summary
本文研究具有背靠背MOSFET的理想二极管以及其他更先进的器件。文中还介绍了一种集成多种功能以提供整体系统保护的理想二极管解决方案。二极管是非常有用的器件,对许多应用都很重要。标准硅二极管的压降为0.6 V至0.7 V。肖特基二极管的压降为0.3 V。一般来说,压降不是问题,但在高电流应用中,各个压降会产生显著的功率损耗。理想二极管是此类应用的理想器件。幸运的是,MOSFET可以取代标准硅二极管,并提供意想不到的应用优势。
Introduction
An ideal diode uses a low on-resistance power switch (usually a MOSFET) to simulate the unidirectional current behavior of a diode, but without the voltage drop loss of a diode. With additional back-to-back MOSFETs and control circuitry, this solution can provide more system control functions, such as priority source selection, current limiting, inrush limiting, etc. In traditional solutions, these functions are scattered across different controllers, so achieving complete system protection can be complex and cumbersome. Here we will examine the key circuit specifications of an ideal diode and introduce an application example and a new ideal diode solution that also integrates the other functions required to achieve overall system protection in a single IC.
Figure 1 shows a basic ideal diode using an N-channel power MOSFET. The MOSFET is oriented so that its intrinsic body diode is in the same direction as the diode function to be simulated (above). When VA is higher than VC, current can naturally flow through the intrinsic diode from left to right. When current flows in this direction, the control circuit turns the MOSFET on to reduce the forward voltage drop. To prevent current from flowing in the reverse direction (right to left) when VC is higher than VA, the control circuit must quickly turn the MOSFET off. The voltage drop across an ideal diode is low and is determined by the RDS(ON) of the MOSFET and the current. For example, with a 1 A load, a 10 mΩ MOSFET will have a voltage drop of 1 A × 10 mΩ = 10 mV across its terminals, while a typical voltage drop across a conventional diode is 600 mV. The power dissipation of the ideal diode is 1 A2 × 10 mΩ = 10 mW, which is significantly lower than the 1 A × 600 mV = 600 mW (typical) of a conventional diode.
Figure 1. Diode and ideal diode
Thanks to the advancement of MOSFET technology, low RDS(ON) MOSFETs are now available. If back-to-back MOSFETs are added to the ideal diode solution, although the voltage drop will increase slightly, it will also bring many system control functions. Figure 2 shows this circuit concept.
Figure 2. Ideal diode with back-to-back MOSFETs
The original Q1 can control and block the reverse current flowing from VB to VA. The added MOSFET Q2 can control and block the forward current flowing from VA to VB.
This solution enables full system control by turning one or both MOSFETs on/off, or limiting current flow in either direction.
Ideal diode application examples and main specifications
Ideal diodes have many applications. Take an industrial UPS backup power system (Figure 3) as an example. The system uses a 24 V main power supply. This power supply operates in the range of 19.2 VDC to 30 VDC, and the transient voltage can be as high as 60 V. A 24 V battery is used as a backup power supply. To ensure that the backup power is fully available, the battery is fully charged to 24 V during normal operation (when the battery is in standby). When the main power is interrupted, the battery provides backup power, discharging from 24 V to below 19.2 V until the system is no longer operating or until the main power is restored, whichever occurs first. An ideal diode circuit is needed here to provide an ORing function for switching between the system power supply and the backup battery. In addition to the ORing function, the system also requires overvoltage, undervoltage, hot-swap, and eFuse protection to prevent common system failures and enhance system robustness.
Figure 3. Industrial UPS backup power system
ORing with source selector
Figure 4 illustrates the power supply ORing concept. For simplicity, a diode symbol is used here instead of an ideal diode circuit. In this simple ORing configuration, the power supply with the higher voltage is dominant and powers the load, and the other power supply is in standby. This solution works well if the two supplies have different voltage values. The supplies may switch back and forth when the two voltages are close to each other or when there is a voltage fluctuation that causes the voltage values to cross.
Figure 4. Input power ORing
In this use case, a simple ORing function is not enough for two reasons. First, the battery voltage is similar to the nominal system voltage of 24 V. The two sources may switch back and forth, which is undesirable. The effects of source impedance and load current further amplify this problem. For example, when VS is powering the load, the load current will produce a voltage drop across the VS source impedance, causing its terminal voltage to drop to a level slightly lower than the battery terminal voltage (currently unloaded). The battery is then switched on and now carries the load current, which also produces a voltage drop across the battery impedance, causing the battery terminal voltage to drop. At the same time, under no load conditions, the voltage at the main power supply terminal increases, causing VS to try to take over. In this case, oscillation between the two sources will continue until the two voltages diverge from each other.
Secondly, the 24 V system supply has a voltage range of 19.2 VDC (minimum) to 30 VDC (maximum) with peak voltage transients up to 60 V. The backup battery voltage is charged to 24 VDC and will be powered by the battery when the main supply voltage drops below the battery voltage but is still within its operating range. This is also undesirable because the battery will discharge to the non-ideal backup voltage. Whenever the system voltage is below 24 V and above its minimum operating range, the system may try to charge and discharge the battery at the same time. A source selector is useful in this situation. Figure 5 shows the source selector concept using an ideal diode with back-to-back MOSFETs. With back-to-back MOSFETs, the controller can completely cut off the current path in both directions, just like a mechanical switch is open. Figure 6 is a symbolic representation of an ideal diode with back-to-back MOSFETs. This symbol is shown in Figure 5 to implement the source selector function. In this configuration, VS is set to high priority. VB is off and only turns on when VS is below its operating voltage range.
Figure 5. Input source selector
Figure 6. Symbolic representation of an ideal diode with back-to-back MOSFETs
Figure 7 shows the power selector operation during battery standby and backup.
Figure 7. Input source selector operation
Other important system protection requirements
Although Figure 6 shows a closed or open mechanical switch, note that with the appropriate current sensing circuitry, the controller can also regulate current. Important functions such as inrush limiting (hot swap), overload/short circuit protection (eFuse), and undervoltage/overvoltage (UV/OV) can all be implemented using the same existing power MOSFETs.
Hot Swap
As shown in Figure 3, the system board requires hot-swap functionality to limit the inrush current when charging the input capacitor C when the board is plugged into the backplane (the board where the main system power supply and backup battery are located). This hot-swap functionality is implemented by sensing and controlling the current flowing through Q2 in Figure 2.
eFuse
This feature protects the system from overcurrent or short-circuit conditions. Using the same Q2 in Figure 2, the current through Q2 can be monitored, limited, and shut down. The accuracy of the current limit threshold in eFuse applications is very important to optimize the system power budget.
UV/OV
The controller continuously monitors the supply voltage. Undervoltage lockout (UVLO) keeps Q2 (Figure 2) safely off until the supply voltage rises above its minimum operating level (19.2 V in this example). Overvoltage lockout (OV) turns Q2 off when the input transient voltage exceeds the programmed maximum level (>30 V is chosen in this example).
Important ideal diode circuit specifications and their impact on system performance
Let’s go back to the ideal diode and look at some of its key specifications when used in an ORing or source selector function.
Reverse current response time
Referring to Figure 2, this is the time Q1 turns off after the voltages VA and VB reverse and make VB greater than VA. This reverse current response time tR must be small (100 ns) to prevent reverse current from flowing back from VB to VA. In this system, the voltage may reverse when the dominant power supply VS (when driving a load) turns off, transients to a lower voltage, or is shorted. In this case, tR prevents reverse current from flowing back to VS from the board capacitor C or from the backup battery, or minimizes the reverse current.
Recovery after an overvoltage condition
In systems without a backup battery (Figure 8), capacitor C provides backup power and is often referred to as a hold-up capacitor. In this configuration, a transient overvoltage condition on VS triggers Q2 (Figure 8) to turn off. The capacitor provides the necessary power to keep the system running while its voltage drops due to discharge. When VS returns to the normal operating range, Q2 turns back on. The time tON that Q2 turns back on must be short to keep the voltage drop across the capacitor as low as possible. Figure 9 shows a relative comparison, where half the tON reduces the voltage drop by half while holding the same capacitance.
Figure 8. System with hold capacitor
Figure 9. Voltage drop vs. tON
We have studied different functions such as source selector, hot-swap, eFuse, UV/OV, and key specifications to protect against common system failures and enhance system robustness. It would be cumbersome to use many single-function ICs to implement all these functions. Such solutions are complex and require many components. The MAX17614 is a new, highly integrated solution that provides comprehensive protection for power systems by implementing high-performance ideal diode functions and many other functions in a single IC. The device operates from 4.5 V to 60 V, provides 3 A output, and has ideal diode/priority source selector functions, as well as adjustable current limit, hot-swap, eFuse, UV, and OV protection functions. Figure 10 and Figure 11 show simplified schematics of the MAX17614 in ORing applications and priority source selector applications, respectively.
Previous article:Student Area—ADALM2000 Experiment: IC Temperature Sensor
Next article:Student Area - ADALM2000 Activity: Inductor Self-Resonance
Recommended ReadingLatest update time:2024-11-16 09:49
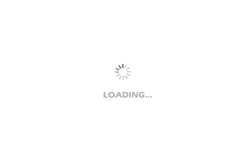
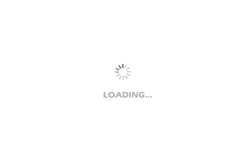
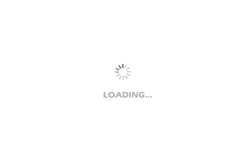
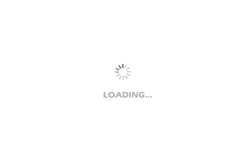
- Popular Resources
- Popular amplifiers
-
Modern Electronic Technology Training Course (Edited by Yao Youfeng)
-
Sensor Principle and Application Circuit Design (Edited by Chen Shuwang, Song Lijun, Xu Yunfeng)
-
Single-chip microcomputer C language programming and simulation
-
100 Examples of Microcontroller C Language Applications (with CD-ROM, 3rd Edition) (Wang Huiliang, Wang Dongfeng, Dong Guanqiang)
- High signal-to-noise ratio MEMS microphone drives artificial intelligence interaction
- Advantages of using a differential-to-single-ended RF amplifier in a transmit signal chain design
- ON Semiconductor CEO Appears at Munich Electronica Show and Launches Treo Platform
- ON Semiconductor Launches Industry-Leading Analog and Mixed-Signal Platform
- Analog Devices ADAQ7767-1 μModule DAQ Solution for Rapid Development of Precision Data Acquisition Systems Now Available at Mouser
- Domestic high-precision, high-speed ADC chips are on the rise
- Microcontrollers that combine Hi-Fi, intelligence and USB multi-channel features – ushering in a new era of digital audio
- Using capacitive PGA, Naxin Micro launches high-precision multi-channel 24/16-bit Δ-Σ ADC
- Fully Differential Amplifier Provides High Voltage, Low Noise Signals for Precision Data Acquisition Signal Chain
- Innolux's intelligent steer-by-wire solution makes cars smarter and safer
- 8051 MCU - Parity Check
- How to efficiently balance the sensitivity of tactile sensing interfaces
- What should I do if the servo motor shakes? What causes the servo motor to shake quickly?
- 【Brushless Motor】Analysis of three-phase BLDC motor and sharing of two popular development boards
- Midea Industrial Technology's subsidiaries Clou Electronics and Hekang New Energy jointly appeared at the Munich Battery Energy Storage Exhibition and Solar Energy Exhibition
- Guoxin Sichen | Application of ferroelectric memory PB85RS2MC in power battery management, with a capacity of 2M
- Analysis of common faults of frequency converter
- In a head-on competition with Qualcomm, what kind of cockpit products has Intel come up with?
- Dalian Rongke's all-vanadium liquid flow battery energy storage equipment industrialization project has entered the sprint stage before production
- Allegro MicroSystems Introduces Advanced Magnetic and Inductive Position Sensing Solutions at Electronica 2024
- Car key in the left hand, liveness detection radar in the right hand, UWB is imperative for cars!
- After a decade of rapid development, domestic CIS has entered the market
- Aegis Dagger Battery + Thor EM-i Super Hybrid, Geely New Energy has thrown out two "king bombs"
- A brief discussion on functional safety - fault, error, and failure
- In the smart car 2.0 cycle, these core industry chains are facing major opportunities!
- The United States and Japan are developing new batteries. CATL faces challenges? How should China's new energy battery industry respond?
- Murata launches high-precision 6-axis inertial sensor for automobiles
- Ford patents pre-charge alarm to help save costs and respond to emergencies
- New real-time microcontroller system from Texas Instruments enables smarter processing in automotive and industrial applications
- About the efficiency and memory usage of CCS9 floating point operations
- [Qinheng RISC-V core CH582] Bluetooth HID keyboard code interpretation
- Ask: Why SP485REN-L/TR is frequently damaged
- Why is 16MHZ not available for msp430?
- The live broadcast has ended [Microchip Embedded Security Solutions | Anti-counterfeiting protection for disposable products]
- Comparison of the advantages of three-resistance current sampling and single-resistance
- [TI recommended course] #Innovation of general-purpose op amp and comparator chips#
- An application example of a certain brand of high power density power module
- Will the DS1100 delay chip affect my analog signal?
- [Sipeed LicheeRV 86 Panel Review] 12. lvgl and pthread to implement TCP Client