introduction
Traditionally, thermistors, thermocouples, or discrete temperature measurement chips have been used to measure system temperature. Moreover, as systems become faster and their relative size becomes smaller, temperature measurement becomes increasingly important.
However, the cost of these devices increases rapidly if the temperature of multiple test points on the board needs to be measured. This in turn creates an urgent need for efficient, compact and low-cost temperature measurement methods, with applications ranging from high-speed computers, telecommunications network switching equipment to industrial temperature control such as portable electronics, biomedical devices, motor control and automotive electronics.
Because timely and accurate temperature correction is critical in many applications, today's intelligent systems use cooling systems and balance their operation based on the system's internal conditions. Such systems have the additional advantage of using on-board temperature sensing diodes (or diode-connected transistors) to track and measure the temperature of specific devices. This can indicate system operation when an abnormal temperature occurs, indicating that a component is not operating correctly. The intelligent system can then respond by taking corrective action and/or providing an out-of-bounds alert to system management.
In addition to performing other system management tasks, today's mixed-signal FPGAs are also intelligent thermal management systems, allowing designers to easily and accurately measure temperatures at multiple locations at a low cost.
Checking and measuring voltages using mixed-signal FPGAs
When studying the relationship between the absolute temperature of a diode and its forward voltage under constant current, the change in the diode forward voltage drop with temperature is approximately 2mV/C. To improve the measurement accuracy and eliminate the difference between different diodes, the ratio data of two known current values and the measured values is used. Figure 1 shows the effect of temperature on the diode voltage and current.
This measurement is expressed by the following equation:
T =DV * q / (n * k * ln(IH / IL) (1)
Where T = absolute temperature, DV = the voltage difference between the diode at high and low currents, q = 1.602×10-19 coulombs (the charge of an electron), n = 1 (ideal factor, assumed to be 1 here), k = 1.38×10-23 J/K (Boltzmann constant), IH = high current intensity, IL = low current intensity.
This article uses Actel's mixed-signal Fusion PSC (Programmable System-on-Chip) as a real-world application case. The mixed-signal FPGA will provide two known current sources (100mA and 10mA) (see Figure 2) and measure the voltage difference through the built-in analog-to-digital
[page]
Solve equation (1) to obtain the conversion voltage to be sent to the ADC, which is equation (2) below; and then obtain the voltage value measured by the mixed signal FPGA.
DV = T * n * k * ln(IH / IL) / q (2)
DV = 298 * 1 * (1.38x10-23 J/K) * ln(10) / (1.602x10-19C)
DV = 298 * 0.00019835 = 59 mV
At room temperature, the voltage value is relatively small. The temperature monitoring circuit in the mixed-signal FPGA has a built-in 12.5x amplifier to amplify the predicted signal, making the temperature signal more accurately measured. Therefore, considering that the voltage signal will be amplified before reaching the ADC, equation (2) needs to be modified, namely:
DV = (T * n * k * ln(IH / IL) / q ) *12.5
DV = (298 * 0.00019835) * 12.5 = 738 mV
Noise filtering
Typically, temperature measurements contain unwanted noise. To remove the noise, it is common practice to average multiple measurements and use the average result. Fortunately, temperature is a relatively slow-changing parameter, so you don't have to worry about actual signal changes when measuring multiple times (often up to 1,000 times). Mixed-signal FPGAs can easily average these measurements by filtering system-level noise. The software tools used also generally provide a convenient graphical user interface (GUI) that the user can use to set the averaging or filtering factors.
Operate within a defined temperature range
Now that the temperature can be measured at a certain location within a system, how can a designer use this information?
Most systems are expected to operate within certain temperature ranges. Therefore, knowing these operating temperature ranges of the system is essential so that the system can respond accordingly. Mixed-signal FPGAs can easily monitor the average temperature and compare it to user-defined temperature thresholds to set appropriate flags. Moreover, since such FPGAs are programmable logic devices, different thresholds can be set.
To illustrate this, let's take an example. Suppose a user defines three operating temperature ranges for a telecom line card: normal, hot, and overheated. The temperature reading will be used as a feedback signal to control the amount of cooling required by the system.
When the average temperature is in the "normal" range, no changes are required to the system; the system is operating under ideal conditions and the "normal" flag is set. However, some internal or external factors may affect the system, causing the operating temperature to move from the "normal" range to the "hot" range. At this time, the "normal" flag will be cleared and the "hot" flag will be set. Although this range is still a valid operating temperature range by definition, the system is approaching a temperature that may cause damage to the system. Moreover, if the cooling system is overloaded or abnormal at this time, the temperature will continue to rise, eventually causing damage to the line cards in the system. Intelligent thermal management systems are used to prevent this from happening.
The system now begins to take corrective action. The line card notifies the system master (i.e., the mixed-signal FPGA) that the system temperature has risen. The system master then increases the output of the cooling system to suppress the temperature rise; that is, the cooling system should increase its output to return the system to the "normal" temperature range and set the appropriate flag. In addition, the mixed-signal FPGA acting as the master can also record the thermal event and the time it occurred in the embedded flash memory for maintenance personnel to retrieve later.
When the average temperature changes from "hot" to "overheated", the mixed-signal FPGA will take more serious measures because the system is in an extremely dangerous state. The line card will then start shutting down the program to prevent damage. The line card can then send a signal to the main control to tell it that the program has been shut down. The overheating of the line card and the time of occurrence will be saved to the embedded flash memory for post-debugging and fault analysis. In addition, the mixed-signal FPGA will shut down the power supply of the line card to prevent damage.
Conclusion
Thermal management is becoming an increasingly important aspect of many designs today as smaller and faster devices are used in a variety of applications. With mixed-signal FPGAs, the temperature of many locations on a system board can be measured by simply connecting some diode-connected transistors. Mixed-signal FPGAs can also filter noise signals for more accurate measurements. Because of the use of programmable logic devices, very flexible thermal windows (i.e., different temperature ranges) can be established, and each window can be defined with its own unique system response, including simple time stamping of thermal events and shutting down the system to avoid permanent thermal damage. Mixed-signal FPGAs can integrate thermal management functions into a comprehensive system management solution in a simple and low-cost way.
Previous article:Design of μC/OS-II Task Management Hardware Based on FPGA
Next article:Research and Design of Electric Bicycle Charging System Based on CPLD
Recommended ReadingLatest update time:2024-11-16 20:42
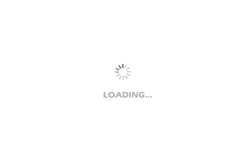
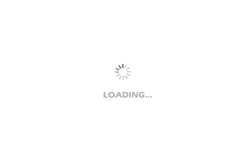
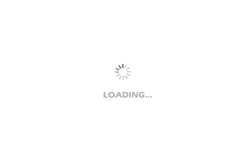
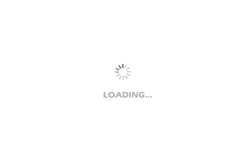
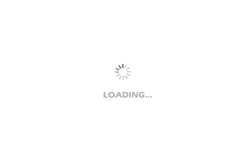
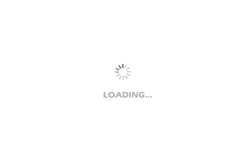
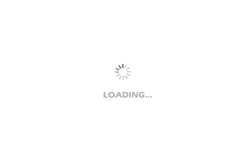
- Popular Resources
- Popular amplifiers
-
Analysis and Implementation of MAC Protocol for Wireless Sensor Networks (by Yang Zhijun, Xie Xianjie, and Ding Hongwei)
-
MATLAB and FPGA implementation of wireless communication
-
Intelligent computing systems (Chen Yunji, Li Ling, Li Wei, Guo Qi, Du Zidong)
-
Summary of non-synthesizable statements in FPGA
- Huawei's Strategic Department Director Gai Gang: The cumulative installed base of open source Euler operating system exceeds 10 million sets
- Analysis of the application of several common contact parts in high-voltage connectors of new energy vehicles
- Wiring harness durability test and contact voltage drop test method
- Sn-doped CuO nanostructure-based ethanol gas sensor for real-time drunk driving detection in vehicles
- Design considerations for automotive battery wiring harness
- Do you know all the various motors commonly used in automotive electronics?
- What are the functions of the Internet of Vehicles? What are the uses and benefits of the Internet of Vehicles?
- Power Inverter - A critical safety system for electric vehicles
- Analysis of the information security mechanism of AUTOSAR, the automotive embedded software framework
Professor at Beihang University, dedicated to promoting microcontrollers and embedded systems for over 20 years.
- Innolux's intelligent steer-by-wire solution makes cars smarter and safer
- 8051 MCU - Parity Check
- How to efficiently balance the sensitivity of tactile sensing interfaces
- What should I do if the servo motor shakes? What causes the servo motor to shake quickly?
- 【Brushless Motor】Analysis of three-phase BLDC motor and sharing of two popular development boards
- Midea Industrial Technology's subsidiaries Clou Electronics and Hekang New Energy jointly appeared at the Munich Battery Energy Storage Exhibition and Solar Energy Exhibition
- Guoxin Sichen | Application of ferroelectric memory PB85RS2MC in power battery management, with a capacity of 2M
- Analysis of common faults of frequency converter
- In a head-on competition with Qualcomm, what kind of cockpit products has Intel come up with?
- Dalian Rongke's all-vanadium liquid flow battery energy storage equipment industrialization project has entered the sprint stage before production
- Allegro MicroSystems Introduces Advanced Magnetic and Inductive Position Sensing Solutions at Electronica 2024
- Car key in the left hand, liveness detection radar in the right hand, UWB is imperative for cars!
- After a decade of rapid development, domestic CIS has entered the market
- Aegis Dagger Battery + Thor EM-i Super Hybrid, Geely New Energy has thrown out two "king bombs"
- A brief discussion on functional safety - fault, error, and failure
- In the smart car 2.0 cycle, these core industry chains are facing major opportunities!
- The United States and Japan are developing new batteries. CATL faces challenges? How should China's new energy battery industry respond?
- Murata launches high-precision 6-axis inertial sensor for automobiles
- Ford patents pre-charge alarm to help save costs and respond to emergencies
- New real-time microcontroller system from Texas Instruments enables smarter processing in automotive and industrial applications
- Qorvo Launches World's Smallest 20-Watt Single-Chip Programmable Motor Control and Drive Solution for Brushless DC Motors
- MSP430 and ATK-NEO-6M GPS module
- 21 "Wanli" Raspberry Pi car - motor control learning (4-wheel speed control)
- Award-winning live broadcast: Microchip&avnet series live broadcast first collection
- HGI HC32A460 series function comparison chart
- PCB drawing process shortcut keys
- How to start power supply design
- Has anyone tried the baud rate adaptation of LIN communication?
- Analog Electronics Design
- Will adding a nonlinear link to the RC bridge sine wave oscillation circuit cause waveform distortion?