In the field of industrial measurement and control, a large number of real-time field parameters need to be obtained. Due to the harsh, complex and changeable environment, data acquisition systems are mostly completed by industrial computers. However, industrial computers are large in size, power consumption, poor in reliability, inconvenient to install and expensive. In addition, there are dedicated data acquisition systems that can work independently and are completed using DSP (digital signal processor) and MCU (microcontroller). The disadvantages are high prices and poor human-computer interaction. The rapid development of embedded processors has effectively made up for the shortcomings of industrial computers, especially ARM processors. It not only combines the advantages of the above-mentioned acquisition systems and overcomes their shortcomings, but also adds some new functions and new features. The addition of new functions and new features has further expanded its application field and scope, and can be targeted at different needs with great flexibility.
This solution is implemented using ARM processors. ARM processors are usually SoC chips. Their large number of on-chip peripherals and more powerful performance than traditional controllers such as single-chip microcomputers are their main features. Today's ARM processors have the ability to handle simple signal processing. Using ARM processors in system design will undoubtedly benefit from all aspects, including performance, function, cost, power consumption and other aspects.
1 System operation principle and hardware design
This project studies the data acquisition hardware platform based on the ARM7 chip STM32F103VBT6 and the data processing software platform based on the embedded Linux operating system. A platform integrating embedded control, high-speed data acquisition, real-time processing and friendly human-computer interaction interface has been developed, which can perform high-speed acquisition, processing and display of field signals. The hardware modules of the data acquisition system mainly include: front-end conditioning module, A/D conversion module, microprocessor main module, and human-machine interface unit. The basic structure diagram of the system is shown in Figure 1.
1.1 Signal conditioning module
The signal conditioning module conditions the sensor signal. Through the isolation, amplification, filtering, etc. of signal conditioning, the reliability and performance of the data acquisition system are greatly improved. To design a suitable signal conditioning circuit, not only the content of the signal conditioning itself should be considered, but also the application environment of the signal conditioning circuit and the significance of the measured parameters.
1.2 ARM processor
In a multi-tasking system, the kernel is responsible for managing each task, or allocating the CPU to each task. The first step in building a data acquisition system hardware development platform is to choose the ARM core. Various series of ARM systems, such as ARM7, ARM9, etc., are targeted at different embedded system applications.
The system uses the 32-bit ARM Cortex-M3 processor STM32F103VBT6 as the main control chip, which has very rich on-chip resources, such as real-time clock (RTC), timer (TIM), general I/O interface (GPIO), DMA controller, A/D converter, USART interface, I2C interface, SPI interface and CAN bus interface, as well as 20 kB on-chip SRAM, 128 KB on-chip FLASH and a full-speed USB peripheral device that supports USB 2.0 specification. It is the main control unit of the entire system, coordinating other modules to complete multiple functions such as data acquisition, storage, processing, control, and transmission. [page]
1.3 Analog-to-digital conversion circuit
The important indicators to measure the performance of an acquisition system are its sampling speed and sampling accuracy. Therefore, the A/D chip is one of the most important devices in the data acquisition system. For the data acquisition of analog signals, it is necessary not only to consider how to cooperate with the front-end signal conditioning part and the back-end signal processing part, but also to consider some requirements of the data acquisition itself. In other words, it is necessary not only to consider the relevant parameters of the analog input, the signal type and connection method of the measurement system, the sampling method, etc., but also to consider how the acquisition module is connected to the microprocessor module behind. At present, there are many varieties of A/D converters on the market, and each chip has different control methods and application conditions. For general industrial acquisition systems, under the condition of ensuring accuracy and speed, the sampling speed should be increased as much as possible to meet the requirements of real-time acquisition, real-time processing and real-time control. Usually, a successive approximation type or parallel comparison type A/D converter is selected. This system uses TI's 16-bit high-speed sampling analog/digital converter (ADC) ADS8317 to achieve fast conversion of analog signals to digital signals.
The power supply voltage of ADS8317 ranges from 2.7 to 5.5 V. It requires only a small amount of current when working at full speed, and when working at low speed, it can keep the high-speed device in shutdown mode most of the time, so that the average power consumption at a data rate of 10 kHz is less than 0.2 mW. The device is widely used in battery-powered systems, remote data acquisition, independent data acquisition, industrial control, robots, vibration analysis and simultaneous sampling of multi-channel systems. The system uses two multiplexers MPC506, and the circuit for converting the signal output from its OUT end to ADS8317 for A/D conversion is shown in Figure 2.
[page]
1.4 Debug interface circuit
As the main control chip, STM32F103VBT6 has a 20-pin JTAG debugging interface that complies with the IEEE STDll49.1-1990 standard. Through this interface, the operation of the chip can be controlled and internal information can be obtained. The system uses the JTAG interface to debug the program and burn the program into the FLASH. It connects the five signal lines TD1, TMS, TCK, TD0, and NRESE-T inside the STM32F103VBT6. Four of them are inputs, and each is connected to an external pull-up resistor to ensure reliable signal transmission. NRESET is the reset pin of the internal JTAG interface circuit. The system reset signal can be connected through a 1 kΩ resistor to use the MULTI-ICE emulator for debugging. The circuit is shown in Figure 3.
2 Software design
For embedded systems, their software design is closely related to the hardware platform. Different hardware environments will affect the choice of operating system. After the hardware solution is determined, the choice of operating system is relatively easy.
When choosing the type of embedded operating system, in addition to the economic cost, the main consideration is their performance evaluation indicators. In addition, there are some other factors: the degree of support for development tools such as compilers, keyers, debuggers, etc.; portability and difficulty of porting; whether the memory supports MMU; whether it is scalable and supports user customization capabilities; the quality of real-time performance and whether the network function is powerful, etc., which are also our key considerations.
At present, the open source free software Linux operating system has become the most used soft real-time embedded operating system, which is due to its unique characteristics and advantages: low development cost, customizable kernel, perfect integrated development environment, and good portability. This system uses the Linux operating system and designs the application on the Linux platform. The flow chart is shown in Figure 4.
3 Conclusion
This system is developed and designed using ARM7. It has the characteristics of high precision, stable operation, good real-time performance, strong anti-interference ability, and high cost performance. It can be widely used in various industrial occasions. The
use of an embedded microprocessor based on ARM7 can make the system miniaturized, facilitate performance improvement and connection and expansion with various peripherals, while reducing costs and being stable and reliable in specific applications.
Previous article:Intelligent wireless signal transmitter based on ARM
Next article:Design of MVB_CAN Gateway Based on ARM7
Recommended ReadingLatest update time:2024-11-16 15:56
![[Embedded] Use Qt to add a software keyboard to ARM9 (mini2440) and add a dynamic link library](https://6.eewimg.cn/news/statics/images/loading.gif)
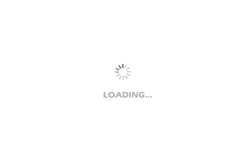
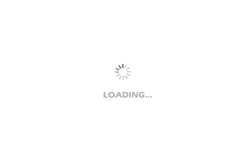
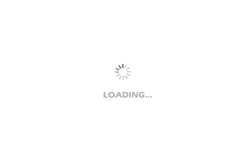
- Popular Resources
- Popular amplifiers
Professor at Beihang University, dedicated to promoting microcontrollers and embedded systems for over 20 years.
- Innolux's intelligent steer-by-wire solution makes cars smarter and safer
- 8051 MCU - Parity Check
- How to efficiently balance the sensitivity of tactile sensing interfaces
- What should I do if the servo motor shakes? What causes the servo motor to shake quickly?
- 【Brushless Motor】Analysis of three-phase BLDC motor and sharing of two popular development boards
- Midea Industrial Technology's subsidiaries Clou Electronics and Hekang New Energy jointly appeared at the Munich Battery Energy Storage Exhibition and Solar Energy Exhibition
- Guoxin Sichen | Application of ferroelectric memory PB85RS2MC in power battery management, with a capacity of 2M
- Analysis of common faults of frequency converter
- In a head-on competition with Qualcomm, what kind of cockpit products has Intel come up with?
- Dalian Rongke's all-vanadium liquid flow battery energy storage equipment industrialization project has entered the sprint stage before production
- Allegro MicroSystems Introduces Advanced Magnetic and Inductive Position Sensing Solutions at Electronica 2024
- Car key in the left hand, liveness detection radar in the right hand, UWB is imperative for cars!
- After a decade of rapid development, domestic CIS has entered the market
- Aegis Dagger Battery + Thor EM-i Super Hybrid, Geely New Energy has thrown out two "king bombs"
- A brief discussion on functional safety - fault, error, and failure
- In the smart car 2.0 cycle, these core industry chains are facing major opportunities!
- The United States and Japan are developing new batteries. CATL faces challenges? How should China's new energy battery industry respond?
- Murata launches high-precision 6-axis inertial sensor for automobiles
- Ford patents pre-charge alarm to help save costs and respond to emergencies
- New real-time microcontroller system from Texas Instruments enables smarter processing in automotive and industrial applications
- What is the manufacturing process level of a microcontroller like STM32?
- LM27762 Charge Pump with Integrated Positive and Negative LDO
- Transfer a video "There is a kind of beauty called mathematics"
- Let novices quickly understand Zigbee----Zigbee Overview
- #RecommendChinaCore# Activity sharing summary
- STM32F030 MCU ADC cannot be interrupted after DMA is enabled
- Why do I think Jiali Chuang’s marketing has failed?
- I have some questions about CORTEX-M TARGET DRIVER SETUP.
- Notepad++ displays Chinese characters normally, but keil4 and source insight4 display garbled characters?
- [New ways to play with SAMR21] 15. WS2812 colored lights