1.1 The design of the microcontroller should choose a lower operating frequency according to customer needs
First, let me introduce the advantages of doing this: using a low crystal oscillator and bus frequency allows us to choose a smaller microcontroller to meet the timing requirements, so that the operating current of the microcontroller can become lower, and most importantly, the current peak from VDD to VSS will be smaller.
Of course, we need to make a compromise here, because the customer's requirements may be compatible and platform-based (the current development trend of automotive electronics is platform-based). Choosing a higher operating frequency can be compatible with more platforms and facilitate future upgrades and expansions. Therefore, we need to choose a lower acceptable operating frequency.
2 Appropriate output drive capability
Given load specifications, rise and fall times, selecting the appropriate output rise time, and minimizing output and internal driver peak currents are among the most important design considerations for reducing EMI. Mismatched drive capabilities or failure to control the output voltage change rate may result in impedance mismatch, faster switching edges, overshoot and undershoot of the output signal, or power and ground bounce noise.
2.1 To design the output driver of the microcontroller, first determine the load required by the module, the rise and fall time, and the output current. Based on the above information, the driving capability and the voltage slew rate are controlled. Only in this way can the module requirements and EMC requirements be met.
When the driver capability is higher than the actual charging speed required by the load, a higher edge rate will be generated, which has two disadvantages:
1. The harmonic components of the signal increase.
2. Together with load capacitance and parasitic internal bonding lines, IC packaging, and PCB inductance, it will cause signal overshoot and undershoot.
Selecting the appropriate di/dt switching characteristics can be achieved by carefully selecting the size of the drive capability and controlling the voltage slew rate. The best option is to use a constant voltage slew rate output buffer that is independent of the load. The voltage slew rate of the same pre-driver output can be reduced (i.e., the rise and fall times can be increased), but the corresponding propagation delay will increase and we need to control the total switching time).
2.2 Use the driving capability of the programmable output port of the microcontroller to meet the actual load requirements of the module.
The simplest driver for a programmable output port is a pair of drivers connected in parallel. Their MOS Rdson is different and their output current capabilities are also different. We can choose different modes during testing and actual use. In fact, current microcontrollers generally have at least two modes to choose from, and some even have three (strong, medium, weak)
2.3 When the timing constraints have enough margin, slow down the edge of the internal clock drive by reducing the output capability.
An important consideration for reducing the peak current and di/dt of synchronous switching is to reduce the internal clock drive capability (actually the amplification factor, the through current is highly correlated with it). Reducing the current at the clock edge will significantly improve EMI. Of course, the disadvantage of doing so is that the average current of the microcontroller may increase due to the longer turn-on time of the clock and load. A compromise needs to be made between fast edges and relatively high peak currents and longer current pulses with slower edges.
2.4 The internal drive (inverter) of the crystal oscillator should not exceed the actual demand.
This problem has actually been discussed before. When the gain is too large, it will cause greater interference.
3 Designing a driver with minimum shoot-through current
3.1 Clock, bus and output drivers should minimize conventional current consumption
The through current [overlap current, short-circuit current] is the current from the power supply to the ground when the PMOS and NMOS are turned on at the same time during the switching process of the microcontroller. The through current directly affects EMI and power consumption.
This content is actually inside the microcontroller, the clock, bus and output driver. The way to eliminate or reduce the through current is to try to turn off a FET first and then turn on a FET. When the current is large, additional pre-drive circuits or voltage slew rates are required.
Previous article:How to understand and distinguish between single chip microcomputer and PLC
Next article:Program to drive ST7565P LCD screen based on SPI of ATMEGA8515
Recommended ReadingLatest update time:2024-11-17 07:51
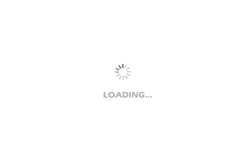
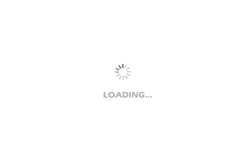
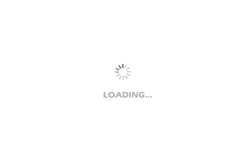
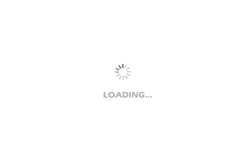
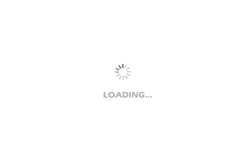
- Popular Resources
- Popular amplifiers
-
Wireless Sensor Network Technology and Applications (Edited by Mou Si, Yin Hong, and Su Xing)
-
Modern Electronic Technology Training Course (Edited by Yao Youfeng)
-
Modern arc welding power supply and its control
-
Small AC Servo Motor Control Circuit Design (by Masaru Ishijima; translated by Xue Liang and Zhu Jianjun, by Masaru Ishijima, Xue Liang, and Zhu Jianjun)
Professor at Beihang University, dedicated to promoting microcontrollers and embedded systems for over 20 years.
- Innolux's intelligent steer-by-wire solution makes cars smarter and safer
- 8051 MCU - Parity Check
- How to efficiently balance the sensitivity of tactile sensing interfaces
- What should I do if the servo motor shakes? What causes the servo motor to shake quickly?
- 【Brushless Motor】Analysis of three-phase BLDC motor and sharing of two popular development boards
- Midea Industrial Technology's subsidiaries Clou Electronics and Hekang New Energy jointly appeared at the Munich Battery Energy Storage Exhibition and Solar Energy Exhibition
- Guoxin Sichen | Application of ferroelectric memory PB85RS2MC in power battery management, with a capacity of 2M
- Analysis of common faults of frequency converter
- In a head-on competition with Qualcomm, what kind of cockpit products has Intel come up with?
- Dalian Rongke's all-vanadium liquid flow battery energy storage equipment industrialization project has entered the sprint stage before production
- Allegro MicroSystems Introduces Advanced Magnetic and Inductive Position Sensing Solutions at Electronica 2024
- Car key in the left hand, liveness detection radar in the right hand, UWB is imperative for cars!
- After a decade of rapid development, domestic CIS has entered the market
- Aegis Dagger Battery + Thor EM-i Super Hybrid, Geely New Energy has thrown out two "king bombs"
- A brief discussion on functional safety - fault, error, and failure
- In the smart car 2.0 cycle, these core industry chains are facing major opportunities!
- Rambus Launches Industry's First HBM 4 Controller IP: What Are the Technical Details Behind It?
- The United States and Japan are developing new batteries. CATL faces challenges? How should China's new energy battery industry respond?
- Murata launches high-precision 6-axis inertial sensor for automobiles
- Ford patents pre-charge alarm to help save costs and respond to emergencies
- KEYENCE Fiber Optic Sensor Disassembly
- DSP28335 burning program, besides CCS software, is there any third-party program download software tool? ?
- What do the front-line people think: In 2022, the local IC industry will face a "big test"
- 【Awarded】Rewarded Survey——We want you! What does a good reference design website look like?
- Foreign digital electronics textbooks don’t talk about competition and risk-taking?
- Global UWB device shipments to reach 317 million
- Share a STLINK V2_1 PCB project, which can be directly sampled and produced
- Is there anyone familiar with ST's BLUENRG-LP? I would like to ask a question
- STM32 Global Unique ID Reading Method
- Qualcomm wins injunction, Chinese court bans sale of several iPhones