At present, the domestic solar automatic trackers in my country mainly include: differential pressure solar tracker, controlled release solar tracker, clock solar tracker, and comparative control solar tracker. Pure mechanical trackers and clock electromechanical trackers have low accuracy. This system uses a relatively high-precision photoresistor-controlled dual-axis solar tracker to keep the photovoltaic cells facing the sun; after dark, the solar panels can be turned back to the east to achieve daily cycle operation.
Solar power generation control system
Sensor structure
The sensor structure of the tracker is shown in Figure 1. A cylindrical shell is set up, and 4 photoresistors are arranged on the outside of the cylinder in the east, south, west and north directions respectively; P1 and P3 are installed symmetrically on both sides of the cylinder from east to west to roughly detect the deflection angle of the sun moving from east to west, that is, the azimuth angle; P2 and P4 are installed symmetrically on both sides of the cylinder from north to south to roughly detect the apparent height of the sun, that is, the altitude angle; inside the cylinder, 4 photoresistors are also arranged in the east, south, west and north directions respectively to accurately detect the deflection angle of the sun moving from east to west and the apparent height of the sun.
Figure 1 Schematic diagram of sensor structure
Column Rotation Tracker
The structure of the tracker is shown in Figure 2. The stepper motor 1 is fixed on the base, the main shaft and its supporting bearing are installed on the base (the main shaft can rotate relative to the base), the rotating frame and the bracket are fixed on the main shaft, the photovoltaic cell and the stepper motor 2 are installed on the bracket (the photovoltaic cell can rotate relative to the bracket), and the output shaft of the stepper motor 2 is connected to the photovoltaic cell.
Figure 2 Schematic diagram of column rotation tracker
When the light is offset, the control unit sends a control signal to drive stepper motor 1 to drive the rotating frame and the main shaft, bracket and photovoltaic cell fixed on the rotating frame to rotate; at the same time, the control signal drives stepper motor 2 to drive the photovoltaic cell to rotate relative to the bracket. Through the joint work of stepper motor 1 and stepper motor 2, the azimuth and altitude angle of the sun can be tracked [2].
MPPT Controller
The output power of a photovoltaic cell is related to its operating voltage (the UP curve is generally a smooth curve that rises first and then falls, and the maximum power is obtained at a certain voltage value in the middle). Only when it works at the most suitable voltage can its output power have a unique maximum value. For example: under a sunlight intensity of 1000W/m2, U=24V, I=1A; U=30V, I=0.9A; U=36V, I=0.7A; it can be seen that the output power is greater under a voltage of 30V. The main functions of the MPPT (maximum power point tracking) controller are: to detect the DC voltage and output current of the main circuit, calculate the output power of the solar cell array, and realize the tracking of the maximum power point [3]. Figure 3 is a schematic diagram of the actual application of the perturbation and observation method to achieve maximum power point tracking.
Figure 3 Schematic diagram of MPPT control implementation
The disturbance resistor R and MOSFET are connected in series. Under the condition that the output voltage is basically stable, the average current passing through the resistor is changed by changing the duty cycle of the MOSFET, thus generating a current disturbance [4]. At the same time, the output current and output voltage of the photovoltaic cell will also change accordingly. By measuring the changes in the output power and voltage of the photovoltaic cell before and after the disturbance, the disturbance direction of the next cycle is determined. When the disturbance direction is correct, the output power of the solar photovoltaic panel increases, and the disturbance continues in the same direction in the next cycle. On the contrary, when the output power of the solar photovoltaic panel decreases, it means that the disturbance direction is wrong, and the disturbance is reversed in the next cycle. The disturbance and observation are repeated in this way to make the solar photovoltaic panel output reach the maximum power point.
System hardware design
The main control circuit of the system plays an important role in the whole design. It mainly controls the main circuit, ensures the effective implementation of the MPPT algorithm, keeps the DC/DC conversion at a constant voltage output, and communicates with the LCD human-machine interface. It also plays an important role in the control circuit of the battery charge and discharge. First, it effectively tracks the power of the photovoltaic cell, so that the battery can be charged with a constant voltage current of maximum power. This avoids the waste of photovoltaic cell energy. Secondly, the constant voltage current controlled by the main controller also makes it easy to design the constant voltage charging and discharging circuit. The system structure block diagram is shown in Figure 4.
Figure 4 System structure diagram
Drive circuit
The photoresistor model used is GM5516, with a bright resistance of 5-10 KΩ and a dark resistance of more than 200KΩ. The system performs A/D acquisition on 4 pairs of 8-way photoresistors (R1 corresponds to P1 in Figure 1, R2 corresponds to P3 in Figure 1, and R3-R8 in the same way), converts the acquired analog quantity into digital quantity, judges the changes in azimuth and pitch angles, and gives a forward or reverse pulse to the stepper motor through I/O (OUT1-OUT8), controls the stepper motor to turn to the correct direction, and then continues A/D acquisition and control until the signal difference is within a certain range, at which time the photovoltaic cell is facing the sun. The circuit is shown in Figures 5 and 6.
Figure 5 Photoresistor acquisition circuit
Figure 6 Stepper motor drive circuit
Stepper motors 57BYG007 and GSP-24RW-046 are both four-phase eight-beat. OUT1, OUT2, OUT3, and OUT4 are high level in turn, and pins 1 to 4 of ULN2803 (stepper motor driver chip, collector output) are high level in turn, so a pulse signal of one step forward rotation is given to stepper motor 1 (57BYG007), and the stepper motor rotates forward 1.8 degrees; conversely, OUT4, OUT3, OUT2, and OUT1 are high level in turn, and the stepper motor reverses 1.8 degrees. The driving principle of GSP-24RW-046 is the same.
DC/DC, MPPT circuit
The photovoltaic cells used in the system have a normal operating voltage of 10-14V and a working current of about 1A. The battery used is 12V-7AH. Since a 12V battery generally requires a voltage of 13-15V to charge it, and the photovoltaic cells cannot guarantee stable charging of the battery without DC/DC processing, the photovoltaic cell voltage is increased by 20V through the BOOST boost circuit (high-power stepper motors require a higher voltage, which can be prepared for future system upgrades), and then reduced to 14V for stable charging of the battery [5]. The circuit diagram is shown in Figure 7.
Figure 7 DC/DC and MPPT circuit
The left end of the circuit in Figure 7 is a photovoltaic cell, and the output voltage on the right end is Uo (Uo in Figure 7 is Uin in Figure 8). We need to get Uo=20V on the right end.
First, a circuit consisting of 50K and 10K resistors is connected in parallel, and A/D data is collected at both ends of the 10K resistor to collect the voltage Uad1, and the voltage Uin=6Uad1 at both ends of the battery is indirectly obtained;
Uo is required to be 20V. The required D (duty cycle of Q1) can be calculated by Uo = Uin/(1-D), and the output control PWM1 waveform is used. Since the high-power MOSFET driving voltage used requires 15V, PWM1 needs to control Q1 after a pull-up voltage of 15V and a combination of an optocoupler switch, rather than simply controlling Q1.
The voltage Uad2 across R6 is collected through the circuit composed of R5 and R6, and Uo=6Uad2 is obtained indirectly. Uo is compared with 20V, and the actual D is adjusted immediately to make D=D-△D or D=D+△D (△D is 5% of the PMW pulse period). Then, delay, collect and judge until the precise duty cycle D is obtained, so that the output voltage Uo=20V can be accurately obtained.
On the basis of the basic stability of the output voltage, set Q4's PWM2 and change the duty cycle of the disturbance resistor R7 to change the output current. Through A/D acquisition of the voltage across R8, the voltage Uad3 is collected to obtain the total circuit current I=Uad3/R8, and thus the total output power of the solar cell P=Uin×I (because the circuit is a current continuous operation, the ripple current on the inductor can be small enough to be close to a smooth DC current, the current of C1 can be ignored, and even the capacitor C1 can be removed, and the collection resistor at the left end of the photovoltaic cell is quite large, the current is extremely small and can also be ignored), and the actual instantaneous output power of the photovoltaic cell is changed to achieve MPPT.
Battery charge and discharge control circuit
During the day, the photovoltaic cell needs to charge the battery so that the battery can power the load (street lights) at night, and the working power of the stepper motor also needs to be provided by the photovoltaic cell (if the power of the photovoltaic cell is not enough to drive the motor, it means that the sunlight is extremely poor and there is no need to rotate the motor). The ARM board must be powered continuously, powered by the photovoltaic cell during the day and by the battery at night. This set of charge and discharge control circuit requires 2 relays, one to control the charging and discharging of the battery, and the other to control whether the working voltage of the ARM board is provided by the photovoltaic cell or the battery. The circuit is shown in Figure 8.
Figure 8 Battery charge and discharge control circuit
The right end of the circuit is Uin=20V as the input voltage. The voltage is reduced to 14V through the BUCK step-down circuit to charge the battery. Uo=Uin×D. To get a voltage of 14V, set the duty cycle of Q2 to 70%. During the day: Both relays are in the normally open state A, the photovoltaic cell powers the stepper motor and ARM (using a 7805 voltage regulator to step down to 5V), and charges the battery. The positive pole of the battery is connected to an anti-phase cut-off diode to ensure charging without discharging. At night (or when the sunshine is extremely poor, as determined by the photoresistor): Relays 1 and 2 are attracted to B, the stepper motor stops working, the battery powers the ARM, and drives the load (street lamp) to work.
System software design
The main control functions of this system are realized by the main control software, which mainly includes: A/D module, DC/DC module, MPPT and battery charge and discharge control, etc. The system focuses on hardware design, and the software design is relatively simple. The main program flow chart is shown in Figure 9.
Figure 9 Flowchart of the main program and the main control background program
Conclusion
The whole system uses ARM LPC2131 as the core to control DC/DC, MPPT, and battery charging and discharging. It uses the maximum power point tracking to make the photovoltaic cells work in the best state, and the actual conversion rate of the photovoltaic cells is increased from 10% to 30%. The system has achieved the expected performance indicators through automatic tracking tests, with high control accuracy. The company has produced finished products and plans to mass produce them. It is simple to make, low in cost, and highly practical, which has a very broad application prospect for my country's vast areas rich in solar energy resources.
Previous article:Design of a gateway between CAN bus and Ethernet based on ARM LPC2292
Next article:Realizing ARM FPGA online configuration based on JTAG interface
Recommended ReadingLatest update time:2024-11-16 16:03
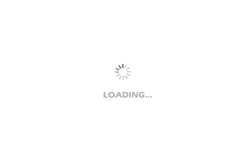
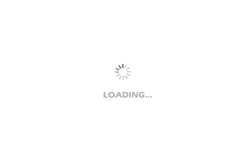
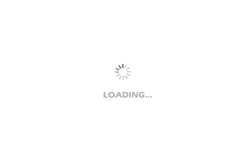
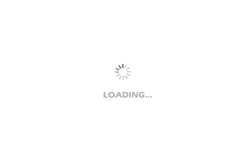
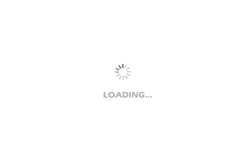
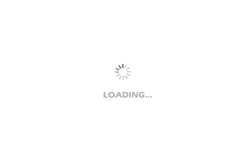
Professor at Beihang University, dedicated to promoting microcontrollers and embedded systems for over 20 years.
- Innolux's intelligent steer-by-wire solution makes cars smarter and safer
- 8051 MCU - Parity Check
- How to efficiently balance the sensitivity of tactile sensing interfaces
- What should I do if the servo motor shakes? What causes the servo motor to shake quickly?
- 【Brushless Motor】Analysis of three-phase BLDC motor and sharing of two popular development boards
- Midea Industrial Technology's subsidiaries Clou Electronics and Hekang New Energy jointly appeared at the Munich Battery Energy Storage Exhibition and Solar Energy Exhibition
- Guoxin Sichen | Application of ferroelectric memory PB85RS2MC in power battery management, with a capacity of 2M
- Analysis of common faults of frequency converter
- In a head-on competition with Qualcomm, what kind of cockpit products has Intel come up with?
- Dalian Rongke's all-vanadium liquid flow battery energy storage equipment industrialization project has entered the sprint stage before production
- Allegro MicroSystems Introduces Advanced Magnetic and Inductive Position Sensing Solutions at Electronica 2024
- Car key in the left hand, liveness detection radar in the right hand, UWB is imperative for cars!
- After a decade of rapid development, domestic CIS has entered the market
- Aegis Dagger Battery + Thor EM-i Super Hybrid, Geely New Energy has thrown out two "king bombs"
- A brief discussion on functional safety - fault, error, and failure
- In the smart car 2.0 cycle, these core industry chains are facing major opportunities!
- The United States and Japan are developing new batteries. CATL faces challenges? How should China's new energy battery industry respond?
- Murata launches high-precision 6-axis inertial sensor for automobiles
- Ford patents pre-charge alarm to help save costs and respond to emergencies
- New real-time microcontroller system from Texas Instruments enables smarter processing in automotive and industrial applications
- Urgent, help, please help me analyze the circuit, I am confused
- The national competition topic has been released. Have you chosen your topic yet?
- Questions about channel selection and multiplexing
- Memory Technology R&D System Latest Recruitment Information 202010
- What is Wearable Technology
- EEWORLD University Hall----GPS Principles and Applications
- Keil5 software simulation problem
- [ESP32 Learning_1] The first ESP32-S3 example - hello_world
- How TI dual-core processor ARM+DSP achieves collaborative work
- GD32F307VG supports Mbed development