Characteristics and Application of Driving Circuit IR2110
The power switching devices in the power conversion device can generally be driven directly or isolated according to the main circuit. Among them, isolation drive can be divided into electromagnetic isolation and photoelectric isolation. Photoelectric isolation has the advantages of small size and simple structure, but it also has the disadvantages of poor common mode suppression and slow transmission speed. The speed of fast optocouplers is only tens of kHz. Electromagnetic isolation uses pulse transformers as isolation elements, which have the characteristics of fast response speed (leading and trailing edges of pulses), high insulation strength of primary and secondary sides, and strong dv/dt common mode interference suppression. However, the maximum transmission width of the signal is limited by the magnetic saturation characteristics, so the top of the signal is not easy to transmit. And the maximum duty cycle is limited to 50%. At the same time, the minimum width of the signal is also limited by the magnetizing current. At the same time, the pulse transformer is large in size, bulky, and complex in process.
For all isolated drive methods, each drive requires a set of auxiliary power supplies. If it is a three-phase bridge converter, six sets are required, and they must be suspended from each other, which increases the complexity of the circuit. With the continuous maturity of drive technology, a variety of integrated thick film drivers have been launched. Such as EXB840/841, EXB850/851, M57959L/AL, M57962L/AL, HR065, etc., they all use optocoupler isolation, and optocoupler isolation is still limited by the above shortcomings.
The IR2110 driver produced by IR Company in the United States has the advantages of optocoupler isolation (small size) and electromagnetic isolation (fast speed), and is the preferred variety of driver devices in small and medium power conversion devices.
1 Structural features of IR2110
IR2110 is manufactured using HVIC and latch anti-interference CMOS process, and is packaged in DIP14 pins. The device has independent low-end and high-end input channels. Its floating power supply uses a bootstrap circuit, the high-end operating voltage can reach 500 V, dV/dt=±50 Wns, and the static power consumption at 15 V is only 116 mW. The output terminal of IR2110 (pin 3, i.e., the gate drive voltage of the power device) has a voltage range of 10 to 20 V, and the logic power supply voltage range (pin 9) is 5 to 15 V, which can be easily matched with TTL and CMOS levels, and an offset of ±5 V is allowed between the logic power supply ground and the power ground; in addition, the operating frequency of the device can reach 500 kHz, and the turn-on and turn-off delays are small (120 ns and 94 ns, respectively), and the totem pole output peak current is 2 A. The
internal functional block diagram of IR2110 is shown in Figure 1. As can be seen from the figure, it consists of three parts: logic input, level shifting and output protection. IR2110 can bring a lot of convenience to the design of the device, especially the successful design of the high-end floating bootstrap power supply, which can greatly reduce the number of driving power supplies.
2 Selection of bootstrap components
Figure 2 shows a half-bridge drive circuit based on IR2110. The bootstrap diode VD1 and capacitor C1 are components that need to be strictly selected when IR2110 is used in high-power pulse width modulation amplifiers, and should be calculated and analyzed according to certain rules. During the circuit experiment, some adjustments should be made to make the circuit work in the best state.
2.1 Design of bootstrap capacitor
IGBT and PM (POWER MOSFET) have similar gate characteristics. They both need to provide sufficient gate charge to the gate in a very short time when turned on. Assume that after the device is turned on, the voltage across the bootstrap capacitor is higher than the voltage required for the device to fully turn on (10 V, the high-voltage side locking voltage is 8.7/8.3 V), and there is a 1.5 V voltage drop (including the forward voltage drop of VD1) on the bootstrap capacitor charging path. At the same time, it is assumed that 1/2 of the gate voltage (the gate threshold voltage VTH is usually 3 to 5 V) causes a voltage drop due to leakage current. Then, the corresponding bootstrap capacitor can be expressed as follows:
For example, the gate charge Qg required when IRF2807 is fully turned on is 160 nC (can be found in the IRF2807 electrical characteristics table), Vcc is 15V, then:
In this way, C1 is about 0.1 μF, and a monolithic capacitor with a C1 of 0.22 μF or larger and a withstand voltage greater than 35 V can be selected in the design.
2.2 Determination of the maximum on-time ton(max) of the suspension drive
When the longest on-time ends, the gate voltage Vgs of the power device must still be high enough, that is, it must satisfy the constraint relationship of formula (1). For MOSFET, because the input impedance of the insulated gate is relatively high, if the gate capacitor (Cgs) is charged, a 15μA leakage current (IgQs) is drawn from C1 when Vcc is 15 V. If the parameters of the bootstrap capacitor design in this article are still used as an example, Qg=160 nC, △U=Vcc-10-1.5=3.5 V, Qavail=△UC=3.5x0.22=0.77μC. Then the excess charge △Q=0.77-0.16=0.61 μC, △Uc=△Q/C=0.61/0.22=2.77 V, so Uc=10+2.77=12.77 V can be obtained. From U=Uc and the gate input impedance R is 1 MΩ, t (i.e. ton(max) can be calculated as:
2.3 Determination of the narrowest on-time ton(min) of the suspension drive
In the charging path of the bootstrap capacitor, the distributed inductance will affect the charging rate. The narrowest on-time of the lower tube should ensure that the bootstrap capacitor has enough charge to meet the charge required by Gge plus the charge lost by the leakage current when the power device is turned on in a steady state. Therefore, considering the narrowest on-time ton(min), the bootstrap capacitor should be small enough.
In fact, when selecting the size of the bootstrap capacitor, comprehensive considerations should be made. It should not be so large as to affect the driving performance of the narrow pulse, but it should not be too small.
2.4
Selection The bootstrap diode is an important bootstrap device. It should be able to block the high voltage on the DC mains when the high-end device is turned on, and it should be a fast recovery diode to reduce the feedback charge from the bootstrap capacitor to the power supply Vcc. The current borne by the diode is the product of the gate charge and the switching frequency. In order to reduce charge loss, a fast recovery diode with a small reverse leakage current should be selected.
If the capacitor needs to store charge for a long time, the high-temperature reverse leakage current is very important. The diode withstand voltage selection can be determined according to the requirements of the subsequent power MOSFET tube, and its maximum reverse recovery time trr must be less than or equal to 100 ns. The current IF borne by the diode is Qbsf.
3 Extended application of IR2110
3.1 Bootstrap
principle In the circuit diagram of IR2110 used to drive the half bridge shown in Figure 2, C1 and VD1 are the bootstrap capacitor and diode respectively, and C2 is the filter capacitor of VCC. Assume that during the period when S1 is turned off, C1 has been charged to a sufficient voltage (Vc1≈Vcc). Then, when HIN is high, VM1 is turned on, VM2 is turned off, VC1 is added between the gate and emitter of S1, and C1 is discharged through VM1, Rg1 and S1 gate gate capacitance Cgc1, so that Cgc1 is charged. At this time, VC1 can be equivalent to a voltage source. When HIN is low, VM2 is turned on, VM1 is turned off, and the gate charge of S1 is quickly released through Rg1 and VM2, causing S1 to turn off. Then after a short dead time (td), LIN is high, S2 is turned on, VCC charges C1 through VD1 and S2, and quickly replenishes energy for C1, and this cycle repeats.
It can be seen that the bootstrap circuit can only play a normal bootstrap role when the IR2110 input signal is constantly changing in high and low levels and the bootstrap capacitor is repeatedly charged and discharged. When the input signal of IR2110 is a DC level signal, the bootstrap capacitor will not be able to complete the charge storage, that is, it cannot be charged normally, and therefore cannot provide a driving signal for the high-end diode. If the shortcomings of this function of IR2110 are not solved, when the motor load actually works at a duty cycle of 1 and the voltage across the load is zero, the motor will stop working; at the same time, it will also bring a large current change rate to the power switch tube, thereby affecting the service life and long-term reliability of the power tube. Therefore, the following two technical measures should be taken in work.
(1) Application of input amplitude identification circuit
In order to overcome the above shortcomings, an input amplitude identification circuit can be designed in work, and its circuit is shown in Figure 3. This circuit can not only ensure that the width-modulated square wave signal is output in the linear region of the input signal, but also that when the input signal is outside the linear region, the circuit can also output a fixed duty cycle signal. In this way, it can ensure that the motor can rotate normally outside the linear region, and at the same time, it can also ensure that the output load current will not produce a large mutation.
(2) Charge pump circuit
When the circuit inputs a 100% duty cycle signal, its core oscillator circuit CD4093 will generate a square wave signal of a certain frequency. When this square wave signal is at a low level, the power supply +Vs charges the energy storage capacitor C3 through D5; and when this square wave signal is at a high level, C3 charges the bootstrap capacitor C2 through D4 to maintain the energy of the bootstrap capacitor, and finally when the circuit inputs a 100% duty cycle signal, the H bridge outputs a 100% duty cycle signal, while also ensuring the continuity of the output current. Figure 4 shows the charge pump circuit diagram.
3.2 Anti-straight-through conduction delay circuit
After adding complementary signals to the upper and lower bridge arm power transistors of the H bridge drive circuit, the off time of the transistor is usually longer than the on time under load. In this way, when the lower bridge arm transistor is not turned off in time and the upper bridge arm is turned on first, the so-called "bridge arm straight-through" fault will occur. This will cause the current to increase rapidly when the bridge arm is straight-through, thereby causing damage to the power switch. Therefore, it is essential to set the turn-on delay and dead time. IR2110 has a certain dead time, which is 10 ns and cannot be adjusted externally. In actual use, the turn-off time of the MOSFET tube is sometimes greater than 10ns than the turn-on time. At this time, an external delay circuit is needed to increase the dead time to prevent the circuit from being directly connected. Figure 5 shows a turn-on delay circuit and its waveform.
The turn-on delay can also be set by the RC time constant. For GTR, it can be set at 0.2μs/A; for MOSFET, it can be designed at 0.1~0.2μs, and it has nothing to do with the current; IGBT can be designed at 2~5μs. If the f of GTR is 5 kHz and bipolar operation, the adjustment width area is T/2=1/10=0.1 ms. At this time, if I is 100 A, then △t=0.2×100=20μs. The maximum possible resolution of PWM modulation is:
This means that the dead time occupies 1/5 of the modulation cycle, which is obviously not feasible. Therefore, for a 100 A motor system, the switching frequency of GTR must be lower than 5 kHz. For example, below 2 kHz, the resolution can reach about 12.5.
4 Conclusion
IR2110 is a driver integrated circuit with relatively good performance. Its bootstrap suspension drive power supply can simultaneously drive the upper and lower switching devices of the same bridge arm, with a drive voltage of up to 500 V, an operating frequency of 500 kHz, and a power supply undervoltage protection shutdown logic. The output of IR2110 uses a totem pole structure, with a drive peak current of 2 A, and two channels are also equipped with a low-voltage delay lock (50ns). In addition, the chip also has a protection terminal SD that locks the two outputs. When the SD input is high, both outputs are locked. These advantages of IR2110 bring great convenience to the actual system design, especially the bootstrap suspension drive power supply greatly simplifies the drive power supply design, because only one power supply can complete the drive of the two power switch devices of the upper and lower bridge arms. However, compared with other driver integrated circuits, the protection function of IR2110 is slightly insufficient, and the dead time cannot be adjusted externally; when the circuit works at a 100% duty cycle signal input, an external charge pump circuit is also required to maintain sufficient energy for the bootstrap capacitor. However, these deficiencies can be improved and supplemented in practical applications through the extended application circuit described in this article.
The author of this article has applied the above extended application circuit to the application development of the SAxx series products of the American APEX company, and achieved good results. The developed products have passed all the identification tests and the identification organized by the National Defense Science and Technology Commission. This achievement can replace similar products of APEX in aerospace and weapon systems, and the system works normally, and users are quite satisfied.
Previous article:Application circuit and principle of LM324
Next article:Design of audio decoder using WM8741
Recommended ReadingLatest update time:2024-11-17 00:41
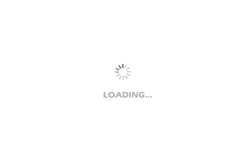
- High signal-to-noise ratio MEMS microphone drives artificial intelligence interaction
- Advantages of using a differential-to-single-ended RF amplifier in a transmit signal chain design
- ON Semiconductor CEO Appears at Munich Electronica Show and Launches Treo Platform
- ON Semiconductor Launches Industry-Leading Analog and Mixed-Signal Platform
- Analog Devices ADAQ7767-1 μModule DAQ Solution for Rapid Development of Precision Data Acquisition Systems Now Available at Mouser
- Domestic high-precision, high-speed ADC chips are on the rise
- Microcontrollers that combine Hi-Fi, intelligence and USB multi-channel features – ushering in a new era of digital audio
- Using capacitive PGA, Naxin Micro launches high-precision multi-channel 24/16-bit Δ-Σ ADC
- Fully Differential Amplifier Provides High Voltage, Low Noise Signals for Precision Data Acquisition Signal Chain
- Innolux's intelligent steer-by-wire solution makes cars smarter and safer
- 8051 MCU - Parity Check
- How to efficiently balance the sensitivity of tactile sensing interfaces
- What should I do if the servo motor shakes? What causes the servo motor to shake quickly?
- 【Brushless Motor】Analysis of three-phase BLDC motor and sharing of two popular development boards
- Midea Industrial Technology's subsidiaries Clou Electronics and Hekang New Energy jointly appeared at the Munich Battery Energy Storage Exhibition and Solar Energy Exhibition
- Guoxin Sichen | Application of ferroelectric memory PB85RS2MC in power battery management, with a capacity of 2M
- Analysis of common faults of frequency converter
- In a head-on competition with Qualcomm, what kind of cockpit products has Intel come up with?
- Dalian Rongke's all-vanadium liquid flow battery energy storage equipment industrialization project has entered the sprint stage before production
- Allegro MicroSystems Introduces Advanced Magnetic and Inductive Position Sensing Solutions at Electronica 2024
- Car key in the left hand, liveness detection radar in the right hand, UWB is imperative for cars!
- After a decade of rapid development, domestic CIS has entered the market
- Aegis Dagger Battery + Thor EM-i Super Hybrid, Geely New Energy has thrown out two "king bombs"
- A brief discussion on functional safety - fault, error, and failure
- In the smart car 2.0 cycle, these core industry chains are facing major opportunities!
- The United States and Japan are developing new batteries. CATL faces challenges? How should China's new energy battery industry respond?
- Murata launches high-precision 6-axis inertial sensor for automobiles
- Ford patents pre-charge alarm to help save costs and respond to emergencies
- New real-time microcontroller system from Texas Instruments enables smarter processing in automotive and industrial applications
- What is the difference between AGPS and DGPS?
- Can Software Radio Become Open Radio?
- Sincerely recruiting embedded software and hardware engineers
- The problem of sending 10 seconds of data through the network port
- What is the function of the forward connection of the op amp output to the voltage regulator diode here?
- Adjustable speed fan cooling system with temperature measurement feedback
- Wi-Fi Solutions for IoT Wireless Designs
- [TI recommended course] #TI? Application of interface chips in automotive products#
- 【GD32E231_DIY】-01: Schematic diagram & PCB
- Live broadcast at 10 am today [ST three-phase motor control solution for home appliances]