1 Introduction
Temperature controllers have been widely used in many fields such as industrial control. The intelligent temperature controller with computer communication function introduced in this article is a novel automatic instrument. It uses the single-chip microcomputer AT89C52 as the core, adopts voltage/frequency conversion technology and RS-485 communication interface chip MAX487, and has the advantages of high measurement accuracy, good reliability, strong anti-interference performance, and can realize computer network control. It can be widely used in metallurgy, textile, chemical industry, medical and other industries. It has the temperature measurement and automatic control in the range of -200 to +500°C, and is a substitute for the old temperature controller, with broad market prospects.
2 System hardware design
The system hardware block diagram is shown in Figure 1.
After the system is connected to the 220V AC power supply, the voltage regulator circuit (7805, 7905) generates a ±5V DC working power supply to meet the working needs of the integrated circuit in this system, and the system's telemetry circuit starts to work: in places where personnel cannot enter or are difficult to enter, the temperature sensor platinum resistor PT100 and operational amplifier OP07 convert the measured temperature change into a voltage signal, and the LM331 performs V/F conversion into a pulse signal input to the T0 port of 89C52 for frequency counting. The counting pulse frequency reflects the size of the measured temperature. The system performs PID calculation. If the measured temperature does not match the system set temperature, the electromagnetic relay in the output circuit is controlled by the optical coupler TIL117 according to the PID calculation result to control the temperature adjustment. At the same time, the communication port MAX487 of each extension communicates and transmits data with the host. The host inputs parameters to set the temperature of all temperature control meters. The temperature data set by the system is stored in the watchdog chip X25045. At the same time, when the detected temperature exceeds a certain value of the set temperature, the system will alarm. This system uses a 8155 as the interface of 8-bit LED digital tube and 4-bit keyboard, and displays the system set temperature and detected temperature value at the same time. The 4-bit keyboard is: bit selection, increment, decrement, function.
2.1 Temperature detection and signal amplification circuit
This system uses platinum resistor PT100 as the temperature measuring element. PT100 has the advantages of stable performance, strong anti-oxidation ability and high measurement accuracy. The bridge circuit composed of PT100 and resistor elements converts the resistance change of the platinum resistor caused by temperature change into a voltage signal input amplifier. Because the platinum resistor installed at the measurement site needs to be connected to the console through a connecting wire, in order to reduce the influence of the lead resistance, a three-wire wiring method is used.
The signal amplification circuit is composed of the integrated operational amplifier OP07. The peak-to-peak noise of OP07 is 0.6μV, and the common mode rejection ratio CMRR is greater than 106dB. The pin functions of OP07 are: IN+ and IN- are signal differential input terminals, pins 1 and 8 are zero adjustment terminals, and pin 6 is the output terminal.
2.2 Voltage/Frequency Conversion Circuit (LM331)
In control and measurement systems, AD converters usually connect electrical or non-electrical quantities to subsequent circuits through sensors and pre-circuits. This system uses V/F converter LM331 to convert temperature signal changes into frequency signals.
LM331 is an integrated circuit produced by NS Corporation of the United States with high performance-price ratio, simple peripheral circuit, single power supply and low power consumption. LM331 has a dynamic range of up to 100dB, and has good linearity when the operating frequency is as low as 0.1Hz, and the digital resolution is up to 12 bits. The output driver of LM331 adopts the open collector form, so the logic level of the output pulse can be flexibly changed by selecting the logic current and external resistor to adapt to different logic circuits such as TTL, DTL and CMOS. LM331 can operate between 4.0V and 40V, the output can be as high as 40V, and it can prevent VCC from short circuit.
In this system, LM331 converts the output frequency signal into TTL level and sends it to the P3.4 port of the microcontroller as the counting pulse of T0. The conversion circuit has good linearity and strong anti-interference ability. The output range is above 10Hz~10kHz, which is conducive to improving the measurement range of the system.
The main pin functions of LM331 are:
RC: reference current input terminal; CO: current output terminal; FO: frequency output terminal; CI: voltage input terminal.
2.3 CPU and peripheral circuits
AT89C52 is a MCS-51 series single-chip microcomputer produced by ATMEL. It has a built-in 8K-byte electrically erasable programmable EEPROM on-chip program memory and 256 bytes of RAM. The on-chip program memory space can meet the program storage needs of this system, eliminating the need for off-chip EPROM program memory and address latches, making the circuit structure simple.
TXD, RXD, P1.5, P1.6 are connected to DI, RO, and DE of MAX487 for data communication control, P1.0~P1.4 ports and RESET are connected to X25045ALE, P0 port, P2.0, and P2.1 are connected to 8155. The counter T0 input of P3.4 port is connected to the frequency output of LM331 for pulse counting. P1.7 port is the control end of the optocoupler TIL117.
The system data storage and fault protection part is composed of X25045, which is a 512-byte EEPROM with serial communication and has watchdog and power monitoring functions. X25045 has three programmable watchdog cycles. When power is on and VCC is lower than the detection threshold, it outputs a reset signal. The reset high level of X25045 output is valid, and its reset output terminal is directly connected to the reset terminal of 89C52.
X25045 pin functions: chip select input; SO: serial output; SI: serial input; SCK: serial clock input; WP: write protect input; RESET: reset output.
2.4 Communication port (MAX487)
This system uses the RS-485 interface chip MAX487 as the communication port. MAX487 is a differential bus low-power transceiver produced by MAXIM for RS-485 and RS-422 communications. It contains a driver and a receiver, has a driver/receiver enable function, an input impedance of 1/4 load (≥48kW), and a node number of 128, that is, each MAX487 driver can drive 128 standard loads. The driver of MAX487 is designed to limit the slope so that the output signal edge is not too steep, so as to avoid generating too many high-frequency components in the transmission line, thereby effectively suppressing interference. The receiving sensitivity of MAX487 is ±200MV, that is, when the differential voltage at the receiving end is ≥+200MV, the receiver output is high level, when it is ≤-200MV, the receiver output is low level, and when it is between ±200MV, the receiver output is in an uncertain state. Therefore, once the receiver of a certain node generates a low level when the bus is idle, the transmission line is open or short-circuited, the serial receiver will not be able to find the start bit, thus causing communication abnormalities. For this reason, this system has made hardware processing: the A and B output terminals of MAX487 are connected with pull-up and pull-down resistors to ensure that all receivers can receive complete data when valid data is sent.
The data transmission rate of MAX487 is 0.25Mbps, the static working current is 120μA, and it works with a single 5V power supply. In this system, MAX487 adopts half-duplex communication mode, and the communication between each node is through a pair of twisted pair as the transmission medium. Because the characteristic impedance of the twisted pair is 120Ω, the system connects a 120Ω resistor at the beginning and end of MAX487 to reduce the reflection of the transmission signal on the line. Since the host and the extension are far apart, and the extension system is often powered on or reset at different times, if a MAX487 is in the sending state at this time, it will occupy the communication bus and make other extensions unable to communicate with the host. This system adds an optical coupler TIL117 between the P1.6 port of 89C52 and the DE end of MAX487 to ensure that the DE end of MAX487 is "0" when the system is powered on and reset, which effectively solves this problem.
The main pin functions of MAX487 are: RO: receiver output; : receiver output enable, RO is enabled when is "0"; DE: driver output enable; DI: driver input; A: receiver in-phase input and driver in-phase output; B: receiver inverting input and driver inverting output.
3 Design of control software
The system software adopts modular design, which consists of main program, subprogram and interrupt service program. The main program flow chart is shown in Figure 2. The main subprograms include: display subprogram; keyboard scanning subprogram; PID operation subprogram. Due to space limitations, the specific program is omitted.
4 Conclusion
This intelligent temperature controller has high measurement accuracy and stable and reliable performance. It can not only replace the old temperature controller, but also realize efficient data management in computer network. It is a practical intelligent instrument in the field of modern industrial control.
Previous article:Design of Single-CPU Simulator for Single-Chip Microcomputer
Next article:Motor soft starter based on single chip microcomputer AT89C5l
Recommended ReadingLatest update time:2024-11-16 20:33
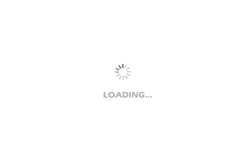
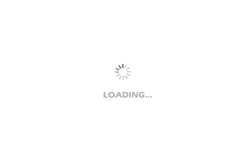
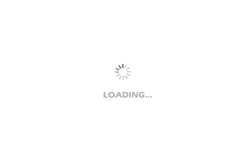
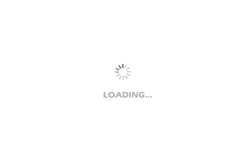
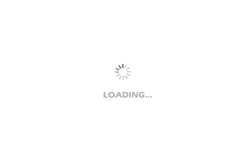
- Popular Resources
- Popular amplifiers
-
Wireless Sensor Network Technology and Applications (Edited by Mou Si, Yin Hong, and Su Xing)
-
Modern Electronic Technology Training Course (Edited by Yao Youfeng)
-
Modern arc welding power supply and its control
-
Small AC Servo Motor Control Circuit Design (by Masaru Ishijima; translated by Xue Liang and Zhu Jianjun, by Masaru Ishijima, Xue Liang, and Zhu Jianjun)
Professor at Beihang University, dedicated to promoting microcontrollers and embedded systems for over 20 years.
- Innolux's intelligent steer-by-wire solution makes cars smarter and safer
- 8051 MCU - Parity Check
- How to efficiently balance the sensitivity of tactile sensing interfaces
- What should I do if the servo motor shakes? What causes the servo motor to shake quickly?
- 【Brushless Motor】Analysis of three-phase BLDC motor and sharing of two popular development boards
- Midea Industrial Technology's subsidiaries Clou Electronics and Hekang New Energy jointly appeared at the Munich Battery Energy Storage Exhibition and Solar Energy Exhibition
- Guoxin Sichen | Application of ferroelectric memory PB85RS2MC in power battery management, with a capacity of 2M
- Analysis of common faults of frequency converter
- In a head-on competition with Qualcomm, what kind of cockpit products has Intel come up with?
- Dalian Rongke's all-vanadium liquid flow battery energy storage equipment industrialization project has entered the sprint stage before production
- Allegro MicroSystems Introduces Advanced Magnetic and Inductive Position Sensing Solutions at Electronica 2024
- Car key in the left hand, liveness detection radar in the right hand, UWB is imperative for cars!
- After a decade of rapid development, domestic CIS has entered the market
- Aegis Dagger Battery + Thor EM-i Super Hybrid, Geely New Energy has thrown out two "king bombs"
- A brief discussion on functional safety - fault, error, and failure
- In the smart car 2.0 cycle, these core industry chains are facing major opportunities!
- The United States and Japan are developing new batteries. CATL faces challenges? How should China's new energy battery industry respond?
- Murata launches high-precision 6-axis inertial sensor for automobiles
- Ford patents pre-charge alarm to help save costs and respond to emergencies
- New real-time microcontroller system from Texas Instruments enables smarter processing in automotive and industrial applications
- Accelerometer and gyroscope
- Download of Siemens e-book "PCB Manufacturing Process - Optimization through Digital Transformation" has started~
- DP83822I Industrial Ethernet PHY auto-negotiation function and its strap resistor configuration
- 【DIY】Remodeling the mobile phone battery charger
- Modern processors and optimized code performance
- TMS320F28035 ECAN interrupt sending and receiving
- Request X-CUBE-MEMS1 firmware package
- TI CCS compiler download update
- Simple and efficient zero-point acquisition circuit
- BMS solutions for electric bicycles and electric motorcycles under the new national standard for electric vehicles