As a new type of inertial device, fiber optic gyroscope has received more and more attention in recent years because it has many advantages that other gyroscopes cannot match, such as simple structure, high precision, large dynamic range, anti-electromagnetic interference, no drift caused by acceleration, low cost, good reliability, etc. The gyroscope can provide accurate signals such as angular velocity and angular displacement for the carrier to complete the control of the attitude and trajectory of the moving body. Its excellent quality enables it to meet the stringent requirements of military and civilian inertial devices and is widely used.
The performance of inertial devices directly affects the stability of the control system itself. Therefore, when the fiber optic gyroscope is applied to air-to-air missiles, it is necessary to have a full understanding of the characteristics of the gyroscope. For this purpose, a gyroscope acquisition system is constructed to realize the acquisition and characteristic analysis of gyroscope signals.
1 Working principle of fiber optic gyroscope
Fiber optic gyroscope is a kind of laser gyroscope. Its basic principle is based on the Sagnac effect, that is, the optical fiber is wound into a cylindrical optical path. The light emitted by the light source is divided into two beams by the beam splitter and sent to the optical fiber. As the gyroscope rotates, it is transmitted in the clockwise and counterclockwise directions respectively. After one cycle, the two beams of light propagating in opposite directions return to the beam splitter to form interference. When the circular loop formed by the optical fiber does not rotate, the time for the forward and reverse light paths to reach the beam splitter is equal, and the phase difference between the two beams is zero; when the circular loop rotates, the forward and reverse light paths differ. Within a period of time, the beam splitter has rotated from point A to point A'. For the clockwise propagating light beam, when it reaches the beam splitter again, it has traveled an additional distance of AA' (as shown in Figure 1). The angular velocity of the loop rotation can be obtained based on the phase difference between the two beams. The detection sensitivity and resolution of optical fiber are several orders of magnitude higher than those of laser gyroscopes.
2 System composition and working principle
The signal acquisition system designed in this paper realizes the communication between the host computer and DSP through the dual-port RAM. The control board adopts the DSP+CPLD method to control the AD chip to complete the acquisition of multi-channel fiber optic gyroscope data. The system workflow is that the DSP receives the acquisition instruction from the host computer through the dual-port RAM, communicates with the CPLD through the address/data bus, controls the AD chip to collect the external multi-channel gyroscope signal, and then sends it to the host computer through the dual-port RAM. The host computer implements various graphical interface operations and back-end signal processing, and analyzes the collected signals. The system principle block diagram is shown in Figure 2.
[page]
3 System Hardware Structure
The system is mainly composed of DSP chip
TMS320F2812
, dual-port RAMCY7C131, CPLD chip EPM7128T1100, ADC chip
ADS8364
and sensor signal conditioning circuit.
DSP is mainly responsible for communicating with the host computer and controlling AD with CPLD to realize the acquisition of multi-channel fiber optic gyroscope data. TMS320F2812 produced by TI is selected here. This chip is specially designed for control system applications. It uses a core voltage of 1.8 V and has a peripheral interface voltage of 3.3 V. The on-chip storage capacity is 18 KB SRAM, 128 KB FLASH, the highest main frequency is 150 MHz, and a variety of peripheral interfaces are integrated in the chip.
The dual-port RAM mainly outputs data acquisition instructions and receives gyroscope values transmitted by DSP. The selected dual-port RAM model is CY7C131, which is powered by 5 V, has a capacity of 1K×8 b, and the actual data exchange area is 256×8 b. The 256 B storage space is divided into two data areas, one data area (A) stores the command information sent by the host computer, and the other data area (B) stores the collected gyro data information. Since the control DSP and the host computer have different read and write speeds for the dual-port RAM, in order to prevent read and write conflicts caused by speed mismatch, the corresponding storage area in the software is set with a read and write flag, and the read and write status of the dual-port RAM is determined by this flag.
In this system, CPLD is an important component. The logic control module composed of CPLD receives the action command sent by DSP and controls a certain AD channel to collect data. The EPM7128 chip of Altera is selected here. CPLD is a separate control execution structure. By writing the corresponding VHDL code, the corresponding operation circuit can be generated to realize the latching, judgment and execution of various input signals. The
A/D conversion chip uses TI's high-speed, low-power, six-channel synchronous sampling 16 b converter ADS8364, which can ensure that the sampling accuracy reaches more than 12 bits. The chip contains six sample-and-hold devices to ensure simultaneous sampling of six signals; the signal input range is 0-5 V, and the maximum conversion speed is 250K, which can meet the requirements of potentiometer and resolver signal acquisition speed and accuracy. And the digital logic level is 3.3 V. Considering that the sampling frequency of the data acquisition and processing system is generally high, if the DSP is used to directly control the access of ADS8364, it will occupy more DSP resources, and the real-time requirements of DSP are also high. Therefore, in this system design, CPLD is used to implement the interface control circuit of ADS8364.
The gyro analog signal is a -5-+5 V differential signal, which is converted to 0-5 V through signal conditioning. When the speed is low, there are glitches on the signal due to the influence of the system, and filtering is required. An RC low-pass filter circuit is designed to remove high-frequency interference.
4 System software flow
The DSP software code in the system mainly consists of two parts: communication with the host computer and acquisition of gyro signals. Software development is carried out in CCS3.1 (Code Composer Studio). The main program flow of TMS 320F2812 is shown in Figure 3.
After the system is powered on, the initialization of each register in the DSP is completed first, including configuring the RAM module, setting the timer, interrupt, etc., and then the system enters a loop waiting state. When entering the interrupt, the dual-port RAM is first queried to monitor whether there is a collection instruction issued. If so, the A/D is started, and then the data is transmitted to the host computer through the dual-port RAM, otherwise it returns to the loop waiting state.
[page]
5 System anti-interference designIn order to ensure the stability and reliability of the control system, various interference conditions during system operation should be fully considered during system design to avoid anti-interference remedial measures after the design is completed. Each power pin of each IC on the circuit board should be connected in parallel with a 0.1μF high-frequency capacitor to reduce the impact of the IC on the power supply; the drive part and the control part of the control system should be completely isolated, and optical coupling isolation should be used when the control signal is added to the drive module; for high-current, frequently switched components, in order to effectively reduce the instability caused by heat, add a heat sink to the chip; when PCB wiring, the power line and ground line should be as thick as possible, in addition to reducing the voltage drop, more importantly, to reduce coupling noise. Isolation of digital ground and analog ground, and finally connecting them together at one point, etc. In short, the anti-interference ability of the system should be improved as much as possible in the design.
6 Experimental verification and analysis
The experimental results show that this acquisition system can obtain high-precision fiber optic gyroscope signals. Figure 4 is the gyroscope data tested by the system in a static state, and Figure 5 is the data tested by the system during the vibration test (the scale is 100:1). The effect of vibrations of different magnitudes on the performance of the gyroscope can be obtained from the figure, and subsequent spectrum analysis or noise quantization processing can be performed based on this data.
7 Conclusions
The design of this fiber optic gyro acquisition system is novel and has a very important significance for signal acquisition design. The system is easy and fast to use and can meet the needs of daily research. In the future, filtering can be added to the software to process the collected data, making the collected data more valuable for research and more convenient to use.
Previous article:Digital Circuit Design Based on CPLD
Next article:Three-phase five-level inverter PWM pulse generator using DSP and CPLD
Recommended ReadingLatest update time:2024-11-16 15:53
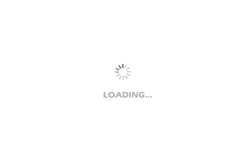
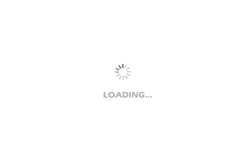
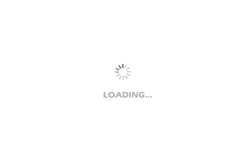
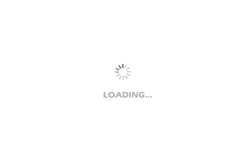
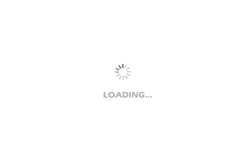
- Popular Resources
- Popular amplifiers
-
Learn CPLD and Verilog HDL programming technology from scratch_Let beginners easily learn CPLD system design technology through practical methods
-
Practical Electronic Components and Circuit Basics (4th Edition)_Explanation of basic circuit principles, introduction to electronic components, design of various circuits and practical circuit analysis
-
FPGA Principle and Structure (Zhao Qian)
-
EDA Technology Practical Tutorial--Verilog HDL Edition (Sixth Edition) (Pan Song, Huang Jiye)
Professor at Beihang University, dedicated to promoting microcontrollers and embedded systems for over 20 years.
- Innolux's intelligent steer-by-wire solution makes cars smarter and safer
- 8051 MCU - Parity Check
- How to efficiently balance the sensitivity of tactile sensing interfaces
- What should I do if the servo motor shakes? What causes the servo motor to shake quickly?
- 【Brushless Motor】Analysis of three-phase BLDC motor and sharing of two popular development boards
- Midea Industrial Technology's subsidiaries Clou Electronics and Hekang New Energy jointly appeared at the Munich Battery Energy Storage Exhibition and Solar Energy Exhibition
- Guoxin Sichen | Application of ferroelectric memory PB85RS2MC in power battery management, with a capacity of 2M
- Analysis of common faults of frequency converter
- In a head-on competition with Qualcomm, what kind of cockpit products has Intel come up with?
- Dalian Rongke's all-vanadium liquid flow battery energy storage equipment industrialization project has entered the sprint stage before production
- Allegro MicroSystems Introduces Advanced Magnetic and Inductive Position Sensing Solutions at Electronica 2024
- Car key in the left hand, liveness detection radar in the right hand, UWB is imperative for cars!
- After a decade of rapid development, domestic CIS has entered the market
- Aegis Dagger Battery + Thor EM-i Super Hybrid, Geely New Energy has thrown out two "king bombs"
- A brief discussion on functional safety - fault, error, and failure
- In the smart car 2.0 cycle, these core industry chains are facing major opportunities!
- The United States and Japan are developing new batteries. CATL faces challenges? How should China's new energy battery industry respond?
- Murata launches high-precision 6-axis inertial sensor for automobiles
- Ford patents pre-charge alarm to help save costs and respond to emergencies
- New real-time microcontroller system from Texas Instruments enables smarter processing in automotive and industrial applications