1 RFID technology and EPC code
1.1 RFID Technology
RFID radio frequency identification is a contactless automatic identification technology that automatically identifies the target object and obtains relevant data through radio frequency signals. The identification work does not require human intervention and can work in various harsh environments. RFID technology can identify high-speed moving objects and can identify multiple tags at the same time, and the operation is quick and convenient. RFID is a simple wireless system with only two basic components. The system is used to control, detect and track objects. The system consists of an interrogator (or reader) and many transponders (or tags). A unique code is stored in the RFID tag, usually 64 bits, 96 bits or even higher. Its address space is much higher than the space that can be provided by the barcode, so single-item item coding can be achieved. The internal structure of the RFID tag chip mainly includes four parts: RF front end, analog front end, digital baseband processing unit and EEPROM storage unit.
The reader and the tag exchange information by wireless induction, which has the following characteristics: non-contact identification; no need for "line of sight", can be identified through water, paint, wood and even human body; can identify fast-moving objects; can identify multiple objects at the same time, etc. In the application of RFID system, the tag is attached to the identified object (surface or inside), once the identified object with electronic tag enters the readable range, the reader reads the agreed information from the tag automatically and contactlessly, thus completing the function of automatically identifying objects or automatically collecting object mark information. The biggest benefit of using RFID is that it can visualize the production process of the enterprise to effectively reduce costs. Therefore, more and more manufacturers are concerned about and support the development and application of this technology.
1.2 EPC Code
The full name of EPC is Electronic Product Code, which is called product electronic code in Chinese. The carrier of EPC is RFID electronic tag, and the Internet is used to realize the transmission of information. EPC aims to establish a global and open identification standard for each single product, realize the tracking and tracing of single products worldwide, so as to effectively improve the level of supply chain management and reduce logistics costs. EPC is a complete, complex and comprehensive system. Advantages of EPC/RFID technology in warehouse management The data characteristics of EPC/RFID electronic tags are: 1. Contactless reading 2. Long-distance reading 3. Dynamic reading 4. Multiple quantity and variety reading 5. Passive tag 6. Massive storage capacity and other advantages are unmatched by barcodes. Therefore, the use of EPC electronic tag technology can realize digital warehouse management; and with the use of EPC coding, inventory goods can be truly managed in a networked manner.
2 RFID-based production logistics management information system for an automobile manufacturing company
2.1 System Requirements Analysis
The production logistics of the final assembly workshop of a certain automobile manufacturing company is carried out according to the process flow. The final assembly workshop mainly completes the assembly of the body and chassis and the installation of interior parts. Through investigation, research and analysis, the production logistics management system of the final assembly workshop generally has the following problems:
(1) During the equipment process, information entry at each link is done manually, and transcription errors often occur, resulting in the inability to connect work steps normally, affecting the entire production flow.
(2) Workers in the workshop work in shifts every day. The number of workers in each shift is fixed. Sometimes, due to shortage of raw materials or equipment failure, the workload of some workers cannot reach saturation, which increases production costs.
(3) When a product is found to be defective, the specific responsible person cannot be found in time due to incomplete records and inconsistent data.
(4) The communication and connection between the production line and the warehouse is not good enough, resulting in low batching efficiency.
(5) Managers cannot understand the status of the production line intuitively and promptly, and thus cannot adjust the work plan in time according to the actual production situation and conveniently solve problems in production.
According to the above demand analysis, the delay of information transmission and the inaccuracy of information are the key to the whole problem. Therefore, in order to improve the effect of production management and reduce the cost of products, it is necessary to start with the fundamental information collection technology, thereby changing the way of information transmission in the production process. Based on this situation, a logistics management information system based on RFID is proposed.
2.2 System overall structure design
Through the above demand analysis, a dynamic real-time tracking information management system for work-in-process assembly production is constructed to meet the needs of modern enterprises for comprehensive information management, so that managers can see the equipment status of work-in-process in the background. In addition to monitoring the production process, the system also needs to realize data information sharing and real-time statistics to facilitate production monitoring and scheduling of the management department. Based on the above requirements and the actual situation of the unit, the main design of the system adopts a star topology structure of distributed control, as shown in Figure 2. The entire system consists of a production business management layer, a production process monitoring layer, and a data acquisition management layer, and uses a communication interface and Ethernet structure to connect information servers, field bus monitoring servers, RFID readers, and other modules and terminals.
Figure 2 Overall structure of the system
(1) Data collection management layer. Data collection management is the basis for production process supervision and control. It is responsible for collecting equipment information of products in production lines, packaging and uploading to the company management department for production process supervision and control analysis. RFID is the core of the data collection management layer. It collects information from electronic tags through readers and writers and performs simple information preprocessing (decoding, anti-collision, multi-channel information deduplication, information filtering, and classification).
(2) Production process monitoring layer. The production process monitoring layer is responsible for managing the processing information of work-in-progress and the status information of the production line during the production process, and presenting this real-time information to the production management department in a timely manner, so that the enterprise leaders and production management personnel can grasp the first-hand production operation situation. At the same time, the management department can control the production based on this information, adjust the production operation plan and modify the production control parameters in a timely manner, so as to make the production process return to normal working state in the shortest time and ensure that the production plan can be completed smoothly. The production process monitoring layer includes the fieldbus monitoring server, RFID vehicle identification terminal, and vehicle model information display terminal, which form a star network structure through industrial Ethernet.
(3) Business management layer. The business management layer is the top layer of the system and the interface of the entire system to the outside. Through the management layer, the factory-level information network can access the internal system. As the center of workshop-level production management and scheduling, the information server is responsible for integrating and distributing production information reported by the monitoring layer, realizing information sharing within the workshop, and providing reliable analysis basis for managers to issue scheduling instructions in a timely manner.
2.3 System Hardware Selection
The selection of RFID equipment is mainly based on frequency, because the choice of frequency is a key issue in RFID technology. The operating frequencies of RFID systems are mainly: low frequency (30-300KHZ), high frequency (3-30MHZ) and ultra-high frequency (300MHZ-3GHZ). The common operating frequencies of low-frequency systems are 125KHz and 134KHz. This frequency band mainly works through inductive coupling. Its characteristics are short recognition distance and slow transmission speed. The main application areas are: animal husbandry, access control, identity recognition, etc. The common operating frequency of high-frequency systems is 13.56MHz. It changes the voltage on the reader antenna by connecting and disconnecting the load resistor on the sensor, and realizes the amplitude modulation of the antenna voltage by a long-distance sensor. High-frequency systems are used for access control and applications that require the transmission of large amounts of data. Ultra-high frequency systems (working frequencies between 860MHz and 960MHz) transmit energy through electric fields. The reading distance of this frequency band is relatively long, and the passive reading distance can reach about 10m, and the signal transmission speed is fast. Main application areas: management and application in supply chain, management and application of production line automation, etc.
In summary and comparison, considering the electromagnetic characteristics of RFID, in order to reduce costs, ensure efficacy, simplify the system, and facilitate use and maintenance, we use the ultra-high frequency RFS-2022 (2011) reader, which can read and write ISO-18000-6 protocol tags. The system's operating frequency is 902MHz~928MHz, and its performance indicators are: reading distance greater than 5m, writing distance greater than 3m, reading speed is an average of 6ms per word (32bits), writing speed is an average of 50ms per word (32bits), and the number of cards that can be read at one time can reach 30 electronic tags. This frequency band is currently expected to have the greatest application potential, and the frequency and standards used are fully in line with various current laws and regulations.
2.4 System software functional module design
According to the requirements for the overall system design, the entire system mainly includes system management, assembly line production operation management, assembly line production query management, assembly line resource management, and assembly line quality monitoring management. The main modules are described as follows:
2.4.1 System Management
The system management module can define the production and logistics management information system users of a vehicle assembly line, the authority to execute functions, and the authorization of user functions. It also maintains the basic data shared by each subsystem and completes the data backup operation.
2.4.2 Assembly line on-site production operation management
The production plan is accepted in a rolling manner, and the workshop operation plan is automatically generated. The controller set by the system will trigger the reader to read the vehicle model information on the assembly line according to the production rhythm. Through the RFID reading of the tag, the on-site operation information (including the equipment information and quality inspection information of the online vehicle) is input, and the relevant information is entered into the database on the server. At the same time, the vehicle model information, optional equipment, parts and components on the assembly line are displayed in real time on the screen of each workstation. The on-site operator can not only intuitively understand what the current workstation should do, but also publish demand information to the material department in real time, so that the required parts can be delivered to the required workstation in time.
2.4.3 Assembly Line Production Query Management
The production query management function provides managers with timely information about the working status of the production line so that they can prepare for solving problems in production. It can query the assembly information of each workstation, the specific time of assembly, material demand information, employee operation results and other information.
2.4.4 Assembly Line Resource Management
Assembly line resource management is to manage some equipment required for the production line, timely understand the actual use of existing equipment, so as to provide a reference for arranging production or purchasing. The maximum load of the production line per day, week, and month can be formulated according to the situation of the production equipment to ensure the normal progress of production.
2.4.5 Assembly line quality monitoring and management
Comprehensively manage the quality information of the automobile assembly process, realize the automation of quality information collection, and analyze it through the field bus monitoring server so as to make timely adjustments to reduce the generation of waste. This module can realize statistical query and print relevant reports.
3 Conclusion
This article analyzes the production logistics of a certain automobile manufacturing company's assembly workshop and points out that the traditional manual identification method will affect the timeliness and accuracy of information flow, which will further affect the circulation of the entire production due to the unsmooth information flow. After adopting RFID technology with fast identification speed, large storage capacity and real-time data update, the above situation will be solved. Modern production control and logistics control and information management of automobile manufacturing have become an important part of automobile manufacturing.
Previous article:Design of inverted F-type antenna based on Bluetooth technology
Next article:Analysis of various technologies of MIMO antenna
Recommended ReadingLatest update time:2024-11-16 16:47
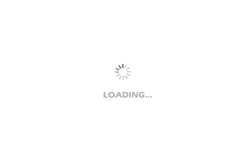
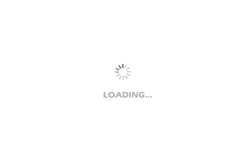
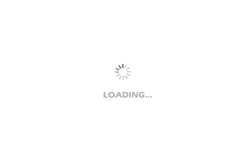
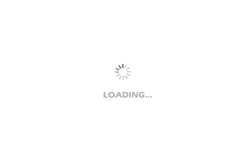
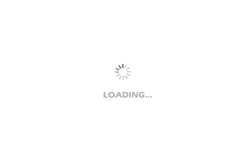
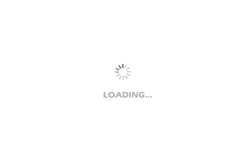
- Popular Resources
- Popular amplifiers
-
Radio Frequency Identification (RFID) System Technology and Application (Written by Ci Xinxin, Wang Subin, and Wang Shuo)
-
MATLAB and FPGA implementation of wireless communication
-
Introduction to Internet of Things Engineering 2nd Edition (Gongyi Wu)
-
Multi-port and shared memory architecture for high-performance ADAS SoCs
- High signal-to-noise ratio MEMS microphone drives artificial intelligence interaction
- Advantages of using a differential-to-single-ended RF amplifier in a transmit signal chain design
- ON Semiconductor CEO Appears at Munich Electronica Show and Launches Treo Platform
- ON Semiconductor Launches Industry-Leading Analog and Mixed-Signal Platform
- Analog Devices ADAQ7767-1 μModule DAQ Solution for Rapid Development of Precision Data Acquisition Systems Now Available at Mouser
- Domestic high-precision, high-speed ADC chips are on the rise
- Microcontrollers that combine Hi-Fi, intelligence and USB multi-channel features – ushering in a new era of digital audio
- Using capacitive PGA, Naxin Micro launches high-precision multi-channel 24/16-bit Δ-Σ ADC
- Fully Differential Amplifier Provides High Voltage, Low Noise Signals for Precision Data Acquisition Signal Chain
- Innolux's intelligent steer-by-wire solution makes cars smarter and safer
- 8051 MCU - Parity Check
- How to efficiently balance the sensitivity of tactile sensing interfaces
- What should I do if the servo motor shakes? What causes the servo motor to shake quickly?
- 【Brushless Motor】Analysis of three-phase BLDC motor and sharing of two popular development boards
- Midea Industrial Technology's subsidiaries Clou Electronics and Hekang New Energy jointly appeared at the Munich Battery Energy Storage Exhibition and Solar Energy Exhibition
- Guoxin Sichen | Application of ferroelectric memory PB85RS2MC in power battery management, with a capacity of 2M
- Analysis of common faults of frequency converter
- In a head-on competition with Qualcomm, what kind of cockpit products has Intel come up with?
- Dalian Rongke's all-vanadium liquid flow battery energy storage equipment industrialization project has entered the sprint stage before production
- Allegro MicroSystems Introduces Advanced Magnetic and Inductive Position Sensing Solutions at Electronica 2024
- Car key in the left hand, liveness detection radar in the right hand, UWB is imperative for cars!
- After a decade of rapid development, domestic CIS has entered the market
- Aegis Dagger Battery + Thor EM-i Super Hybrid, Geely New Energy has thrown out two "king bombs"
- A brief discussion on functional safety - fault, error, and failure
- In the smart car 2.0 cycle, these core industry chains are facing major opportunities!
- The United States and Japan are developing new batteries. CATL faces challenges? How should China's new energy battery industry respond?
- Murata launches high-precision 6-axis inertial sensor for automobiles
- Ford patents pre-charge alarm to help save costs and respond to emergencies
- New real-time microcontroller system from Texas Instruments enables smarter processing in automotive and industrial applications
- c8051F060 program download problem
- 1
- Thermistor, hysteresis resistor, gas resistor, varistor, photoresistor application circuit collection
- Can a bandpass filter be powered from a single supply?
- Discussion on Graphical Programming Method of Single Chip Microcomputer
- Op amp problem
- MSP430 MCU Basics
- Evaluation Invitation Ticket Record Form
- How does a MCU software engineer write simple computer software?
- Smart IoT Student Dormitory Based on RSL10