O Introduction
At present, AC speed control electric drive has become the mainstream of electric speed control drive. With the development of modern AC motor speed control theory and the improvement of power electronic device functions, especially the development of microcomputers and large-scale integrated circuits, AC motor speed control has made a breakthrough.
The control method of constant voltage-frequency ratio (U/F=constant) is open-loop speed control. It does not require a speed sensor, has a simple control circuit, and the load can be a general standard asynchronous motor. Therefore, it has strong versatility and good economy. It is a control method that is currently used more in general frequency converter products and is widely used in speed regulation systems of fans and pumps.
The voltage space vector method (SVPWM), also known as "flux tracking control", is different from the classic SPWM control which focuses on making the output voltage as close to a sine wave as possible. It starts from the perspective of the motor and focuses on how to make the motor obtain a circular rotating magnetic field with a constant amplitude.
This system designs a hardware platform with TMS320LF2407A as the central processor, and realizes constant voltage-frequency ratio control of AC motor through SVPWM control method. On this basis, the software design of variable frequency speed control system is given.
1 Space Voltage Vector PWM Principle
Theoretical analysis shows that: the three-phase symmetrical sinusoidal voltage generates a voltage space vector with constant amplitude and rotating at a constant speed, and when this voltage space vector is added to the motor, it will generate a stator flux space vector with constant amplitude and rotating at a constant speed, and the motion trajectory of the stator flux vector vertex forms a circular space rotating magnetic field. Therefore, the trajectory problem of the rotating magnetic field of the motor can be transformed into the motion trajectory problem of the voltage space vector.
The SVPWM method starts from the perspective of the motor, regards the inverter and the AC motor as one, and focuses on how to make the motor obtain a circular rotating magnetic field with a constant amplitude.
1.1 Basic voltage space vector
Figure 1 is a general voltage-source PWM inverter circuit.
V0-V5 in the figure are 6 power switch tubes, and a, b, and c represent the switch states of the three bridge arms respectively. For each bridge arm, there are two working states, "upper tube is on, lower tube is off", which is called "1" state, and "lower tube is on, upper tube is off", which is called "0" state. The three bridge arms have only two states of "1" or "0", so a, b, and c form a total of eight switch modes of 000, 001, 010, 011, 100, 101, 110, and 111. Among them, the 000 and 111 switch modes are called zero states.
The 8 switching modes correspond to 8 basic voltage vectors. According to the characteristics of their phase angles, they are named as: O000, U0, U60, U120, U180, U240, U300, O111. The voltage vector space is divided into 6 symmetrical sectors according to the 6 effective working vectors, as shown in Figure 2:
1.2 Synthesis of voltage space vector
The way that each effective working vector acts only once in one cycle can only generate a regular hexagonal rotating magnetic field. If we try to form a regular polygonal rotating magnetic field in the stator, we can get an approximate circular rotating magnetic field. Moreover, the more sides of the regular polygon, the better the approximation.
However, if we want to obtain as many polygonal rotating magnetic fields as possible, we must have more inverter switching states. We can use the linear time combination of six non-zero basic voltage space vectors to obtain more switching states. This is the basic idea of voltage space vector PWM.
Among the six sectors of the voltage vector space, when the desired output voltage vector falls in a certain sector, the two sides of the sector are used to equivalently synthesize the desired output vector.
In Figure 3, Ux and Ux±60 represent two adjacent basic voltage space vectors; Uout is the output reference phase voltage vector, whose amplitude represents the amplitude of the phase voltage, and its rotation angular velocity is the angular frequency of the output sinusoidal voltage. Uout can be synthesized by the linear time combination of Ux and Ux±60, which is equal to the vector sum of t1/Tpwm times Ux and t2/Tpwm times Ux±60. Among them, t1 and t2 are the time when Ux and Ux±60 act respectively; Tpwm is the time when Uout acts.
The amplitude and position of the expected output voltage vector can be used to determine the two adjacent basic voltage vectors and the length of their action time, and thus the action time of the zero vector can be obtained.
2 Hardware circuit design of variable frequency speed regulation system based on DSP
The designed system uses TMS320LF2407A as the core controller. The circuit consists of three parts: main circuit, system protection circuit and control circuit. The overall design diagram is shown in Figure 4.
The main circuit consists of a rectifier circuit, a filter circuit, an inverter circuit and an IPM drive circuit. The working principle of the main circuit is to convert the three-phase AC power supply into a pulsating DC voltage through a three-phase bridge rectifier circuit, and then filter it through a large capacitor C to become a smooth and stable DC voltage. The DC voltage is then converted into an AC power with adjustable frequency and voltage through an IPM inverter circuit to form a PWM wave, which is provided to the load motor.
The system protection circuit includes pump-up voltage control, overvoltage and undervoltage protection, current limiting start and IPM fault protection, etc. Overvoltage and undervoltage protection uses resistor voltage division to collect bus voltage and compare it with the specified value to ensure the stability of the bus voltage of the voltage-type inverter; current limiting start is to prevent the instantaneous large current from damaging the diode in the rectifier circuit when the main circuit is turned on. A current limiting resistor R is connected in series in the main circuit. When the capacitor voltage reaches the specified value, R is short-circuited through the relay, and the main circuit enters normal working state.
The control circuit includes DSP minimum system circuit, optocoupler isolation circuit, etc. The minimum system consists of DSP itself and external data SRAM, program SRAM, reset circuit, crystal oscillator, decoding circuit, power conversion circuit. The optocoupler isolation circuit is to reliably isolate the weak current signal output by DSP from the strong current signal of the main circuit.
3. Software Design of Frequency Conversion Speed Regulation System Based on DSP
The most significant feature of the TMS320LF2407A DSP is that it has a powerful built-in event manager module (Event Manager). The EM module has built-in hardware circuits to simplify the generation of symmetrical space vector PWM waveforms to the greatest extent possible.
The generation of a voltage space vector PWM wave is very flexible in the use of zero vector. Usually, the order of action of the basic vector and the zero vector is arranged based on the principle of small switching loss and small harmonic component. Generally, while reducing the number of switching times, the PWM output waveform is made symmetrical as much as possible to reduce the harmonic component.
This article uses the most commonly used seven-segment voltage space vector PWM waveform, which consists of 3 zero vectors and 4 adjacent two non-zero vectors. The zero vector is placed at the beginning, middle and end of the PWM wave respectively.
In this program, the modulation wave frequency f is input from the outside and is assumed to have been converted into a frequency adjustment ratio through f/50 Hz. The carrier frequency and sampling frequency in the program are both 20MHz-z. The modulation wave frequency 0~50Hz frequency conversion function and dead zone function can be realized. The dead zone time is 1.6μs. The DSP crystal oscillator is 10MHz, internally doubled, the clock frequency is 20MHz, and the counting period is 50ns.
3.1 Main program design
The main program is to initialize and convert the external input frequency adjustment ratio into angular frequency, and determine the amplitude of the reference voltage according to the U/F curve.
3.2 Design of interrupt subroutine
The interrupt subroutine works to calculate the comparison values of the three comparison registers of the next PWM cycle in each PWM cycle and send them to the comparison registers. The three-phase SVPWM wave is output by the PWM1~6 pins of the DSP.
4 Experimental Results
Based on the above software and hardware design, a frequency converter is constructed to perform frequency conversion and speed regulation on the AC asynchronous motor. The experimental object is a squirrel cage asynchronous motor with the following parameters: model: JO-11-2, rated power 1kW, rated voltage 380V, rated current: 2.31A. The waveform in the experiment is measured by a digital oscilloscope. The experimental process tests the current of the motor at different frequency outputs. It can be seen from the experimental waveform that its output current is basically a sine wave.
5 Conclusion
Based on the space voltage vector control technology, this paper designs a speed open-loop variable frequency speed control system and gives the software design of the variable frequency speed control system. The test shows that the control performance and accuracy of this system are good.
Previous article:DSP Design of Audio Signal Acquisition and AGC Algorithm
Next article:Radar-type life detector based on DSP chip TMS320
Recommended ReadingLatest update time:2024-11-17 07:39
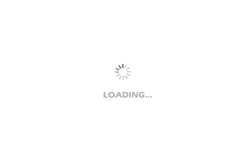
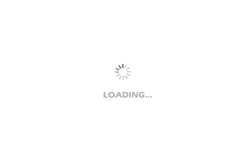
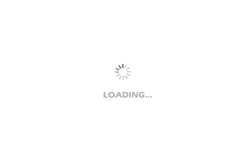
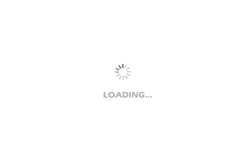
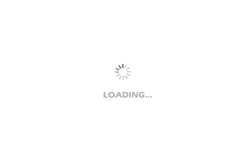
- Popular Resources
- Popular amplifiers
- Huawei's Strategic Department Director Gai Gang: The cumulative installed base of open source Euler operating system exceeds 10 million sets
- Analysis of the application of several common contact parts in high-voltage connectors of new energy vehicles
- Wiring harness durability test and contact voltage drop test method
- Sn-doped CuO nanostructure-based ethanol gas sensor for real-time drunk driving detection in vehicles
- Design considerations for automotive battery wiring harness
- Do you know all the various motors commonly used in automotive electronics?
- What are the functions of the Internet of Vehicles? What are the uses and benefits of the Internet of Vehicles?
- Power Inverter - A critical safety system for electric vehicles
- Analysis of the information security mechanism of AUTOSAR, the automotive embedded software framework
Professor at Beihang University, dedicated to promoting microcontrollers and embedded systems for over 20 years.
- Innolux's intelligent steer-by-wire solution makes cars smarter and safer
- 8051 MCU - Parity Check
- How to efficiently balance the sensitivity of tactile sensing interfaces
- What should I do if the servo motor shakes? What causes the servo motor to shake quickly?
- 【Brushless Motor】Analysis of three-phase BLDC motor and sharing of two popular development boards
- Midea Industrial Technology's subsidiaries Clou Electronics and Hekang New Energy jointly appeared at the Munich Battery Energy Storage Exhibition and Solar Energy Exhibition
- Guoxin Sichen | Application of ferroelectric memory PB85RS2MC in power battery management, with a capacity of 2M
- Analysis of common faults of frequency converter
- In a head-on competition with Qualcomm, what kind of cockpit products has Intel come up with?
- Dalian Rongke's all-vanadium liquid flow battery energy storage equipment industrialization project has entered the sprint stage before production
- Allegro MicroSystems Introduces Advanced Magnetic and Inductive Position Sensing Solutions at Electronica 2024
- Car key in the left hand, liveness detection radar in the right hand, UWB is imperative for cars!
- After a decade of rapid development, domestic CIS has entered the market
- Aegis Dagger Battery + Thor EM-i Super Hybrid, Geely New Energy has thrown out two "king bombs"
- A brief discussion on functional safety - fault, error, and failure
- In the smart car 2.0 cycle, these core industry chains are facing major opportunities!
- Rambus Launches Industry's First HBM 4 Controller IP: What Are the Technical Details Behind It?
- The United States and Japan are developing new batteries. CATL faces challenges? How should China's new energy battery industry respond?
- Murata launches high-precision 6-axis inertial sensor for automobiles
- Ford patents pre-charge alarm to help save costs and respond to emergencies
- Mobile information think tank, accompanying technical consultant
- Selection of MOS in BMS---
- 【AT-START-F403A Review】Part 4: Comparison and test of internal FLASH parameters of F403A
- VGA Driver and Implementation.pdf
- STM32SPI interrupt can only accept the first two bytes each time
- Wi-Fi HaLow: Making Smart Homes Even Smarter
- [Original] New Driver MM32F031 Development Board Review 3: Discovering and Fixing Bugs in the MM32F031 Library
- BlueNrg-1 and Raspberry Pi communication abnormality
- China's automotive electronics: Forging core competitiveness2
- 【GD32307E-START】Light up an LED