The basic principle of the automobile shock absorber spring fault diagnosis instrument is based on nonlinear spectrum analysis technology. The basic idea of this technology is: according to the input and output data of the shock absorber spring obtained by sampling, the vibration equation of the spring is obtained by using an effective nonlinear system identification method, and then the frequency domain representation of the nonlinear transfer function of the shock absorber spring is obtained by multi-dimensional Fourier transform - Generalized Frequency Response Function (GFRF).
GFRF is a non-parametric model that describes the nonlinear transfer characteristics of the system. It can uniquely characterize the frequency domain characteristics of the system transfer characteristics, so the nonlinear changes in the transfer characteristics before and after the system failure can be accurately reflected through GFRF. When the spring is in normal working state, it only has a first-order GFRF; after the spring fails due to fatigue, the most obvious change is the large-scale appearance of the third-order GFRF. By analyzing the GFRF of the spring system, the working state of the spring can be determined. At present, there is still a lack of effective means for fault diagnosis of automobile shock absorber springs in China, and the practical application based on this principle is still in its infancy at home and abroad, so this instrument has a good application prospect.
1 System Overall Plan
The nonlinear system identification algorithm is huge and complex, and requires high computing power of the system. DSP is a chip specially used for digital signal processing, with strong computing power and fast operation speed, which can meet the requirements of the system. Although the computing power of DSP is very strong, its event management ability is weak, and there are few I/O ports directly supported. In order to conveniently realize human-computer interaction, the DSP and the single-chip microcomputer are used to work together: the single-chip microcomputer is used as the host to control the DSP through the communication interface; at the same time, the single-chip microcomputer's strong peripheral device management ability is used to realize human-computer interface, display and other functions. The main working process is: the input and output signals of the spring are conditioned by the filter circuit, converted into digital signals by the A/D converter, and then enter the DSP for calculation. The diagnostic results are sent to the single-chip microcomputer through the communication interface circuit, and the single-chip microcomputer displays the results on the LCD display and sends them to the PC through the serial port. The single-chip microcomputer controls the working state of the DSP through the communication interface. The system principle block diagram is shown in Figure 1.
2 Hardware Circuit Design
2.1 Signal conditioning circuit
The anti-aliasing filter circuit is composed of an integrated switched capacitor filter MAX280. MAX280 is a fifth-order low-pass filter with an adjustable cutoff frequency. When its clock pin is connected to the internal clock, the maximum cutoff frequency is 1.4 kHz; when the automobile shock absorber spring works stably, the signal frequency does not exceed 500 Hz, so the filter cutoff frequency is set to 700 Hz.
2.2 DSP Circuit
The DSP circuit completes data acquisition and digital filtering, and uses built-in algorithms to complete tasks such as fault diagnosis.
The DSP in this system uses the TMS320VC5409 produced by Texas Instruments (TI), which is a high-speed, cost-effective, low-power 16-bit fixed-point general-purpose DSP chip in the TMS320C54xx series. Its main features include: improved Harvard structure (1 program memory bus, 3 data memory buses and 4 address buses), with dedicated hardware logic CPU, on-chip memory, 6-stage pipeline structure, and dedicated instruction set for on-chip peripherals.
The TMS320VC5409 contains 16K words of on-chip ROM and 32K words of on-chip DARAM. The addressing range of the program space reaches 8M, and the addressing range of the data and I/O space is 64K respectively.
The single-cycle instruction execution time is 10ns, and it is powered by dual power supplies (1.8V and 3.3V). It has JTAG boundary scan emulation logic that complies with the IEEE1149.1 standard. The DSP circuit adopts 16-bit parallel self-boot mode. For TMS320VC5409, the user program is stored in the external data space (8000H~FFFFH), so a FLASH ROM is expanded as data storage space. The FLASH ROM uses INTEL's TE28F400B3T90 (256Kx16), which is divided into 15 blocks (8 blocks of 4K words, 7 blocks of 32K words), and one of them can be erased separately. The programming voltage only needs 3.3V, and the fastest reading speed reaches 90ns. The system expands a piece of SRAM as an external program space. The SRAM uses CYPRESS's CY7C1041BV33 (256Kx16), and the access speed reaches 10ns.
2.3 A/D conversion circuit
Signal acquisition and conversion are completed by AD7874. AD7874 is a 12-bit A/D converter produced by AD. The system requires the input and output signal phases to be synchronized. AD7874 has a built-in sample and hold device, which can realize synchronous sampling of four-way signals. Synchronous sampling can minimize the error of the input and output signal phase matching of the system. The start of A/D conversion is triggered by the rising edge. After the conversion of the four-way signal is completed, an interrupt signal is generated. The sampling frequency of each channel can reach 29 kHz. Since the output of A/D conversion is TTL level, and DSP works in a 3.3V signal environment, a level conversion circuit needs to be added between the output of A/D and the input of DSP. In this system, SN74LVC245 is used to achieve level conversion. The power supply of DSP system is completed by TI's voltage conversion module TPS767D318PWP, which can output two voltages of 3.3V and 1.8V.
2.4 Single-Chip Microcomputer Circuit
The single chip microcomputer circuit realizes the keyboard input response, LCD display and interaction with the PC.
The microcontroller used in this system is AT89C51 from ATMEL. Keyboard management is done through keyboard controller 8279. The LCD module uses VPG12864T (128×64 dot matrix) from Truly, which has a built-in T6963C controller and can work in text or graphic mode. The LCD display interface program is relatively large, so an AT28C256 is expanded as an external program memory. The level of the RS-232 serial port of the PC is incompatible with the TTL level of the serial port of the microcontroller, so MAX232 is used to complete the conversion between the two levels.
[page]
2.5 Communication Circuit
The communication circuit realizes the communication between the single-chip microcomputer and the DSP. Since the data communication volume between the single-chip microcomputer and the DSP is not large, an 8-bit bidirectional latch is used to realize data exchange. The bidirectional latch uses TI's SN74LVC543. When the DSP sends data to the AT89C51, it first latches the data in the SN74LVC543, then sends an interrupt to the AT89C51, and the AT89C51 responds to the interrupt and takes the data from the latch. Vice versa.
3 Software Design
The software design mainly includes DSP programming and single-chip microcomputer programming. The main tasks of the DSP program are to initialize and manage the DSP peripheral circuits and complete the fault diagnosis algorithm. The single-chip microcomputer program includes the keyboard control program, the LCD drive display program, and the program for communicating with the DSP and the PC.
3.1 DSP main program
The DSP main program flow chart is shown in Figure 2.
3.2 Download and guide of DSP program
In this system, the FLASH ROM is a TSOP package, which is soldered on the circuit board. It cannot be burned by a burner, and you can only write the erase program yourself. Write the program code according to the format of the 16-bit parallel boot mode boot table (see Table 1), compile and link it, and then download it to the DSP through the JTAG port; write the erase program of TE28F400B3, and download the program to different locations in the DSP. Run the erase program, and the program code will be written into the FLASH. It should be noted that since the writing speed of FLASH is very slow compared to DSP, after writing a word each time, it is necessary to delay for a sufficient time, otherwise the next word cannot be written normally.
[page]
After writing, you need to reset the FLASH ROM to read mode so that you can see the correct results in the development environment CCS. The maximum read speed of TE28F400B3 is 90ns, while TMS320VC5409 can only set up to 7 wait states. Therefore, set the CLKMD1, CLKMD2, and CLKMD3 pins of the DSP so that the system clock of the DSP is 50MHz when it is powered on and reset. This ensures that the FLASH data can be read reliably. After completing the boot process, you must first clear the CLKMD register and then reset the CLKMD register so that the system clock is 100MHz. The main operation commands of TE28F400B3 are shown in Table 2.
4 Experimental system
The vibration test system of the shock-absorbing spring is shown in Figure 3. The platform uses the suspension system and shock-absorbing spring of a real Santana 2000. The rotation of the motor is controlled by the inverter, and the wheel is driven to rotate through the transmission shaft. The lower end of the wheel contacts a rotatable iron rod with a protruding bar on the surface mounted on a fixed bracket. When the wheel rotates, it collides with the bar, and the suspension system causes the shock-absorbing spring to vibrate accordingly.
Two good springs and three bad springs were used for the experiment. The experimental results show that the automobile shock absorber spring fault diagnosis instrument works stably and the diagnosis results are effective.
The automobile shock absorber spring fault diagnosis instrument designed in this paper can be directly used for automobile shock absorber spring fault diagnosis, and can be extended to the diagnosis of nonlinear mechanical faults such as bearing wear and brake failure. On the basis of this fault diagnosis instrument, by slightly modifying the circuit, it can be used for fault diagnosis of higher frequency signal systems.
Previous article:Lear: Direct TPMS is the only choice for active safety
Next article:Perfect? DSG and S-Tronic gearbox analysis
Recommended ReadingLatest update time:2024-11-16 19:32
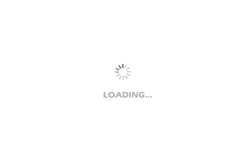
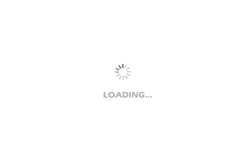
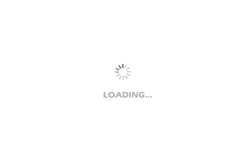
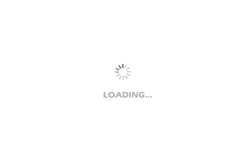
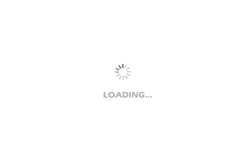
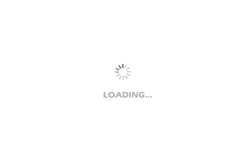
- Popular Resources
- Popular amplifiers
- Car key in the left hand, liveness detection radar in the right hand, UWB is imperative for cars!
- After a decade of rapid development, domestic CIS has entered the market
- Aegis Dagger Battery + Thor EM-i Super Hybrid, Geely New Energy has thrown out two "king bombs"
- A brief discussion on functional safety - fault, error, and failure
- In the smart car 2.0 cycle, these core industry chains are facing major opportunities!
- The United States and Japan are developing new batteries. CATL faces challenges? How should China's new energy battery industry respond?
- Murata launches high-precision 6-axis inertial sensor for automobiles
- Ford patents pre-charge alarm to help save costs and respond to emergencies
- New real-time microcontroller system from Texas Instruments enables smarter processing in automotive and industrial applications
- Innolux's intelligent steer-by-wire solution makes cars smarter and safer
- 8051 MCU - Parity Check
- How to efficiently balance the sensitivity of tactile sensing interfaces
- What should I do if the servo motor shakes? What causes the servo motor to shake quickly?
- 【Brushless Motor】Analysis of three-phase BLDC motor and sharing of two popular development boards
- Midea Industrial Technology's subsidiaries Clou Electronics and Hekang New Energy jointly appeared at the Munich Battery Energy Storage Exhibition and Solar Energy Exhibition
- Guoxin Sichen | Application of ferroelectric memory PB85RS2MC in power battery management, with a capacity of 2M
- Analysis of common faults of frequency converter
- In a head-on competition with Qualcomm, what kind of cockpit products has Intel come up with?
- Dalian Rongke's all-vanadium liquid flow battery energy storage equipment industrialization project has entered the sprint stage before production
- Allegro MicroSystems Introduces Advanced Magnetic and Inductive Position Sensing Solutions at Electronica 2024
- Car key in the left hand, liveness detection radar in the right hand, UWB is imperative for cars!
- After a decade of rapid development, domestic CIS has entered the market
- Aegis Dagger Battery + Thor EM-i Super Hybrid, Geely New Energy has thrown out two "king bombs"
- A brief discussion on functional safety - fault, error, and failure
- In the smart car 2.0 cycle, these core industry chains are facing major opportunities!
- The United States and Japan are developing new batteries. CATL faces challenges? How should China's new energy battery industry respond?
- Murata launches high-precision 6-axis inertial sensor for automobiles
- Ford patents pre-charge alarm to help save costs and respond to emergencies
- New real-time microcontroller system from Texas Instruments enables smarter processing in automotive and industrial applications
- Highly integrated analog front-end signal conditioning circuit diagram
- [TI star product limited time purchase] + familiar with participating in the event, the old man bought another CC2640R2
- Applications of Embedded AI
- Large capacitors filter low frequencies, and small capacitors filter high frequencies?
- 【Old Posts】Record Total Posts
- The evolution of mesh networks and IoT devices
- 12VDC power port surge protection tube BV-SMDJ13A
- Question about the number of concurrent services provided by base stations
- Power chip burnt out
- A brief talk on overtime