After 5nm, foundry competition began to move toward the more advanced 3nm node. Currently, Samsung, TSMC, and Intel have formed a three-way split in the advanced process competition. And from the perspective of 3nm, the competition between Samsung and TSMC is particularly fierce.
Regarding the progress of 3nm, TSMC said that the 3nm process is in line with the schedule, trial production will be carried out this year, and mass production will be carried out in the second half of 2022. Samsung Electronics announced that it will start production of the first batch of 3nm chips in the first half of 2022, and the second-generation 3nm chips are expected to start production in 2023.
In terms of time, Samsung's 3nm will be ahead of TSMC for about half a year, and it is obvious that it wants to surpass TSMC with 3nm. Overall, what are the strengths of the two companies? This article will start from the aspects of technology, capital, production capacity, customers, etc., in order to reflect the general strength of the two companies.
Technical route
The biggest difference between TSMC and Samsung at 3nm lies in the choice of technology.
TSMC's 3nm process will continue to use FinFET (fin field-effect transistor) technology . Why did TSMC make this choice? Analysts believe that on the one hand, it is precisely because its R&D team has brought the performance of FinFET to a new level. Compared with 5nm, 3nm has a 10%~15% increase in speed, a 25~30% decrease in power consumption, and a 1.7-fold increase in logic density, and a 20% increase in SRAM density; on the other hand, 3nm can be mass-produced in the second half of 2022, which will enable customers who place orders to achieve rapid technology upgrades and be the first to launch leading products.
In order to catch up with TSMC in semiconductor process technology, Samsung was the first to introduce the new GAA (Gate-all-around) technology in the research and development of 3nm process.
It is understood that there are many forms of GAA-based FETs (GAAFETs), and most of the research is based on nanowire-based GAAFETs, which have a smaller channel width. These types of GAAFETs are often used in low-power designs, but they are difficult to manufacture. Another way to achieve this is to make the channel like a horizontally laid paper, which brings benefits to performance and size by increasing the channel area. Samsung calls its nanosheet-based GAAFET a multi-bridge channel FET or MBCFET, which can significantly enhance transistor performance and mainly replace FinFET transistor technology.
Compared with FinFET transistor technology, GAAFET transistors provide better electrostatic characteristics, which reduces leakage power and thus reduces power consumption. Samsung said that compared with the 5nm process, GAA process technology will reduce chip area by another 35%, improve performance by 30% or reduce power consumption by 50%.
Samsung's 3nm process is divided into two versions, of which 3GAE (low-power version) will be put into mass production in early 2022, and 3GAP (high-performance version) will be put into mass production in early 2023.
R&D Strength
To stay ahead in chip manufacturing technology means investing a lot of money in research and development.
TSMC's R&D investment has been growing steadily. According to TSMC's financial report, in 2019, R&D expenditures were US$2.959 billion. In 2020, in pursuit of 5-nanometer and more advanced 3-nanometer processes, TSMC's R&D expenditures increased by 26%, exceeding US$3 billion in one fell swoop to US$3.72 billion. Judging from TSMC's first-quarter financial report released on April 15, its investment in R&D this year will be even higher, with R&D expenditures of US$1.096 billion in the first quarter, significantly higher than last year's average level.
In terms of capital expenditure, TSMC announced on January 14 this year that it plans to increase its capital expenditure this year to between US$25 billion and US$28 billion. IC Insights estimates that TSMC's average quarterly capital expenditure will be approximately US$6.9 billion, doubling its spending in the fourth quarter of 2020.
Samsung is also not far behind in this regard. Samsung's R&D expenditure has increased significantly year by year, and its R&D expenditure in 2020 was US$5.5 billion.
In terms of capital expenditure, according to the IC Insights report, Samsung's semiconductor capital expenditure has been very strong since 2017, reaching $21.6 billion in 2018, $19.3 billion in 2019, and $28.1 billion last year. Data shows that Samsung's total capital expenditure during the period 2017-2020 was $93.2 billion. Although Samsung has not yet provided guidance for its 2021 spending, IC Insights estimates that the company's spending will be roughly the same as in 2020.
In addition, in April 2019, Samsung announced its "Semiconductor Vision 2030" development blueprint, planning to invest US$116 billion over 10 years and hire 15,000 professionals in order to significantly improve its competitiveness in the foundry market by 2030, and surpass TSMC to become the industry leader by 2030.
Lithography Machine
In addition to technological research and development, foundry manufacturers also need to invest a lot of money in equipment, among which the expenditure on lithography machines is the most expensive.
Lithography machines are necessary equipment for producing chips, especially for producing chips with a process below 7nm, which must use EUV lithography machines. ASML is currently the only manufacturer in the world that can manufacture EUV lithography machines. ASML provides the extreme ultraviolet lithography machines required for mass production of advanced chip processes for TSMC, Samsung, and Intel. According to ASML's financial report, revenue from lithography machines in the first quarter totaled 3.129 billion euros, of which EUV lithography machines accounted for 36%, or 1.126 billion euros, and the average price of lithography machines was 160 million euros.
Data shows that by the end of 2020, ASML has shipped 100 EUV lithography machines, but Samsung has only received 30 EUV lithography machines. In contrast, TSMC is as stable as a rock in terms of EUV lithography machines. It is reported that it has installed more than 70 EUV lithography machines, twice as many as Samsung. Not only that, in terms of EUV lithography machine delivery and installation, ASML often gives priority to TSMC.
It was previously reported that in order to meet the demand for the expansion of new process technology capacity, TSMC's cumulative purchase of ultraviolet lithography machines will exceed 50 this year, and it is expected to obtain 18 this year. Assuming that each machine costs 160 million euros, 13 sets of EUV may cost TSMC up to 2.08 billion euros (about 2.34 billion US dollars).
In order to win the future, Samsung's ten-year plan with a total investment of US$116 billion mentioned above aims to promote the development of its wafer foundry business, and the most core capability is to master EUV lithography technology.
As early as 2019, Samsung spent $17 billion to build an EUV factory in Hwaseong, Gyeonggi Province, South Korea. Samsung also purchased 15 EUV lithography machines specifically for the Hwaseong factory (delivered in three years). ASML's EUV lithography machine costs as much as $172 million per unit. The purchase of 15 machines at once shows Samsung's determination to turn around in the field of wafer foundry.
At the beginning of 2020, foreign media reported that Samsung has started mass production of its newly built V1 wafer factory, becoming the industry's first pure extreme ultraviolet lithography (EUV) production line that fully uses 6LPP and 7LPP manufacturing processes. The factory is also considered to be the main base for Samsung's 3nm process. According to news on February 21 this year, Samsung Electronics stated in a document that it will expand the V1 production line of its chip factory in Hwaseong, Gyeonggi Province in advance to expand the production capacity of its EUV dedicated production line. Samsung is preparing for 3nm mass production.
Capacity
For foundry manufacturers, being the first to mass-produce advanced processes and ensuring stable performance is the key to seizing market share.
TSMC's 3nm process technology will be put into production as early as 2022, and is scheduled to be mass-produced in the second half of 2022, and actual application products are expected to be launched in 2023. TSMC is currently investing in a new plant in Arizona, the United States, which will mainly produce 5nm process technology, while the 3nm process technology will be provided in a plant built in the Southern Science and Industrial Park in Taiwan, China.
TSMC Chairman Liu Deyin once said that the cumulative investment in the 3nm process in the Southern Taiwan Science Park will exceed NT$2 trillion, and the goal is to achieve a monthly production capacity of more than 600,000 12-inch wafers when 3nm is mass-produced. According to Digitimes, TSMC's 3nm chips will begin mass production in the second half of 2022, with a monthly production capacity of 55,000 pieces, and in 2023, it will reach 105,000 pieces.
In terms of production capacity, TSMC has the ability to dynamically adjust production lines, which can increase capacity utilization to 110-120%. In terms of yield, TSMC's new process order standard is generally not less than 75%, and in mature process lines such as 14nm, the yield can be guaranteed to reach 95%-98%, which also consolidates TSMC's advantages. In short, TSMC's competitiveness does not only come from core processes, but its entire set of internal management systems is the key to ensuring production capacity and yield.
As for Samsung, due to its own business, the production capacity it can open to others is not as good as that of TSMC, which is a pure foundry. Currently, Samsung still has a gap with TSMC in terms of production capacity and yield. The well-known research institution The Information Network predicts that TSMC leads Samsung in advanced process production capacity of foundry by about 242% to 460%.
Previous article:Plasin: Determined to build a leading domestic semiconductor packaging equipment company
Next article:Wang Yu, Dean of the Department of Electronic Engineering at Tsinghua University, was elected IEEE Fellow, and 73 Chinese scholars were elected
Recommended ReadingLatest update time:2024-11-16 13:24
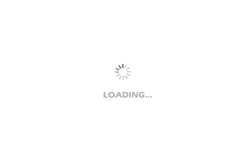
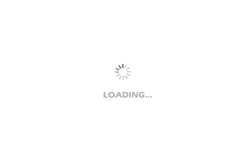
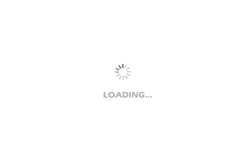
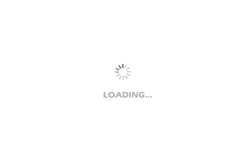
- Popular Resources
- Popular amplifiers
- Apple faces class action lawsuit from 40 million UK iCloud users, faces $27.6 billion in claims
- Apple and Samsung reportedly failed to develop ultra-thin high-density batteries, iPhone 17 Air and Galaxy S25 Slim phones became thicker
- Micron will appear at the 2024 CIIE, continue to deepen its presence in the Chinese market and lead sustainable development
- Qorvo: Innovative technologies lead the next generation of mobile industry
- BOE exclusively supplies Nubia and Red Magic flagship new products with a new generation of under-screen display technology, leading the industry into the era of true full-screen
- OPPO and Hong Kong Polytechnic University renew cooperation to upgrade innovation research center and expand new boundaries of AI imaging
- Gurman: Vision Pro will upgrade the chip, Apple is also considering launching glasses connected to the iPhone
- OnePlus 13 officially released: the first flagship of the new decade is "Super Pro in every aspect"
- Goodix Technology helps iQOO 13 create a new flagship experience for e-sports performance
- Innolux's intelligent steer-by-wire solution makes cars smarter and safer
- 8051 MCU - Parity Check
- How to efficiently balance the sensitivity of tactile sensing interfaces
- What should I do if the servo motor shakes? What causes the servo motor to shake quickly?
- 【Brushless Motor】Analysis of three-phase BLDC motor and sharing of two popular development boards
- Midea Industrial Technology's subsidiaries Clou Electronics and Hekang New Energy jointly appeared at the Munich Battery Energy Storage Exhibition and Solar Energy Exhibition
- Guoxin Sichen | Application of ferroelectric memory PB85RS2MC in power battery management, with a capacity of 2M
- Analysis of common faults of frequency converter
- In a head-on competition with Qualcomm, what kind of cockpit products has Intel come up with?
- Dalian Rongke's all-vanadium liquid flow battery energy storage equipment industrialization project has entered the sprint stage before production
- Allegro MicroSystems Introduces Advanced Magnetic and Inductive Position Sensing Solutions at Electronica 2024
- Car key in the left hand, liveness detection radar in the right hand, UWB is imperative for cars!
- After a decade of rapid development, domestic CIS has entered the market
- Aegis Dagger Battery + Thor EM-i Super Hybrid, Geely New Energy has thrown out two "king bombs"
- A brief discussion on functional safety - fault, error, and failure
- In the smart car 2.0 cycle, these core industry chains are facing major opportunities!
- The United States and Japan are developing new batteries. CATL faces challenges? How should China's new energy battery industry respond?
- Murata launches high-precision 6-axis inertial sensor for automobiles
- Ford patents pre-charge alarm to help save costs and respond to emergencies
- New real-time microcontroller system from Texas Instruments enables smarter processing in automotive and industrial applications
- Qinheng CH32V103 Review Summary
- Motor stroke control problem
- Urgently looking for chip model
- ESP32-S3 KORVO-2 2.4'' ARDUINO TFT Unboxing Report
- A troubleshooting example of connecting XDS100V3 debugging target board with CCS
- 【Android Development Learning Road】Part 2-- HelloEEWorld
- 51 MCU library serial port sends a segment of characters and the digital tube receives and displays them (use the serial port debugging assistant to modify the data)
- pic18F27Q10 eeprom erase problem
- 【BearPi-HM Micro】Part 4: Familiar with the Openharmomy compilation framework and serial port interactive output
- 50 ways to use TI CC6678 digital signal processor (DSP)