Pyroelectric infrared thermometer is a new type of infrared thermometer that works by using the pyroelectric effect. Compared with other traditional thermometers, it has the advantages of no need for refrigeration, ability to work at room temperature and wide spectral response, and has high sensitivity, fast response speed and strong anti-interference ability [2]. This paper uses pyroelectric detectors and combines the advantages of low power consumption, high performance and low cost of 32-bit ARM core processor to design an infrared thermometer with ARM microcontroller STM32 as the core.
1 Principle of infrared temperature measurement
All objects with a temperature higher than absolute zero are constantly emitting infrared radiation energy to the surrounding space. The size of the radiation energy and the distribution of its wavelength are closely related to its surface temperature. According to Wien's displacement law, for an object with a temperature of Tc, the ratio Z of the monochromatic radiation power corresponding to wavelengths λ1 and λ2 is expressed by the following formula: 2 Overall composition

Since this system needs to measure the surface temperature of a high-temperature object, a colorimetric temperature measurement scheme is adopted, that is, the ratio of the brightness of monochromatic radiation of the same object under two wavelengths changes with temperature as its temperature measurement principle. The structure of the infrared thermometer is shown in Figure 1, which mainly consists of an optical system, an infrared detector, signal processing and display output. The optical system completes the collection of light and determines the size of the field of view. The infrared detector is used to convert the infrared energy focused on the detector into an electrical signal, which is amplified, filtered, and then sent to the microcontroller for analog-to-digital conversion and signal processing. Finally, it is converted into the temperature of the measured target after temperature compensation and calibration and displayed on the LCD. 2.1 Microcontroller STM32 The STM32 series is based on the ARM Cortex-M3 core designed specifically for embedded applications that require high performance, low cost, and low power consumption. It also has a 512 KB high-speed Flash memory, which integrates 3 12-bit ADCs, 1 2-channel 12-bit DAC, and up to 11 timers, including two 16-bit PWM advanced control timers with dead zone control and emergency brake for motor control. This controller can be used to quickly perform data processing tasks such as digital filtering and temperature compensation [3]. 2.2 Optical system This part adopts a typical Newton system in the reflective optical system. Compared with the transmission and transmission-reflection combined systems, this system has less light energy loss, no chromatic aberration, simple structure and easy processing. 2.3 Detector and chopper design This system uses a pyroelectric sensor. At present, the core components of pyroelectric sensors, pyroelectric materials, mainly include lead zirconate titanate PZT, barium strontium titanate (BST) and lead tantalate scandate (PST). Here, BST film is selected. Compared with pyroelectric materials, pyroelectric film has the advantages of small size, light weight, high resolution, fast response and compatibility with microelectronics technology. Because the received radiation is very weak and the DC amplifier has zero drift, the radiation energy must be modulated before the radiation signal reaches the sensor to convert it into an alternating signal. The fan-shaped modulation disk used in this system drives the stepper motor with a square wave signal with a duty cycle of 50% generated by the pulse width modulator output port PA8 of STM32. 2.4 Signal conditioning The signal amplification circuit is divided into a preamplifier circuit and a post-amplifier circuit. In particular, the noise coefficient of the preamplifier plays a decisive role in the noise of the entire detection system. The amplifier used in this design is OP07 produced by MAXIM, USA. OP07 is an ultra-low offset operational amplifier (generally about 10 μV), with a common-mode input impedance of up to 200 MΩ and an output impedance of only 60 Ω, which can meet the needs of system design. Since the input signal range of the A/D converter of STM32 is 0-3.3 V, it is necessary to select a suitable amplification factor so that the corresponding output voltage is within 3.3 V when the highest temperature is measured. When the signal is amplified by the amplifier, its broadband noise is large. Therefore, a bandpass filter is added between the preamplifier and the post-amplifier to suppress the broadband noise and improve the signal-to-noise ratio. However, the bandwidth of the bandpass filter should be wider, otherwise when the temperature changes, the signal spectrum will easily deviate from the passband of the filter and cause measurement errors [4]. According to the needs of this system, the system uses a second-order Butterworth bandpass filter, whose center frequency is designed to be 100 Hz and the bandwidth is about 20 Hz. [page] 2.5 Detection circuit The electronic switch detector is used in this design. Compared with the analog multiplier detector, it has the advantages of simple circuit, higher accuracy, fast operation speed and no nonlinearity. The specific circuit is shown in Figure 2. As can be seen from Figure 2, the input signal V4 is the output signal of the sensor amplified by the main amplifier, V5 is the pulse signal sent by the PWM port of STM32, which is used for chopping modulation after phase shifting; V6 is the inverting voltage of V5, which is achieved by adding an inverter. In the figure, R27=R28=R29=R31=R32=0.5 R33, when V5 is high level, Q2 is turned on, and the in-phase end of OP07 is grounded; when V5 is low level, Q2 is turned off, the inverting end of OP07 is grounded, and the output voltage is 0.5. After the above circuit, the signal is still mixed with noise, which is mainly eliminated by low-pass filters. 2.6 Temperature compensation unit Since the system is affected by the ambient temperature, it is necessary to perform temperature compensation on the system. This system uses the integrated temperature sensor AD592, which is a high-performance integrated temperature sensor from AD Company in the United States. It has the advantages of high accuracy, small nonlinear error, and wide input range. The adjustable resistor R2 in the system is used to calibrate the output voltage V2. When the ambient temperature is 0, the output voltage V2 is 0; R5 is used to calibrate the temperature coefficient. After calibration, the output voltage V2 is the product of the temperature coefficient and the ambient temperature, and is connected to the ADC port PC0 of the STM32. 2.7 Analog/digital conversion unit The STM32 has three built-in 12-bit analog/digital converters (ADCs). Each ADC has up to 21 external channels and can realize single or scan conversion. In the scan mode, it automatically performs conversion on a selected set of analog inputs [5]. The measurement range of its A/D converter is 0~5 V. Because the operating frequency of this system is 150 Hz and the sampling is 10 times per cycle, the conversion rate of ADC is set to 1.5 kHz. The system uses PC1 port to sample the voltage. 2.8 Input and output unit STM32 has up to 80 multifunctional bidirectional I/O ports, so 5 independent keys can be used when designing the keyboard, namely power on, Celsius and Fahrenheit temperature conversion, emissivity correction and backlight display keys. The LCD display uses character LCD NT7502 display. The microprocessor sends data/commands to NT7502 through an 8-bit serial interface, and uses GPIO to realize the LCD read and write control timing and data signal to complete the operation control of the LCD. At the same time, it can be used to display the value of the ambient temperature. The LCD display interface circuit is shown in Figure 3. 3 System software design The system software design adopts a modular design, including the control program of the stepper motor design, the detection of the target temperature, the recognition of the key, the LCD drive, the sampling of the data, and the data processing algorithm. The flow of the entire temperature measurement process is shown in Figure 4. 4 Calibration of infrared thermometer Infrared thermometer must be calibrated to correctly display the temperature of the measured target. Traditional calibration methods such as table lookup and curve fitting method not only need to measure multiple temperature points, but also have low accuracy and large errors. In the calibration process of this system, a three-layer BP neural network algorithm is used to calibrate the temperature measurement data, which has the ability of self-learning and adaptive information parallel processing. In the calibration process, a black body furnace is used to simulate the measured target and collect the size of the signal voltage at different temperatures. After repeated measurements, the temperature measurement range is 800℃~1500℃ in the working environment temperature of 10℃~50℃. A comparative experiment was carried out with platinum-rhodium thermocouples on a medium-frequency vacuum induction melting furnace. The system has an accuracy of ±1‰, a resolution of 0.5℃, and a response time of less than 50 ms, which basically meets the initial design requirements of the system. This paper develops an infrared thermometer based on the principle of colorimetric temperature measurement. Compared with other thermometers, it can offset the influence of emissivity on temperature measurement accuracy, making the measurement result closer to the actual surface temperature of the object to be measured. Because it uses a 32-bit STM32 as the processing chip, compared with other 8-bit or 16-bit processors, the data processing capability is greatly enhanced, the temperature measurement performance is greatly improved, and the size of the thermometer is reduced. It has the advantages of simple structure, easy operation, good reliability and low price.
Previous article:Digital Temperature Measurement System Based on ARM and DS18B20
Next article:Design of embedded greenhouse environment monitoring system based on UML
Recommended ReadingLatest update time:2024-11-16 21:34
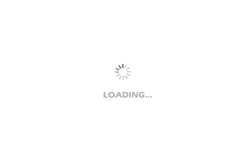
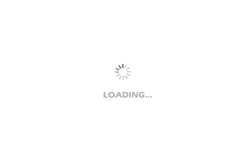
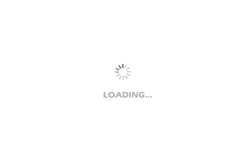
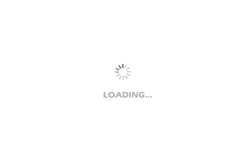
- Popular Resources
- Popular amplifiers
Professor at Beihang University, dedicated to promoting microcontrollers and embedded systems for over 20 years.
- Innolux's intelligent steer-by-wire solution makes cars smarter and safer
- 8051 MCU - Parity Check
- How to efficiently balance the sensitivity of tactile sensing interfaces
- What should I do if the servo motor shakes? What causes the servo motor to shake quickly?
- 【Brushless Motor】Analysis of three-phase BLDC motor and sharing of two popular development boards
- Midea Industrial Technology's subsidiaries Clou Electronics and Hekang New Energy jointly appeared at the Munich Battery Energy Storage Exhibition and Solar Energy Exhibition
- Guoxin Sichen | Application of ferroelectric memory PB85RS2MC in power battery management, with a capacity of 2M
- Analysis of common faults of frequency converter
- In a head-on competition with Qualcomm, what kind of cockpit products has Intel come up with?
- Dalian Rongke's all-vanadium liquid flow battery energy storage equipment industrialization project has entered the sprint stage before production
- Allegro MicroSystems Introduces Advanced Magnetic and Inductive Position Sensing Solutions at Electronica 2024
- Car key in the left hand, liveness detection radar in the right hand, UWB is imperative for cars!
- After a decade of rapid development, domestic CIS has entered the market
- Aegis Dagger Battery + Thor EM-i Super Hybrid, Geely New Energy has thrown out two "king bombs"
- A brief discussion on functional safety - fault, error, and failure
- In the smart car 2.0 cycle, these core industry chains are facing major opportunities!
- The United States and Japan are developing new batteries. CATL faces challenges? How should China's new energy battery industry respond?
- Murata launches high-precision 6-axis inertial sensor for automobiles
- Ford patents pre-charge alarm to help save costs and respond to emergencies
- New real-time microcontroller system from Texas Instruments enables smarter processing in automotive and industrial applications
- [National Technology Low Power Series N32L43x Review] 05. SPI drive TFT screen & TF card to achieve Chinese and English mixed display
- How to prevent LCD screen from moisture and humidity
- Ask for help 50 E coins
- ②. Build development environment and running lights
- Comparison between altera's USB BLASTER II and USB BLASTER
- circuitpython starts testing WebBluetooth functionality
- What are the remedies for a pulse with a shallow rising edge?
- Novice talks about the application and difference of CAN (FD), RS485/RS422, RS232, Ethernet, and EtherCat
- Initial performance test of R329 development board
- Arteli-AT32F4xx timer input capture mode