Great Wall Motors has finally revealed its ambition to enter the L3 autonomous driving field and has clearly stood on the side of lidar.
In the strategic cooperation signed with Liangdao Intelligent and Ibeo on the mass production of L3/L4 autonomous driving, Great Wall Motors launched the next-generation VV7 model of the WEY brand. LiDAR supplier Ibeo provided the industry's first 4D pure solid-state LiDAR, while Liangdao Intelligent was responsible for the testing and verification services of this new LiDAR sensor in Great Wall's L3 project.
The foundation of the tripartite cooperation may be the common understanding of the LiDAR route: from the perspective of the safety redundancy required for L3 projects, LiDAR is a must. In the advanced assisted driving stage, cameras are often regarded as the mainstream overall perception solution, while LiDAR, with its high-precision and high-reliability detection capabilities, can play a role as a core sensor with stronger perception capabilities in high-level autonomous driving.
The problem is that according to Zhen Longbao, head of autonomous driving at Great Wall Motors, and Ju Xueming, CEO of Liangdao Intelligent, the various types of sensors currently on the market are still not good enough in terms of perception performance. They put forward several requirements for the selection of an ideal LiDAR:
Longer detection distance, wider detection viewing angle, higher resolution, better integration, lower cost, longer service life, greater product design flexibility and the ability to pass automotive-grade verification.
Therefore, in order to meet Great Wall's requirements for functional safety, Ibeo specially developed a new 4D pure solid-state laser radar. The so-called 4D means that in addition to the basic three-dimensional information (X, Y, Z), energy information is added. Flash uses the receiver to identify the energy and distinguish the strength of the energy. Cheyunjun learned that the product has a maximum detection distance of 300 meters, and the horizontal field of view can be adjusted according to the user's usage scenario, with a maximum angular resolution of 0.05 degrees.
In view of the differences between L3 and L4 autonomous driving scenarios, there is no sensor on the market that can be applied to all scenarios at this stage. Therefore, while keeping the cost unchanged, the adjustment of parameter performance has a strong driving significance for the overall autonomous driving, enabling it to cover L2-L5 autonomous driving applications.
In principle, this product is similar to the Flash solution, and there are no moving parts in it, which lays a good foundation for its service life and product reliability. Currently, many solid-state solutions promoted by LiDAR on the market still use Mems galvanometers.
The most important thing is that it plans to complete mass production of automotive specifications in 2021. At present, the only LiDAR product on the market that truly achieves this goal is Valeo's SCALA.
During the SOP process, Liangdao Intelligence proposed to automatically evaluate the capabilities of various perception modules and then output KPIs. At the same time, the "threshold" between L2 and L3 is the transfer of driving responsibilities, and the workload of testing and verification is also facing an increase of several orders of magnitude. In order to meet the requirements of L3 and L4 autonomous driving, the output of various KPIs using the previous manual labeling method obviously cannot meet the normal cycle of automotive product development.
Liangdao Intelligence specifically plans to provide a complete tool chain for automated KPI output to support mass production projects. Ju Xueming revealed that for HWP (high-speed scenarios), under normal driving conditions, the automation rate of its 1.0 version of the truth value establishment system has reached about 98%, and other information targets can be automatically and correctly labeled during vehicle driving.
In other words, only after having a clear understanding of the perception capabilities of their own products can they accelerate the iteration of perception research and development. As for all the technical details between the three parties from technology research and development to final implementation, Cheyunjun also has a more comprehensive understanding:
Q: How many IbeoNEXTs will be included in the sensor system that Great Wall is collaborating on?
Zhen Longbao: There are two in the current technical solutions.
Q: Will pure solid-state LiDAR change the traditional installation location in the future?
Ju Xueming: The installation method is similar to that of SCALA. At the height of the vehicle bumper, it will have a better integration with the vehicle body.
It still depends on how the autonomous driving plan is finally formulated. For example, our current plan is to mainly demonstrate its capabilities forward. Of course, if there are driverless buses in the future and there are requirements for 360-degree environmental recognition, the FOV of the solid-state sensor I just mentioned is adjustable. It can be adjusted to a large field of view, such as 120 degrees, and then installed in different positions of the car, such as on the side and the back. This can be configured relatively flexibly according to the autonomous driving plan.
We are also considering integrating LiDAR into headlights with a German OEM, but this is very technically challenging because it involves heat dissipation in headlights, and the recognition distance will be attenuated if there is light in front. If it can be put into headlights or made into laser headlights, this will also be a major breakthrough in autonomous driving, but I think the technology is very difficult. We have been looking at this direction for a long time. Especially for some sports cars, like classic sports cars, you cannot change its appearance.
So to sum up, the ibeoNEXT solid-state lidar has very high upper limits and meets the requirements of L3 and L4, so I think it is possible that Ibeo's lidar will become a standard module in the future.
Q: What stage is the mass production of this solid-state lidar currently at?
Ju Xueming: We are still at the A1 sample stage. The mass production will be close to 2021. Our SOP will be completed before the mass production of Great Wall L3 models.
If ibeoNEXT is to be mass-produced, Great Wall will be the first domestic OEM, and other OEMs cannot get mass-production orders for the time being.
Q: How to ensure the safety redundancy of L3 autonomous driving systems?
Zhen Longbao: Great Wall vehicles are equipped with laser radar, millimeter-wave radar, and visual sensors at the same time, and different sensors are connected to different controllers. In order to ensure safety, two controllers will also be set up. The laser radar and even part of the visual sensor will be connected to one of the controllers, and the millimeter-wave radar plus part of the visual sensor will be connected to the other controller, so as to ensure that any sensor or any controller is broken, it can still have basic functions. In addition to the vehicle execution platform itself, we have guaranteed the minimum safety level purely from the perspective of the autonomous driving system. If you want to achieve true L3, you must do this.
Q: What stage has the vehicle architecture design reached now?
Zhen Longbao: The model design and development plan for mass production in 2021 have been finalized. Because time needs to be set aside for sufficient verification and development, the entire system development has now entered the embedded development stage. What we mean by embedded is to put it into a small ECU to run.
Q: What are Great Wall’s specific plans for L3 and L4 autonomous driving?
Zhen Longbao: We are doing it simultaneously. L3 is planned to be mass-produced in 2021, and L4 is to be operated in some demonstration areas in 2021. We already have a small DEMO. L3 is for C, and L4 is for B, in mini buses, including some low-speed logistics vehicles, etc. This tripartite cooperation is also very likely to expand to the L4 level.
Q: There is quite a lot of buzz about MEMS lidar in China. From the perspective of the OEM, how did we choose Ibeo?
Zhen Longbao: Several years ago, we had already started cooperation in the field of LiDAR, which involved mechanical LiDAR and Ibeo's LUX four-line LiDAR. After testing, we found that the stability of LUX output, including the reliability of the target, was relatively high.
MEMS is indeed a hot topic in the current laser radar industry, but it is also a semi-solid route, relatively speaking, not a complete solid state. Especially for products such as laser radar that require high precision, there is no reliable data on whether it can fully meet the automotive grade verification, and the detection angle of general MEMS is relatively small.
Ju Xueming: There were several schools of thought on solid-state LiDARs, each with its own drawbacks. From our perspective, as long as it can meet OEM requirements, it is a good LiDAR. After Ibeo's product came out, we conducted a comprehensive evaluation and found that it had no obvious shortcomings. The technology itself is relatively mature, and considering the final landing cost, I think there are still great expectations.
Q: During testing and verification, how do we judge two lidars with different working modes?
Ju Xueming: I personally think that some of the laser radars currently on the market are not good enough, whether it is L2 or L3. I think there are still problems with the traditional 64-line laser radar in terms of cost, service life, and installation method. Robo Taxi may be able to accept it, but it is difficult for OEMs targeting mass production to accept this installation method.
If we compare emerging sensors horizontally, first of all, in terms of performance, the resolution of Ibeo's pure solid-state lidar can reach 0.05 degrees. Because in order to develop high-speed autonomous driving, it is necessary to detect a small obstacle of 10 centimeters at a distance of 100 meters or even 100 meters, but the sensors on the market, especially lidar, cannot do this.
Previous article:Tesla may launch battery products with a lifespan of 1.6 million kilometers in 2020
Next article:Alternative test and verification route for automotive-grade LiDAR
Recommended ReadingLatest update time:2024-11-16 14:51
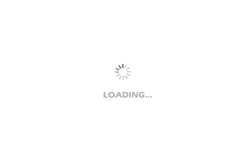
- Popular Resources
- Popular amplifiers
-
A review of deep learning applications in traffic safety analysis
-
Dual Radar: A Dual 4D Radar Multimodal Dataset for Autonomous Driving
-
A review of learning-based camera and lidar simulation methods for autonomous driving systems
-
Multimodal perception parameterized decision making for autonomous driving
- Car key in the left hand, liveness detection radar in the right hand, UWB is imperative for cars!
- After a decade of rapid development, domestic CIS has entered the market
- Aegis Dagger Battery + Thor EM-i Super Hybrid, Geely New Energy has thrown out two "king bombs"
- A brief discussion on functional safety - fault, error, and failure
- In the smart car 2.0 cycle, these core industry chains are facing major opportunities!
- The United States and Japan are developing new batteries. CATL faces challenges? How should China's new energy battery industry respond?
- Murata launches high-precision 6-axis inertial sensor for automobiles
- Ford patents pre-charge alarm to help save costs and respond to emergencies
- New real-time microcontroller system from Texas Instruments enables smarter processing in automotive and industrial applications
- Innolux's intelligent steer-by-wire solution makes cars smarter and safer
- 8051 MCU - Parity Check
- How to efficiently balance the sensitivity of tactile sensing interfaces
- What should I do if the servo motor shakes? What causes the servo motor to shake quickly?
- 【Brushless Motor】Analysis of three-phase BLDC motor and sharing of two popular development boards
- Midea Industrial Technology's subsidiaries Clou Electronics and Hekang New Energy jointly appeared at the Munich Battery Energy Storage Exhibition and Solar Energy Exhibition
- Guoxin Sichen | Application of ferroelectric memory PB85RS2MC in power battery management, with a capacity of 2M
- Analysis of common faults of frequency converter
- In a head-on competition with Qualcomm, what kind of cockpit products has Intel come up with?
- Dalian Rongke's all-vanadium liquid flow battery energy storage equipment industrialization project has entered the sprint stage before production
- Allegro MicroSystems Introduces Advanced Magnetic and Inductive Position Sensing Solutions at Electronica 2024
- Car key in the left hand, liveness detection radar in the right hand, UWB is imperative for cars!
- After a decade of rapid development, domestic CIS has entered the market
- Aegis Dagger Battery + Thor EM-i Super Hybrid, Geely New Energy has thrown out two "king bombs"
- A brief discussion on functional safety - fault, error, and failure
- In the smart car 2.0 cycle, these core industry chains are facing major opportunities!
- The United States and Japan are developing new batteries. CATL faces challenges? How should China's new energy battery industry respond?
- Murata launches high-precision 6-axis inertial sensor for automobiles
- Ford patents pre-charge alarm to help save costs and respond to emergencies
- New real-time microcontroller system from Texas Instruments enables smarter processing in automotive and industrial applications
- CAN communication
- "Constant power" power control strategy for hard-start loads (such as high-power permanent magnet brushed motors and solenoid valves)
- Please help me explain the principle of this filter circuit and the calculation of inductance and capacitance parameters.
- Happy New Year to everyone! I wish you all a happy new year!
- Countdown! The 15th Automechanika Shanghai is coming soon
- How does the Zigbee coordinator select the appropriate channel to create a network?
- How can I learn FPGA quickly?
- Why is Huawei's 5G technology stronger than that of the United States?
- msp430f5137+adxl362 accelerometer, can read ID but cannot read acceleration data!
- Microchip Live: MPLAB breaks the "This microcontroller programming is too difficult, I can't do it" and calls you to develop quickly