Micro-arc oxidation (MAO) is a surface treatment technology that grows a ceramic layer in situ on the metal surface. This technology uses the principles of plasma chemistry and electrochemistry to produce micro-area arc discharge on the material surface. Under the combined action of chemistry, electrochemistry and plasma, a new technology for in-situ growth of ceramic layers is used. The micro-arc oxidation power supply is one of the key links to ensure the micro-arc oxidation process. Its main function is to generate and control the pulsed electric field and the automatic detection and control of process parameters during the micro-arc oxidation production process.
The micro-arc oxidation power supply developed in this paper adopts power module commutation technology to achieve the high voltage, large current, wide bandwidth and high-quality positive and negative pulse output required by the micro-arc oxidation process. The ARM-based automatic control system is used to realize automatic monitoring of electrical parameters such as voltage, current, pulse frequency, and duty cycle. The ARM (Advanced RISC Machines) processor is a 32-bit embedded microprocessor. Compared with industrial control computers, the ARM embedded microprocessor has the advantages of small size, light weight, low cost, and high reliability; compared with the 16-bit single-chip microcomputer in reference 2 [2], the ARM embedded microprocessor has the advantages of fast speed, multiple functions, low power consumption, and good scalability. The CPU used in the micro-arc oxidation power supply control system developed in this paper is the ARM7-based LPC2119 processor, which is a 16/32-bit CPU that supports real-time simulation and embedded tracking. It has a zero-wait 256K on-chip FLASH and 16K SRAM, and does not require extended memory. It has many peripheral components such as UART, hardware I2C, SPI bus, PWM, timer, ADC, CAN bus controller, etc., and is powerful.
2. Description of the control system
The main circuit of the micro-arc oxidation power supply consists of four parts: transformer output, thyristor rectification, inductor capacitor filtering, and IGBT chopper converter [3]. The main task of the micro-arc oxidation power supply control system designed in this paper is to drive the thyristors, IGBTs and other modules of the micro-arc oxidation control system according to the process requirements, and complete the functions of setting process requirements, storing process numbers, and outputting alarm signals. Therefore, this control system is divided into the following parts:
Minimum system part: generates CPU working power, external crystal oscillator and JATAG debugging port;
A/D and D/A conversion part: collect voltage and current values and send the set values to the thyristor module;
Input and output part: generates some input and output signals;
CAN communication part: transmit and receive some setting parameters;
E2PROM part: completes the storage of process number and real-time data.
3. Hardware system design
3.1 Minimum system part
Figure 1 Minimum system diagram
As shown in Figure 1, the minimum system consists of a reset circuit, a crystal oscillator circuit, a power supply circuit, and LPC2119. The reset chip uses the MAX809 monitoring chip, which can output a low-level reset pulse with a width of up to 240MS, which is enough to ensure real-time reset of the system; the external crystal oscillator is set to 11.0592MHZ, and the internal frequency can be multiplied to 60MHZ, which greatly improves the speed of the CPU; the power supply circuit mainly provides the LPC2119 with two required voltages, one is 3.3 volts for powering the external port, and the other is 1.8 volts for powering the ARM core; LPC2119 has 256K on-chip FLASH and 16K SRAM with zero waiting, no need to expand the memory, and also has a watchdog function, which not only saves resources for the system, but also improves reliability.
3.2 A/D and D/A conversion section
The schematic diagram is shown in Figure 2. TLC2543 is a 12-bit serial analog-to-digital converter from TI, which uses switched capacitor successive approximation technology to complete the A/D conversion process. It has a conversion time of 10μs, 11 analog input channels, a serial input structure, supports SPI bus timing (and LPC2119 itself has an SPI interface, which saves I/O resources), and is moderately priced and has a high resolution.
MAX5322 is a ±10V dual 12-bit serial digital-to-analog converter with an operating voltage of ±12V~±15V and an output from ±5V~±10V. It has excellent INL and DNL linearity, with a maximum value of ±1LSB and a settling time of 10us to 0.5LSB. Since it also has a serial input structure and supports SPI bus timing, MAX5322 and TLC2543 can share the SPI bus. Different chips can be selected by chip select. This design not only saves the I/O resources of LPC2119, but also facilitates programming.
The function of TLC2543 is to convert the collected real-time voltage and current values into digital values, and transmit them to the host computer through the CAN bus for display; the function of MAX5322 is to convert the working voltage and working current values set by the host computer into analog values to control the output of the thyristor so that it reaches the set voltage in a very short time. When there are positive and negative outputs, adding a MAX5322 can meet the requirements.
The function of the CAN interface is to transmit some variables to be displayed to the host computer and to transmit the variables set by the host computer to the lower computer, such as voltage, current, PWM frequency, duty cycle, number of positive pulses and negative pulses, etc. The CAN bus is widely used in data communication between detection and actuators in control systems due to its high performance, high reliability, and real-time performance. It has been recognized as one of the most promising field buses. It is a multi-master bus, and the communication medium can be twisted pair. The communication rate can reach 1M/s and the maximum communication distance can reach 10km. It is a serial communication local area network that supports distributed real-time control systems [1]. LPC2119 itself has an integrated CAN controller, so only an external CAN transceiver PCA82C250 is needed to drive CAN bus communication. As shown in Figure 3.
Figure 2 A/D and D/A conversion circuits
Figure 3 CAN communication circuit
Figure 4 E2PROM circuit
3.4 E2PROM part
E2PROM completes the storage of process numbers and real-time data. This article uses the AT24C64 chip produced by ATMEL, which has a storage size of 8192 bytes; it can always be read and written; it can be erased and written at least 1 million times; and it has a data retention period of at least 100 years. It supports the I2C bus, and the LPC2119 integrates an I2C bus interface, so that hardware communication can be realized. The schematic diagram is shown in Figure 4.
4. Software system design
This system has many complex functions. Considering the real-time requirements of industrial control, it uses the uC/OS-II embedded operating system with high real-time performance. μC/OS-II is a real-time multi-tasking kernel that uses a preemptive scheduling method based on fixed priorities. It is solidifiable, customizable, and has high stability and reliability. In addition, the distinctive feature of μC/OS-II is that the source code is open, which is easy to transplant and maintain [3]. The task sequence of this system is as follows:
Task 1: Establish Task 2, Task 3 and Task 4;
Task 2: Receive signals sent by the host computer through the CAN interface, including pre-set parameter values; (sent regularly by the host computer)
Task 3: Perform A/D conversion, PID regulation, and D/A conversion; these three are closely linked: A/D conversion converts the input analog signal into digital quantity and serves as the input of PID regulation, while the output of PID regulation is output to the input of the thyristor through D/A conversion, thereby changing the output of the module;
Task 4: E2PROM completes the storage of process number and real-time data, and the CAN interface transmits the output parameter value to the host computer for display;
Fast interrupt: When receiving the start or end signal from the host computer, the PWM fast interrupt generates the corresponding number of pulses and stop signals respectively. The response speed requirement here is high. If it is not timely, the module may burn out, so fast interrupt must be used.
5. Conclusion
This system has been successfully developed and applied to actual products with good results. This system combines the LPC2119 processor and the uC/OS-II embedded operating system into the control system, and uses the CAN field bus for communication, which greatly improves the high stability and reliability of the system; the constant voltage or constant current working mode can be selected according to the settings of the host computer; the voltage adjustment range can be set to 0~1000 volts (different models have different maximum values); the pulse frequency is adjustable from 20Hz to 10KHz; the duty cycle is adjustable between 5% and 95%. This system is easy to maintain and expand, enough to meet the needs of the current micro-arc oxidation power supply control system!
Previous article:Design of high-resolution infrared touch screen based on ARM7 and VC platform
Next article:Chinese LCD Display Technology Based on ARM7 Microprocessor
Recommended ReadingLatest update time:2024-11-16 22:39
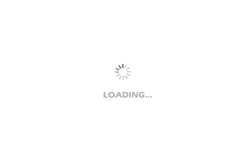
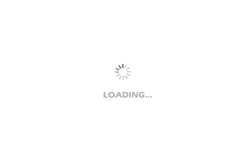
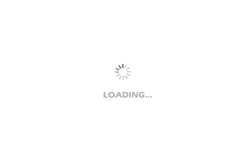
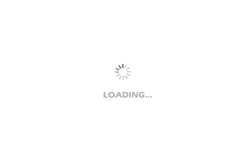
Professor at Beihang University, dedicated to promoting microcontrollers and embedded systems for over 20 years.
- Innolux's intelligent steer-by-wire solution makes cars smarter and safer
- 8051 MCU - Parity Check
- How to efficiently balance the sensitivity of tactile sensing interfaces
- What should I do if the servo motor shakes? What causes the servo motor to shake quickly?
- 【Brushless Motor】Analysis of three-phase BLDC motor and sharing of two popular development boards
- Midea Industrial Technology's subsidiaries Clou Electronics and Hekang New Energy jointly appeared at the Munich Battery Energy Storage Exhibition and Solar Energy Exhibition
- Guoxin Sichen | Application of ferroelectric memory PB85RS2MC in power battery management, with a capacity of 2M
- Analysis of common faults of frequency converter
- In a head-on competition with Qualcomm, what kind of cockpit products has Intel come up with?
- Dalian Rongke's all-vanadium liquid flow battery energy storage equipment industrialization project has entered the sprint stage before production
- Allegro MicroSystems Introduces Advanced Magnetic and Inductive Position Sensing Solutions at Electronica 2024
- Car key in the left hand, liveness detection radar in the right hand, UWB is imperative for cars!
- After a decade of rapid development, domestic CIS has entered the market
- Aegis Dagger Battery + Thor EM-i Super Hybrid, Geely New Energy has thrown out two "king bombs"
- A brief discussion on functional safety - fault, error, and failure
- In the smart car 2.0 cycle, these core industry chains are facing major opportunities!
- The United States and Japan are developing new batteries. CATL faces challenges? How should China's new energy battery industry respond?
- Murata launches high-precision 6-axis inertial sensor for automobiles
- Ford patents pre-charge alarm to help save costs and respond to emergencies
- New real-time microcontroller system from Texas Instruments enables smarter processing in automotive and industrial applications
- May 19 live broadcast review: MPS, Nexperia and Tektronix gathered to discuss the key points of new energy power design
- R329 Development Board Application - Operation Image (2)
- IOT desk lamp software design
- A 5G base station is worth this price. Do you think it is expensive?
- Thank you for being here-Community Activities
- One week evaluation information, delivered on time~
- Tips for selecting brushless DC motor driver chips
- Communication between EMIF and FPGA of TMS320C6455
- 【GD32L233C-START Review】12. Hardware IIC drive OLED
- EEWORLD University Hall----Live Replay: TI 60G mmWave Sensor Overview and Application Introduction