Magnetostrictive displacement sensor is a displacement sensor for high-precision, long-stroke absolute position measurement manufactured based on the principle of magnetostriction. It adopts a non-contact measurement method. Since the active magnetic ring used for measurement and the sensor itself have no direct contact, they will not be rubbed or worn. Therefore, it has a long service life, strong environmental adaptability, high reliability, good safety, and is convenient for system automation . It can work normally even in harsh industrial environments (such as those prone to oil spills, dust or other pollution). In addition, it can withstand high temperature, high pressure and strong vibration. It has been widely used in the measurement and control of mechanical displacement. However, this measurement method has some shortcomings: ① The analog signal has limited anti-interference ability and cannot be transmitted over long distances; ② The noise introduced by circuit conversion makes its measurement accuracy low; ③ The signal interchangeability is poor, and expensive A/D interchange equipment is required. The single-chip microcomputer and its peripheral circuits are used for better processing, and multi-point high-precision measurement is achieved, and long-distance transmission and access to the industrial monitoring network are achieved through RS-485 serial communication. In addition, due to the use of PIC low-power single-chip microcomputers and other low-power chips, the circuit structure is optimized, and the system power consumption is greatly reduced. 1 Introduction to magnetostrictive displacement sensor 1.1 Sensor structure The magnetostrictive displacement sensor consists of two parts: one is a measuring rod with a movable magnet; the other is a measuring circuit located at the upper end of the measuring rod. The structure of the magnetostrictive displacement sensor is shown in Figure 1. In Figure 1, the magnetostrictive displacement sensor mainly includes the following parts: waveguide wire, protective tube sleeve, moving magnet, and circuit board. The measuring tube is the core sensing part of the entire sensor, which includes: bias magnet, waveguide wire, protective tube sleeve, end attenuation damping device, non-contact magnetic ring, and converter output.
Figure 1 Structure of magnetostrictive displacement sensor
The magnetostrictive wire is installed in a stainless steel tube, and the outer side of the steel tube can slide freely. The pulse generator in the electronic device generates a current pulse (starting pulse) and propagates along the waveguide. The generated magnetic field is superimposed with the inherent magnetic field vector of the active magnetic ring to form a spiral magnetic field, which generates instantaneous torque, causing the waveguide to twist and generate a tension pulse (waveguide pulse). This pulse is transmitted back along the waveguide at a fixed speed, generating an induction pulse (termination pulse) at both ends of the coil (converter). By measuring the time difference between the starting pulse and the termination pulse, the measured displacement can be accurately determined. As shown in Figure 2. Because the speed of the tension pulse on the waveguide is constant, the measured time difference is multiplied by this speed to obtain the position of the magnetic ring. This process is continuous, and every time the magnetic ring moves, the new position will be sensed.
Figure 2. Magnetostrictive displacement sensor waveform
At present, it is not easy to directly measure the time interval between the start and end pulses of the sensor and obtain the accurate position. The method currently used is to convert the time interval between the two pulse signals into a PWM signal proportional to the position of the magnetic ring, and then output it in the form of a current loop. In the actual measurement process, the current pulse and induction pulse in the sensor will cause certain interference to the output signal; and the magnetic field induced by the magnetic material of the sensor itself and the current in the waveguide will inevitably produce electromagnetic interference (EMIElectroMagneticInterference), which makes the measured output signal have a certain degree of distortion, as shown in Figure 3, which is the waveform obtained by converting the current loop output signal of the sensor into a voltage signal. In addition, if it is necessary to use several magnetostrictive displacement sensors in the same system for displacement measurement, there will be interference between the sensors. The existence of these interference signals makes the dynamic and static performance of the control system poor. For control systems with high precision and fast response frequency, the degree of influence is very obvious, which will affect the stability of the system and must be eliminated. A sensor signal processing system based on a single-chip microcomputer is designed, and the stable output signal obtained after processing is directly transmitted to the computer for control in the form of a digital signal through remote communication. This makes the output signal of this type of magnetostrictive displacement sensor stable, with high accuracy and long transmission distance. The interface with the control system is simple, interchangeable and practical, making the sensor more intelligent and the overall performance greatly optimized and improved.
Figure 3. Original waveform of magnetostrictive displacement sensor signal
2.1 System structure
The hardware structure of the magnetostrictive displacement sensor displacement measurement system is shown in Figure 4. Since the magnetostrictive displacement sensor adopts the form of 4-20mA current loop output that meets the industrial control standard, it is necessary to first convert the output current signal of the sensor into a voltage signal, then collect it for A/D conversion, and then output it to the microcontroller for signal processing and communication processing, and finally transmit the ideal sensor signal in binary form to the LCD screen and PC. The sensor circuit is composed of a sensitive element head, a receiving circuit, a signal shaping circuit, a parameter correction input circuit, a computer processing circuit, a display circuit, and a measurement parameter output circuit.
Figure 4 System hardware design
The single-chip microcomputer uses the AT89C4051 8-bit microprocessor based on CMOS technology from ATMEL, which is fully compatible with the instructions of the MCS-51 product series. It contains a 4kb Flash EPROM. Its most prominent feature is that the chip is small in size and has only 20 pins, which is particularly suitable for the design of miniaturized systems. In addition, the AT89C4051 is cheap and has a high cost performance.
2.3 Signal Shaping Circuit
The sliding digital filtering algorithm based on extracting the characteristic quantity of the measured signal is adopted. As shown in Figure 3, it is the analog signal waveform output by the sensor when the magnetic ring is in a static state. It can be seen that there is a high-frequency interference signal superimposed on the measured stable value, with a maximum peak-to-peak value of about 25mV and a period of 440μs. If the single measurement value is directly sampled and transmitted to the controller, the probability of randomly obtaining an abnormal measurement value is relatively high in high-precision measurement occasions, and the maximum error is 12 LSB. Therefore, it is best to measure a certain displacement multiple times continuously to obtain a group of N measurement values, and make this group of measurement values contain an interference cycle, so as to obtain a measurement value that can represent the correct value. The structure of the signal shaping circuit includes a measurement operational amplifier and an optocoupler; its function is to shape the measurement amplified signal and send it to the computer. 89C4051 is the core part of the system hardware to realize digital processing. Its main frequency works at 11.0592MHz and includes a peripheral reset circuit. It is mainly used to complete the functions of controlling A/D conversion, signal processing, and sending data to the host and LCD in serial mode. The P3 port of the microcontroller is used as the control line for A/D conversion and communication. When reading the A/D conversion value, the 12-bit A/D conversion value is directly read in twice using the PI port.
Figure 5 shows the measurement characteristics of the magnetic ring of the sensor using the digital processing system when it is in static and dynamic state. Figure 5 (a) shows that the system has good measurement accuracy and stability, and the error is only 1 LSB; Figure 5 (b) shows that the system has good dynamic measurement characteristics.
Figure 5 Static and dynamic characteristics of magnetostrictive displacement sensor
The correction circuit is composed of MAX25C045, keyboard and selection switch. Its function is to adjust the zero position and full scale of the sensor, and set the transmission speed of waveguide current pulse and store parameters.
2.5 Display circuit
Based on the structure and principle of LCD display, the code corresponding to the number to be displayed is converted and written, that is, the corresponding segment selection code table is written. The table is called from the display main program, and the output change value of the sensor can be displayed on the LCD.
2.6 Measurement parameter output circuit
The data output includes the 12bit high-speed D/A conversion chip MAX5302 and the operational amplifier output 0~5V, 0~10V, 0~10mA, 4~20mA measurement data; the binary data output includes the 485 interface chip MAX1428 output binary measurement data, and the data transmission distance can reach more than 1000m.
3 Development direction of magnetostrictive displacement sensor
The Temposonics ER displacement sensor being developed by MTS represents the development direction of magnetostrictive displacement sensor. The Temposonics ER displacement sensor is based on the magnetostrictive measurement principle, and uses the accurate speed and time measurement of ultrasonic waves (torsion wave pulses generated by the sensor) to calculate the target position. The sensor directly converts the measurement results into standard output by processing the signal conversion process. Magnetostrictive displacement sensors have developed in the direction of long measurement distance and high measurement accuracy. In the future, the use of modular design, modular assembly, digital output, strong electromagnetic interference resistance and temperature detection compensation technologies will greatly reduce the cost of such sensors, significantly improve performance, and expand the scope of application. In order to meet the requirements of sensor engineering and practicality, the sensor is also durable in the worst industrial environment. Regardless of whether the target position is difficult or not, the sensor will adjust the parameters according to the actual situation and configure the corresponding structure to suit the application system. The structure and packaging technology of the sensor also need to be broken through, and the effective integration of mechanical design and electronic devices should be achieved.
4 Conclusion
The use of single-chip microcomputer chips and EIA RS-422/485 international serial data transmission standard circuits, and the use of ultra-small electronic components for surface welding in the built-in electronic module can make the new magnetostrictive sensor more stable and reliable, greatly extend the data transmission distance of the sensor, and can communicate directly with PLC, computers, etc., saving expensive transmitters and A/D conversions, so that the measurement and control system composed of the magnetostrictive sensor is more convenient and stable, and the cost is greatly reduced.
While improving the elastic modulus and mechanical strength of the waveguide wire, ensuring its stable expansion coefficient is the key to the development of sensitive components, and is also a very important part of the development of magnetostrictive displacement sensors. High-precision time detection technology and packaging technology that can resist harsh environments cannot be ignored. The research on magnetostrictive displacement sensors has broad market prospects.
Previous article:Freescale proximity sensors accelerate touch-control design for portable terminals
Next article:Application of Intelligent Magnetostrictive Displacement Sensor on Ships
Recommended ReadingLatest update time:2024-11-16 23:51
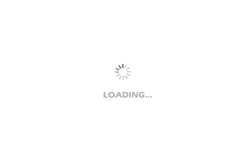
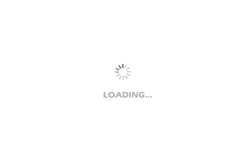
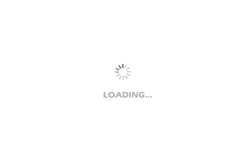
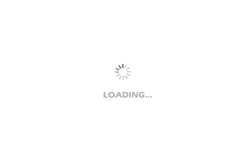
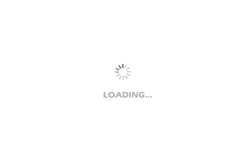
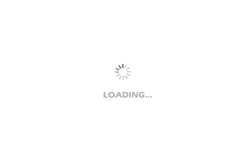
- Popular Resources
- Popular amplifiers
-
Analysis and Implementation of MAC Protocol for Wireless Sensor Networks (by Yang Zhijun, Xie Xianjie, and Ding Hongwei)
-
Introduction to Internet of Things Engineering 2nd Edition (Gongyi Wu)
-
西门子S7-12001500 PLC SCL语言编程从入门到精通 (北岛李工)
-
Modern Motor Control Technology (Wang Chengyuan, Xia Jiakuan, Sun Yibiao)
- Melexis launches ultra-low power automotive contactless micro-power switch chip
- Infineon's PASCO2V15 XENSIV PAS CO2 5V Sensor Now Available at Mouser for Accurate CO2 Level Measurement
- Milestone! SmartSens CMOS image sensor chip shipments exceed 100 million units in a single month!
- Taishi Micro released the ultra-high integration automotive touch chip TCAE10
- The first of its kind in the world: a high-spectral real-time imaging device with 100 channels and 1 million pixels independently developed by Chinese scientists
- Melexis Launches Breakthrough Arcminaxis™ Position Sensing Technology and Products for Robotic Joints
- ams and OSRAM held a roundtable forum at the China Development Center: Close to local customer needs, leading the new direction of the intelligent era
- Optimizing Vision System Power Consumption Using Wake-on-Motion
- Infineon Technologies Expands Leading REAL3™ Time-of-Flight Portfolio with New Automotive-Qualified Laser Driver IC
- Innolux's intelligent steer-by-wire solution makes cars smarter and safer
- 8051 MCU - Parity Check
- How to efficiently balance the sensitivity of tactile sensing interfaces
- What should I do if the servo motor shakes? What causes the servo motor to shake quickly?
- 【Brushless Motor】Analysis of three-phase BLDC motor and sharing of two popular development boards
- Midea Industrial Technology's subsidiaries Clou Electronics and Hekang New Energy jointly appeared at the Munich Battery Energy Storage Exhibition and Solar Energy Exhibition
- Guoxin Sichen | Application of ferroelectric memory PB85RS2MC in power battery management, with a capacity of 2M
- Analysis of common faults of frequency converter
- In a head-on competition with Qualcomm, what kind of cockpit products has Intel come up with?
- Dalian Rongke's all-vanadium liquid flow battery energy storage equipment industrialization project has entered the sprint stage before production
- Allegro MicroSystems Introduces Advanced Magnetic and Inductive Position Sensing Solutions at Electronica 2024
- Car key in the left hand, liveness detection radar in the right hand, UWB is imperative for cars!
- After a decade of rapid development, domestic CIS has entered the market
- Aegis Dagger Battery + Thor EM-i Super Hybrid, Geely New Energy has thrown out two "king bombs"
- A brief discussion on functional safety - fault, error, and failure
- In the smart car 2.0 cycle, these core industry chains are facing major opportunities!
- The United States and Japan are developing new batteries. CATL faces challenges? How should China's new energy battery industry respond?
- Murata launches high-precision 6-axis inertial sensor for automobiles
- Ford patents pre-charge alarm to help save costs and respond to emergencies
- New real-time microcontroller system from Texas Instruments enables smarter processing in automotive and industrial applications
- [Liquid Level Sensor Evaluation] Re-understanding of Capacitive-Contactless Liquid Level Sensor
- LED PWM Dimming C Program
- FPGA introductory series experimental tutorial - key debounce control LED on and off
- Crazy Shell AI open source drone flight control machine code reading, compilation and burning
- TWS Headphones ANC Design Guide Basics 01
- What is c_int00 when programming DSP?
- Keil.STM32H7xx_DFP.2.2.0 installation package problem
- [Ultra-low power STM32U5 IoT Discovery Kit] - 2: wifi
- Why can't I debug CCS7.0 suddenly?
- Drawing