Modern communication equipment, electronic products, electric vehicles, UPS, etc. generally use batteries as power sources. However, most charging devices have single functions, poor versatility, and low maintenance quality, which greatly reduces the efficiency of product use. This paper uses UCC3895 and PIC microcontrollers to design and develop an intelligent charger for commonly used lead-acid batteries.
UCC3895 is a new control chip produced by TI that is dedicated to PWM phase-shifted full-bridge DC/DC conversion. It can work in voltage mode or current mode, and can realize output pulse duty cycle from 0 to 100% phase shift control. Soft start and soft stop can be adjusted as required; built-in 7MHz bandwidth error comparison amplifier; has perfect current limiting and overcurrent protection, power supply undervoltage protection, reference undervoltage protection, soft start and soft stop functions.
PICl6F917 microcontroller and UCC3895 together form the controller part. Compared with the method of using only microcontroller as the controller, it has the advantages of fast response speed, high control accuracy, simple software design, and stable operation.
l Overall structure
As shown in Figure 1, the power supply of the charger uses a switching power supply, and its input is 220V AC mains. After rectification and filtering, one part provides auxiliary working power and reference voltage for the digital devices of the control circuit, and the other part is converted into high-frequency AC through full-bridge inverter, and then high-frequency rectification and filtering are performed to provide 0-60V pulse DC for the battery. PIC and UCC3895 cooperate to form a closed-loop control circuit. By comparing the user set value and the feedback value obtained by sampling, the inverter is PWM controlled at different stages of the charging process. At the same time, PIC completes functions such as display and alarm.
2 Hardware Design
1) Main Circuit Design
As shown in Figure 2, the charging main circuit adopts phase-shifted full-bridge ZVT-PWM conversion technology, using the output capacitor of the power MOS tube and the leakage inductance of the output transformer as resonant elements, so that the four switch tubes of the FB-PWM converter are turned on in sequence at zero voltage, realizing constant frequency soft switching, reducing switching losses, and ensuring that the transformer efficiency reaches 80-90%, and there will be no problem of excessive switch stress.
2) Control circuit design
The control circuit is divided into two parts. The first part is the front-stage controller, which consists of UCC3895 and its peripheral circuits, used to generate PWM pulses to control the switch tube. The second part is the back-stage controller, which consists of PIC and TLV5618 and their peripheral circuits, and realizes the management functions of the charging process such as user settings, sampling, display, timing, alarm, main circuit on and off. [page]
0 Introduction
Modern communication equipment, electronic products, electric vehicles, UPS, etc. generally use batteries as power sources. However, most charging devices have single functions, poor versatility, and low maintenance quality, which greatly reduces the efficiency of product use. This paper uses UCC3895 and PIC microcontrollers to design and develop an intelligent charger for commonly used lead-acid batteries.
UCC3895 is a new control chip produced by TI that is dedicated to PWM phase-shifted full-bridge DC/DC conversion. It can work in voltage mode or current mode, and can realize output pulse duty cycle from 0 to 100% phase shift control. Soft start and soft stop can be adjusted as required; built-in 7MHz bandwidth error comparison amplifier; has perfect current limiting and overcurrent protection, power supply undervoltage protection, reference undervoltage protection, soft start and soft stop functions.
PICl6F917 microcontroller and UCC3895 together form the controller part. Compared with the method of using only microcontroller as the controller, it has the advantages of fast response speed, high control accuracy, simple software design, and stable operation.
l Overall structure
As shown in Figure 1, the power supply of the charger uses a switching power supply, and its input is 220V AC mains. After rectification and filtering, one part provides auxiliary working power and reference voltage for the digital devices of the control circuit, and the other part is converted into high-frequency AC through full-bridge inverter, and then high-frequency rectification and filtering are performed to provide 0-60V pulse DC for the battery. PIC and UCC3895 cooperate to form a closed-loop control circuit. By comparing the user set value and the feedback value obtained by sampling, the inverter is PWM controlled at different stages of the charging process. At the same time, PIC completes functions such as display and alarm.
2 Hardware Design
1) Main Circuit Design
As shown in Figure 2, the charging main circuit adopts phase-shifted full-bridge ZVT-PWM conversion technology, using the output capacitor of the power MOS tube and the leakage inductance of the output transformer as resonant elements, so that the four switch tubes of the FB-PWM converter are turned on in sequence at zero voltage, realizing constant frequency soft switching, reducing switching losses, and ensuring that the transformer efficiency reaches 80-90%, and there will be no problem of excessive switch stress.
2) Control circuit design
The control circuit is divided into two parts. The first part is the front-stage controller, which consists of UCC3895 and its peripheral circuits, used to generate PWM pulses to control the switch tube. The second part is the back-stage controller, which consists of PIC and TLV5618 and their peripheral circuits, and realizes the management functions of the charging process such as user settings, sampling, display, timing, alarm, main circuit on and off. [page]
Sampling part
Since PIC's RA0~RA2 can be used as A/D channels at the same time, they are used to receive the sampled battery voltage, charging current, and battery temperature, and convert them into ten-bit binary numbers for storage. The charging current is converted into a voltage value through an external detection resistor and linearly calculated, and the battery temperature is obtained through the temperature sensor TC1047.
The control output and alarm part
TLV5618 is connected to the microcontroller, serially receives the digital signal representing the user's set value sent by RB0, completes the DA conversion, and outputs the obtained analog quantity through OUTA (control voltage VKV) and OUTB (control current VKI), providing reference voltage and reference current for
UCC3895
. RB3 and RB4 are set as outputs to control the main circuit on and off (SWITCH) and drive the alarm device (BUZZ). RB5 is set as input to receive the alarm signal (ALART).
3 Software Design
According to the charging characteristics of lead-acid batteries, in order to improve charging efficiency, extend battery life and achieve fast charging, this paper adopts a three-stage intelligent identification charging method. As shown in Table 1, taking a 12V lead-acid battery as an example, different conversion voltages, conversion currents and floating charge voltages are selected at different temperatures in each charging stage.
1) Main program
The charging main program mainly completes the initialization of each functional part, cyclic sampling, display output real-time status, judgment of charging stage, charging timing, fault alarm and other tasks. Its flow chart is shown in Figure 7.
2) Constant current charging stage[page]
Figure 8 is a flowchart of the constant current charging stage. The microcontroller controls UCC3895 according to the set charging current value to make the main circuit output a constant current. According to the current temperature, the conversion voltage from the constant current to the constant voltage stage is obtained by looking up the table, and the battery voltage is sampled. When the battery voltage exceeds the conversion voltage, this stage ends and enters the constant voltage charging stage; if it does not exceed, continue sampling. During the process, it is also determined whether there is an overcurrent (at this time ALART=1) or the set charging time has been reached to determine whether to stop charging.
3) Constant voltage charging stage
Figure 9 is a flow chart of the constant voltage charging stage. The microcontroller controls UCC3895 according to the current battery voltage value to make the main circuit output a constant voltage and sample the current. If the current is less than the floating charge stage conversion value, this stage ends and enters the floating charge stage; if it is not less than, continue sampling. During the process, it is also determined whether there is an overvoltage (at this time ALART=1) or the set charging time has been reached to determine whether to stop charging.
4) Floating charge stage
In this stage, the battery is fully charged. In order to make up for the energy loss of the battery self-discharge, the microcontroller controls UCC3895 according to the floating charge voltage value in Table 1 to make the main circuit output a constant voltage and give the battery a small charging current. At the same time, the charging voltage and current of the battery are judged to switch between the constant voltage charging and constant current charging stages, and the charging time is judged. If the charging time is up, the main circuit is disconnected (SWITCH=0, and charging stops. The flow chart is similar to the constant voltage stage.
4 Conclusion
The intelligent charger designed with UCC3895 and PIC microcontroller as controller can charge the commonly used 12V~48V lead-acid batteries, ensure the battery full rate, and prevent overcharging. The whole charger is small in size, simple in structure, low in cost, has good charging management and maintenance functions, and is conducive to extending the service life of the battery, with very high practical value and promotion value.
Previous article:Design of CAN bus ultrasonic ranging intelligent node based on PIC18F2580
Next article:Design of ABS electronic controller based on dsPIC30F5011
Recommended ReadingLatest update time:2024-11-16 20:32
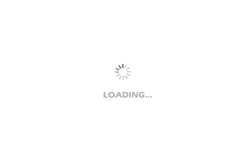
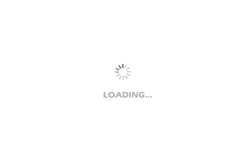
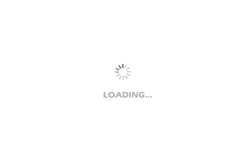
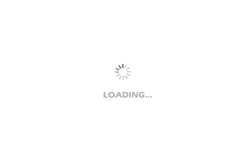
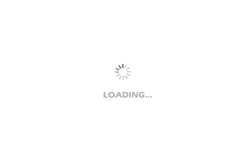
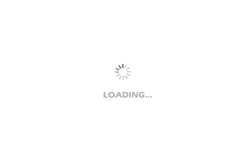
- Popular Resources
- Popular amplifiers
Professor at Beihang University, dedicated to promoting microcontrollers and embedded systems for over 20 years.
- Innolux's intelligent steer-by-wire solution makes cars smarter and safer
- 8051 MCU - Parity Check
- How to efficiently balance the sensitivity of tactile sensing interfaces
- What should I do if the servo motor shakes? What causes the servo motor to shake quickly?
- 【Brushless Motor】Analysis of three-phase BLDC motor and sharing of two popular development boards
- Midea Industrial Technology's subsidiaries Clou Electronics and Hekang New Energy jointly appeared at the Munich Battery Energy Storage Exhibition and Solar Energy Exhibition
- Guoxin Sichen | Application of ferroelectric memory PB85RS2MC in power battery management, with a capacity of 2M
- Analysis of common faults of frequency converter
- In a head-on competition with Qualcomm, what kind of cockpit products has Intel come up with?
- Dalian Rongke's all-vanadium liquid flow battery energy storage equipment industrialization project has entered the sprint stage before production
- Allegro MicroSystems Introduces Advanced Magnetic and Inductive Position Sensing Solutions at Electronica 2024
- Car key in the left hand, liveness detection radar in the right hand, UWB is imperative for cars!
- After a decade of rapid development, domestic CIS has entered the market
- Aegis Dagger Battery + Thor EM-i Super Hybrid, Geely New Energy has thrown out two "king bombs"
- A brief discussion on functional safety - fault, error, and failure
- In the smart car 2.0 cycle, these core industry chains are facing major opportunities!
- The United States and Japan are developing new batteries. CATL faces challenges? How should China's new energy battery industry respond?
- Murata launches high-precision 6-axis inertial sensor for automobiles
- Ford patents pre-charge alarm to help save costs and respond to emergencies
- New real-time microcontroller system from Texas Instruments enables smarter processing in automotive and industrial applications
- Thank you for being there + bow deeply
- How to view the complex technical documentation of TI DSP
- Please help analyze this circuit.
- kicad-eda_6-layer-pcb_A64-OlinuXino_Rev_D
- The wheel speed pulse signal of the car is too narrow, and the sampling frequency of the equipment is too low to collect it. Is there any way to extend the pulse width?
- Battery Test Equipment --- Signal Chain
- iTOP-4418 development board TF card burning-boot uboot
- LSM6DSL cannot generate interrupts, WAKE_UP_SRC is always 0; changing CTRL1_XL doubles the Z-axis reading
- MSP432 learning experience: system tick timer
- Introduce the factors to be considered in selecting DSP chips with examples