introduction
With the emergence of various sensors and the rapid development of chip technology, the safety and intelligence of automobiles are increasing day by day. The functions of automobile electronic control units (ECUs) and the information interaction between ECUs are increasing day by day. Automobile manufacturers have developed a variety of bus technologies to provide reliable and low-cost connections, implement corresponding network structures according to different requirements of safety and intelligence, and meet the different requirements of data exchange between units. For the control of the door area, there are many functions to be realized, including window lifting, rearview mirror position adjustment, door lock switch , switch quantity detection, etc. For different target customer groups, there are also many optional intelligences, including window anti-pinch, rearview mirror folding and heating, etc. The author uses low-speed CAN bus and LIN bus to realize the door distributed control system, selectively realizes part of the intelligence, and the system can be quickly modified and upgraded without too much design changes. This article describes the determination of the system structure and the specific implementation of distributed control.
Determination of system structure
The door control system adopts a bus topology structure. The bus generally adopts a low-speed CAN bus or LIN bus. Different bus protocols and different topologies can provide different levels of intelligence. The first solution is to use a centrally controlled CAN node for each door. The BSI and four doors are connected through a CAN network, as shown in Figure 1.
Figure 1 Centralized door control solution
The second solution is to use a distributed LIN network structure for each door, and make each function into a separate node, that is, a separate rearview mirror control node, a window control node, a door lock control node, and a switch input control node. The switch input control node can also be used as the master node of LIN. The master node of each door is also a CAN-LIN gateway node. The BSI and the four doors are connected through the CAN network. As shown in Figure 2.
Figure 2 Distributed door control solution
Solution 1 is a typical solution currently adopted by a large number of manufacturers. This centralized control method integrates window lifting and anti-pinch, rearview mirror position adjustment, door locks, and switch input detection in one ECU. It has low cost, uses a low-speed CAN bus connection, has a simple topology structure, simple and real-time communication, and relatively simple protocol formulation. CAN uses a multi-master dual-line fault-tolerant mechanism, so it has high security. CAN bus-based diagnosis also makes fault finding and repair more convenient.
With the development of technology and consumers' pursuit of automobile intelligence, the improvement of automobile intelligence and rapid upgrading are key factors to ensure the competitiveness of automobile manufacturers. The shortcomings of using a single CAN bus for centralized control have also begun to be exposed. Since the high-performance MCU in the door node directly controls the windows and mirrors, when the ECU's intelligence requirements are getting higher and higher and it is necessary to increase functions or intelligence, the MCU functions of each centralized control node can only be enhanced, resulting in an increase in MCU specifications; centralized control is also complex to install, with many connectors and cables. When intelligence increases, the number of interconnections increases, lacking flexibility, and product upgrades require a lot of costs, which ultimately leads to reduced efficiency [2].
Hierarchical networks are an effective solution to the rapid and low-cost upgrade of automotive products. As an effective supplement to the CAN bus, the LIN bus is a key factor in the feature upgrade and function enhancement of hierarchical automotive networks [3]. The CAN-LIN hierarchical network structure shown in Scheme 2 fully utilizes the respective advantages of the CAN/LIN bus, transplants some functions to smaller and more reliable nodes, reduces the complexity of each ECU, and the LIN nodes in the four doors can be universal, with better interchangeability and compatibility. A node can be added or removed at any time according to the configuration requirements of the door function without any impact on the entire network, so it can be quickly upgraded without incurring greater cost consumption.
The emergence of single-chip sensors and actuators provides a low-cost solution for distributed nodes, making it possible to adopt distributed technology to reduce costs. As LIN bus technology continues to mature, by making appropriate choices for MCU and LIN state machine, a more powerful and flexible distributed system can be obtained.
Implementation of Distributed Control
In the distributed control implementation of the door system, each door is a LIN network. The front door includes the window node, rearview mirror node and door lock node, while the rear door does not include the rearview mirror node. The following discusses the implementation of the door distributed control system from two aspects: the implementation of distributed nodes and the implementation of gateways.
Rearview mirror node
The rearview mirror node solution is shown in the figure below. It can adjust the position of the rearview mirror in the up and down, front and back directions, and realize the folding and heating functions. It is implemented using Freescale's intelligent distributed control single chip MM908E625. MM908E625 is a highly integrated single-package solution that integrates the HC08 core and SmartMOS analog control IC in a SOIC54 package. The analog control IC includes a LIN physical layer transceiver , a voltage regulator, 4 half-H bridges and a high-end switch. The half-H bridge is used to drive the rearview mirror motor to achieve position adjustment and folding, and the high-end switch is used to achieve rearview mirror heating.
Figure 3 Rearview mirror node solution
Window Node
The window node solution is shown in the figure below. To achieve window lifting and anti-pinch, an intelligent power driver chip with current feedback is used, and a small algorithm based on current feedback is designed to achieve the anti-pinch function. When the window motor is started, it can run smoothly after hundreds of milliseconds. After this startup time, the current feedback value of the driver chip is sampled, and the ADC sampling in the MCU on the window ECU is compared with the threshold. If an obstacle is encountered, the operating current of the window motor increases, and the ADC sampling value exceeds the set threshold. At this time, it is considered that an obstacle has been encountered, and the MCU controls the driver chip to stop driving the window motor, thereby achieving anti-pinch.
Figure 4 Window node solution
Gateway
The master node of each door LIN network completes the switch status detection of the door area, controls all communications on the LIN network, designs a reasonable schedule to control the transmission of each information frame, and effectively controls the maximum transmission delay of key signals. This node is also a CAN-LIN gateway node, completing data buffering and information exchange between the CAN network and the LIN network.
Conclusion
This paper comprehensively considers the advantages and disadvantages of different system structures and the requirements of intelligentization and upgrading of automotive products, and designs and implements a door distributed control system based on CAN/LIN bus. The system runs well and has certain practical value.
Previous article:Design of intelligent node for fuel cell vehicle air conditioning based on MCU, CAN controller and transceiver
Next article:Spireon Launches Trailer Image Capture and Retrieval to Reduce Cargo Damage and Improve Operational Efficiency
Recommended ReadingLatest update time:2024-11-15 10:22
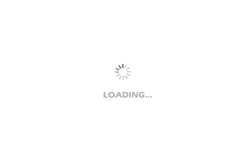
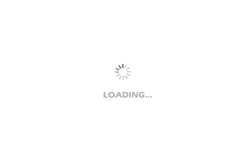
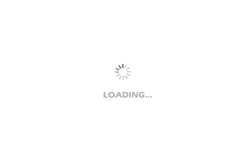
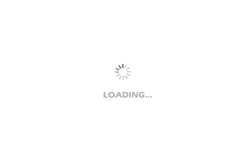
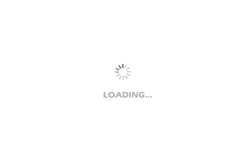
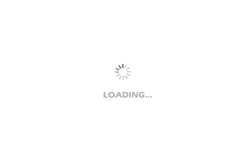
- Popular Resources
- Popular amplifiers
-
New Energy Vehicle Control System Inspection and Maintenance (Edited by Bao Pili)
-
Detailed explanation of big data technology system: principles, architecture and practice (Dong Xicheng)
-
Automotive CAN embedded intrusion detection system based on deep learning
-
Lightweight FPGA-based IDS-ECU architecture for automotive CAN networks
- A new chapter in Great Wall Motors R&D: solid-state battery technology leads the future
- Naxin Micro provides full-scenario GaN driver IC solutions
- Interpreting Huawei’s new solid-state battery patent, will it challenge CATL in 2030?
- Are pure electric/plug-in hybrid vehicles going crazy? A Chinese company has launched the world's first -40℃ dischargeable hybrid battery that is not afraid of cold
- How much do you know about intelligent driving domain control: low-end and mid-end models are accelerating their introduction, with integrated driving and parking solutions accounting for the majority
- Foresight Launches Six Advanced Stereo Sensor Suite to Revolutionize Industrial and Automotive 3D Perception
- OPTIMA launches new ORANGETOP QH6 lithium battery to adapt to extreme temperature conditions
- Allegro MicroSystems Introduces Advanced Magnetic and Inductive Position Sensing Solutions
- TDK launches second generation 6-axis IMU for automotive safety applications
- LED chemical incompatibility test to see which chemicals LEDs can be used with
- Application of ARM9 hardware coprocessor on WinCE embedded motherboard
- What are the key points for selecting rotor flowmeter?
- LM317 high power charger circuit
- A brief analysis of Embest's application and development of embedded medical devices
- Single-phase RC protection circuit
- stm32 PVD programmable voltage monitor
- Introduction and measurement of edge trigger and level trigger of 51 single chip microcomputer
- Improved design of Linux system software shell protection technology
- What to do if the ABB robot protection device stops
- Detailed explanation of intelligent car body perception system
- How to solve the problem that the servo drive is not enabled
- Why does the servo drive not power on?
- What point should I connect to when the servo is turned on?
- How to turn on the internal enable of Panasonic servo drive?
- What is the rigidity setting of Panasonic servo drive?
- How to change the inertia ratio of Panasonic servo drive
- What is the inertia ratio of the servo motor?
- Is it better for the motor to have a large or small moment of inertia?
- What is the difference between low inertia and high inertia of servo motors?
- The Academic Degrees Committee of the State Council voted to approve the proposal to "establish integrated circuit as a first-level discipline"!
- esp32-s2-wrover cannot start after upgrading micropython 1.18
- Today is International Day Against Spatting. Were you ever spanked as a child?
- B&O Beoplay E8 TWS True Wireless Bluetooth Earphones
- Flyback switching power supply simulation using Saber
- Our company makes FOC motor drivers. The algorithm is mature. We want to find a chip manufacturer to cooperate with us to make a motor-specific chip.
- How to build a simple and efficient isolated power supply below 2W
- Six common circuit board surface treatment processes
- [N32L43X Review] 1. Getting Started Environment Configuration
- Tektronix THz Radar Signal Test Solution