introduction
Considering the impending global energy crisis and people's growing expectations for environmental protection, energy conservation is essential for the operation of efficient wireless networks. The power amplifier (PA) is the heart of base stations and repeaters, and its power consumption may account for half of the total power consumption of base stations. Monitoring the power amplifier can not only improve power efficiency, reduce operating costs, improve output power and linearity, but also enable system operators to detect and solve problems in a timely manner, thereby improving reliability and maintainability.
Analog Devices offers three PA monitor implementations: a discrete device solution, an integrated monitoring and control system based on the AD729422 12-bit, and an integrated solution based on the ADuC7026 high-precision analog microcontroller3. Discrete solutions require more components, and the PCB layout is complex and the PCB area is large, all of which lead to higher costs. The advantages of the AD7294 are high integration, low cost, and high reliability, but the disadvantage is that an external microcontroller (MCU) is required to implement the PA monitoring function. The ADuC7026 has many of the same advantages as the AD7294, with the main difference being that the ADuC7026 includes an MCU. In addition, the ADuC7026 supports external synchronous sampling, a feature that is useful in TD-SCDMA applications.
This article introduces a reference design based on the ADuC7026 to implement power amplifier monitoring. The functions include setting the output power, monitoring the voltage standing wave ratio (VSWR), monitoring the drain current and temperature of the laterally diffused metal oxide semiconductor (LDMOS) field effect transistor, and issuing an alarm signal when a parameter exceeds a predetermined threshold.
System Block Diagram
Figure 1 shows the system block diagram of the PA monitor. The RF signal is transmitted by the antenna after being processed by the variable voltage attenuator (VVA), ADL5323 pre-driver, power amplifier, and bidirectional coupler. The on-chip MCU of ADuC7026 samples the temperature and current of the two-stage LDMOS in the PA module and the forward and reverse power of the PA module. The MCU sends the sampled data to the PC for display on the user interface (UI). The operator can adjust the system parameters through the user interface.

Figure 1: System block diagram.
PA monitoring module
Temperature monitoring: The power consumption of the power amplifier affects its performance. The PA sometimes operates at a higher quiescent operating point, but the output power is low. A large amount of energy is converted into heat in the LDMOS device, which not only wastes energy but also reduces reliability. Monitoring the temperature of the PA and adjusting its quiescent operating point can enable the system to achieve optimal performance.
Figure 2 shows the functional block diagram of the temperature monitor, which uses the ADT75 digital temperature sensor to monitor the temperature of the two LDMOS stages. The ADT75 (available in 8-pin MSOP and SOIC packages) converts the temperature into a digital signal with a resolution of 0.0625°C, and its shutdown mode reduces the supply current to 3µA (typical).

Figure 2: Temperature monitor functional block diagram.
Figure 3 shows the flow chart of the temperature monitoring program. After receiving the temperature detection command, the ADuC7026 MCU first sets the temperature detection flag, then reads the temperature data from the ADT75 through the I2C® bus and sends the data to the PC. Next, the program checks the overtemperature pin (OS/ALERT) status of the ADT75 and lights the LED if the temperature exceeds the threshold. When receiving the command to configure the temperature threshold, the ADuC7026 reads the configuration data from the PC and writes the threshold temperature to the ADT75 through the I2C bus. When the microcontroller receives the command to read the temperature threshold, it reads the threshold temperature from the ADT75 and transmits it to the PC.

Figure 3: Flowchart of the temperature monitoring procedure.
Current Monitoring: Controlling the PA drain current to keep it constant over temperature and time can greatly improve the overall performance of the PA while ensuring that the PA operates within the regulated output power range. The two main factors that affect the PA drain current are changes in the PA's high voltage supply line and changes in on-chip temperature. The drain voltage of the PA transistor is easily affected by changes in the high voltage supply line. The drain current of the LDMOS can be measured using a high voltage current shunt monitor. If the drain current is continuously monitored, the operator can readjust the gate voltage to keep the LDMOS at the optimal operating point when voltage fluctuations occur on the power supply.
Figure 4 shows the functional block diagram of the current monitor. The system uses the AD8211 high-voltage, high-precision current shunt amplifier to sample the drain current of the two LDMOS stages in the PA module. The gain of the AD8211 is fixed at 20V/V, and the gain error is ±0.5% (typical) over the entire operating temperature range. The output voltage of the AD8211 buffer is directly output to the analog-to-digital converter and sampled by the on-chip ADC of the ADuC7026. The drain current threshold is set by the AD5243 digital potentiometer, and the ADuC7026 controls the AD5243 through the I22C bus. The system determines whether the drain current exceeds or falls below the threshold based on the output of the ADCMP600 comparator. If the drain current exceeds the threshold, the system lights up the corresponding LED to alert the operator.

Figure 4: Current monitor functional block diagram.
Voltage Standing Wave Ratio (VSWR) Monitoring: VSWR is a key parameter of the antenna system, which reflects the matching degree between the components in the antenna system. Reverse power affects the output power of the PA, and excessive reverse power will cause distortion of the transmitted signal. Therefore, it is necessary to monitor VSWR to ensure the optimal performance of the base station.
Figure 5 shows the functional block diagram of the VSWR monitor. The system uses a bidirectional coupler and the AD8364 dual-channel TruPwr™ detector to measure forward and reverse power. The AD8364 dual-channel rms RF power measurement subsystem can accurately measure and control the power of the signal. The AD8364 is highly flexible and can easily monitor and control RF power amplifiers, radio transceiver AGC circuits, and other communication systems. Its output can be used to calculate VSWR and monitor the matching of transmission lines. Large VSWR values indicate that the antenna is faulty and the operator should protect the system by adjusting the PA gain or power supply voltage.
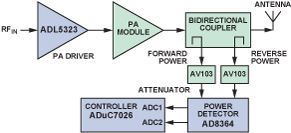
Figure 5: VSWR monitor functional block diagram. Automatic power control: According to the requirements of the communication system, the transmitter must ensure that the power amplifier can meet the transmission needs, adjust the base station transmission power to maintain a precise value, and control the output power within the coverage range. It is not too small to meet the coverage distance requirements during network planning, and it will not reduce the cell coverage range, and will not produce too strong output signals to interfere with adjacent base stations. Since overpower will cause the power amplifier to saturate and cause nonlinear distortion of the signal, the system should provide overpower protection to ensure that the power amplifier does not work under overpower conditions. For the above reasons, the output power must be measured and controlled to keep it stable.
Figure 6 shows the functional block diagram of the automatic power control loop, which includes a bidirectional coupler, a TruPwr detector, a microcontroller, and a variable voltage attenuator. The bidirectional coupler transmits the forward power to the TruPwr detector, which tracks the changes in the signal amplitude. The ADuC7026 on-chip ADC samples the output of the detector. The microcontroller compares the actual value of the output power with the expected value and uses a PID algorithm to adjust the control voltage deviation to make the power amplifier operate at the best performance point.

Figure 6: Functional block diagram of the automatic power control loop.
Figure 7 shows the flow chart of the PID algorithm. First, the program sets the initial control parameters Kp, Ki, and Kd and sets the expected value of the output power. Then, the ADC samples the output of the AD8364, and the sampled data is converted into power after filtering. The program calculates the difference between the expected value and the actual value of the output power, as well as the next expected sample value and the control voltage based on the transfer function of the system, and configures the DAC register. This completes a sampling and control process cycle, and this process is repeated continuously.

Figure 7: Flowchart of the PID algorithm.
user interface
The UI is mainly used to provide a human-computer interaction interface, display the detection data in real time, and respond to the operator's input commands. Figure 8 shows the flowchart of the user interface program. After the program is running, the serial port must be opened and the communication link must be started. Then, each functional module can be selected for monitoring and control.

Figure 8: Flowchart of UI control.
Figure 9 shows a temperature test result. The user can change the high and low temperature thresholds at any time. In this example, the high temperature threshold is changed from 35°C to 31°C. When the ambient temperature rises above the new threshold, the over-temperature alarm light turns red and the PC emits a continuous alarm sound.

Figure 9: Interface for displaying temperature test results.
Hardware Hookup
Figure 10 shows the connection diagram of the demonstration circuit board of the PA monitor. The main board is powered by a 6V adapter and is connected to the PC through a serial port line so that the lower computer ADuC7026 can communicate with the upper computer PC; the RF signal generated by the ADF4252 evaluation board is connected to the RF signal input of the main control board, and then output through the following link: RF input → adjustable attenuator AV103 → PA pre-stage driver power amplifier ADL5323 → dual directional coupler ZABDC10-25HP → RF output → spectrum analyzer Agilent 4396B. The output frequency of the ADF4252 evaluation board is controlled by the PC, and the PC and ADF4252 are connected by a parallel-to-serial cable.

Figure 10: PA monitor demonstration board hardware connections.
in conclusion
This reference design provides an integrated solution for monitoring and controlling PA in cellular base stations (GSM, EDGE, UMTS, CDMA, TD-SCDMA), point-to-multipoint and other RF transmission systems. Using ADI's high-precision analog microcontroller ADuC7026 to implement PA monitor applications can increase flexibility because it has multi-channel high-performance 12-bit ADCs and DACs, as well as an on-chip programmable logic array (PLA). Its AD conversion can be started by external conversion input or PLA conversion output. This feature is very helpful for TD-SCDMA application systems that require forward power sampling using a synchronization signal. The benefits of integrating PLA on the chip are very obvious: users can easily and concisely implement various logics according to requirements. Moreover, various algorithms, such as PID control, VSWR monitoring, temperature monitoring, and current monitoring algorithms can be implemented by ADuC7026 without the use of other controllers. From the perspective of system design, this integrated solution can save PCB area, facilitate PCB layout, reduce system cost and improve system reliability.
Previous article:Application of P1 port of new microcontroller AduC812
Next article:A schedule management system based on MSP430 single chip microcomputer
Professor at Beihang University, dedicated to promoting microcontrollers and embedded systems for over 20 years.
- Innolux's intelligent steer-by-wire solution makes cars smarter and safer
- 8051 MCU - Parity Check
- How to efficiently balance the sensitivity of tactile sensing interfaces
- What should I do if the servo motor shakes? What causes the servo motor to shake quickly?
- 【Brushless Motor】Analysis of three-phase BLDC motor and sharing of two popular development boards
- Midea Industrial Technology's subsidiaries Clou Electronics and Hekang New Energy jointly appeared at the Munich Battery Energy Storage Exhibition and Solar Energy Exhibition
- Guoxin Sichen | Application of ferroelectric memory PB85RS2MC in power battery management, with a capacity of 2M
- Analysis of common faults of frequency converter
- In a head-on competition with Qualcomm, what kind of cockpit products has Intel come up with?
- Dalian Rongke's all-vanadium liquid flow battery energy storage equipment industrialization project has entered the sprint stage before production
- Allegro MicroSystems Introduces Advanced Magnetic and Inductive Position Sensing Solutions at Electronica 2024
- Car key in the left hand, liveness detection radar in the right hand, UWB is imperative for cars!
- After a decade of rapid development, domestic CIS has entered the market
- Aegis Dagger Battery + Thor EM-i Super Hybrid, Geely New Energy has thrown out two "king bombs"
- A brief discussion on functional safety - fault, error, and failure
- In the smart car 2.0 cycle, these core industry chains are facing major opportunities!
- Rambus Launches Industry's First HBM 4 Controller IP: What Are the Technical Details Behind It?
- The United States and Japan are developing new batteries. CATL faces challenges? How should China's new energy battery industry respond?
- Murata launches high-precision 6-axis inertial sensor for automobiles
- Ford patents pre-charge alarm to help save costs and respond to emergencies
- LIS2HH12 MEMS Digital Output Motion Sensor Datasheet
- The problem of not being able to sample the AD value using the official ADC routine based on the BlueNRG-LP chip
- [RVB2601 Creative Application Development] Environmental Monitoring Terminal 06-Synchronize Data to Alibaba Cloud
- One question per week, relax and broaden your mind
- Crowdfunding 3,000 yuan to buy batteries for needle penetration tests, BYD VS CATL technology game
- [Evaluation of EC-01F-Kit, the NB-IoT development board of Anxinke] + Alibaba Cloud connection to upload light illumination data
- Operate the lmx2582 registers through stm32, the project file is in the attachment
- 【ESP32-S2-Kaluga-1 Review】2. Update the firmware
- Speed sensor
- How to use Labview to perform secondary development on Ginkgo 2