Vehicle systems generate and consume large amounts of data, raising concerns about data integrity and security.
The growth of plug-in hybrid and electric vehicles, as well as the increasingly complex development of advanced driver assistance systems (ADAS) and autonomous driving systems, are changing industry standards for electrical and electronic connectors. Power transmission is only one aspect of connectivity, but as vehicle systems generate and consume large amounts of data, there are also concerns about data integrity and security, as well as the ever-present challenge of electromagnetic compatibility. In this rapidly changing scenario, what industry standards do designers need to keep in mind?
The automotive industry is undergoing a dramatic transformation
The automotive industry is constantly changing, and this has become especially prevalent during this decade. As technological change occurs in one area, the resulting evolution is that technology can spur change in several other areas.
Moving towards semi-autonomous or fully autonomous vehicles. Autonomous vehicles require a large number of sensors around their bodies to navigate safely. Modern vehicles already have a variety of ADAS features, such as adaptive cruise control, emergency braking, and blind spot detection. With these increasing features, the ability to integrate and interpret sensor data becomes possible, enabling basic autonomy. Sensors located around the vehicle need to be networked, and timely innovations in Single Pair Ethernet (SPE) protocols, such as multi-point 10Base-T1S and long-distance 10Base-T1L, make this possible.
Another important industry trend is electrification. The growing demand for electric vehicles (EVs) is driving a shift in the way automotive engineers develop. For example, the considerable weight of EV batteries and the increase in wiring around the vehicle require automotive engineers to consider a new approach to vehicle electrical/electronic (E/E) architecture to reduce weight, reduce costs, and simplify implementation. Most automakers have adopted a zone architecture, which greatly reduces the number of cables reaching specific locations. For example, the driver's door zone only requires power and network connectivity, and the zone controller manages communication with the door mirrors, blind spot sensors, locks, window motors, and turn indicators.
The basis of any electrical and electronic installation are the cables and connectors that connect electronic control units and computers to sensors, actuators and motors.
Reliability of connections in the automotive sector
The automotive environment places demands on all required components. Devices, cables, and connectors are subject to extreme temperatures, humidity, and dust. Since each component is critical not only to the performance of the vehicle, but also to its safety, it is vital to maintain reliable and robust connections. Sensors that measure everything from cabin temperature to wheel traction effects need to be fit for purpose.
When selecting connectors for automotive applications, engineering teams should consider several factors.
Environmental:
Whether inside or outside the vehicle, the environment is challenging for cabling and connectors, with extremes in every factor from temperature and humidity to vibration and shock. Oscillating motion can fatigue cables and associated connector joints, so special attention needs to be paid to connector placement, installation, and construction. For some applications, connectors may be frequently immersed in water, so sealing is critical.
application:
The application will determine the type of cabling and connectors specified, ranging from unshielded twisted pair data cables and coaxial antenna feeds to high current, high voltage power connectors used in electric vehicles. Exposure to environmental conditions should also be reviewed.
mechanical:
The mechanical strength and ruggedness of the connector is critical. Protection from environmental factors and application requirements will guide connector specifications, such as the use of locking rings or latches, ingress protection, quality of the connected cable, and bulkhead or in-line retention. Other mechanical considerations include insertion force and retention force.
electric:
The electrical parameters of the connector include voltage, current, EMI shielding and isolation voltage. Increasingly, hybrid connectors may contain small signal sensor outputs, high-speed data networks and regional 12V/24V power rails. E/E engineering teams must consider multiple factors when taking this approach.
Assembly and production:
Consideration should also be given to how the connector will be assembled. Can a standard off-the-shelf connector be used to meet the requirements, or will a custom part be required? Will it be installed during the production process on a wire loom? All of these factors will impact connection selection, labor, and material costs.
Regulations and Standards:
Some automotive applications, such as electric vehicle charging, require specific connectors. Engineering teams should check with the relevant automotive standards bodies to determine if a defined specification exists for a specific use case.
Popular off-the-shelf connector formats have evolved and are available from a variety of suppliers. Examples include 2-pin to 32-pin rectangular low-voltage (LV) connectors for everything from single-pair Ethernet to hybrid power and signal connectors to support regional architectures.
Standards organizations involved in the automotive industry
In addition to the evolution of the above factors, several standards organizations have published automotive connector specifications that can help designers select appropriate components.
The Society of Automotive Engineers (SAE)
is a global association of more than 128,000 engineers and related technical experts in the aerospace, automotive and commercial vehicle industries. It has a formal, well-established standards-setting process that covers all aspects of vehicle systems, materials and methods.
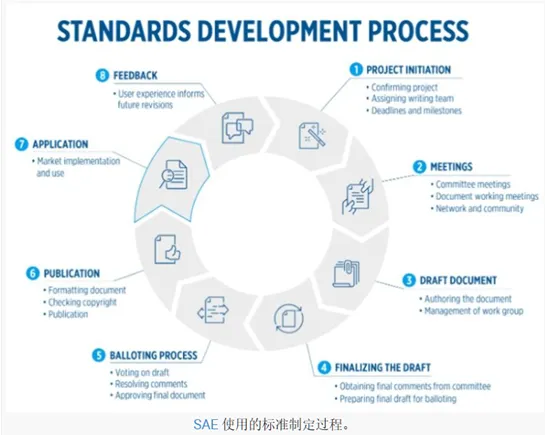
The United States Council for Automotive Research (USCAR)
works with member organizations and SAE to define and publish automotive standards. For example, its EWCAP specification specifies a series of formal performance test methods for electrical connections. In Europe, the LV214 standard is roughly consistent with USCAR's standards.
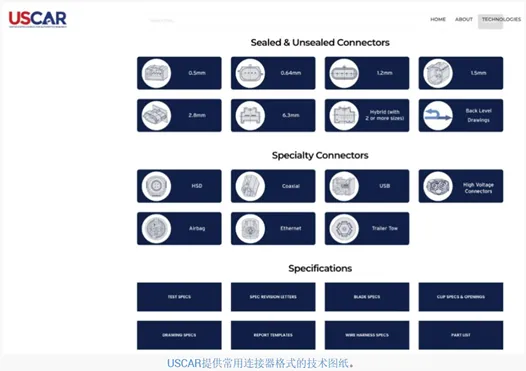
The International Electrotechnical Commission (IEC)
provides standards covering all functions of electrical and electronic equipment.
Examples of automotive connector standards
IEC 62196: This standard applies to plugs and sockets for AC or DC conductive charging of electric vehicles. It has several parts, including -1, which specifies general connector requirements; -3, dimensions and interchangeability specifications for DC and AC connectors; and -3-1, thermal management effects and precautions for DC charging connectors. Parts of this standard are also consistent with the single-phase connectors of SAE J1772 and the three-phase connections of SAE J3068.
USCAR12-6: This standard provides specific and measurable design requirements that manufacturers must follow when designing automotive electrical connectors. The performance standards for related connections specified in USCAR2 must also be followed.
USCAR2: Compliance with USCAR2 is an essential component of any automotive connector. The specification provides manufacturers with a measurable performance standard that covers all types of coaxial cables from low voltage (defined as 0 to 20VDC) to RF applications. It does not include any connector carrying more than 20VDC, board-level connections, or eyelet terminals.
SAE J1742: This standard outlines the test methods and performance requirements for connectors used in high-voltage on-board electrical harnesses. It covers full development and production testing for vehicle systems with any current level from 20VDC to 600 VDC or any vehicle system carrying more than 80A, regardless of voltage. In mixed connector arrangements, for example, high-voltage batteries and data from battery management system sensors, other connections must comply with the SAE J2223-2 standard.
Connector standards continue to evolve
Major trends in the automotive industry, such as the move to 800VDC infrastructure, regional wiring architectures, and the removal of traditional 12V batteries, all have an impact on current electrical standards. Working with automakers and equipment suppliers, standards organizations ensure that connector standards keep pace with these advances.
Previous article:Network controller based on S32G2 processor creates innovative car connectivity for SDV!
Next article:USCAR Connector Product Overview
- Popular Resources
- Popular amplifiers
- A new chapter in Great Wall Motors R&D: solid-state battery technology leads the future
- Naxin Micro provides full-scenario GaN driver IC solutions
- Interpreting Huawei’s new solid-state battery patent, will it challenge CATL in 2030?
- Are pure electric/plug-in hybrid vehicles going crazy? A Chinese company has launched the world's first -40℃ dischargeable hybrid battery that is not afraid of cold
- How much do you know about intelligent driving domain control: low-end and mid-end models are accelerating their introduction, with integrated driving and parking solutions accounting for the majority
- Foresight Launches Six Advanced Stereo Sensor Suite to Revolutionize Industrial and Automotive 3D Perception
- OPTIMA launches new ORANGETOP QH6 lithium battery to adapt to extreme temperature conditions
- Allegro MicroSystems Introduces Advanced Magnetic and Inductive Position Sensing Solutions
- TDK launches second generation 6-axis IMU for automotive safety applications
- LED chemical incompatibility test to see which chemicals LEDs can be used with
- Application of ARM9 hardware coprocessor on WinCE embedded motherboard
- What are the key points for selecting rotor flowmeter?
- LM317 high power charger circuit
- A brief analysis of Embest's application and development of embedded medical devices
- Single-phase RC protection circuit
- stm32 PVD programmable voltage monitor
- Introduction and measurement of edge trigger and level trigger of 51 single chip microcomputer
- Improved design of Linux system software shell protection technology
- What to do if the ABB robot protection device stops
- Brief Analysis of Automotive Ethernet Test Content and Test Methods
- How haptic technology can enhance driving safety
- Let’s talk about the “Three Musketeers” of radar in autonomous driving
- Why software-defined vehicles transform cars from tools into living spaces
- How Lucid is overtaking Tesla with smaller motors
- Wi-Fi 8 specification is on the way: 2.4/5/6GHz triple-band operation
- Wi-Fi 8 specification is on the way: 2.4/5/6GHz triple-band operation
- Vietnam's chip packaging and testing business is growing, and supply-side fragmentation is splitting the market
- Vietnam's chip packaging and testing business is growing, and supply-side fragmentation is splitting the market
- Three steps to govern hybrid multicloud environments
- The mobile station adds a new board, the STM32F723 Discovery Kit
- [Teardown of the car wireless charger] - Disassembling the Deli wireless car charger
- TTP250-S001 dimming solution and capacitive touch switch chip
- [Fudan Micro FM33LG0 Series Development Board Review] A Preliminary Study on the Rubik's Cube Development Environment
- BOOST Circuit Simulation
- Bluetooth (cc2540) protocol stack learning 1
- XMC4800 Review (Part 4) - Data Sharing
- 【DIY Creative LED】WS2812 Effect Display File
- One watt of GaN is less than one yuan, and it is free shipping by SF Express? Lenovo has launched a price war on GaN.
- B-U585I-IOT02A uses WIFI function