On March 1 of this year, an article titled "I've heard so many reasons for the dead light, and this teacher Liang has the most comprehensive analysis!" received more than 32,000 views and was reprinted by dozens of other corporate media, causing heated discussions in the industry. Let's follow the mobile phone portable editor to learn about the relevant content.
Recently, another enthusiastic fan left a message in the background, expressing his personal opinion on the cause of LED light failure. Since the content is quite detailed, today the editor will sort out the fan's views for your reference.
The following is the original fan's opinion (slightly modified):
The direct cause of LED light failure:
1. Die bonding: Too little glue around the chip substrate. The thermal conductivity coefficient is low, and the heat dissipation conditions during the use of the lamp beads are not good, resulting in dead lamps. (The heat dissipation itself is the biggest technical difficulty in making LEDs)
2. Wire welding: One or two solder balls are too flat and the breaking force is not enough, or the pulling force is enough, but the positive and negative poles at the contact point are fragile or too round, and the bonding force is not enough. During use, as the temperature inside the lamp bead gradually rises, it is easy to break the wire and die, or there will be a false failure and die problem (the chip or lamp bead lights up when pressed by hand)
3. Driving power supply: The current and voltage values are unstable. The impact load energy brought by the current is too large and exceeds the range that the chip can withstand, causing the chip to burn black, the circuit to burn out the electrical circuit, performance failure or gold wire disconnection, causing the lamp bead to die.
4. Encapsulation of silicone or epoxy resin: As the internal temperature of the lamp bead increases during use, the thermal expansion coefficient and stress index of the silicone will reach a peak after a period of use. The silicone will then undergo thermal expansion and cracking, which will directly affect the internal conductive gold wire breakage, causing the lamp bead to die. (The elongation coefficient of the gold wire and the thermal expansion coefficient of the silicone are very critical when selecting)
5. Chip: Chip leakage, leakage caused by process manufacturing and leakage of the chip itself when leaving the factory. It lights up normally during testing, and sometimes small leakage cannot be detected (high-power lamp beads are the best place to find these problems). During the application process, it will cause electrical overload, and a small part of the current will be unevenly distributed and delivered to the lamp board or bracket. After a period of use, the brightness is not enough, the light decay is serious, the lamp beads fail, and the internal structure turns black and burns, causing a dead lamp.
6. Heat dissipation: When using heat dissipation silicone, there are gaps between the radiator and the heat dissipation conditions or devices, the screws are not tightened, the heat dissipation silicone is unevenly applied, the total power wattage of the radiator and the lamp beads does not match, and the heat dissipation conditions are poor. After a period of use, the lamp beads will fail and the light decay seriously, turning black and dead.
7. Undiscovered problem dead light: Material, process, heat dissipation conditions, all normal, but there is still dead light phenomenon and generally almost no reason to find the dead light problem point, this has troubled the older generation of LED people for a long time, and also sent it to a special testing center and their own technical laboratory for stripping and testing, but the answer is very vague. (Generally, not very experienced LED enthusiasts will say these days the condition defects) So far, the specific cause has not been found, and it is possible that such testing equipment has appeared outside.
The above is the most common customer complaint experience of my 8-9 years of experience in the packaging industry engineering team, which is similar to the one mentioned in the article. Because I and my engineering team members have also attended lectures at the LED Research Center of Hong Kong University of Science and Technology in Foshan, the results of the analysis of the LED failure problem by the HKUST Research Center in the article and our own team are basically the same. I hope the above will be helpful to everyone.
Let’s take a look at other fans’ comments and opinions on the original article:
@淡然: The analysis is correct.
@爵: The die bonding wire is very important.
@LED: It’s not necessarily a problem with the soldering wires; the glue also has a lot to do with it.
@Next moment, goodbye: Static electricity can also cause dead lights.
@Gansu Zhonglian Optoelectronics-Xueshi Blue View-led Lighting: spirit of exploration.
@贝壳: The analysis is correct. Many people will encounter such situations.
@Xiaobai: The welding wire determines the quality of the lamp beads.
@蒋华春: Regarding 1.2 Case 2, my personal opinion is that it was caused by external force: because the article mentioned that it was mainly concentrated on the fourth solder joint, it seems to be a regular pattern, indicating that the solder wire was lost at this position. It may be that the steel tip caused the gold wire to be lost during soldering, or the nozzle squeezed the lamp bead during patching, or the lamp bead was squeezed during placement, board separation, and assembly after reflow soldering. It still needs to be investigated.
@Wind flower: Soldering wire determines quality, glue determines reliability.
In the words of Mr. Liang, the original author, there are many reasons for LED dead lights, from packaging , application, to use. How to reduce and eliminate dead lights and improve product quality and reliability is a key issue that every LED company needs to face.
The above is an introduction to the insights of a 9-year practitioner in the packaging industry on the causes of LED die in portable mobile phones. If you want to know more relevant information, please pay more attention to eeworld. eeworld Electronic Engineering will provide you with more complete, detailed and updated information.
Previous article:Has it replaced SLR? You should know how difficult it is to put optical zoom in a mobile phone
Next article:Security may become an important sector of artificial intelligence in the future
Recommended ReadingLatest update time:2024-11-16 12:56
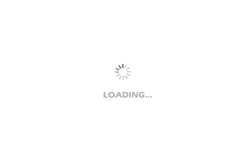
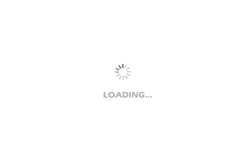
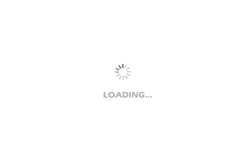
- Popular Resources
- Popular amplifiers
- Apple faces class action lawsuit from 40 million UK iCloud users, faces $27.6 billion in claims
- Apple and Samsung reportedly failed to develop ultra-thin high-density batteries, iPhone 17 Air and Galaxy S25 Slim phones became thicker
- Micron will appear at the 2024 CIIE, continue to deepen its presence in the Chinese market and lead sustainable development
- Qorvo: Innovative technologies lead the next generation of mobile industry
- BOE exclusively supplies Nubia and Red Magic flagship new products with a new generation of under-screen display technology, leading the industry into the era of true full-screen
- OPPO and Hong Kong Polytechnic University renew cooperation to upgrade innovation research center and expand new boundaries of AI imaging
- Gurman: Vision Pro will upgrade the chip, Apple is also considering launching glasses connected to the iPhone
- OnePlus 13 officially released: the first flagship of the new decade is "Super Pro in every aspect"
- Goodix Technology helps iQOO 13 create a new flagship experience for e-sports performance
- Innolux's intelligent steer-by-wire solution makes cars smarter and safer
- 8051 MCU - Parity Check
- How to efficiently balance the sensitivity of tactile sensing interfaces
- What should I do if the servo motor shakes? What causes the servo motor to shake quickly?
- 【Brushless Motor】Analysis of three-phase BLDC motor and sharing of two popular development boards
- Midea Industrial Technology's subsidiaries Clou Electronics and Hekang New Energy jointly appeared at the Munich Battery Energy Storage Exhibition and Solar Energy Exhibition
- Guoxin Sichen | Application of ferroelectric memory PB85RS2MC in power battery management, with a capacity of 2M
- Analysis of common faults of frequency converter
- In a head-on competition with Qualcomm, what kind of cockpit products has Intel come up with?
- Dalian Rongke's all-vanadium liquid flow battery energy storage equipment industrialization project has entered the sprint stage before production
- Allegro MicroSystems Introduces Advanced Magnetic and Inductive Position Sensing Solutions at Electronica 2024
- Car key in the left hand, liveness detection radar in the right hand, UWB is imperative for cars!
- After a decade of rapid development, domestic CIS has entered the market
- Aegis Dagger Battery + Thor EM-i Super Hybrid, Geely New Energy has thrown out two "king bombs"
- A brief discussion on functional safety - fault, error, and failure
- In the smart car 2.0 cycle, these core industry chains are facing major opportunities!
- The United States and Japan are developing new batteries. CATL faces challenges? How should China's new energy battery industry respond?
- Murata launches high-precision 6-axis inertial sensor for automobiles
- Ford patents pre-charge alarm to help save costs and respond to emergencies
- New real-time microcontroller system from Texas Instruments enables smarter processing in automotive and industrial applications
- [Evaluation of EC-01F-Kit, the EC-01F NB-IoT development board] Flash
- What do you think about the 360 annual meeting special prize exemption coupons?
- [Anxinke NB-IoT Development Board EC-01F-Kit] Part 1: Getting to know EC-01F-Kit
- [Jihai APM32E103VET6S development board] Evaluation 3, TFT LCD
- OV7670 simple driver for MSP430F5438A
- Looking back at 2018 and looking forward to 2019
- [Sipeed LicheeRV 86 Panel Review] 2. Firmware Burning, Linux System Test
- How-to video | Achieve seamless interoperability in your next IoT design
- MATLAB simulation model for online parameter identification of permanent magnet synchronous motor based on RLS least squares method
- Research on constant false alarm rate control technology of laser radar based on FPGA (1)