The following is an example of the steps to port u-boot to the 44B0 development board. Only the hardware-related parts need to be modified during the porting. In terms of code structure:
1) Create the ev44b0ii directory in the board directory, and create ev44b0ii.c, flash.c, memsetup.S, u-boot.lds, etc. You don't need to start from scratch. You can choose a similar directory, copy it directly, and modify the file name and content. When I was porting u-boot, I chose the ep7312 directory. Since u-boot already contains the development board directory based on s3c24b0, you can also copy the corresponding directory as a reference.
2) Create the arm7tdmi directory in the cpu directory, which mainly contains start.S, interrupts.c, cpu.c, and serial.c files. There is no need to create files from scratch. Just copy them from arm720t and then modify the corresponding content.
3) Add ev44b0ii.h in the include/configs directory, and put global macro definitions here.
4) Find the Makefile in the u-boot root directory and modify it to add
ev44b0ii_config: unconfig
@./mkconfig $(@:_config=) arm arm7tdmi ev44b0ii
5) Run make ev44bii_config, if there is no error, you can start the hardware related code transplantation work
3. u-boot architecture
1) Overall structure
u-boot is a hierarchical structure. As can be seen from the above figure, the software personnel doing the transplantation work should provide serial port driver (UART Driver), Ethernet driver (Ethernet Driver), Flash driver (Flash Driver), USB driver (USB Driver). At present, it is not very necessary to download the program through the USB port, so the USB driver has not been transplanted for the time being. Above the driver layer is the u-boot application, and the command provides a human-machine interface through the serial port. We can use some commands to do some common work, such as the memory viewing command md.
The Kermit application is mainly used to support the use of the serial port to download applications through the hyperterminal. TFTP is to download applications through the network, such as the uclinux operating system.
2) Memory distribution
Memory distribution in flash rom The flash size of ev44b0ii is 2M (8bits), and now 0-40000, a total of 256k, is used as the storage space of u-boot. Since there are some environment variables in u-boot, such as IP address, boot file name, etc., they can be configured through setenv in the command line and saved in the space of 40000-50000 (64k in total) through saveenv. If there are saved environment variables, u-boot boot will directly use these environment variables. As can be seen from the code analysis, we will move the flash boot code to DRAM for execution. The following figure shows the location of the u-boot code in DRAM. The boot code u-boot will be moved from 0x0000 0000 to 0x0C700000. Special attention should be paid to the fact that the interrupt vector program address of ev44b0ii uclinux is at 0x0c00 0000, so the program cannot be downloaded to 0x0c00 0000, and is usually downloaded to 0x0c08 0000.
4. Start.S Code Structure
1) Define Entry
An executable Image must have an entry point and can only have one unique global entry point, which is usually placed at the 0x0 address of Rom (flash). For example,
.globl _start
_start in start.S:
It is worth noting that you must tell the compiler to know this entry point. This work mainly involves modifying the connector script file (lds).
2) Set the Exception Vector
The exception vector table, also known as the interrupt vector table, must start from address 0 and be stored continuously. The following includes reset, undefined handling (undef), software interrupt (SWI), pre-instruction error (Pabort), data error (Dabort), reserved, and IRQ, FIQ, etc. Note that the value here must be consistent with the vector_base of uclinux. That is to say, if vector_base (include/armnommu/proc-armv/system.h) in uclinux is defined as 0x0c00 0000, then HandleUndef should be at
0x0c00 0004.
b reset //for debug
ldr pc,=HandleUndef
ldr pc,=HandleSWI
ldr pc,=HandlePabort
ldr pc,=HandleDabort
b .
ldr pc,=HandleIRQ
ldr pc,=HandleFIQ
ldr pc,=HandleEINT0 /*mGA H/W interrupt vector table*/
ldr pc,=HandleEINT1
ldr pc,=HandleEINT2
ldr pc,=Han dleEINT3
ldr pc,=HandleEINT4567
ldr pc,=HandleTICK /*mGA*/
b .
b .
ldr pc,=HandleZDMA0 /*mGB*/
ldr pc,=HandleZDMA1
ldr pc,=HandleBDMA0
ldr pc,=HandleBDMA1
ldr pc,=HandleWDT
ldr pc,=
HandleTIMER4
ldr
pc
,=
HandleTIMER5 /*
mGC
*/
b .
b .
ldr pc,=HandleTIMER2 ldr pc,=HandleTIMER3
ldr
pc,=HandleTIMER4 /*mGC*/
b .
=HandleURXD0 /*mGD*/
ldr pc,=HandleURXD1
ldr pc,=HandleIIC
ldr pc,=HandleSIO
ldr pc,=HandleUTXD0
ldr pc,=HandleUTXD1 /*mGD*/
b .
b .
ldr
pc,=HandleRTC /*mGKA*/
b
. b .
b .
b .
b . /*mGKA*/
b .
b .
ldr pc,=HandleADC /*mGKB*/
b .
b .
b .
b .
b . /*mGKB*/
b .
b .
ldr pc,=EnterPWDN
For comparison: See the values of the above tags:
.equ HandleReset, 0xc000000
.equ HandleUndef,0xc000004
.equ HandleSWI, 0xc000008
.equ HandlePabort, 0xc00000c
.equ HandleDabort, 0xc000010
.equ HandleReserved, 0xc000014
.equ HandleIRQ, 0xc000018
.equ HandleFIQ, 0xc00001c
/*the value is different with an address you think it may be.
*IntVectorTable */
.equ HandleADC, 0xc000020
.equ HandleRTC, 0xc000024
.equ HandleUTXD1, 0xc000028
.equ HandleUTXD0, 0xc00002c
.equ HandleSIO, 0xc000030
.equ HandleIIC, 0xc000034
.equ HandleURXD1, 0xc000038 .equ
HandleURXD0, 0xc00003c
.equ
HandleTIMER 5, 0xc000040
.equ HandleTIMER4, 0xc000044
.equ HandleTIMER3, 0xc000048
.equ HandleTIMER2, 0xc00004c
.equ HandleTIMER1, 0xc000050
.equ HandleTIMER0, 0xc000054
.equ HandleUERR01, 0xc000058
.equ HandleWDT, 0xc00005c
.equ HandleBDMA1, 0xc000060
.equ HandleBDMA0, 0xc000064
.equ HandleZDMA1, 0xc000068 .equ
HandleZDMA0, 0xc00006c
.equ HandleTICK, 0xc 000070
.equ HandleEINT4567, 0xc000074
.equ HandleEINT3, 0xc000078
.equ HandleEINT2, 0xc00007c
.equ HandleEINT1, 0xc000080
.equ HandleEINT0, 0xc000084
3) Initialize CPU Related pll, clock, interrupt control registers
These are to turn off the watch dog timer, turn off interrupts, set LockTime, PLL (phase lock loop), and clock.
These values (except LOCKTIME) can be found in the Samsung 44b0 manual.
ldr r0,WTCON //watch dog disable
ldr r1,=0x0
str r1,[r0]
ldr r0,INTMSK
ldr r1,MASKALL //all interrupt disable
str r1,[r0]
/************ *******************************************
* Set clock control registers *
* *************************************************** **/
ldr r0,LOCKTIME
ldr r1,=800 // count = t_lock * Fin (t_lock=200us, Fin=4MHz) = 800
str r1,[r0]
ldr r0,PLLCON /*temporary setting of PLL*/
ldr r1 ,PLLCON_DAT /*Fin=10MHz,Fout=40MHz or 60MHz*/
str r1,[r0]
ldr r0,CLKCON
ldr r1,=0x7ff8 //All unit block CLK enable
str r1,[r0]
4) Initialize memory controller
The memory controller is mainly configured by setting 13 registers starting from 1c80000, including bus width,
8 memory banks, bank size, sclk, and two bank modes.
/* ************************************************** **
* Set memory control registers *
****************************************** ***********/
memsetup:
adr r0,SMRDATA
ldmia r0,{r1-r13}
ldr r0,=0x01c80000 //BWSCON Address
stmia r0,{r1-r13}
5) Put the program in rom Copy to RAM
First, use PC to get the starting address of bootloader in flash, and then calculate
the size of the program code by the difference of labels. The compiler will generate the correct distribution value of these labels when linking. After getting
the correct information, copy the code to RAM through registers (r3 to r10) as the intermediate medium for copying.
relocate:
/*
* relocate armboot to RAM
*/
adr r0, _start /* r0 <- current position of code */
ldr r2, _armboot_start
ldr r3, _armboot_end
sub r2, r3, r2 /* r2 <- size of armboot */
ldr r1, _TEXT_BASE /* r1 <- destination address */
add r2, r0, r2 /* r2 <- source end address */
/*
* r0 = source address
* r1 = target address
* r2 = source end address
*/
copy_loop:
ldmia r0!, {r3-r10}
stmia r1!, {r3-r10}
cmp r0, r2
ble copy_loop
6) Initialize stack
Enter various modes and set the stack of corresponding mode.
InitStacks:
/*Don't use DRAM,such as stmfd,ldmfd...
SVCstack is initialized before*/
mrs r0,cpsr
bic r0,r0,#0X1F
orr r1,r0,#0xDB /*UNDEFMODE|NOINT*/
msr cpsr,r1 /*UndefMode*/
ldr sp,UndefStack
orr r1,r0,#0XD7 /*ABORTMO DE|NOINT*/
msr cpsr,r1 /*AbortMode*/
ldr
sp,AbortStack
orr r1,r0,#0XD2 /*IRQMODE|NOINT*/
msr cpsr,r1 /*IRQMode*/
ldr sp,IRQStack
orr r1,r0,#0XD1 /*FIQMODE|NOINT*/
msr cpsr,r1 /*FIQMode*/
ldr sp,FIQStack
bic r0,r0,#0XDF /*MODEMASK|NOINT*/
orr r1,r0,#0X13
msr cpsr,r1 /*SVCMode*/
ldr sp,SVCStack
7) Transfer to RAM for execution
Use the instruction ldr,pc, the C function address in RAM to transfer to RAM for execution.
5. System initialization part
1. Serial port part
The setting of the serial port mainly includes the initialization of the serial port part. It is worth noting that the Baudrate of the serial port is closely related to the clock MCLK, which is calculated by: rUBRDIV0=( (int)(MCLK/16./(gd ->baudrate) + 0.5) -1 ). This can be found in the manual. Other functions include sending and receiving. There is no interrupt at this time, and the loop wait is used to determine whether the action is completed.
For example, the receiving function:
while(!(rUTRSTAT0 & 0x1)); //Receive data read
return RdURXH0();
2. Clock part
The delay function udelay is implemented.
Since get_timer here does not use interrupts, it uses global variables to accumulate.
3. Flash part
As part of the memory, there is definitely no problem in reading flash. The key is the writing part of flash.
Flash must be erased first and then written.
unsigned long flash_init (void)
{
int i;
u16 manId,devId;
//first we init it as unknown, even if you forget assign it below, it's not a problem
for (i=0; i < CFG_MAX_FLASH_BANKS; ++i){
flash_info[i].flash_id = FLASH_UNKNOWN;
flash_info[i].sector_count=CFG_MAX_FLASH_SECT;
}
/* check manId,devId*/
_RESET();
_WR(0x555,0xaa);
_WR(0x2aa,0x55);
_WR(0x555,0x90);
manId=_RD(0x0);
_WR(0x555,0xaa);
_WR(0x2aa,
0x55
);
_WR(0x555,0x90);
devId=_RD(0x1);
_RESET();
printf("flashn");
printf("Manufacture ID=%4x(0x0004), Device ID(0x22c4)=%4xn",manId,devId);
if(manId!=0x0004 && devId!=0x22c4){
printf("flash check faliluren");
return 0;
}else{
for (i=0; i < CFG_MAX_FLASH_BANKS; ++i){
flash_info[i].flash_id=FLASH_AM160T;/*In fact it is fujitu,I only don't want to
modify common files*/
}
}
/* Setup offsets */
flash_get_offsets (CFG_FLASH_BASE, &flash_info[0]);
/* zhangyy comment
#if CFG_MONITOR_BASE >= CFG_FLASH_BASE
//onitor protection ON by default
flash_protect(FLAG_PROTECT_SET,
CFG_MONITOR_BASE,
CFG_MONITOR_BASE+monitor_flash_len-1,
&flash_info[0]);
#endif
*/
flash_info[0].size = PHYS_FLASH_SIZE;
return (PHYS_FLASH_SIZE);
}
flash_init completes the initialization part. The main purpose here is to check the flash Is the model correct?
int flash_erase (flash_info_t *info, int s_first, int s_last)
{
volatile unsigned char *addr = (volatile unsigned char *)(info->start[0]);
int flag, prot, sect, l_sect;
//ulong start, now, last;
u32 targetAddr;
u32 targetSize;
/*zyy note:It is required and can't be omitted*/
rNCACHBE0=( (0x2000000>>12)<<16 )|(0>>12); //flash area(Bank0) must be non-cachable
area.
rSYSCFG=rSYSCFG & (~0x8); //write buffer has to be off for proper timing.
if ((s_first < 0) || (s_first > s_last)) {
if ( info->flash_id == FLASH_UNKNOWN) {
printf ("- missingn");
} else {
printf ("- no sectors to erasen");
}
return 1;
}
if ((info->flash_id == FLASH_UNKNOWN) ||
(info->flash_id > FLASH_AMD_COMP)) {
printf ("Can't erase unknown flash type - abortedn");
return 1;
}
prot = 0;
for (sect=s_first; sect<=s_last; ++sect) {
if (info->protect[sect]) {
prot++;
}
}
if (prot) {
printf ("- Warning: %d protected sectors will not be erased!n",
prot);
} else {
printf ("n");
}
l_sect = -1;
/* Disable interrupts which might cause a timeout here */
flag = disable_interrupts();
/* Start erase on unprotected sectors */
for (sect = s_first; sect<=s_last; sect++) {
if (info->protect[sect] == 0) {/* not protected */
targetAddr=0x10000*sect;
if(targetAddr<0x1F0000)
targetSize=0x10000
;
else if(targetAddr<0x1F8000) targetSize=0x8000; else if(targetAddr<0x1FC000
)
targetSize=0x2000;
else
targetSize=0x4000;
F29LV160_EraseSector(targetAddr);
l_sect = sect;
if(! BlankCheck (targetAddr, targetSize))
printf("BlankCheck Errorn");
}
}
/* re-enable interrupts if necessary */
if (flag)
enable_interrupts();
/* wait at least 80us - let's wait 1 ms */
udelay (1000 );
/*
*We wait for the last triggered sector
*/
if (l_sect < 0)
goto DONE;
DONE:
printf (" donen");
return 0;
}
int BlankCheck(int targetAddr,int targetSize)
{
int i,j;
for(i=0;i{
j=*((u16 *)(i+targetAddr));
if( j!=0xffff)
{
printf(" E:%x=%xn",(i+targetAddr),j);
return 0;
}
}
return 1;
}
flash_erase erases flash, BlankCheck checks whether the content is erased successfully.
/*----- -------------------------------------------------- ----------------
*Write a word to Flash, returns:
* 0 - OK
* 1 - write timeout
* 2 - Flash not erased
*/
static int write_word (flash_info_t *info, ulong dest, ulong data)
{
volatile u16 *tempPt;
/*zhangyy note:because of compatiblity of function,I use low & hi*/
u16 low = data & 0xffff;
u16 high = (data >> 16) & 0xffff;
low=swap_16(low);
high=swap_16(high);
tempPt=(volatile u16 *)dest;
_WR(0x555,0xaa);
_WR(0x2aa,0x55);
_WR(0x555,0xa0);
* tempPt=high;
_WAIT();
_WR(0x555,0xaa);
_WR(0x2aa,0x55);
_WR(0x555,0xa0);
*(tempPt+1)=low;
_WAIT();
return 0;
}
write_word to flash Write unsigned long data in it. Since the flash can only write 16 bits at a time, it is written in two times.
Previous article:Analysis of uboot.lds of uboot
Next article:uboot_freescale_imx51_start.s_Detailed explanation
Recommended ReadingLatest update time:2024-11-15 18:34
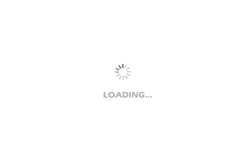
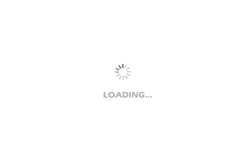
- Popular Resources
- Popular amplifiers
Professor at Beihang University, dedicated to promoting microcontrollers and embedded systems for over 20 years.
- LED chemical incompatibility test to see which chemicals LEDs can be used with
- Application of ARM9 hardware coprocessor on WinCE embedded motherboard
- What are the key points for selecting rotor flowmeter?
- LM317 high power charger circuit
- A brief analysis of Embest's application and development of embedded medical devices
- Single-phase RC protection circuit
- stm32 PVD programmable voltage monitor
- Introduction and measurement of edge trigger and level trigger of 51 single chip microcomputer
- Improved design of Linux system software shell protection technology
- What to do if the ABB robot protection device stops
- Sandia Labs develops battery failure early warning technology to detect battery failures faster
- Ranking of installed capacity of smart driving suppliers from January to September 2024: Rise of independent manufacturers and strong growth of LiDAR market
- Industry first! Xiaopeng announces P7 car chip crowdfunding is completed: upgraded to Snapdragon 8295, fluency doubled
- P22-009_Butterfly E3106 Cord Board Solution
- Keysight Technologies Helps Samsung Electronics Successfully Validate FiRa® 2.0 Safe Distance Measurement Test Case
- Innovation is not limited to Meizhi, Welling will appear at the 2024 China Home Appliance Technology Conference
- Innovation is not limited to Meizhi, Welling will appear at the 2024 China Home Appliance Technology Conference
- Huawei's Strategic Department Director Gai Gang: The cumulative installed base of open source Euler operating system exceeds 10 million sets
- Download from the Internet--ARM Getting Started Notes
- Learn ARM development(22)
- LaunchPad Development Kit for SimpleLinktm MCUs
- Automatically generate Dockerfile to build Docker image
- [Help] What happens if PT100 is used at over-temperature?
- Design of frequency sweeper using digital frequency synthesis technology, FPGA and single chip microcomputer
- Bluetooth MESH technology makes up for the shortcomings of networking
- Some Problems with Differential Circuits
- Performance indicators of power amplifiers
- Common base amplifier circuit problems
- Analog input
- [Sipeed LicheeRV 86 Panel Review] 10-Video Playback Test