Today's cars have entered an era of intelligent and environmentally friendly design. In terms of intelligence, digital electronic technology is used to improve the safety and comfort of cars, and in terms of environmental protection, hybrid and electric vehicles are used to achieve energy saving and carbon saving. Therefore, today's cars are becoming more and more electronic. From infotainment, body, safety to powertrain, the use of electronic components for sensing and control has penetrated into every corner of the car.
In various systems of automotive electronics, microcontrollers (MCUs) are often used as the core of operation and control. The heavy reliance of automobiles on electronic systems has also stimulated the rapid growth of the automotive microcontroller market. Automotive microcontrollers cover low-, medium-, and high-end product levels such as 8-bit, 16-bit, and 32-bit, and each has its own suitable application system, which is roughly as follows:
8-bit MCU: Mainly used in various subsystems of the vehicle body, including fan control, air conditioning control, wipers, sunroof, window lifts, low-level instrument panels, junction boxes, seat control, door control modules and other lower-level control functions.
16-bit MCU: Mainly used in powertrain systems, such as engine control, gear and clutch control, and electronic turbine systems; also suitable for chassis mechanisms, such as suspension systems, electronic power steering, torque distribution control, and electronic pumps, electronic brakes, etc.
32-bit MCU: Main applications include instrument panel control, body control, multimedia information system (Telematics), engine control, and emerging intelligent and real-time safety systems and power systems, such as pre-crash, adaptive cruise control (ACC), driver assistance system, electronic stability program and other safety functions, as well as complex X-by-wire and other transmission functions.
Common interfaces for automotive MCUs: CAN & LIN
As today's automobiles have higher and higher requirements for application functions, the systems that need to be integrated are becoming more and more complex, which has led to an increasing demand for high-end 32-bit MCUs in automotive electronic systems. Such automotive MCUs are often placed in operating environments with high heat, dust, severe vibration, and severe electronic interference, so the tolerance requirements are much higher than those of general-purpose MCUs. In addition, in the automotive application environment, automotive MCUs must be connected to multiple automotive electronic control units (ECUs), among which the most common transmission interfaces are CAN and LIN.
CAN is divided into high-speed CAN and low-speed CAN. The transmission rate of high-speed CAN can reach 1 Mbps, which is suitable for applications that emphasize real-time response, such as ABS and EMS; low-speed CAN can reach 125 Kbps, which is suitable for the control of lower-speed body parts. In addition, the types of CAN controllers can be divided into the old 1.x, the standard 2.0A and the extended 2.0B. The newer the specification, the better the performance. Among them, 2.0B can be divided into passive type and active type.
LIN is a communication solution with lower speed and lower cost than CAN. It adopts the concept of one master node and multiple slave nodes (supporting up to 16 nodes), with a data transmission rate of up to 20 kbps and a bus cable length that can be extended to up to 40 meters. It is very suitable as a distributed communication solution for simpler systems such as climate control, mirrors, door modules, seats, smart switches , and low-cost sensors.
The following will introduce the new generation of MCU technology for instrument panel control and body control, and use Fujitsu's new generation MB91770 series and MB91725 series new microcontrollers as design references. Please refer to (Figure 1).
Figure 1 Application of instrument panel control and body control MCU in automobiles (taking MB91770 series and MB91725 series as examples)
Essentials of automobile instrument panel and body control design
The dashboard of a car provides a variety of real-time visual information for driving. This information is an important reference for decision-making and must be quickly and accurately delivered to the driver. In addition, the air conditioning and body control module (BCM) system in the car is responsible for providing a comfortable riding environment for the driver and passengers. The air conditioning system quickly reduces the temperature inside the car to a more comfortable level by performing optimal control, and maintains a comfortable temperature inside the car based on information from various sensors. The BCM system can centrally control multiple ECUs, such as doors, seats, and combination switches.
Whether it is the MCU for instrument panel control or body control, it must provide higher processing performance, the ability to handle a large number of network nodes, interface functions that support multiple peripheral connections, functions that can expand the scope of circuit board layout, advanced memory architecture, and a more convenient development environment. These design requirements are analyzed as follows:
[page]
1. High processing performance:
To improve the processing performance of MCU, we must start from its core and software and hardware system architecture. Take Fujitsu's new generation MCU FR81S CPU core as an example. Its working performance reaches 1.3MIPS/MHz, which is 30% higher than the previous generation FR60 core. Because it has a built-in single-precision floating-point unit (FPU), it can meet the requirements of image processing systems and those systems that require floating-point operation functions (such as brake control). In addition, through hardware FPU support, software programs can be simplified and computing performance can be improved.
2. Large number of network node processing capabilities:
There are a large number of built-in ECUs in the CAN network of today's cars. Their size is constantly expanding as the number of nodes increases, so automotive MCUs must support more message buffers. The previous generation of 32-bit CAN microcontrollers can provide up to 32 built-in message buffers, but now it is insufficient. The new generation of Fujitsu MCUs can support up to 64 built-in message buffers, and support CAN 2.0A/B specifications and provide a high transmission rate of 1Mbps.
3. Extensive interface support capabilities:
The peripherals connected to automotive MCUs are quite diverse, and the interfaces connected may be UART, frequency synchronous serial, LIN-UART and I2C, so flexible interface connection capabilities are required. In order to meet this demand, Fujitsu uses the built-in multi-function serial interface as a serial communication interface, and switches the above interfaces through software to flexibly support the communication specifications of external components and increase the freedom of system design. The new series of MCUs also provide 6 channels of LIN-UART, so that it can communicate with more control units; among them, the MB91725 series has multiple channels with timer functions and A/D converters, which makes it easier to achieve the integration of various functions. Please refer to (Figure 2).
Figure 2: Using serial interfaces to achieve flexible communication interface function integration
4. Features that extend the scope of board layout:
Since the layout design of automotive circuit board systems is quite diverse, automotive MCUs must be able to meet the requirements of these designs. Some feasible practices include configuring an independent power supply for the external bus interface terminal, so that there is no need to install a level converter on the ECU board. The power supply range of this external bus interface terminal should be wide (such as covering 3.0V to 5.5V), so that it can be flexibly connected to the unit memory or image ASIC.
Another approach is to give the MCU a built-in I/O redistribution function, which can change the allocation of I/O ports through software settings. In this way, designers can connect to specific peripherals more flexibly, thereby greatly increasing the freedom of circuit board layout.
5. Advanced memory architecture:
In order to improve the flexibility of work processing, today's automotive microcontroller systems often have built-in embedded memory (Flash). In the past, Flash was only used for program storage, but the architecture of the new generation of MCUs also includes Flash for data. This architecture not only increases the data writing speed, but also reduces the area of the circuit board because E2PROM is no longer required. In addition, storing data and programs in the Flash memory of the microcontroller at the same time also helps prevent information leakage.
6. More convenient development environment:
Generally, products must use the ICE main unit and the evaluation chip for verification to perform system verification. In order to reduce the complexity of verification, we provide an on-chip debugging method for the new generation of MCU products. It uses a single-wire debugging interface to achieve automotive evaluation or consistency testing , and can use a universal coaxial cable to achieve communication between a small ICE main unit and a target circuit board within a range of up to 10 meters. This can simplify automotive evaluation that is difficult to achieve conventionally.
Figure 3: Using on-chip debugging to achieve automotive evaluation
in conclusion
The electronic systems in a car are becoming more and more complex, and the reliance on automotive MCUs is also increasing. The design of the car dashboard and body control must provide accurate and rapid auxiliary information for the driver, as well as a convenient and comfortable riding space. Therefore, the relevant MCU must also meet higher performance and more flexible design requirements to help the development of application functions.
Previous article:A Passive Keyless Entry solution with door touch switch function
Next article:Overcoming the technical bottleneck of high brightness (HB) LED integration solutions in automotive systems
Recommended ReadingLatest update time:2024-11-16 19:58
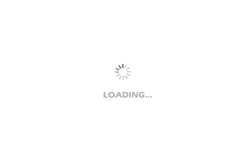
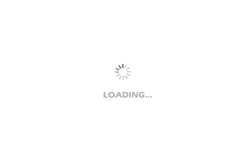
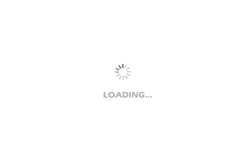
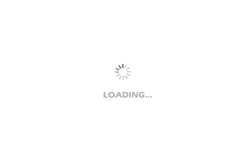
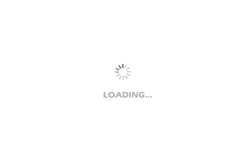
- Popular Resources
- Popular amplifiers
- Car key in the left hand, liveness detection radar in the right hand, UWB is imperative for cars!
- After a decade of rapid development, domestic CIS has entered the market
- Aegis Dagger Battery + Thor EM-i Super Hybrid, Geely New Energy has thrown out two "king bombs"
- A brief discussion on functional safety - fault, error, and failure
- In the smart car 2.0 cycle, these core industry chains are facing major opportunities!
- The United States and Japan are developing new batteries. CATL faces challenges? How should China's new energy battery industry respond?
- Murata launches high-precision 6-axis inertial sensor for automobiles
- Ford patents pre-charge alarm to help save costs and respond to emergencies
- New real-time microcontroller system from Texas Instruments enables smarter processing in automotive and industrial applications
- Innolux's intelligent steer-by-wire solution makes cars smarter and safer
- 8051 MCU - Parity Check
- How to efficiently balance the sensitivity of tactile sensing interfaces
- What should I do if the servo motor shakes? What causes the servo motor to shake quickly?
- 【Brushless Motor】Analysis of three-phase BLDC motor and sharing of two popular development boards
- Midea Industrial Technology's subsidiaries Clou Electronics and Hekang New Energy jointly appeared at the Munich Battery Energy Storage Exhibition and Solar Energy Exhibition
- Guoxin Sichen | Application of ferroelectric memory PB85RS2MC in power battery management, with a capacity of 2M
- Analysis of common faults of frequency converter
- In a head-on competition with Qualcomm, what kind of cockpit products has Intel come up with?
- Dalian Rongke's all-vanadium liquid flow battery energy storage equipment industrialization project has entered the sprint stage before production
- Allegro MicroSystems Introduces Advanced Magnetic and Inductive Position Sensing Solutions at Electronica 2024
- Car key in the left hand, liveness detection radar in the right hand, UWB is imperative for cars!
- After a decade of rapid development, domestic CIS has entered the market
- Aegis Dagger Battery + Thor EM-i Super Hybrid, Geely New Energy has thrown out two "king bombs"
- A brief discussion on functional safety - fault, error, and failure
- In the smart car 2.0 cycle, these core industry chains are facing major opportunities!
- The United States and Japan are developing new batteries. CATL faces challenges? How should China's new energy battery industry respond?
- Murata launches high-precision 6-axis inertial sensor for automobiles
- Ford patents pre-charge alarm to help save costs and respond to emergencies
- New real-time microcontroller system from Texas Instruments enables smarter processing in automotive and industrial applications
- pyRTOS(2):Tasks
- 【AT-START-F403A Review】2. Transplant AN0028--Locate HardFault (including simplified version project files)
- 【Silicon Labs Development Kit Review】Secure Code Testing
- Wireless chip faster than 5G is born
- Grid automation: a bright future for the rapid development of the power grid
- I think the company is wasting money hiring me
- [DIY] Use mosquito repellent to modify wifi repeater, wifi signal booster
- Capacitive Touch Self-Capacitance Buttons, Sliders, Wheels, and Proximity Sensor Demo Board
- How is this comparator with hysteresis implemented?
- Precautions for using chip ferrite beads