0 Introduction
DC regulated power supply is a relatively common electronic device, which has been widely used in many fields such as electronic circuits, experimental teaching, scientific research, etc. In recent years, embedded technology has developed extremely rapidly, and highly integrated processors with single-chip microcomputers and embedded ARM as the core have emerged, and have been widely used in automation, communication and other fields. The power supply industry has also begun to use embedded controllers with rich internal integrated resources to realize the control system of digital regulated power supply. Digital regulated power supply uses pulse width modulation wave (PWM) to control the opening and closing of switching devices such as MOS tubes, so as to achieve stable output of voltage and current. Digital regulated power supply also has self-diagnosis function, which can realize overvoltage and overcurrent protection, fault warning, etc.
Compared with the previous analog power supply, the digital voltage-stabilized power supply has greatly reduced many common problems in analog power supply, such as error, aging, temperature drift, and nonlinear compensation, and improved the flexibility and adaptability of the power supply. The embedded ARM processor S3C2440 chip of SAMSUNG is applied to the design of the digital voltage-stabilized power supply of the laboratory test system. Using C language and assembly language, a digital voltage-stabilized power supply control system for the test system is realized with the embedded ARM processor as the core and equipped with PID controller and touch screen functions.
1 Composition and working principle of digital voltage-stabilized power supply of test system
The digital voltage-stabilized power supply consists of a main controller, a PWM voltage-stabilized circuit, a voltage and current sampling circuit, a PID controller, and a touch screen. The system principle block diagram is shown in Figure 1.
Figure 1 System block diagram
The power supply samples the output voltage and current signals, performs PID control, and finally outputs a PWM drive waveform to adjust the output voltage. The output voltage is provided to the chip test platform for use in testing the chip.
The front-end AC power is input to the rectifier module, which outputs a stable DC voltage after rectification and filtering. This DC voltage is directly output to the IGBT module.
The high-precision A/D converter converts the voltage and current signals output from the back end from analog signals to digital quantities and supplies them to S3C2440 for digital PID operation. After the PID controller operation, S3C2440 outputs PWM to IGBT, thus forming a closed-loop control system to control the stable output of voltage and current, thereby realizing the design of digital voltage-stabilized power supply and providing it to the chip test system. The ARM controller realizes the human-computer interaction interface through the touch screen, setting parameters and displaying information on the touch screen.
2 Hardware Design
2.1 ARM control system composition
In view of the high requirements of PID operation and PWM wave output module, after investigation, SAMSUNG's S3C2440 was selected. This is a 32-bit CPU based on the ARM920T core, with a frequency of up to 400MHz, which can fully meet the real-time requirements of PID controller operation; the 16-bit timer can achieve PWM pulse waves with an accuracy of up to 0.03μs, and has an anti-dead zone function; 24 external interrupt sources can fully meet the real-time response to external fault information of the system; the internal embedded LCD controller and DMA channel enable the voltage and current values to be displayed on the LCD in real time, and some required parameters can also be designed through the touch screen; up to 140 general-purpose I/O ports can easily expand external interfaces and devices; it has an 8-channel multiplexed ADC, 10-bit digital encoding, and a conversion rate of up to 500kSPS, which meets the A/D conversion accuracy required by the test system.
2.2 PWM voltage regulation circuit design
The principle of pulse width modulation (PWM) is that the PWM modulation signal controls the on and off of semiconductor power switching devices, so that the output end obtains a series of pulses with equal amplitudes but unequal widths, and after processing, a stable DC voltage output is obtained.
The PWM modulation signal is modulated by the ARM main controller according to the set voltage value and certain rules to modulate the width of each pulse and give a pulse signal.
The PWM voltage stabilization circuit is shown in Figure 2.
Figure 2 PWM voltage regulation circuit [page]
The switching speed of semiconductor power switch devices directly affects the conversion efficiency and load capacity of the power supply. In the PWM voltage stabilization circuit of this system, the drive circuit is composed of resistors, capacitors, transistors and field effect tubes. MOSFET is a voltage unipolar metal oxide silicon field effect transistor, which requires very little driving power and is easy to drive. The input impedance of MOSFET is very high, and its turn-on and turn-off is equivalent to the charging and discharging process of the input capacitor. According to the parameters of the selected device, the conditions that are met are calculated to ensure that the drive circuit provides a sufficiently large overcharge current to achieve fast and reliable switching of MOSFET.
Software Design
S3C2440 is used as the core processor. Its rich on-chip resources and excellent computing speed ensure the real-time performance of the system. The software is mainly written in C language for driver and application development. Its large-capacity memory can fully meet the data storage needs of system programs.
The main functions and software implementation methods of the ARM processor in this test system are as follows.
3.1 PWM wave generation
PWM is used to drive the IGBT in the circuit. According to the output sampling, the values in the timer configuration register TCFGn and the timer n count buffer register TCNTBn are set and adjusted to change the period and pulse width of the output PWM wave. Modifying the value of TCNTBn can control the duty cycle of the PWM wave to increase or decrease by 1, and the PWM output duty cycle can increase or decrease by one thousandth, which can achieve a control accuracy of one thousandth.
3.2 Monitoring and protection system
In order to enable the digital voltage-stabilized power supply to provide voltage for the test system reliably and safely, the system is equipped with a monitoring and protection system, which is mainly used for overcurrent protection and overvoltage protection. The ARM processor uses dual detection for voltage and current. When the voltage and current exceed the set dangerous value range, an audible and visual alarm is sounded and the protection circuit is activated.
3.3 PID Control Algorithm
The PID controller is a combination of proportional, integral and differential controllers. It compares the measured controlled object (voltage and current values in this system) with the set value and uses this error to adjust the system response to achieve a dynamic and real-time control process.
In the digital voltage-stabilized power supply PID control system, the proportional link is used to control the output of the voltage and current to change proportionally with the input error signal. However, there will be a steady-state error here, that is, the deviation between the actual value and the given value. Therefore, it is necessary to introduce an integral link to eliminate the steady-state error to improve the system accuracy. However, due to the accumulation of integrals when the power supply system is turned on and off, it will cause overshoot of voltage and current, and even oscillation. In order to reduce the impact of this aspect, a given error value range is set. When the error between the voltage and current and the set working value is less than this given value, the integral link is used to eliminate the steady-state error generated by the proportional link of the system. The PID control algorithm sets the threshold ε. When |e(k)|>ε, the PD control link is used to reduce the overshoot and make the system respond faster; when |e(k)|<ε, PID control is used to ensure the accuracy and stability of voltage and current. After the voltage reaches the accuracy range of one thousandth, an integral link needs to be added to complete the rapid and stable output when the power supply is turned on. The PID algorithm flow chart is shown in Figure 3.
Fig. 3 PID control algorithm flow chart.
The PID control algorithm program uses a structure definition:
struct PID{
unsigned int SetPoint; //Set the desired value
unsigned int Proportion; //Proportional constant Proportional Const
unsigned int Integral; //Integral constant Integral Const
unsigned int Derivative; //Derivative constant Derivative Const
unsigned int LastError; //Error[-1]
unsigned int PrevError; //Error[-2]
unsigned int SumError; //Sums of Errors
}spid;
In the PID control algorithm, the voltage and current output are dynamically controlled to ensure stability through continuous comparison with given values, while also ensuring the accuracy of the voltage and current output. [page]
The PID control algorithm program is as follows:
unsigned int PIDCalc (struct PID *pp, unsigned int Next-Point)
{
unsigned int dError,Error;
Error=pp->SetPoint-NextPoint; //Deviation
pp->SumError+= Error; //Integral
dError=pp->LastError-pp->PrevError; //Current differential
pp->PrevError=pp->LastError;
pp->LastError= Error;
return (pp->Proportion* Error //proportion
+pp->Integral*pp->SumError //Integral term
+pp->Derivative*dError); // differential term
}
3.4 System Programs
The overall program flow chart of the test system is shown in Figure 4.
Figure 4 Main program flow chart
The digital voltage-stabilized power supply of the test system designed in this paper can meet the power supply requirements for chip testing. Figure 5 shows the output voltage. It can be seen from the figure that the output voltage is stable.
Figure 5 Output voltage waveform
4 Conclusion
The voltage provided by the voltage-stabilized power supply designed in this paper is stable and reliable, and the system operation is also very stable. Due to the large number of expandable I/Os, various required voltage values of the voltage-stabilized power supply can be provided for multiple chips at the same time. This system can not only be used in laboratory chip testing work, but also can modify some control programs through software programming methods to make the designed voltage-stabilized power supply as the power supply voltage for the performance test of intelligent electronic products, thus improving the use efficiency of the equipment and having good application prospects.
Previous article:SD storage technology and its application based on S3C2410
Next article:Design of Touch Screen Interface Based on Embedded Microprocessor S3C44BOX
Recommended ReadingLatest update time:2024-11-16 16:19
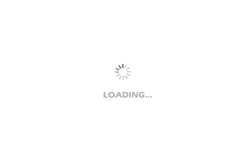
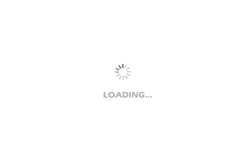
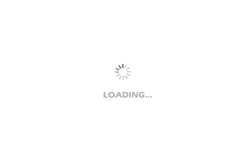
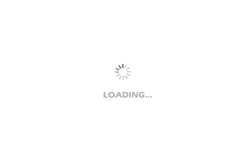
- Popular Resources
- Popular amplifiers
Professor at Beihang University, dedicated to promoting microcontrollers and embedded systems for over 20 years.
- Innolux's intelligent steer-by-wire solution makes cars smarter and safer
- 8051 MCU - Parity Check
- How to efficiently balance the sensitivity of tactile sensing interfaces
- What should I do if the servo motor shakes? What causes the servo motor to shake quickly?
- 【Brushless Motor】Analysis of three-phase BLDC motor and sharing of two popular development boards
- Midea Industrial Technology's subsidiaries Clou Electronics and Hekang New Energy jointly appeared at the Munich Battery Energy Storage Exhibition and Solar Energy Exhibition
- Guoxin Sichen | Application of ferroelectric memory PB85RS2MC in power battery management, with a capacity of 2M
- Analysis of common faults of frequency converter
- In a head-on competition with Qualcomm, what kind of cockpit products has Intel come up with?
- Dalian Rongke's all-vanadium liquid flow battery energy storage equipment industrialization project has entered the sprint stage before production
- Allegro MicroSystems Introduces Advanced Magnetic and Inductive Position Sensing Solutions at Electronica 2024
- Car key in the left hand, liveness detection radar in the right hand, UWB is imperative for cars!
- After a decade of rapid development, domestic CIS has entered the market
- Aegis Dagger Battery + Thor EM-i Super Hybrid, Geely New Energy has thrown out two "king bombs"
- A brief discussion on functional safety - fault, error, and failure
- In the smart car 2.0 cycle, these core industry chains are facing major opportunities!
- The United States and Japan are developing new batteries. CATL faces challenges? How should China's new energy battery industry respond?
- Murata launches high-precision 6-axis inertial sensor for automobiles
- Ford patents pre-charge alarm to help save costs and respond to emergencies
- New real-time microcontroller system from Texas Instruments enables smarter processing in automotive and industrial applications
- [Full cash back for orders, capped at 300 yuan] MPS Mall Power Design Products Recommendation, Huge Discount Experience Season!
- [CH549 Review] Part 4 Low-Level Driver Software Review - Touch Button Driver
- 【AT32F421 Review】+ DHT22 Temperature and Humidity Detection
- Crazy Shell AI open source drone GPIO (remote control indicator light control)
- Where can I get an evaluation board for Toshiba's rice-sized Bluetooth module?
- 16. Low-power intelligent TWS in-ear detection chip VK233DS, Shenzhen Yongjia Microelectronics is the first choice
- [Atria AT32WB415 Series Bluetooth BLE 5.0 MCU] PWM breathing light
- 30V8A stepper motor driver, step angle 1.8 degrees, required accuracy 0.1 degrees, should I choose chip or H bridge
- Can the 66AK2L06 SoC enable miniaturization of test and measurement equipment?
- Circuit diagram of leakage alarm automatic control socket