Single-chip microcomputer is the abbreviation of single-chip microcomputer. It is made by integrating CPU, ROM, RAM, TIMER/COUNTER and input/output interface (I/O) on a large-scale integrated circuit chip. Some single-chip microcomputers also integrate analog-to-digital converters (ADC), pulse width modulation modules (PWM), communication interfaces, etc. Users only need to use a small amount of peripheral circuits to form various application systems. Single-chip microcomputers can be divided into 8-bit machines and 16-bit machines, among which 8-bit machines dominate the market. There are many semiconductor manufacturers that produce single-chip microcomputers, including: INTEL, PHILIPS, SIEMENS, ADM, ATAIEL, MICROCHIP, etc. In recent years, the single-chip microcomputers produced by MICROCHIP have been favored by electronic engineers for their simple instruction system, nanosecond instruction cycle, and powerful peripheral interface functions. The author has used PIC16CXXX and PIC16FXXX series products and finds them very convenient to use.
The functions realized by the motor protector mainly include: three-phase current display, sound alarm, fault tripping, fault memory, overload protection, short circuit protection, leakage protection, phase loss protection, phase imbalance protection, phase sequence protection, over-voltage and under-voltage protection, etc.
The single-chip microcomputer system is used to realize the function of motor protection. In terms of hardware, it is mainly composed of three-phase current signal sampling, leakage current sampling, voltage signal sampling, keyboard interface, display part, control output, alarm output, communication interface and other parts. The key parts are briefly analyzed below.
1. Three-phase current sampling part
This part of the design is directly related to the current sampling accuracy. Therefore, it must be determined through theoretical analysis and repeated experiments. This part of the circuit can use a rectifier circuit or a direct AC proportional conversion circuit. The circuit used directly determines whether the program uses DC sampling or AC sampling, and the program design will be completely different.
If DC sampling is used, the circuit needs to use a rectifier circuit. The rectifier circuit includes half-wave rectification, bridge full-wave rectification, precision half-wave rectification, precision full-wave rectification and other forms. Both diode half-wave rectification and bridge full-wave rectification have the problem that the diode conduction voltage drop affects the linearity of the rectifier circuit, especially when the signal voltage is low. The impact is greater. In order to reduce the impact of the diode conduction voltage drop, Schottky diodes should be selected as rectifier devices, such as IN5819, but it should be noted that the IN5819 withstand voltage is low (only 40V), so the sampling voltage signal should not be too large. Precision half-wave or full-wave rectifier circuits are introduced in many materials, so there is no need to repeat them here. The advantage of this circuit is that it avoids the influence of the forward conduction voltage drop of the rectifier diode, but at the same time increases the complexity of the circuit, and it is also necessary to provide positive and negative power supplies for the amplifier, which increases the cost of the power supply part. In actual use, the pros and cons should be weighed and a comprehensive consideration should be made before making a choice.
In some high-end instruments, people generally use AC sampling. The sampling method is to continuously and real-time sample a complete waveform of the measured signal at a certain period (called sampling period) (for a sine wave, only half a period is needed), and then perform true effective value calculation on the discrete signal obtained by sampling, so as to obtain the true effective value of the current signal, thus avoiding the influence of waveform distortion of the measured signal on the sampling value. There are several key technologies for AC sampling: 1. The sampling period should be much smaller than the period of the measured signal, which is not a problem for the power frequency current signal, because the processing speed of the current microcontroller is sufficient. 2. To avoid sampling signal distortion from the hardware, efforts need to be made from several aspects: ① Ensure that the voltage signal waveform output by the current transformer within the measurement range is less distorted. ② The sampling signal of the current transformer often needs to be proportionally amplified to the input interface of the microcontroller, which requires the signal conversion circuit to have less distortion. ③ To prevent noise interference, the general practice is to add a high-frequency bypass capacitor to the input port of the microcontroller. The AC sampling circuit removes the RC filter capacitor, so the response speed is greatly improved compared to DC sampling, which is especially beneficial for those follow-up systems that require high response characteristics. Although AC sampling has many advantages that DC sampling cannot match, it is rarely used in some simpler small systems because it increases the difficulty of software programming and takes up a large storage space.
2. Display part
LED digital tubes are often used as user interfaces in industrial control instruments. Their advantages are high brightness and simple driving circuits, but they can only display a limited number of characters, and it is very difficult to express relatively rich information. At present, some high-end instruments have begun to use character LCDs or graphic LCDs, and some also contain Chinese character library modules, which are directly displayed in Chinese, making the interface very intuitive, easy to understand and operate. However, it also increases the cost of the circuit, especially the price of graphic LCD modules is too high, which is generally unacceptable for low-priced instruments.
The interface between the microcontroller and the LED digital tube generally adopts serial communication, and is equipped with a shift register to drive the digital tube to work. Different driver programs can be designed to achieve different display modes. For example: the digital tube flashes, the decimal point is automatically changed, and special characters are displayed. In order to reduce the power consumption of the digital tube, a dynamic drive method is generally adopted, that is, it is only displayed within (1/3-1/2) T in a cycle (T). The brightness of the digital tube can be changed by adjusting the duty cycle. In addition, it should be noted that the driving voltage of the digital tube cannot be too high. If it is driven by a +5V power supply, a current limiting resistor or a buck diode must be added. Among them, a buck diode is better to prevent voltage fluctuations caused by changes in the number of digital tubes lit, thereby ensuring the stability of the brightness of the digital tube.
The data line of the interface between the microcontroller and the character LCD module can still use the serial interface mode, and the control signal can be directly controlled by the microcontroller I/O port. If the data line uses the parallel mode, it will occupy a large amount of microcontroller resources, so it is not suitable for use. When compiling the driver, if the performance permits, you should pay attention to reducing the signal frequency of the data line and the clock line as much as possible, so as to reduce electromagnetic interference.
3. Control output
The control output part can use electromechanical relays or solid relays. The former is cheap, has abundant market products, and has a relatively simple driving circuit, but its reliability and service life are limited, and "sparks" will be generated when the contacts are in action, which can seriously affect the normal operation of the system. Therefore, when laying out the PCB board, the relay should be kept as far away from the microcontroller as possible and close to the output port of the instrument. In addition, a freewheeling diode should be connected in parallel at both ends of the relay coil, otherwise a high induced voltage will be generated at the moment when the relay coil is powered off, thereby destroying the circuit. Solid-state relays have the characteristics of long life, stable performance, and no sparks. With the gradual reduction of their prices and the improvement of their performance, they have begun to be widely used, but the price of low-power solid-state relays is still many times higher than that of ordinary relays. Therefore, ordinary relays are used in most motor protectors. In many applications, people hope to have two independent control outputs, one as the main circuit control output and the other as an auxiliary output, as a control of alarm or other functions.
In the single-chip microcomputer system, software is a very important part, which can fully reflect the designer's design ideas. Through the program, the intelligent control of the motor protector and remote communication functions can be realized. Due to limited space, it will not be described in detail here.
Previous article:How to set and adjust PID parameters
Next article:A DSP Processor Design Based on Power Consumption Management
Recommended ReadingLatest update time:2024-11-16 15:55
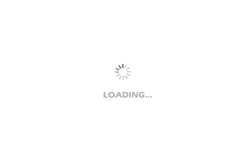
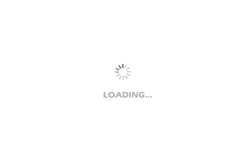
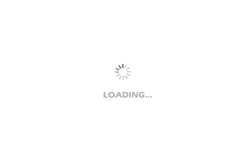
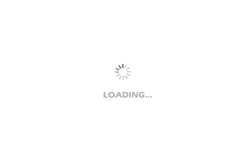
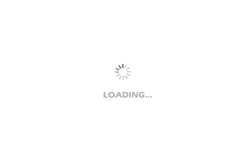
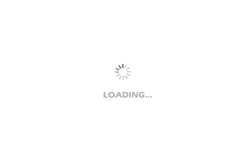
- Popular Resources
- Popular amplifiers
-
Wireless Sensor Network Technology and Applications (Edited by Mou Si, Yin Hong, and Su Xing)
-
Modern Electronic Technology Training Course (Edited by Yao Youfeng)
-
Modern arc welding power supply and its control
-
Small AC Servo Motor Control Circuit Design (by Masaru Ishijima; translated by Xue Liang and Zhu Jianjun, by Masaru Ishijima, Xue Liang, and Zhu Jianjun)
Professor at Beihang University, dedicated to promoting microcontrollers and embedded systems for over 20 years.
- Innolux's intelligent steer-by-wire solution makes cars smarter and safer
- 8051 MCU - Parity Check
- How to efficiently balance the sensitivity of tactile sensing interfaces
- What should I do if the servo motor shakes? What causes the servo motor to shake quickly?
- 【Brushless Motor】Analysis of three-phase BLDC motor and sharing of two popular development boards
- Midea Industrial Technology's subsidiaries Clou Electronics and Hekang New Energy jointly appeared at the Munich Battery Energy Storage Exhibition and Solar Energy Exhibition
- Guoxin Sichen | Application of ferroelectric memory PB85RS2MC in power battery management, with a capacity of 2M
- Analysis of common faults of frequency converter
- In a head-on competition with Qualcomm, what kind of cockpit products has Intel come up with?
- Dalian Rongke's all-vanadium liquid flow battery energy storage equipment industrialization project has entered the sprint stage before production
- Allegro MicroSystems Introduces Advanced Magnetic and Inductive Position Sensing Solutions at Electronica 2024
- Car key in the left hand, liveness detection radar in the right hand, UWB is imperative for cars!
- After a decade of rapid development, domestic CIS has entered the market
- Aegis Dagger Battery + Thor EM-i Super Hybrid, Geely New Energy has thrown out two "king bombs"
- A brief discussion on functional safety - fault, error, and failure
- In the smart car 2.0 cycle, these core industry chains are facing major opportunities!
- The United States and Japan are developing new batteries. CATL faces challenges? How should China's new energy battery industry respond?
- Murata launches high-precision 6-axis inertial sensor for automobiles
- Ford patents pre-charge alarm to help save costs and respond to emergencies
- New real-time microcontroller system from Texas Instruments enables smarter processing in automotive and industrial applications
- [GD32L233C] + 7. Using ds18b20 temperature sensor under RTthread
- EEWORLD University ---- Engineer It Series
- Please help me convert the brd file into one that can be opened by Altium. Thank you.
- 104 capacitors are the most widely used, whether it is power supply filtering or ADC filtering, can any forum friends tell me? Why not 102...
- [Silicon Labs BG22-EK4108A Bluetooth Development Evaluation] 3. Bluetooth protocol test APP lighting and button detection
- [Goodbye 2021, hello 2022] Stop looking at refrigeration units and start clean air conditioning
- What is the difference between quick format and normal format?
- Wake-up function of pedometer bracelet based on F103 and X-NUCLEO-IKS01A3
- Recruiting MBSE part-time training instructors
- [Qinheng Trial] CH559 Development Environment Construction