0 Introduction
In modern industrial production, the scale of production continues to expand, and it is developing in the direction of large-scale, high-speed, automated and continuous production. Therefore, the requirements for the performance of mechanical equipment are getting higher and higher. Many large-scale petroleum, chemical, petrochemical, electric power, steel and other departments have adopted a single-machine, full-load, continuous production operation mode, among which large-scale rotating machinery has become the key equipment in modern large-scale production. Once a shutdown failure occurs, it will lead to the shutdown of the entire plant, and the economic loss is very huge. At the same time, it may also cause major casualties. As a result, the online state monitoring and fault diagnosis technology of large rotating machinery came into being. How to obtain a large and wide range of state quantities (vibration, force, displacement, noise, temperature, pressure and flow, etc.) is the key. This article introduces a multi-function synchronous data acquisition card based on TMS320F2812. The DSP control chip on the card can not only realize the collection of multiple data, but also perform real-time signal processing on the collected data, greatly improving the performance of the entire system.
1 TMS320F2812 Architecture
TMS320F2812 is the best performing chip in the TMS320C28X series, with a maximum frequency of 150MHz, a processing speed of up to 150MIPS, and an instruction cycle of 6.67ns.
Compared with the previous generation products in the TMS320C2000TM platform, the program bus of F2812 includes a 22-bit address bus and a 32-bit data bus, and the data bus includes a 32-bit address bus and a 32-bit data bus. Compared with the 16-bit address bus of C24X/C240X, F2812 has greatly increased the addressable range. At the same time, the 32-bit data bus can implement single-cycle 32-bit instructions. Its on-chip 32×32-bit MAC has the ability to process 64-bit numbers, which can be used to process high-precision digital operations and can completely replace other more expensive floating-point processors. In the spectrum analysis of vibration signals, this advantage is even more obvious. In terms of interrupt response, the automatic context saving function of F2812 speeds up the interrupt response speed, and users can complete more asynchronous events in a shorter time limit, which greatly improves the real-time performance of the system in a multi-channel signal acquisition system.
In terms of peripherals, F2812 also has many new features. In addition to retaining the 4 16-bit general-purpose timers of the previous generation, F2812 has added 3 32-bit timers. It can more conveniently realize the acquisition of a wide range of shaft speed signals and provide more flexible data sampling modes. F2812 has a 12-bit enhanced A/D converter with an A/D conversion rate of up to 80ns. The two independent 8-way analog switches provide users with a way to collect different types of signals at the same time. In terms of on-chip memory, F2812 includes 128K words of FLASHMEMORY, 1K words of 0TPMEMORY, 18K words of on-chip RAM and 4K words of BOOT ROM. The rich on-chip storage resources can meet the needs of users to process large amounts of data. In terms of security, F2812 uses a 128-bit password to protect the user's program.
2 Hardware Implementation of Data Acquisition Card
The hardware implementation of the data acquisition card utilizes many new features of F2182. The data acquisition card can process: 16 asynchronous or synchronous analog signals, 16 digital signals, and 6 speed signals. It uses a PCI interface to connect to the host computer. The system structure is shown in Figure 1.
2.1 Implementation of speed signal acquisition
According to the actual situation of rotating machinery in industrial sites, the speed range collected by data acquisition cards is generally 30 to 18,000 r/min (cycle range is 33ms to 2s). Such a large speed range places requirements on both the count pulse and the count bit number of the timer. If the count pulse of the timer is too large, the resolution is reduced; but if the count pulse is too small, the counter bit number needs to be large enough.
The built-in 16-bit timer of the previous generation products of the C2000TM series could hardly meet the requirements, and generally multiple timers were cascaded to meet the requirements. The three newly added 32-bit timers of the F2812 make up for the shortcomings of the previous series of DSP products.
The event management module EV of F2812 has 6 capture units, and the Schmitt trigger of each unit can capture the jump of the relevant pin. The jump that can be monitored can be the rising edge, the falling edge, or both. The interrupt function and timer of the capture unit can easily realize the measurement of the speed cycle and provide the sampling base frequency for the vibration test of the shaft. The measurement process is shown in Figure 2.
2.2 Implementation of analog signal acquisition
The TMS320F2812 chip integrates a pseudo dual 12-bit A/D converter module. There is actually only one A/D converter inside the module. Under the control of the internal logic, it can sample and convert twice continuously at a very fast speed, which is equivalent to two A/D converters. The user can start the two A/D converters for sampling at the same time, or start a certain A/D converter and let it sample twice continuously.
Compared with traditional A/D, embedded A/D has the following characteristics: after the hardware resources of the A/D module are configured, users can use software instructions to start A/D sampling at any time and obtain the results of A/D conversion. Unlike traditional A/D, the hardware resource configuration of the acquisition function unit is also partially completed by software.
By using the F2812 internal enhanced A/D, the acquisition and A/D conversion of synchronous and asynchronous analog signals can be realized on one acquisition card. Its schematic diagram is shown in Figure 4.
There are two independent 8-way analog switches in the F2812 chip, which can be used alone or in cascade. As shown in Figure 4, the synchronous signal is sent to the ADCINA module, and other signals are directly sent to the ADCINB module, and then the 12-bit A/D conversion module inside the DSP performs A/D conversion. Users can also adjust the external sampling circuit according to actual applications to meet different requirements.
The A/D converter integrated in the TMS320F2812 chip is used for data acquisition. The program first initializes the A/D. When the A/D is very busy, 16 A/D channels are started for conversion, and the main program enters an infinite loop. When the A/D conversion is completed normally, the interrupt service subroutine is entered. The interrupt service program reads the 16 A/D conversion results into the array al[16] and starts the 16 A/D channels for conversion again, and the cycle repeats. The program design uses C++ language to write the source program. The A/D initialization subroutine block diagram is shown in Figure 6. The interrupt service subroutine flow is shown in Figure 7.
2.3 Implementation of digital signal acquisition
Digital signals can be directly obtained using the digital I/0 of F2812. F2812 has up to 56 I/0 shared pins. Most I/0s can be used as ordinary I/0 pins or other functional pins. By programming the I/0 control register, you can specify whether these shared pins are I/0 or other functional pins. When the pin is I/0, the result of reading the corresponding bit of the data and direction register of the I/0 module can get the value of the measured digital signal. If the result read is 0, the corresponding pin is low level; if the result is 1, the corresponding pin is high level.
3. Software modules of data acquisition card
The software on the data acquisition card is mainly divided into modules such as system configuration, speed acquisition, analog signal acquisition conversion, digital signal acquisition, data processing and upper communication. In actual application, it can be configured according to needs.
4 Conclusion
This development platform is used for the analog data acquisition of parameters such as flow, temperature, pressure, seal differential pressure, vibration displacement at each point, catalyst dust content, etc. in the flue gas turbine vibration fault detection in the petrochemical field. Through analysis, it can be seen that because the TMS320F2812 chip contains A/D and SRAM, SRAM replaces the expensive FIFO, so this acquisition method can greatly improve the sampling speed and accuracy, and can reduce the cost and time of hardware design, laying a good foundation for the next step of DSP-based real-time digital signal processing and analysis design.
Previous article:Design of USB Interface IP Core Based on FPGA
Next article:FPGA-based PCI bus interface hardware debugging strategy
Recommended ReadingLatest update time:2024-11-16 16:46
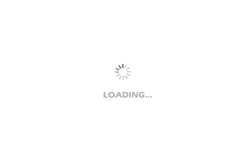
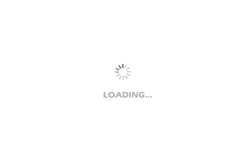
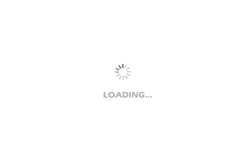
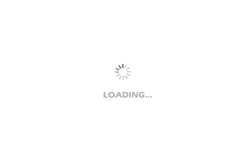
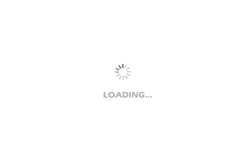
- Popular Resources
- Popular amplifiers
- Huawei's Strategic Department Director Gai Gang: The cumulative installed base of open source Euler operating system exceeds 10 million sets
- Analysis of the application of several common contact parts in high-voltage connectors of new energy vehicles
- Wiring harness durability test and contact voltage drop test method
- Sn-doped CuO nanostructure-based ethanol gas sensor for real-time drunk driving detection in vehicles
- Design considerations for automotive battery wiring harness
- Do you know all the various motors commonly used in automotive electronics?
- What are the functions of the Internet of Vehicles? What are the uses and benefits of the Internet of Vehicles?
- Power Inverter - A critical safety system for electric vehicles
- Analysis of the information security mechanism of AUTOSAR, the automotive embedded software framework
Professor at Beihang University, dedicated to promoting microcontrollers and embedded systems for over 20 years.
- Innolux's intelligent steer-by-wire solution makes cars smarter and safer
- 8051 MCU - Parity Check
- How to efficiently balance the sensitivity of tactile sensing interfaces
- What should I do if the servo motor shakes? What causes the servo motor to shake quickly?
- 【Brushless Motor】Analysis of three-phase BLDC motor and sharing of two popular development boards
- Midea Industrial Technology's subsidiaries Clou Electronics and Hekang New Energy jointly appeared at the Munich Battery Energy Storage Exhibition and Solar Energy Exhibition
- Guoxin Sichen | Application of ferroelectric memory PB85RS2MC in power battery management, with a capacity of 2M
- Analysis of common faults of frequency converter
- In a head-on competition with Qualcomm, what kind of cockpit products has Intel come up with?
- Dalian Rongke's all-vanadium liquid flow battery energy storage equipment industrialization project has entered the sprint stage before production
- Allegro MicroSystems Introduces Advanced Magnetic and Inductive Position Sensing Solutions at Electronica 2024
- Car key in the left hand, liveness detection radar in the right hand, UWB is imperative for cars!
- After a decade of rapid development, domestic CIS has entered the market
- Aegis Dagger Battery + Thor EM-i Super Hybrid, Geely New Energy has thrown out two "king bombs"
- A brief discussion on functional safety - fault, error, and failure
- In the smart car 2.0 cycle, these core industry chains are facing major opportunities!
- The United States and Japan are developing new batteries. CATL faces challenges? How should China's new energy battery industry respond?
- Murata launches high-precision 6-axis inertial sensor for automobiles
- Ford patents pre-charge alarm to help save costs and respond to emergencies
- New real-time microcontroller system from Texas Instruments enables smarter processing in automotive and industrial applications
- Three-port network
- RSL10 drives ink screen
- GoKit Case Study: Gizwits IoT Development Platform’s Pet House Transformed into an Air Quality Detector
- Embedded licensing: why not and why not?
- I found a 1963 "Electron Tube Handbook"
- How to extract the effective value of fundamental wave and each harmonic in MATLAB?
- Analysts predict Bluetooth location services will grow at a CAGR of 32% by 2025
- TI blog post - Introduction to basic parameters of analog switches and multiplexers
- Bluetooth chip
- [Mil MYB-YT507 development board trial experience] Unboxing + HELLOWORLD