The three most common types of pressure sensors are strain gages, variable capacitors, and piezoelectric sensors.
Of all the pressure sensors, the Wheatstone bridge (strain-based) sensor is the most common, providing solutions that meet different accuracy, size, ruggedness, and cost requirements. Bridge sensors can measure absolute, gauge, or differential pressure for both high- and low-pressure applications. All bridge sensors use a strain gage and a diaphragm (Figure 4).

Figure 4. Cross section of a typical strain gauge pressure sensor [3]
When changes in pressure cause the diaphragm to deflect, the resistance of the strain gauge changes accordingly, which can be measured by a data acquisition (DAQ) system. These strain gauge pressure sensors are classified into different types: bonded strain gauges, sputtered strain gauges, and semiconductor strain gauges.
Bonded strain gauge pressure sensors are made by actually bonding a metal foil strain gauge to the surface where the strain is to be measured. These bonded foil strain gauges (BFSGs) have been the industry standard for many years and continue to be used primarily because of their fast 1000 Hz response time to pressure changes and their wide operating temperature range.
Sputtered strain gauge manufacturers sputter a layer of glass onto a diaphragm and then deposit a thin layer of metal strain gauge onto the sensor diaphragm. Sputtered strain gauge sensors actually form a molecular bond between the strain gauge element, the insulating layer, and the sensing diaphragm. These instruments are best suited for long and difficult measurement conditions.
Integrated circuit manufacturers have developed composite pressure sensors that are very easy to use. These devices generally use a semiconductor diaphragm on which a semiconductor strain gauge and temperature compensation sensor are placed. Appropriate signal conditioning is also included in the form of an integrated circuit to provide a dc voltage or current that is linearly proportional to pressure over a specified range.
If the distance between two metal plates changes, the capacitance between the two plates will also change. A variable capacitance pressure sensor (Figure 5) measures the change in capacitance between a metal diaphragm and a fixed metal plate. These pressure sensors are generally stable and linear, but they are very sensitive to high temperatures and are more complex to install than most pressure sensors.

Figure 5. Capacitive pressure sensor [4]
Piezoelectric pressure sensors (Figure 6) exploit the electrical properties of naturally occurring crystals such as quartz. These crystals generate an electrical charge when subjected to pressure. Piezoelectric pressure sensors do not require an external excitation source and are very rugged. However, these sensors do require charge amplification circuitry and are very susceptible to shock and vibration.

Figure 6. Piezoelectric pressure sensor [4]
Dynamic shock is a common cause of sensor failure in pressure measurement applications, causing the sensor to overload. A classic example of a pressure sensor overload is water hammer. Water hammer occurs when a fast-moving liquid is suddenly stopped by a closed valve. The force of the liquid is suddenly suppressed, causing the walls of the liquid tube to stretch suddenly. This stretching creates a pressure surge that can damage the pressure sensor. To reduce the effects of "water hammer", a shock absorber is often installed between the sensor and the pressure line. The shock absorber is usually a mesh filter or sintered material that allows the pressurized liquid to pass through, but not the bulk liquid, thereby preventing the pressure surge when water hammer occurs. Shock absorbers are a good choice for protecting the sensor in some applications, but in many tests, the peak shock pressure is what needs to be tested. In this case, a pressure sensor without overload protection should be selected. [3]
Back to top
3. Pressure measurement
As mentioned above, the natural output of a pressure sensor is a voltage. Many strain-based pressure sensors output a small mV voltage. This small signal requires several signal conditioning considerations, which are detailed in the next section. In addition, many pressure sensors also output a conditioned 0-5 V signal or a 4-20 mA current. Both of these outputs are linear over the sensor's operating range. For example, 0 V and 4 mA correspond to a zero pressure measurement. Similarly, 5 V and 20 mA correspond to the full-scale capacity, or maximum pressure, that the sensor can measure. Both 0-5 V and 4-20 mA signals can be easily measured with NI multifunction data acquisition (DAQ) hardware.
Back to top
4. Signal conditioning for measuring pressure
As with other bridge-based sensors, there are several signal conditioning factors that need to be considered in order to accurately measure pressure. The following factors are important:
- Bridge Complete
- excitation
- remote sensing
- enlarge
- Filtering
- Offset
- Shunt Calibration
Each of these factors is explained in detail in the "Strain Measurement Using Strain Gages" tutorial linked at the bottom.
Once a measurable voltage signal is obtained, this signal must be converted to actual pressure units. Pressure sensors generally produce a linear response over the operating range, so linearization is generally not required, but some hardware or software is required to convert the voltage output of the sensor into a pressure measurement. The conversion formula used depends on the type of sensor used and is provided by the sensor manufacturer. Typical conversion formulas are related to the excitation voltage, the full-scale capacity of the sensor, and the calibration factor.

For example, a pressure sensor with a full scale capacity of 10,000 PSI and a calibration factor of 3mv/V, and a pressure transducer that receives a 10V DC excitation voltage will produce a measured voltage of 15 mV, which would give a measured pressure of 5000 PSI.
After the signal has been properly scaled, the proper rest position must be achieved. Pressure sensors (whether absolute or gauge) have a certain strength that is considered a rest or reference position. The strain gage should produce 0 volts at this position. Offset nulling circuits add or remove resistance from one side of the strain gage to achieve this "equilibrium" position. Offset nulling is very important in ensuring accurate pressure measurements, and for best results, offset nulling should be performed in hardware, not software.
Previous article:Resistance strain gauge DC bridge measurement circuit strategy
Next article:Measuring sound using a microphone
- Popular Resources
- Popular amplifiers
- Keysight Technologies Helps Samsung Electronics Successfully Validate FiRa® 2.0 Safe Distance Measurement Test Case
- From probes to power supplies, Tektronix is leading the way in comprehensive innovation in power electronics testing
- Seizing the Opportunities in the Chinese Application Market: NI's Challenges and Answers
- Tektronix Launches Breakthrough Power Measurement Tools to Accelerate Innovation as Global Electrification Accelerates
- Not all oscilloscopes are created equal: Why ADCs and low noise floor matter
- Enable TekHSI high-speed interface function to accelerate the remote transmission of waveform data
- How to measure the quality of soft start thyristor
- How to use a multimeter to judge whether a soft starter is good or bad
- What are the advantages and disadvantages of non-contact temperature sensors?
- LED chemical incompatibility test to see which chemicals LEDs can be used with
- Application of ARM9 hardware coprocessor on WinCE embedded motherboard
- What are the key points for selecting rotor flowmeter?
- LM317 high power charger circuit
- A brief analysis of Embest's application and development of embedded medical devices
- Single-phase RC protection circuit
- stm32 PVD programmable voltage monitor
- Introduction and measurement of edge trigger and level trigger of 51 single chip microcomputer
- Improved design of Linux system software shell protection technology
- What to do if the ABB robot protection device stops
- Allegro MicroSystems Introduces Advanced Magnetic and Inductive Position Sensing Solutions at Electronica 2024
- Car key in the left hand, liveness detection radar in the right hand, UWB is imperative for cars!
- After a decade of rapid development, domestic CIS has entered the market
- Aegis Dagger Battery + Thor EM-i Super Hybrid, Geely New Energy has thrown out two "king bombs"
- A brief discussion on functional safety - fault, error, and failure
- In the smart car 2.0 cycle, these core industry chains are facing major opportunities!
- The United States and Japan are developing new batteries. CATL faces challenges? How should China's new energy battery industry respond?
- Murata launches high-precision 6-axis inertial sensor for automobiles
- Ford patents pre-charge alarm to help save costs and respond to emergencies
- New real-time microcontroller system from Texas Instruments enables smarter processing in automotive and industrial applications
- EEWORLD University - Brushless Motor Tutorial
- Introduction to FPGA design process and tool software
- EEWORLD University----[High Precision Laboratory] Interface: RS-485
- 【Perf-V Review】VIVADO Flowing Light
- [The third stop of Shijian’s ADI journey] Learn about cutting-edge IoT devices and solutions, and win Kindle and other gifts
- Are there any netizens working in the field of motors?
- Evaluation report summary: Mir MYS-8MMX
- 2020 Share the beauty of Qingdao in my eyes
- Zigbee Technology Exchange
- ST's new 400W power board