Real-world circuit components are much more complex than ideal resistors and exhibit resistive, capacitive, and inductive properties that together determine the impedance characteristic. Impedance differs from resistance in two main ways. First, impedance is an alternating current (AC) characteristic, and second, impedance is usually defined at a specific frequency. If impedance is measured at different frequencies, different impedance values are obtained. Measuring impedance at multiple frequencies is the only way to obtain valuable component data. This is the basis for impedance spectroscopy (IS), a fundamental concept that underlies many industrial, instrumentation, and automotive sensor applications.
The impedance of an electronic component can be made up of resistance, capacitance or inductance, or more generally a combination of the three. Imaginary impedance can be used to model this. An inductor has an impedance of jωL and a capacitor has an impedance of 1/jωC, where j is the imaginary unit and ω is the angular frequency of the signal. Complex operations are used to combine these impedance components. The imaginary part of the impedance is called reactance, and the overall expression is Z=R+jX, where X is reactance and Z is impedance. When the frequency of the signal increases, the capacitive reactance Xc decreases, while the inductive reactance XL increases, causing a change in the total impedance as a function of frequency. The impedance of a pure resistor does not change with frequency. .
Figure 1: Nyquist plot for a resistor and capacitor in parallel.
How to Analyze Impedance
To detect the impedance of a component, it is usually necessary to measure the response signal in the time domain or frequency domain when the device is scanned at different frequencies. Measuring the frequency domain response signal generally uses analog signal analysis methods, such as an AC-coupled bridge, but using a high-performance analog-to-digital converter (ADC) allows data to be acquired in the time domain and then converted to the frequency domain.
Many integral transforms can be used to convert data to the frequency domain, such as Fourier analysis. This method takes a series of time domain signal representations of the signal and then applies an integral transform to map it into a frequency spectrum. This method can give a mathematical description of the relationship between any two signals. In impedance analysis, the relationship between the excitation current (the input of the component) and the voltage response (the output of the component) is of interest. If the system is linear, the ratio of the respective Fourier transforms of the measured time domain voltage and current is equal to its impedance, and it can be expressed as a complex number. The real and imaginary parts of this complex number form the key parts of the subsequent data analysis.
Where E = system voltage; I = system current; t = time domain parameter
By converting the complex form into polar coordinate form, we can get the relationship between the amplitude and phase of the response signal and the excitation signal at a specific frequency.
Where R and X represent the real and imaginary parts of the complex number, respectively. The amplitude calculated above represents the complex impedance of the component under specific frequency conditions. In the case of frequency sweep, the complex impedance corresponding to each frequency point can be calculated.
Impedance data analysis
A common approach is to use the resulting impedance vs. frequency curve as part of the data analysis. When the frequency is swept over a given range, the Nyquist plot is a curve in the complex plane with the real and imaginary parts of the transfer function as parameters. If the x-axis in the figure represents the real part and the y-axis represents the imaginary part (note: the y-axis is negative), the impedance representation at each frequency point can be obtained. In other words, each point on the curve represents the impedance at a certain frequency point. The impedance can be calculated from the vector length |Z| and the angle ? between the vector and the x-axis. Figure 1 shows a typical Nyquist plot when a resistor and a capacitor are connected in parallel.
Although the Nyquist curve is very commonly used, it does not give frequency information, so for any specific impedance, it is impossible to know what frequency value is used. Therefore, the Nyquist curve is usually supplemented by other curves. Another commonly used representation method is the Bode plot. In the Bode plot, the x-axis represents the logarithm of the frequency, and the absolute value of the impedance amplitude |Z| and the phase shift are both represented by the y-axis. Therefore, the Bode plot simultaneously represents the relationship between impedance and frequency and phase shift and frequency. The Nyquist curve and the Bode plot are usually used together to analyze the transfer function of the sensor element.
Impedance-based sensors
Consider a sensor based on impedance characteristics. Under normal conditions, the combination of its capacitance, inductance and resistance characteristics will produce a specific impedance signal. If the changes in the sensor's surrounding environment cause any changes in the above characteristics, it will cause a change in impedance. By measuring the characteristics of this impedance sensor that change with frequency, a series of new impedance characteristics will be obtained.
A fairly simple approach is to compare the measured and predicted impedance values to draw some conclusion. An example of this operating principle is a metal detection sensor that uses the eddy current principle. A high frequency AC signal is generated in a coil located in the sensor housing. The electromagnetic field generated by the coil induces eddy currents in the conductive target. This eddy current in turn interacts with the sensor coil, so changing its impedance.
Figure 2: Bode plots showing impedance vs. frequency and phase angle vs. frequency.
Measuring the impedance of a coil as it changes with frequency has many benefits. Because the permeability of the material affects the impedance of the coil, empirical impedance characteristics can be used to draw some conclusions about the type of metal. This approach can also allow the impedance characteristic sensor to detect metals with different permeabilities. Permeability changes can also be used to measure metal pressure, because changes in pressure change permeability, which in turn changes impedance. Bode plots and Nyquist plots are useful in examining the frequency response of a sensor. Measuring the impedance at a large number of frequency points gives a more accurate result than measuring the impedance at a single frequency point because it helps to remove noise. The best operating frequency point can also be determined by measuring the frequency response of the capacitive and inductive components under certain specific conditions.
The method of comparing the measured impedance to its ideal value is applicable to many sensor technologies based on the principle that impedance characteristics can cause changes in resistance, capacitance or inductance. Common applications range from gas detection using chemical sensors, humidity sensors based on capacitance characteristics, metal coin or particle feature recognition in the gaming or food industry, to soil monitoring in agriculture.
Impedance analysis involves more than simply comparing the impedance response characteristics to their ideal characteristics. Impedance spectroscopy (IS) is often used to characterize a system and obtain valuable information about it. For the purpose of this article, a system is generally defined as a component or material that is in electrical contact with an electrode. This contact can be a solid-solid interface (in the case of many chemical sensors) or a solid-liquid interface (when measuring the concentration of a component in a liquid). Using IS, information can be obtained about the component itself and the interface between the component and the electrode.
The principle of IS exploits the fact that if a small potential is applied to an interface, it polarizes. The way the interface polarizes, combined with the speed at which the polarization changes when the applied potential is reversed, characterizes the properties of the interface. For system interfaces, information such as adsorption and reaction rate constants, diffusion coefficients, and capacitance can be obtained. For the components themselves, information about their dielectric constant, conductivity, charge balance mobility, concentrations of the components, and bulk formation and recombination rates can be estimated.
An equivalent circuit model of the system or component is the basis for analyzing the data generated by the impedance sweep. This model is usually a combination of resistors, capacitors, and inductors connected to simulate the electrical characteristics of the system. We are looking for a model whose impedance matches the measured impedance characteristics at different frequencies. Ideally, the model's components and interconnections are chosen to represent the specific electrochemical characteristics and to match the physical characteristics of the process. An existing model from the literature can be used, or a new model can be established based on experience.
In the case of empirically based models, the best match is found between the empirical model and the measured data. Because the components in the model may not always conform to the physical characteristics of the electrochemical process, the model can be constructed separately to obtain the best match. The empirical model can be established by gradually increasing or decreasing the impedance of the components until the best match is obtained. Modeling is usually done based on the principle of nonlinear least squares fitting (NLLS). With the help of a computer, the NLLS algorithm is used to first preliminarily estimate the model parameters, and then each model parameter is gradually changed and the resulting fit is evaluated. The software is used for iterative processing until an acceptable best fit is found.
Figure 3. Common equivalent circuits used for corrosion analysis
Data analysis and equivalent circuit models should be treated with great care and as many model validations as possible should be performed. Although a very good model can almost always be built by adding components, it cannot be considered to represent the electrochemical process of the system. In general, empirical models should use as few components as possible and should use physical models based on the theoretical basis of the electrochemical process of the system as much as possible.
In addition, it is often possible to build many different empirical models with the same impedance characteristics. Although it is possible to get a good least squares fit model, it is still possible to get an inappropriate model that does not represent the physical system. It is also possible that the NLLS fit algorithm misses some of the measured characteristics or does not converge. This is because many algorithms try to optimize the fit curve over the entire frequency spectrum, so it is possible to miss poor fit data at certain specific frequency points in the spectrum.
Corrosion analysis is a common application and a good example of where IS methods are used to characterize system characteristics. Corrosion of metals, such as aluminum and steel, is a major safety consideration in many industries. If not taken seriously, it can lead to the premature end of the metal's life. The ability to automatically monitor corrosion can provide significant cost savings, safety and reliability advantages, and help optimize preventive maintenance systems.
In addition to determining the extent of corrosion, it is possible to predict metal fatigue by monitoring the rate of corrosion. As metal fatigue develops, it changes from being elastic to being inelastic where small cracks appear. These cracks are new, but the corrosion rate is quite fast, and the rate of crack growth and subsequent corrosion is indicative of the extent of metal fatigue. Methods for early identification of corrosion, especially in locations that are difficult to reach and cannot be seen, can prevent or slow the damage of severe corrosion. It can also be used to help identify different protective coatings under real-world conditions.
The following is an equivalent circuit model of the corrosion process based on physics knowledge and the electrochemical process that occurs during corrosion. The equivalent circuit commonly used for corrosion monitoring is represented by a resistor (Rp) and a capacitor (Cp) in parallel and then in series with a resistor Rs.
In model A, the resistor Rs represents the solution in which the metal is located, while the capacitor Cc represents the protective coating or paint on the metal surface, which represents the capacitance of the initial coating. After a period of time, water penetrates the coating to form a new liquid-metal interface. As the metal corrodes, an ionic conductive path is formed through the protective coating between the solution and the metal. This can be represented by a parallel model of Rx and Cc. In addition, some models (model B) have an additional circuit of R and C in parallel and in series with Rx to represent the delamination model of the metal protective coating over time.
The resistivity or conductivity of the solution in which the metal resides is usually known or easily available, so Rs can be obtained. The value of Cp can also be obtained because it can be calculated from the dielectric constant of the protective coating (usually provided by the manufacturer) and the area it covers. Then it is necessary to solve RX to determine the extent of corrosion. This problem is usually solved by obtaining the best fit of the measured impedance characteristic data through a curve fitting algorithm. Bode plots are also a common method, which detects the characteristics of the corrosion sensor based on its impedance frequency response and phase frequency response.
The IS method is not limited to corrosion analysis, but can be used to characterize a variety of electrochemical systems. For example, it can be used to optimize fuel cell performance, predict battery health, check the concentration of a component in a fluid to determine its quality, and characterize the electrochemical performance of a material.
Optimizing circuit design
Once the equivalent circuit model is determined, the electronic data acquisition system must be designed to complete the frequency sweep and acquire the data. This is usually a complex and time-consuming task that requires an indispensable knowledge of electronics in order to optimize the circuit design.
The designed circuit must be able to generate frequency sweeps with the required resolution over a useful range. In many electrochemical systems, the collected data must be protected from interference from the electrochemical process itself. Therefore, a small AC signal is usually used, and it is also important not to introduce a DC potential difference in the system because it will cause further electrochemical reactions. The ADC must then be used to collect the system's response to the excitation frequency. In some designs, two ADCs are required to capture the excitation signal and the response signal respectively. This is very complicated because the two ADCs need to be sampled synchronously in order to detect phase changes between the signals.
The AD5933 is a typical integrated circuit chip that provides a programmable frequency sweep generator and an integrated ADC that can work with the excitation frequency to obtain the response signal. In addition, the entire system must remain linear. In other words, the total bandwidth of the system must be sufficient and the signal size must be sufficient to obtain good measurement results, but the signal cannot be so large that it exceeds the range of the ADC or other components and causes distortion. Because the impedance range of the component to be measured is usually unknown, it is usually necessary to do some repeated trials at the beginning to optimize the system and ensure its linear characteristics. After converting the response signal into digital form, the digital signal is usually sent to a computer for further analysis.
The latest solutions, such as the AD5933, extract the real and imaginary parts of the response signal before sending it to the computer for processing, completing a large amount of analysis on the chip. This greatly reduces the computing burden on the computer and improves the quality of data acquisition because the analog signal processing circuit is optimized to work with other functional modules. It should be noted that while keeping the entire system linear, the measurement results of the analog signal must be verified, otherwise the final result will be biased even though the computer can easily provide 4 bits or more of accuracy. Careful system design and verification to obtain valid measurements are the key to improving the accuracy of the final result.
Previous article:Analysis and Design of Phase-Sensitive Detector in Atmospheric Electric Field Instrument
Next article:Bioelectrical Impedance Spectrum Measurement System Based on Single Chip Microcomputer
Recommended ReadingLatest update time:2024-11-16 21:23
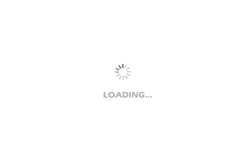
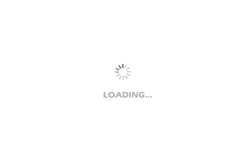
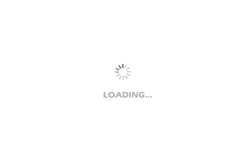
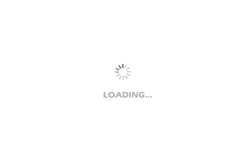
- Popular Resources
- Popular amplifiers
-
Analysis and Implementation of MAC Protocol for Wireless Sensor Networks (by Yang Zhijun, Xie Xianjie, and Ding Hongwei)
-
Introduction to Internet of Things Engineering 2nd Edition (Gongyi Wu)
-
西门子S7-12001500 PLC SCL语言编程从入门到精通 (北岛李工)
-
Modern Motor Control Technology (Wang Chengyuan, Xia Jiakuan, Sun Yibiao)
- High signal-to-noise ratio MEMS microphone drives artificial intelligence interaction
- Advantages of using a differential-to-single-ended RF amplifier in a transmit signal chain design
- ON Semiconductor CEO Appears at Munich Electronica Show and Launches Treo Platform
- ON Semiconductor Launches Industry-Leading Analog and Mixed-Signal Platform
- Analog Devices ADAQ7767-1 μModule DAQ Solution for Rapid Development of Precision Data Acquisition Systems Now Available at Mouser
- Domestic high-precision, high-speed ADC chips are on the rise
- Microcontrollers that combine Hi-Fi, intelligence and USB multi-channel features – ushering in a new era of digital audio
- Using capacitive PGA, Naxin Micro launches high-precision multi-channel 24/16-bit Δ-Σ ADC
- Fully Differential Amplifier Provides High Voltage, Low Noise Signals for Precision Data Acquisition Signal Chain
- Innolux's intelligent steer-by-wire solution makes cars smarter and safer
- 8051 MCU - Parity Check
- How to efficiently balance the sensitivity of tactile sensing interfaces
- What should I do if the servo motor shakes? What causes the servo motor to shake quickly?
- 【Brushless Motor】Analysis of three-phase BLDC motor and sharing of two popular development boards
- Midea Industrial Technology's subsidiaries Clou Electronics and Hekang New Energy jointly appeared at the Munich Battery Energy Storage Exhibition and Solar Energy Exhibition
- Guoxin Sichen | Application of ferroelectric memory PB85RS2MC in power battery management, with a capacity of 2M
- Analysis of common faults of frequency converter
- In a head-on competition with Qualcomm, what kind of cockpit products has Intel come up with?
- Dalian Rongke's all-vanadium liquid flow battery energy storage equipment industrialization project has entered the sprint stage before production
- Allegro MicroSystems Introduces Advanced Magnetic and Inductive Position Sensing Solutions at Electronica 2024
- Car key in the left hand, liveness detection radar in the right hand, UWB is imperative for cars!
- After a decade of rapid development, domestic CIS has entered the market
- Aegis Dagger Battery + Thor EM-i Super Hybrid, Geely New Energy has thrown out two "king bombs"
- A brief discussion on functional safety - fault, error, and failure
- In the smart car 2.0 cycle, these core industry chains are facing major opportunities!
- The United States and Japan are developing new batteries. CATL faces challenges? How should China's new energy battery industry respond?
- Murata launches high-precision 6-axis inertial sensor for automobiles
- Ford patents pre-charge alarm to help save costs and respond to emergencies
- New real-time microcontroller system from Texas Instruments enables smarter processing in automotive and industrial applications
- Has anyone used LT3751 to boost 400V?
- [Voice and vision module based on ESP32S3] Hardware design, debugging and progress-serial port circuit-2
- rfeasylinkRx initialization problem solved
- This mini motorcycle is so cool!
- Ask about the issue of emission exceeding the standard
- What do phase, displacement, sinusoidal light, and gradient light mean in 3D scanners?
- Tektronix's best-selling oscilloscopes are on sale, optional features become standard features, saving up to 50,000!
- [GD32E231 DIY Contest]——06. ESP8266 Software Secondary Development
- 02Power on and program download and debugging
- [Silicon Labs BG22-EK4108A Bluetooth Development Review] VI. WeChat applet controls LED and receives button status 1