In the current embedded application development process, C language has become the best choice for most occasions. In this way, the main function seems to be the natural starting point - because C programs often start execution from the main function. But a question that is often overlooked is: how does the microcontroller (single-chip microcomputer) find and execute the main function after it is powered on? Obviously, the microcontroller cannot locate the entry address of the main function from the hardware, because after using C language as the development language, the address of the variable/function is automatically allocated by the compiler during compilation, so the entry address of the main function is no longer absolutely unchanged in the internal storage space of the microcontroller. I believe that readers can all answer this question. The answers may be similar, but there is definitely a key word, called "startup file", which is described in English as "Bootloader".
Regardless of performance, structure, or price, every microcontroller (processor) must have a startup file. The role of the startup file is to execute the work that must be done during the period from "reset" to "starting to execute the main function" (called the startup process). The most common microcontrollers such as 51, AVR or MSP430 also have corresponding startup files, but the development environment often automatically and completely provides this startup file, so developers do not need to intervene in the startup process. They only need to start designing the application from the main function.
Turning to the topic of STM32 microcontrollers, whether it is keiluvision4 or IAR EWARM development environment, ST provides ready-made directly available startup files, and program developers can directly reference the startup files and directly develop C applications. This can greatly reduce the difficulty of developers jumping from other microcontroller platforms to the STM32 platform, and also reduce the difficulty of adapting to STM32 microcontrollers (for the last generation of ARM's leading star ARM9, the startup file is often the first difficult but insurmountable hurdle).
Compared with the mainstream ARM7/ARM9 core architecture of the previous generation of ARM, the startup mode of the new generation of Cortex core architecture has changed significantly. After the controller of the ARM7/ARM9 core is reset, the CPU will fetch the first instruction from the absolute address 0x000000 of the storage space to execute the reset interrupt service program to start, that is, the starting address after reset is fixed to 0x000000 (PC = 0x000000) and the location of the interrupt vector table is not fixed. The Cortex-M3 core is just the opposite, there are 3 situations:
1. The interrupt vector table can be located in the SRAM area through the boot pin setting, that is, the starting address is 0x2000000, and the PC pointer is located at 0x2000000 after reset;
2. The interrupt vector table can be located in the FLASH area through the boot pin setting, that is, the starting address is 0x8000000, and the PC pointer is located at 0x8000000 after reset;
3. The interrupt vector table can be located in the built-in Bootloader area through the boot pin setting. This article does not discuss this situation;
The Cortex-M3 core stipulates that the starting address must store the stack top pointer, and the second address must store the reset interrupt entry vector address. In this way, after the Cortex-M3 core is reset, it will automatically fetch the reset interrupt entry vector from the next 32-bit space of the starting address and jump to execute the reset interrupt service program. Compared with the ARM7/ARM9 core, the Cortex-M3 core has a fixed interrupt vector table location and a variable starting address.
With the above preparations, the following is a brief and comprehensive analysis of the STM32 startup process using the startup file "stm32f10x_vector.s" provided by the STM32 2.02 firmware library as a template.
Program List 1:
; File "stm32f10x_vector.s" with comments as line numbers
DATA_IN_ExtSRAM EQU 0 ;1
Stack_Size EQU 0x00000400 ;2
AREA STACK, NOINIT, READWRITE, ALIGN = 3;3
Stack_Mem SPACE Stack_Size ;4
__initial_sp ;5
Heap_Size EQU 0x00000400 ;6
AREA HEAP, NOINIT, READWRITE, ALIGN = 3;7
__heap_base ;8
Heap_Mem SPACE Heap_Size ;9
__heap_limit ;10
THUMB ;11
PRESERVE8 ;12
IMPORT NMIException ;13
IMPORT HardFaultException ;14
IMPORT MemManageException ;15
IMPORT BusFaultException ;16
IMPORT UsageFaultException ;17
IMPORT SVCHandler ;18
IMPORT DebugMonitor ;19
IMPORT PendSVC ;20
IMPORT SysTickHandler ;21
IMPORT WWDG_IRQHandler ;22
IMPORT PVD_IRQHandler ;23
IMPORT TAMPER_IRQHandler ;24
IMPORT RTC_IRQHandler ;25
IMPORT FLASH_IRQHandler ;26
IMPORT RCC_IRQHandler ;27
IMPORT EXTI0_IRQHandler ;28
IMPORT EXTI1_IRQHandler ;29
IMPORT EXTI2_IRQHandler ;30
IMPORT EXTI3_IRQHandler ;31
IMPORT EXTI4_IRQHandler ;32
IMPORT DMA1_Channel1_IRQHandler ;33
IMPORT DMA1_Channel2_IRQHandler ;34
IMPORT DMA1_Channel3_IRQHandler ;35
IMPORT DMA1_Channel4_IRQHandler ;36
IMPORT DMA1_Channel5_IRQHandler ;37
IMPORT DMA1_Channel6_IRQHandler ;38
IMPORT DMA1_Channel7_IRQHandler ;39
IMPORT ADC1_2_IRQHandler ;40
IMPORT USB_HP_CAN_TX_IRQHandler ;41
IMPORT USB_LP_CAN_RX0_IRQHandler ;42
IMPORT CAN_RX1_IRQHandler ;43
IMPORT CAN_SCE_IRQHandler ;44
IMPORT EXTI9_5_IRQHandler ;45
IMPORT TIM1_BRK_IRQHandler ;46
IMPORT TIM1_UP_IRQHandler ;47
IMPORT TIM1_TRG_COM_IRQHandler ;48
IMPORT TIM1_CC_IRQHandler ;49
IMPORT TIM2_IRQHandler ;50
IMPORT TIM3_IRQHandler ;51
IMPORT TIM4_IRQHandler ;52
IMPORT I2C1_EV_IRQHandler;53
IMPORT I2C1_ER_IRQHandler;54
IMPORT I2C2_EV_IRQHandler;55
IMPORT I2C2_ER_IRQHandler;56
IMPORT SPI1_IRQHandler ;57
IMPORT SPI2_IRQHandler ;58
IMPORT USART1_IRQHandler ;59
IMPORT USART2_IRQHandler ;60
IMPORT USART3_IRQHandler ;61
IMPORT EXTI15_10_IRQHandler ;62
IMPORT RTCAlarm_IRQHandler ;63
IMPORT USBWakeUp_IRQHandler ;64
IMPORT TIM8_BRK_IRQHandler ;65
IMPORT TIM8_UP_IRQHandler ;66
IMPORT TIM8_TRG_COM_IRQHandler ;67
IMPORT TIM8_CC_IRQHandler ;68
IMPORT ADC3_IRQHandler ;69
IMPORT FSMC_IRQHandler ;70
IMPORT SDIO_IRQHandler ;71
IMPORT TIM5_IRQHandler ;72
IMPORT SPI3_IRQHandler ;73
IMPORT UART4_IRQHandler; 74
IMPORT UART5_IRQHandler ;75
IMPORT TIM6_IRQHandler;76
IMPORT TIM7_IRQHandler ;77
IMPORT DMA2_Channel1_IRQHandler ;78
IMPORT DMA2_Channel2_IRQHandler ;79
IMPORT DMA2_Channel3_IRQHandler ;80
IMPORT DMA2_Channel4_5_IRQHandler ;81
AREA RESET, DATA, READONLY ;82
EXPORT __Vectors ;83
__Vectors ;84
DCD __initial_sp ;85
DCD Reset_Handler ;86
DCD NMIException ;87
DCD HardFaultException ;88
DCD MemManageException ;89
DCD BusFaultException ;90
DCD UsageFaultException ;91
DCD 0 ;92
DCD 0 ;93
DCD 0 ;94
DCD 0 ;95
DCD SVCHandler ;96
DCD DebugMonitor ;97
DCD 0 ;98
DCD PendSVC ;99
DCD SysTickHandler ;100
DCD WWDG_IRQHandler ;101
DCD PVD_IRQHandler ;102
DCD TAMPER_IRQHandler ;103
DCD RTC_IRQHandler ;104
DCD FLASH_IRQHandler ;105
DCD RCC_IRQHandler ;106
DCD EXTI0_IRQHandler ;107
DCD EXTI1_IRQHandler ;108
DCD EXTI2_IRQHandler ;109
DCD EXTI3_IRQHandler ;110
DCD EXTI4_IRQHandler ;111
DCD DMA1_Channel1_IRQHandler ;112
DCD DMA1_Channel2_IRQHandler ;113
DCD DMA1_Channel3_IRQHandler ;114
DCD DMA1_Channel4_IRQHandler ;115
DCD DMA1_Channel5_IRQHandler ;116
DCD DMA1_Channel6_IRQHandler ;117
DCD DMA1_Channel7_IRQHandler ;118
DCD ADC1_2_IRQHandler ;119
DCD USB_HP_CAN_TX_IRQHandler ;120
DCD USB_LP_CAN_RX0_IRQHandler ;121
DCD CAN_RX1_IRQHandler ;122
DCD CAN_SCE_IRQHandler ;123
DCD EXTI9_5_IRQHandler ;124
DCD TIM1_BRK_IRQHandler ;125
DCD TIM1_UP_IRQHandler; 126
DCD TIM1_TRG_COM_IRQHandler ;127
DCD TIM1_CC_IRQHandler ;128
DCD TIM2_IRQHandler ;129
DCD TIM3_IRQHandler ;130
DCD TIM4_IRQHandler ;131
DCD I2C1_EV_IRQHandler;132
DCD I2C1_ER_IRQHandler;133
DCD I2C2_EV_IRQHandler;134
DCD I2C2_ER_IRQHandler;135
DCD SPI1_IRQHandler ;136
DCD SPI2_IRQHandler ;137
DCD USART1_IRQHandler ;138
DCD USART2_IRQHandler ;139
DCD USART3_IRQHandler ;140
DCD EXTI15_10_IRQHandler ;141
DCD RTCAlarm_IRQHandler ;142
DCD USBWakeUp_IRQHandler ;143
DCD TIM8_BRK_IRQHandler ;144
DCD TIM8_UP_IRQHandler; 145
DCD TIM8_TRG_COM_IRQHandler ;146
DCD TIM8_CC_IRQHandler ;147
DCD ADC3_IRQHandler ;148
DCD FSMC_IRQHandler ;149
DCD SDIO_IRQHandler ;150
DCD TIM5_IRQHandler ;151
DCD SPI3_IRQHandler ;152
DCD UART4_IRQHandler ;153
DCD UART5_IRQHandler ;154
DCD TIM6_IRQHandler ;155
DCD TIM7_IRQHandler ;156
DCD DMA2_Channel1_IRQHandler ;157
DCD DMA2_Channel2_IRQHandler ;158
DCD DMA2_Channel3_IRQHandler ;159
DCD DMA2_Channel4_5_IRQHandler ;160
AREA |.text|, CODE, READONLY ;161
Reset_Handler PROC ;162
EXPORT Reset_Handler ;163
IF DATA_IN_ExtSRAM == 1 ;164
LDR R0,= 0x00000114 ;165
LDR R1,= 0x40021014 ;166
STR R0,[R1] ;167
LDR R0,= 0x000001E0 ;168
LDR R1,= 0x40021018 ;169
STR R0,[R1] ;170
LDR R0,= 0x44BB44BB ;171
LDR R1,= 0x40011400 ;172
STR R0,[R1] ;173
LDR R0,= 0xBBBBBBBB ;174
LDR R1,= 0x40011404 ;175
STR R0,[R1] ;176
LDR R0,= 0xB44444BB ;177
LDR R1,= 0x40011800 ;178
STR R0,[R1] ;179
LDR R0,= 0xBBBBBBBB ;180
LDR R1,= 0x40011804 ;181
STR R0,[R1] ;182
LDR R0,= 0x44BBBBBB ;183
LDR R1,= 0x40011C00 ;184
STR R0,[R1] ;185
LDR R0,= 0xBBBB4444 ;186
LDR R1,= 0x40011C04 ;187
STR R0,[R1] ;188
LDR R0,= 0x44BBBBBB ;189
LDR R1,= 0x40012000 ;190
STR R0,[R1] ;191
LDR R0,= 0x44444B44 ;192
LDR R1,= 0x40012004 ;193
STR R0,[R1] ;194
LDR R0,= 0x00001011 ;195
LDR R1,= 0xA0000010 ;196
STR R0,[R1] ;197
LDR R0,= 0x00000200 ;198
LDR R1,= 0xA0000014 ;199
STR R0,[R1] ;200
ENDIF ;201
IMPORT __main ;202
LDR R0, =__main; 203
BX R0 ;204
ENDP ;205
ALIGN ;206
IF :DEF:__MICROLIB ;207
EXPORT __initial_sp ;208
EXPORT __heap_base ;209
EXPORT __heap_limit ;210
ELSE; 211
IMPORT __use_two_region_memory ;212
EXPORT __user_initial_stackheap ;213
__user_initial_stackheap ;214
LDR R0, = Heap_Mem; 215
LDR R1, = (Stack_Mem + Stack_Size) ;216
LDR R2, = (Heap_Mem + Heap_Size) ;217
LDR R3, = Stack_Mem; 218
BX LR ;219
ALIGN ;220
ENDIF ;221
END ;222
ENDIF ;223
END ;224
As shown in Listing 1, the STM32 startup code has a total of 224 lines, written in assembly language. The main reason for this will be explained below. Let's start with the first line:
? Line 1: Defines whether to use external SRAM, 1 means use, 0 means not use. This line is equivalent to the following if expressed in C language:
#define DATA_IN_ExtSRAM 0
? Line 2: Define the stack space size as 0x00000400 bytes, or 1Kbyte. This line is also equivalent to:
#define Stack_Size 0x00000400
? Line 3: Pseudo-instruction AREA, indicating
? Line 4: Allocate a memory space of size Stack_Size as the stack.
? Line 5: Label __initial_sp indicates the top address of the stack space.
? Line 6: Define the heap space size as 0x00000400 bytes, also 1Kbyte.
? Line 7: Pseudo-instruction AREA, indicating
? Line 8: Label __heap_base indicates the starting address of the heap space.
? Line 9: Open up a memory space of size Heap_Size as a heap.
? Line 10: Label __heap_limit indicates the end address of the heap space.
? Line 11: Tells the compiler to use the THUMB instruction set.
? Line 12: Tells the compiler to align to 8 bytes.
? Lines 13-81: IMPORT directive, indicating that subsequent symbols are defined in external files (similar to global variable declarations in C language), and these symbols may be used below.
? Line 82: Define the read-only data segment, which is actually in the CODE area (assuming that STM32 is started from FLASH, the starting address of this interrupt vector table is 0x8000000)
? Line 83: Declare the label __Vectors as a global label so that external files can use this label.
? Line 84: Label __Vectors indicates the entry address of the interrupt vector table.
? Lines 85-160: Create interrupt vector table.
? Line 161:
? Line 162: Reset interrupt service routine, the PROC…ENDP structure indicates the beginning and end of the program.
? Line 163: Declare the reset interrupt vector Reset_Handler as a global attribute so that external files can call this reset interrupt service.
? Line 164: IF…ENDIF is a pre-compiled structure that determines whether to use external SRAM, which has been defined as "not used" in line 1.
? Lines 165-201: This part of the code is used to set up the FSMC bus to support SRAM. Since external SRAM is not used, this part of the code will not be compiled.
? Line 202: Declare the __main label.
? Lines 203-204: Jump to __main address for execution.
? Line 207: IF…ELSE…ENDIF structure, determines whether to use DEF:__MICROLIB (not used here).
? Lines 208-210: If DEF:__MICROLIB is used, __initial_sp, __heap_base, __heap_limit, i.e. the top address of the stack and the start and end addresses of the heap, will be assigned global attributes so that they can be used by external programs.
? Line 212: Define the global label __use_two_region_memory.
? Line 213: Declare the global label __user_initial_stackheap so that external programs can also call this label.
? Line 214: Label __user_initial_stackheap indicates the entry of the user stack initializer.
? Lines 215-218: Save the stack top pointer and stack size, stack start address and stack size to R0, R1, R2, R3 registers respectively.
? Line 224: The program ends.
The above is a complete analysis of the STM32 startup code. Next, I will explain a few small details:
1. AREA instruction: pseudo instruction, used to define code segment or data segment, followed by attribute label. One of the more important labels is "READONLY" or "READWRITE", where "READONLY" means that the segment has read-only attribute. In connection with the internal storage medium of STM32, it can be seen that the segment with read-only attribute is saved in the FLASH area, that is, after the address 0x8000000. "READONLY" means that the segment has "readable and writable" attribute, and it can be seen that the "readable and writable" segment is saved in the SRAM area, that is, after the address 0x2000000. From the 3rd and 7th lines of code, it can be seen that the stack segment is located in the SRAM space. From the 82nd line, it can be seen that the interrupt vector table is placed in the FLASH area, and this is also the first data to be placed in the FLASH area in the entire startup code. Therefore, we can get an important piece of information: the address 0x8000000 is the top address of the stack __initial_sp, and the address 0x8000004 is the reset interrupt vector Reset_Handler (STM32 uses a 32-bit bus, so the storage space is 4-byte aligned).
2. DCD instruction: It is used to open up a space, which is equivalent to the address symbol "&" in C language. Therefore, the interrupt vector table established from line 84 is similar to defining a pointer array in C language, each member of which is a function pointer, pointing to each interrupt service function.
3. Label: The word "label" is used in many places in the previous text. Label is mainly used to indicate a certain position in a piece of memory space, which is equivalent to the concept of "address" in C language. Address only indicates a position in the storage space. From the perspective of C language, there is no essential difference between the address of a variable, the address of an array or the entry address of a function.
4. The __main label in line 202 does not indicate the entry address of the main function in the C program, so line 204 does not jump to the main function to start executing the C program. The __main label indicates the entry address of an initialization subroutine __main in the C/C++ standard real-time library function. One of the main functions of this program is to initialize the stack (for Listing 1, it jumps to the __user_initial_stackheap label to initialize the stack), initialize the image file, and finally jump to the main function in the C program. This explains why all C programs must have a main function as the starting point of the program - because this is stipulated by the C/C++ standard real-time library - and it cannot be changed because the C/C++ standard real-time library does not develop source code to the outside world. Therefore, in fact, under the premise of being visible to the user, the program jumps to the main function in the .c file after line 204 and starts executing the C program.
At this point, we can summarize the startup file and startup process of STM32. First, define the size of the stack and heap, and establish an interrupt vector table at the beginning of the code area. The first table entry is the stack top address, and the second table entry is the reset interrupt service entry address. Then jump to the __main function of the C/C++ standard real-time library in the reset interrupt service program. After completing the initialization of the user stack, jump to the main function in the .c file to start executing the C program. Assuming that STM32 is set to start from the internal FLASH (which is also the most common case), the starting position of the interrupt vector table is 0x8000000, then the stack top address is stored at 0x8000000, and the reset interrupt service entry address is stored at 0x8000004. When STM32 encounters a reset signal, it takes out the reset interrupt service entry address from 0x80000004, then executes the reset interrupt service program, then jumps to the __main function, and finally enters the mian function to enter the world of C.
Previous article:The difference between STM32 startup file selection
Next article:STM32 IAP APP startup process
Recommended ReadingLatest update time:2024-11-16 14:56
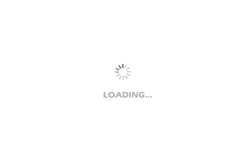
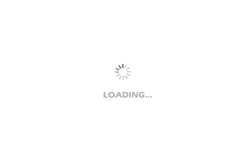
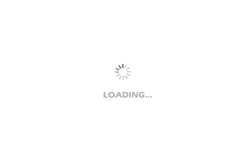
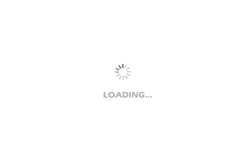
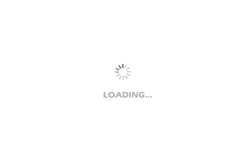
- Popular Resources
- Popular amplifiers
Professor at Beihang University, dedicated to promoting microcontrollers and embedded systems for over 20 years.
- Innolux's intelligent steer-by-wire solution makes cars smarter and safer
- 8051 MCU - Parity Check
- How to efficiently balance the sensitivity of tactile sensing interfaces
- What should I do if the servo motor shakes? What causes the servo motor to shake quickly?
- 【Brushless Motor】Analysis of three-phase BLDC motor and sharing of two popular development boards
- Midea Industrial Technology's subsidiaries Clou Electronics and Hekang New Energy jointly appeared at the Munich Battery Energy Storage Exhibition and Solar Energy Exhibition
- Guoxin Sichen | Application of ferroelectric memory PB85RS2MC in power battery management, with a capacity of 2M
- Analysis of common faults of frequency converter
- In a head-on competition with Qualcomm, what kind of cockpit products has Intel come up with?
- Dalian Rongke's all-vanadium liquid flow battery energy storage equipment industrialization project has entered the sprint stage before production
- Allegro MicroSystems Introduces Advanced Magnetic and Inductive Position Sensing Solutions at Electronica 2024
- Car key in the left hand, liveness detection radar in the right hand, UWB is imperative for cars!
- After a decade of rapid development, domestic CIS has entered the market
- Aegis Dagger Battery + Thor EM-i Super Hybrid, Geely New Energy has thrown out two "king bombs"
- A brief discussion on functional safety - fault, error, and failure
- In the smart car 2.0 cycle, these core industry chains are facing major opportunities!
- The United States and Japan are developing new batteries. CATL faces challenges? How should China's new energy battery industry respond?
- Murata launches high-precision 6-axis inertial sensor for automobiles
- Ford patents pre-charge alarm to help save costs and respond to emergencies
- New real-time microcontroller system from Texas Instruments enables smarter processing in automotive and industrial applications
- TecoCore Co., Ltd. is looking for SSD firmware development talents to join
- Some unclear points about self-oscillation
- Responsibility is heavier than Mount Tai! Talking about the safety requirements of China's high-speed rail signaling
- Write EEPROM, write FLASH experience record
- Commonly used algorithms for drones - Kalman filter (Part 9)
- Reset time problem
- Why does DLL not found error appear when running VB with Ginkgo?
- The problem of STM8L151k4t6 with programmed code being damaged by soldering?
- DSP28335 external interrupt configuration process
- Circuit PCB Design