1 Introduction
Laser wavelength/frequency measuring instruments, also known as wavemeters, can be used to measure the output wavelength of a tuned laser or the wavelength of an unknown laser, and play an important role in the field of optical frequency standard research. Laser wavelength meters are based on the Michelson interference principle: two laser beams are superimposed on each other to produce interference fringes. By comparing the number of interference fringes between a reference laser with a known wavelength and a laser with an unknown wavelength, the wavelength/frequency value of the laser being measured can be obtained.
2 Principle of wavelength meter based on Michelson interferometer
The Michelson wavelength meter is suitable for measuring the wavelength of continuous lasers. Its optical system adopts the Michelson interference principle, as shown in Figure 1.
The reference light source outputs light beam 1, which is divided into two beams of the same frequency after multiple reflections. Finally, they converge at point B to interfere and are received by the light detector D1 as a reference signal.
The light to be measured is injected through the light barrier and adjusted to coincide with the emitted reference light; the two reflectors R1 and R2 are installed on the same movable parallel rail. When the wavelength meter is working, the driving motor drags the rail to move back and forth continuously along the axial direction, so that the reference light and the light to be measured have an optical path difference, causing interference, which is received by the light detectors D1 and D2, thereby obtaining the signal of their interference fringes.
Figure 1 Michelson wavemeter structure
The single wavelength measurement technology obtains the number of interference fringes of the reference laser and the measured laser respectively through the subdivision, shaping and counting circuit of the interference fringes signal. The measured laser wavelength value can be directly obtained based on the reference laser wavelength value and the ratio of the two groups of fringes.
Since the system only uses a simple counting method for the photoelectric signal, when mixed-frequency lasers (such as green light and red light) are injected into the wavelength meter, an erroneous wavelength value will be obtained.
3. Improvement plan
3.1 Plan formulation
The light intensity signal obtained after photoelectric conversion is an analog electrical signal, which needs to be converted into a digital signal for computer analysis. The acquisition of light intensity signals requires high acquisition rate, large data storage capacity, and high analog-to-digital conversion accuracy.
To achieve the above performance, three parameters are required: Precision: The higher the number of AD conversion bits, the higher the precision; Sampling rate: The higher the conversion rate, the more favorable it is for high-frequency signals; Storage capacity: Large-capacity storage can facilitate the processing of large amounts of data.
Although the existing ADC has reached a conversion rate of hundreds of megahertz, it is usually an independent component separated from the microcontroller. The use of 6000 series DSP processors will increase costs and extend the development cycle. According to the characteristics of the signal and the requirements of fast system acquisition, a high-speed, large-capacity signal acquisition system for laser wavelength meters based on the ADμC842 microcontroller was developed.
Usually there are four ways to transfer I/O data, namely: synchronous transfer, asynchronous transfer, interrupt transfer, and DMA transfer .
In the above three data transmission methods, they all need to be transferred to the CPU to be realized. The single-chip microcomputer system cannot achieve high-speed data transmission and data acquisition that is less than its instruction cycle. This limits the application of single-chip microcomputers in the field of high-speed data transmission.
DMA (Direct Memory Access) means direct memory access, which is a working mode that uses hardware to perform data transfer. Today, ADI has launched a new ADμC842 microcontroller, which integrates AD conversion, DMA function, and microcontroller core, which can fully meet the required accuracy and acquisition rate. In addition, the ADμC842 chip can be connected to an external 16M off-chip memory.
3.2 System Principle and Composition
The data acquisition system consists of an ADμC842 single-chip microcomputer and an off-chip memory SDRAM, a photoelectric conversion circuit, a phase-locked frequency multiplication circuit, and a host PC. The measured light signal is converted into an electrical signal through a photodetector and input into the ADC port of the ADμC842 chip; the reference laser signal is used to trigger the AD conversion after frequency multiplication, and is used as the time base for data acquisition to offset the unstable speed of the drive motor dragging the reflector to scan. The system consists of a lower computer and a host computer, which are connected via RS232. The entire system is shown in Figure 2.
The ADμC842 chip can use external triggering to perform high-speed signal acquisition, that is, input a square wave trigger pulse to the trigger end of the microcontroller. Every time a square wave is input, the microcontroller acquires the signal once and stores it.
According to the sampling theorem, to ensure that the original continuous time signal can be restored without distortion from the discrete time signal after the signal is sampled (that is, sampling will not cause any information loss), it must be satisfied that: the signal is band-limited (the signal frequency range is limited); the sampling rate is at least twice the highest frequency of the signal. After the reference light is multiplied by 16 using the NE564 phase-locked loop chip, the multiplied signal is used as the trigger signal to meet the sampling theorem. In this way, it can be ensured that the undistorted signal is collected when the frequency of the signal to be collected is unstable. www.51kaifa.com
The ADμC842 chip is a high-performance multi-channel data acquisition system with an embedded MCU, but the internal data storage is limited. The addition of a flash memory such as a 62512 chip can solve these problems. Finally, the collected signal is transformed by FFT to obtain a spectrum signal, which can intuitively observe the frequency domain characteristics of light, and thus solve the problem of two lights of different frequencies entering the wavelength meter at the same time, causing the count value to be wrong. www.51kaifa.com
3.3 Working Principle
3.3.1 DMA enable and response
When the microcontroller system is powered on or performing internal data processing, DMA should be set low to disable the DMA state. When DMA is enabled to 1, it enters the DMA preparation state and waits for the external trigger signal input. The DMA trigger signal can be a zero-crossing pulse of a periodic signal or a single pulse signal amplified and shaped output. When the first trigger pulse after DMA is enabled arrives, the microcontroller starts data acquisition and transmission.
3.3.2 Control of data lines and address lines
The bus selection control is controlled by the ALE enable signal to control two groups of 74LS373 three-state latches, making them in the open and high-impedance states respectively. Port P0 is an address/data multiplexing bus, which uses time-sharing multiplexing function to realize the time-sharing transmission of data signals and address signals on the same physical line.
2 Signal Acquisition System Principle Block Diagram
3.3.3 DMA block data transfer
At the beginning of the main program, the CPU sends the number of data to be input into the counter in the DMA controller through instructions in advance, and sends the starting address of the input data stored in the memory to the address register in the DMA controller. Then, the CPU can execute other programs in the main program, and also wait for the interrupt request sent by the DMA controller.
3.3.4 End of the response process
The DMA controller sends the input data in the address register to the internal memory at the address of the memory, and controls the input data in the data port to be stored in the corresponding storage unit of the internal memory, and then reduces the counter by 1 and determines whether it is equal to 0. If its content is not 0 (the amount of collected data is insufficient), it continues to collect data.
4 System software writing
4.1 Writing the lower computer software
To meet the needs of different working conditions, all components in the ADμC842 on-chip ADC module can be easily set through 3 SFR registers:
(1) ADCCON1 — controls conversion and sampling time
MD1 MD0: Control the working mode of ADC. Different values of the two correspond to the four working modes of ADC power off; ADC normal operation; ADC power off when not executing conversion cycle; ADC standby when not executing conversion cycle.
CK1 CK0: Set the main clock division factor sent to the ADC clock. The optional division factors are 2, 4, 8, and 32.
AQ1 AQ0: Select the time when the sample-and-hold circuit samples the input signal. The optional sampling clock number is 1, 2, 3, or 4 ADC clocks.
T2C: When this bit is set to 1, the ADC conversion will be started by the overflow interrupt of Timer 2.
EXC: When this bit is set to 1, the ADC conversion will be started by the external input signal of the external pin CONVST.
(2) ADCCON2 — controls ADC channel selection and conversion mode www.51kaifa.com
ADCI: ADC interrupt flag. Set by hardware when ADC conversion is completed; cleared by hardware when MCU responds to the interrupt service subroutine.
DMA: DMA mode enable bit. When set to 1, the ADC DMA mode is started.
CCONV: Continuous conversion bit. When set to 1, the ADC enters the continuous conversion mode. www.51kaifa.com
SCONV: Single conversion bit. When set to 1, a single conversion cycle is started; the SCONV bit automatically resets to 0 when the conversion is completed.
CS3 CS2 CS1 CS0: Channel selection bits. 0-7 correspond to 8 analog input channels, 8 is the temperature sensor, and 15 is to stop DMA operation.
(3) ADCCON2 —ADC status indication
BUSY: ADC busy status bit.
It is a read-only status bit, which when set to 1 indicates that the ADC is in a conversion cycle or calibration cycle.
The remaining bits are reserved.
In DMA mode, the system can automatically store the AD conversion results in the specified location without the need for single-chip control. DMA mode is used to sample a fast-changing signal for a certain period of time, and the host computer can perform accurate spectrum analysis on the signal during this period of time.
4.2 Upper computer software writing
The host computer software uses VB visual programming tools. The receiving, sending and processing of command bytes are written in a multi-threaded manner. The collected data results are displayed in the interface. Data reception is completed by serial communication. The host computer part can also provide a data trend display function, which can dynamically display the change trend of data over a period of time. The data trend chart is represented by a line chart. The curve of the measured parameter changing with time can be displayed in the same rectangular system.
Figure 4 Reproduction of collected data and reproduction of graphics through VT RS232 host computer program
5. AD sampling debugging results
As shown in Figure 3, a signal generator is used to generate two waveforms, the sampling waveform is a square wave, and the waveform to be sampled is a sawtooth wave. In order to verify the correctness of the A/D conversion in the DMA mode, the following experiment was performed.
The waveform to be sampled is a sawtooth wave. After DMA conversion, the data can be viewed online on the PC through the RS232 communication serial port through the program DeBug V2, as shown in Figure 4. The correctness of the collected data can be verified, which can prove that DMA works normally.
6. Conclusion
As a new type of microcontroller, ADμC842 has powerful functions that cannot be matched by general single-chip microcomputers. It has an internal integrated 8-channel high-precision ADC, and can use the external trigger continuous conversion DMA mode when the ADC is collected, with an acquisition frequency of up to 420kHz. This project mainly uses the external trigger DMA mode of the ADC module of ADμC842 to realize the high-speed and large-capacity acquisition of the signal inside the laser wavelength meter, achieving the expected effect and providing a preliminary solution for the research of multi-wavelength measurement technology.
Innovation of the author of this article: At present, most of the wavelength meters based on the Michelson principle in China use simple photoelectric conversion, frequency doubling and counting to measure the laser wavelength value. Although the accuracy is getting higher and higher, when a laser with multiple wavelength values is injected, the measurement will be wrong. This system uses the method of dual-path optical tracking to collect signals, and triggers the external DMA function through the reference light signal to realize the collection of the light signal to be measured, which overcomes this defect and can measure the laser values of multiple wavelengths.
References
1. Zhang Hang, Li Yongjun, Sun Tiezheng, Yu Tao. Application of PXA255 in CCD image acquisition. Microcomputer Information, 2006, 10-1: 84-85
2. Li Gang. ADμC8XX series single chip microcomputer principle and application technology. Beijing: Beijing University of Aeronautics and Astronautics Press, 2002. www.51kaifa.com
3. ADμC842 Users Manual. Analogy Devices, Inc, 2004.
4. He Limin. Selected Microcontroller Application Technology. Beijing: Beijing University of Aeronautics and Astronautics Press, 1999.
5. Xu Aiqing. Single-chip microcomputer application and development system. Beijing: Beijing University of Aeronautics and Astronautics Press, 1995.
Previous article:Design of dot matrix electronic display screen based on SPCE061A
Next article:Design of an ultra-low power consumption dairy cow estrus monitor
Recommended ReadingLatest update time:2024-11-16 23:51
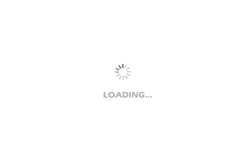
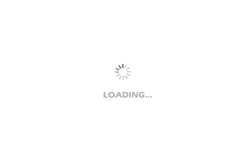
- Popular Resources
- Popular amplifiers
-
Microcomputer Principles and Interface Technology 3rd Edition (Zhou Mingde, Zhang Xiaoxia, Lan Fangpeng)
-
Automotive Electronics S32K Series Microcontrollers: Based on ARM Cortex-M4F Core
-
LPC1700 Chapter 31 General Purpose DMA
-
ARM Cortex-M4+Wi-Fi MCU Application Guide (Embedded Technology and Application Series) (Guo Shujun)
Professor at Beihang University, dedicated to promoting microcontrollers and embedded systems for over 20 years.
- Innolux's intelligent steer-by-wire solution makes cars smarter and safer
- 8051 MCU - Parity Check
- How to efficiently balance the sensitivity of tactile sensing interfaces
- What should I do if the servo motor shakes? What causes the servo motor to shake quickly?
- 【Brushless Motor】Analysis of three-phase BLDC motor and sharing of two popular development boards
- Midea Industrial Technology's subsidiaries Clou Electronics and Hekang New Energy jointly appeared at the Munich Battery Energy Storage Exhibition and Solar Energy Exhibition
- Guoxin Sichen | Application of ferroelectric memory PB85RS2MC in power battery management, with a capacity of 2M
- Analysis of common faults of frequency converter
- In a head-on competition with Qualcomm, what kind of cockpit products has Intel come up with?
- Dalian Rongke's all-vanadium liquid flow battery energy storage equipment industrialization project has entered the sprint stage before production
- Allegro MicroSystems Introduces Advanced Magnetic and Inductive Position Sensing Solutions at Electronica 2024
- Car key in the left hand, liveness detection radar in the right hand, UWB is imperative for cars!
- After a decade of rapid development, domestic CIS has entered the market
- Aegis Dagger Battery + Thor EM-i Super Hybrid, Geely New Energy has thrown out two "king bombs"
- A brief discussion on functional safety - fault, error, and failure
- In the smart car 2.0 cycle, these core industry chains are facing major opportunities!
- The United States and Japan are developing new batteries. CATL faces challenges? How should China's new energy battery industry respond?
- Murata launches high-precision 6-axis inertial sensor for automobiles
- Ford patents pre-charge alarm to help save costs and respond to emergencies
- New real-time microcontroller system from Texas Instruments enables smarter processing in automotive and industrial applications
- XMC4800 ECAT Evaluation Board First Experience - Unboxing Review
- Notes on wiring for st-link and jlink debugging stm32
- Misunderstanding of using XF pin in DSP program interruption during programming
- Vicor: Innovative solutions for powering computing applications and data centers
- [Raspberry Pi Pico Review] - USB CDC serial communication (BSP compiled, not MicroPython)
- DSP GPIO Programming
- It’s better to play with the board than to spend money, this Double 11 free good board is waiting for you to play with!
- Purely handmade transistors! This is how a CPU that can run programs is made!
- [ESP32-Audio-Kit Audio Development Board] - 2: Installing "esp-idf-v3.3.5" on Windows 10
- CC2640 Software Architecture