introduction
Traditionally, permanent magnet synchronous motors with trapezoidal wave back EMF are called brushless DC motors. Torque control of brushless DC motors requires rotor position information to achieve effective stator current control. Moreover, speed control also requires speed signals. The use of position sensors is the basis of vector control of brushless DC motors. However, the existence of position sensors also brings many defects and inconveniences to the application of brushless DC motors: first, position sensors increase the size and cost of the motor; second, connecting many position sensors will reduce the reliability of motor operation. Even the most widely used Hall sensors have a certain degree of magnetic insensitivity; third, in some harsh working environments, such as in sealed air-conditioning compressors, due to the strong corrosiveness of the refrigerant, conventional position sensors cannot be used at all; finally, the installation accuracy of the sensor will also affect the operating performance of the motor and increase the difficulty of the production process.
Sensorless control technology has been an important research direction of brushless DC motor (BLDCM) in the past 30 years. The current research status of sensorless control of BLDCM at home and abroad is discussed. The basic principles, implementation methods, application scenarios, advantages and disadvantages of several conventional methods that are currently widely used and studied are introduced, and a comprehensive analysis and comparison are made. Sensorless control is control without a mechanical position sensor. At this time, the rotor position signal, which is the timing signal for the inverter switch commutation conduction, is still indispensable, but it is no longer provided by the position sensor, but should be replaced by a new position signal detection measure, that is, to reduce the complexity of the motor structure by increasing the complexity of the circuit and control.
At present, the core of BLDCM position sensorless control research is to construct a rotor position signal detection circuit, indirectly obtain reliable rotor position signals from both software and hardware aspects, thereby triggering the corresponding power devices to drive the motor to operate. So far, among the many position signal detection methods, the most widely used and studied ones are stator inductance method, speed-independent position function method, back-EMF method, fundamental potential commutation method and state observer method.
1 Rotor position detection scheme based on back electromotive force
Brushless DC Motor (BLDCM) has the advantages of no commutation spark, reliable operation, easy maintenance, and simple structure, so it has been widely used in many occasions. However, the traditional BLDCM requires an additional position sensor to control the rotor position, which has brought many adverse effects on its application. The position sensorless control of BLDCM has been a popular research topic at home and abroad in the past 30 years [1]. At present, for the position sensorless control of BLDCM, people have proposed a variety of different control theories and implementation methods for different performance requirements and application occasions, such as stator inductance method, speed-independent position function method, back-EMF method, fundamental potential commutation method, state observer method, etc. Based on a brief discussion of the current status of BLDCM position sensorless control research, this paper introduces in detail the basic principles, implementation methods, application occasions, advantages and disadvantages of several methods that are currently used and studied more.
When the motor speed is greater than zero, there are only two positions in each electrical cycle where the back EMF is zero. These positions can be distinguished by the slope of the back EMF when it crosses zero as shown in Figure 1. Each section corresponds to a 60° interval in the electrical cycle. Commutation occurs at the boundary of each section. There is a 30° offset between the back EMF zero crossing point and the position where commutation is required, which needs to be compensated.
Figure 1 Back EMF zero crossing point
At any one time, only two phases are energized, and the currents flowing through these two phases are opposite. Figure 2 shows the situation when the W phase is used for back EMF detection. When a positive current (defined as the current flowing to the center point of the star connection) flows through the U phase and a negative current flows through the V phase, corresponding to the intervals 6Q and 1Q in Figure 1, this set 1 operates. Assuming that the two ends of the energized phase are always symmetrically connected to the two ends of the DC power supply, the voltage at the center point of the star connection is always 1/2VDC, regardless of the voltage polarity applied to the two energized phase windings.
The above method can be easily implemented by hardware, that is, the three-phase terminal voltage and VDC are sampled respectively by the voltage divider circuit, and the sampled values are sent to the comparison port of the comparator. The zero-crossing moment is the moment of 1/2VDC. Use an available fixed back electromotive force timer to measure 60° (i.e., the time between two back electromotive force zero crossings).
[page] 2DSP control scheme system implementation
2.1TMS320LF240x Chip Introduction
The TMS320LF240x series DSP is designed by TI to meet a wide range of digital motor control (DMC) applications. The chip has a high-performance 16-bit fixed-point DSP core, adopts an improved Harvard bus structure, has a dedicated hardware multiplier, uses pipeline operation, has a processing capacity of 30MIPS, and most instructions can be executed in a single cycle. TMS320LF240x can replace analog devices with software, complete complex control algorithms, easily modify control strategies, and correct control parameters, which can meet the real-time control requirements of sensorless DC brushless motor control systems.
2.2 Hardware Implementation of DSP Control System
The DSP system is composed of TMS320LF2407A and peripheral circuits such as the emulation port (JTAG). There is already a 32K-word FlashROM inside the DSP, but for the convenience of debugging (the program in the FlashROM cannot set breakpoints, and a special download program is required), a program RAM is added. After the program has been debugged many times and is mature and reliable, it can be written to the internal FlashROM. By setting the corresponding jumper, the program can be executed from the internal FlashROM when the DSP is reset. There are 544 words of dual-port RAM (DARAM) on the DSP chip, all of which are configured in the data space. The variables frequently accessed in the program are allocated to this part of the dual-port RAM to increase the processing speed. There are also 2K words of single-port RAM (SARAM) on the DSP chip configured in the data space, which is also used to store temporary variables.
Figure 3 is a DSP-based brushless DC motor control system designed according to the above control principle. The system is mainly composed of a brushless DC motor, a power converter circuit, a motor rotor position detection circuit, various protection circuits, and a digital controller with TMS320LF240x as the core. The power converter circuit consists of a rectifier filter circuit, an inverter circuit (IPM power module), and corresponding protection circuits.
Figure 3 DSP control system
The IPM module in the inverter circuit integrates multiple protection functions, such as overvoltage protection, undervoltage protection and overcurrent protection. When the protection threshold is reached, the IPM module outputs a low-level signal through the FO pin and sends this low-level signal to the PDPINTx pin of the DSP, triggering the power drive protection interrupt and setting all PWM output pins to a high-impedance state, thereby shutting off the drive signal and protecting the circuit.
The rotor position detection circuit is implemented using the 1/2 voltage sampling method. The three-phase terminal voltage and DC bus voltage of the motor are sampled respectively, and the sampling results are sent to the comparator for comparison to obtain the zero-crossing moment, and the result is sent to the capture port of the DSP.
[page] 2.3 DSP control system software design
This control system adopts a speed and current double closed loop control structure. Due to the use of high-speed DSP for motor control, digital signal processing technology is used in both the design of the speed loop and the realization of the current loop, as well as the processing of various feedback signals and the generation of PWM control signals. The functions of the hardware circuit are realized by software to complete the real-time control of the DC brushless motor.
The software design of the control system mainly includes two parts: DSP initialization program and motor control program. The DSP initialization program mainly completes the setting of system clock, definition of interrupt vector, initialization of I/O port, setting of control register and initialization of each functional module; the motor control program is mainly responsible for the motor start control, speed and current double closed-loop control, system monitoring and fault handling, etc. Therefore, the motor control program includes the start subroutine, current and position detection interrupt service subroutine, speed control subroutine, current control subroutine, PWM modulation subroutine and system monitoring and fault handling subroutine.
The detection of various feedback signals is the premise of forming a double closed-loop control. The detection of position signal and current signal is realized by the position detection interrupt service program and the current detection interrupt service program respectively, and the detection of speed is obtained indirectly through software calculation. In order to improve the dynamic performance and steady-state accuracy of the system. The control loop diagram is shown in Figure 4.
Figure 4 Current and speed control loop
The PWM modulation subroutine generates a PWM modulation signal through the event manager (EV) according to the detected rotor position signal and current signal. The counting mode of the general timer is set to the continuous increase/decrease counting mode through the bit pattern in the timer control register TxCON to generate a symmetrical PWM waveform.
2.4 Motor starting scheme
Since it is difficult to correctly detect the back EMF signal when the brushless DC motor is stationary or running at low speed, the problem of starting the motor in a stationary state must be solved. In the past, there were many starting methods, but some required the addition of complex starting circuits, while others were closely related to the motor characteristics, making them difficult to implement and having low reliability.
This system uses a three-stage method to start the motor using software alone, and divides the motor start-up process into three stages: pre-positioning, forced operation, and synchronous switching. When the motor is stationary, the initial position of the rotor is unknown. It is necessary to pass a short current through the set two-phase armature winding to stabilize the rotor pole on the axis of the magnetic field formed by the two-phase winding, which is used as the initial position of the rotor pole (i.e., pre-positioning). Then, the corresponding power devices are turned on according to the correct spatial phase relationship between the stator and rotor poles, and the mode is switched at a fixed time. During this period, the back electromotive force amplitude is small, and zero-crossing detection is not suitable.
3 Experimental results
The above control scheme is applied to the DC variable frequency air conditioner compressor system for experimental verification. The number of motor pole pairs is 2, the PWM carrier frequency is set to 5kHz, the maximum output power is 2kW, and the speed regulation range is 15~~110Hz. The experiment proves that the system starts smoothly, the speed control system has good real-time performance, and has good control performance. Figure 5 is the waveform of the three-phase voltage of the brushless DC motor, and Figure 6 is the waveform of the three-phase current of the brushless DC motor. It can be seen from the waveform diagram that the output waveform has a high quality, which shows the feasibility and practicality of the control strategy and algorithm adopted by the system.
Figure 5 Three-phase voltage waveform
Figure 6 Three-phase current waveform
4 Conclusion
Brushless DC motors have the advantages of high efficiency, high power density, high power factor, small size, high control accuracy, etc., and their application range is very wide. The control technology of brushless DC motors is transitioning from traditional closed-loop PID control with position sensors to intelligent control without position sensors, and its speed regulation range, torque pulsation, system robustness and other performance are constantly improving.
Based on the full use of the powerful real-time computing capability of TMS320LF240x and the rich integrated devices on the chip, a control scheme for a position sensorless DC brushless motor based on DSP is designed, and the software and hardware structure of the control system is given. The control system has good control performance and speed regulation performance, can obtain good dynamic characteristics and high steady-state accuracy, high operating efficiency, strong anti-interference ability, and has high practical application value.
Previous article:Causes and solutions for MOS tube breakdown
Next article:Current status and improvement methods of photoelectric parameters and detection methods of LED modules
Recommended ReadingLatest update time:2024-11-16 15:20
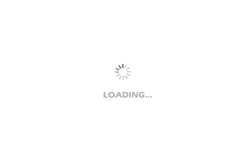
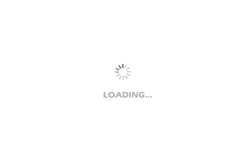
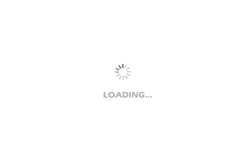
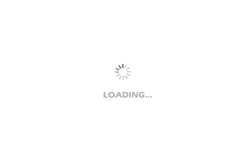
- Popular Resources
- Popular amplifiers
-
西门子S7-12001500 PLC SCL语言编程从入门到精通 (北岛李工)
-
New Energy Vehicle Detection and Diagnosis Experiment (Edited by Mao Caiyun, Zhou Xien, and Long Jiwen)
-
Virtualization Technology Practice Guide - High-efficiency and low-cost solutions for small and medium-sized enterprises (Wang Chunhai)
-
ESP32-S3 source code
- MathWorks and NXP Collaborate to Launch Model-Based Design Toolbox for Battery Management Systems
- STMicroelectronics' advanced galvanically isolated gate driver STGAP3S provides flexible protection for IGBTs and SiC MOSFETs
- New diaphragm-free solid-state lithium battery technology is launched: the distance between the positive and negative electrodes is less than 0.000001 meters
- [“Source” Observe the Autumn Series] Application and testing of the next generation of semiconductor gallium oxide device photodetectors
- 采用自主设计封装,绝缘电阻显著提高!ROHM开发出更高电压xEV系统的SiC肖特基势垒二极管
- Will GaN replace SiC? PI's disruptive 1700V InnoMux2 is here to demonstrate
- From Isolation to the Third and a Half Generation: Understanding Naxinwei's Gate Driver IC in One Article
- The appeal of 48 V technology: importance, benefits and key factors in system-level applications
- Important breakthrough in recycling of used lithium-ion batteries
- Innolux's intelligent steer-by-wire solution makes cars smarter and safer
- 8051 MCU - Parity Check
- How to efficiently balance the sensitivity of tactile sensing interfaces
- What should I do if the servo motor shakes? What causes the servo motor to shake quickly?
- 【Brushless Motor】Analysis of three-phase BLDC motor and sharing of two popular development boards
- Midea Industrial Technology's subsidiaries Clou Electronics and Hekang New Energy jointly appeared at the Munich Battery Energy Storage Exhibition and Solar Energy Exhibition
- Guoxin Sichen | Application of ferroelectric memory PB85RS2MC in power battery management, with a capacity of 2M
- Analysis of common faults of frequency converter
- In a head-on competition with Qualcomm, what kind of cockpit products has Intel come up with?
- Dalian Rongke's all-vanadium liquid flow battery energy storage equipment industrialization project has entered the sprint stage before production
- Allegro MicroSystems Introduces Advanced Magnetic and Inductive Position Sensing Solutions at Electronica 2024
- Car key in the left hand, liveness detection radar in the right hand, UWB is imperative for cars!
- After a decade of rapid development, domestic CIS has entered the market
- Aegis Dagger Battery + Thor EM-i Super Hybrid, Geely New Energy has thrown out two "king bombs"
- A brief discussion on functional safety - fault, error, and failure
- In the smart car 2.0 cycle, these core industry chains are facing major opportunities!
- The United States and Japan are developing new batteries. CATL faces challenges? How should China's new energy battery industry respond?
- Murata launches high-precision 6-axis inertial sensor for automobiles
- Ford patents pre-charge alarm to help save costs and respond to emergencies
- New real-time microcontroller system from Texas Instruments enables smarter processing in automotive and industrial applications
- Theoretical speed calculation of WiFi protocols
- BQ76930: Design help needed for BQ76930 based BMS
- Application of the concepts of virtual short and virtual disconnect in operational amplifiers in actual product circuits
- What is the application of PWM
- Guess the questions in the electronic competition and win prizes!
- MSP430f5529
- What is Full SRT?
- Introduction to MSP430 development tools (JTAG SBW BS)
- The experiment got me all greasy:lol
- EEWORLD University Hall----Live Replay: Supporting 'Dual Carbon' - ADI Smart Factory Solution