Introduction
A stepper motor is an actuator that converts electrical pulses into angular displacement. After receiving a pulse signal, the driver drives the stepper motor to rotate a fixed angle in the set direction. First, the angular displacement is controlled by controlling the number of pulses to achieve accurate positioning; second, the speed and acceleration of the motor are controlled by controlling the pulse rate to achieve the purpose of speed control. At present, stepper motors have the characteristics of low inertia, high positioning accuracy, no cumulative error, and simple control. They are widely used in mechatronic products and are often used for positioning control and constant speed control. The commonly used chips for stepper motor drive circuits are L297 and L298 combination applications, 3977, 8435, etc. These chips generally have a single-phase drive current of about 2 A and cannot drive higher power motors, limiting their application range. This paper proposes a design scheme for a stepper motor drive circuit based on the stepper motor driver chip TB6560 launched by Toshiba in 2008.
1 Stepper motor drive circuit design
1.1 Introduction to TB6560 TB6560
is a low-power, highly integrated two-phase hybrid stepper motor driver chip launched by Toshiba. Its main features are: internal integrated dual full-bridge MOSFET driver; maximum withstand voltage of 40 V, single-phase output maximum current of 3.5 A (peak); full step, 1/2, 1/8, 1/16 subdivision modes; built-in temperature protection chip, automatically disconnect all outputs when the temperature is greater than 150°C; overcurrent protection; HZIP25 package. The TB6560 stepper motor drive circuit mainly includes three circuits: control signal isolation circuit, main circuit and automatic half-current circuit.
The subdivision control of the stepper motor is essentially to control the current in the excitation winding of the stepper motor so that the synthetic magnetic field inside the stepper motor is a uniform circular rotating magnetic field, thereby realizing the subdivision of the stepper motor step angle. In general, the amplitude of the synthetic magnetic field vector determines the size of the stepper motor rotation torque, and the angle between two adjacent synthetic magnetic field vectors determines the size of the step angle. DCY2 and DCY1 external dip switches set the current decay mode (0, 25%, 50%, 100%) to meet the needs of different stepper motors. Due to the influence of the motor's own conditions, power supply conditions, pulse frequency and other factors, stepper motors may generate high-frequency noise. This noise can be reduced or even eliminated by setting the current decay mode. Figure 3 shows the change of coil current when the decay mode is 0 and 50%, and it can be seen that the waveform has been significantly improved.
1.4 Stepper Motor Automatic Half-current Circuit
To reduce the heat generation of stepper motors, copper loss and iron loss must be reduced. Reducing copper loss means reducing resistance and current. It is required to select motors with small resistance and small rated current when selecting, but this often conflicts with the requirements of torque and high speed. For the selected motor, first of all, the automatic half-current control function and offline function of the driver should be fully utilized. The automatic half-current automatically reduces the current when the motor is in a static state, and the offline function cuts off the output motor current; secondly, the subdivision driver has less heat generation because the current waveform is close to sine and there are fewer harmonics. Reducing iron loss is related to the motor drive voltage. Although high-voltage driven motors will improve high-speed characteristics, they will also increase heat generation. Therefore, the appropriate drive voltage level should be selected, taking into account high speed, stability, heat generation, noise and other indicators.
In order to minimize the motor heat generation, the TQ2 and TQ1 pin levels of TB6560 need to be set to the maximum current output when the motor is working, and the current is halved or even smaller when the motor is not working, so it is called "automatic half-current circuit". After defining the maximum output current with NFA and NFB, the current ratio output is set through TQ2 and TQ1. When set to 00, 01, 10, and 11, the output current is 100%, 75%, 50%, and 25% of the maximum current respectively. Changing the drive current of the motor also changes the size of the motor output torque. The automatic half-current circuit design uses a retriggered monostable circuit chip 74CH123, and uses the motor drive pulse CLK as the trigger pulse of the monostable circuit. The reverse output of the monostable circuit is connected to the TQ2 pin. When the motor drive pulse continues, TQ2 keeps a low level and keeps a high level when there is no drive pulse. In the circuit of Figure 2, TQ1 is connected to 3 jumper caps. When jumper 1 is connected, TQ2 and TQ1 are always at the same high or low level, and the drive current switches between 25% and 100%; when jumper 2 is connected, TQ2 is always low, and the current switches between 50% and 100%; when jumper 3 is connected, the current switches between 25% and 75%. Different jumpers can be selected according to the working drive current.
2 Stepper motor step-out and overstep problems and solutions
The synchronous torque generated in the stepper motor cannot make the rotor speed follow the rotation speed of the stator magnetic field, thus causing step-out. The main reasons for step-out and solutions:
① The torque of the stepper motor is insufficient and the drag capacity is insufficient. When the drive pulse frequency reaches a certain critical value, it starts to lose step. Since the dynamic output torque of the stepper motor decreases with the increase of the continuous operation frequency, any operating frequency higher than this frequency will cause step-out.
There are three solutions: the electromagnetic torque generated by the stepper motor can be increased, and the drive current can be appropriately increased within the rated current range; when the torque is insufficient in the high-frequency range, the drive voltage of the drive circuit can be appropriately increased; using a stepper motor with large torque, etc. can also reduce the torque that the stepper motor needs to overcome, and the motor operating frequency can be appropriately reduced to increase the output torque of the motor.
② Stepper motor starts out of step. Due to the inertia of the stepper motor itself and the load it carries, this phenomenon will occur when the acceleration time is too short. A reasonable acceleration time should be set to allow the motor to rise smoothly from a low speed to a certain speed.
③ Resonance of the stepper motor is also a cause of out of step. When the stepper motor is in continuous operation, if the frequency of the control pulse is equal to the natural frequency of the stepper motor, resonance will occur. Within a control pulse cycle, the vibration has not been fully attenuated, and the next pulse has arrived, so the dynamic error is the largest near the resonance frequency and causes the stepper motor to lose step. Solution: Reduce the drive current of the stepper motor; use subdivision drive method and damping method.
When the rotor obtains too much energy during the stepping process, the average speed of the rotor will be higher than the average rotation speed of the stator magnetic field, which will increase the output torque generated by the stepper motor, thereby causing the stepper motor to overstep.
When the stepper motor oversteps, the drive current of the stepper motor can be reduced to reduce the output torque of the stepper motor or prolong the deceleration time.
3 Experimental results
During the design, the chip logic voltage should be lower than the drive voltage, otherwise the chip cannot work properly; when selecting NFA and NFB current sensing resistors, non-inductive resistors with a power of not less than 2 W should be selected; the printed circuit board wiring of the motor drive power supply and the drive output connection and ground should ensure that 3 A current can be passed stably; a fuse is added to the power inlet to protect the drive circuit to prevent the motor from burning the circuit board due to excessive current. The designed driver is applied to the drive of the three-axis stepper motor of the engraving machine X, Y, and Z. After testing, the engraved sample is shown in Figure 4. From the final result, the accuracy meets the target requirements.
Conclusion
This paper proposes a design scheme for a stepper motor drive circuit based on TB6500, and provides a solution to the problem of stepping out of step and overstepping of the stepper motor. The experiment proves that the effect is good and the expected goal is achieved.
1.2 Stepper motor control signal isolation circuit
The stepper motor control signal isolation circuit is shown in Figure 1. There are three stepper motor control signals (CLK, CW, ENABLE), which control the motor's rotation angle and speed, the motor's forward and reverse direction, and enable, respectively. All of them must be isolated by optocouplers and connected to the chip. Optocouplers have two functions: first, to prevent the motor from interfering with and damaging the interface board circuit; second, to shape the control signal. For CLK and CW signals, medium-speed or high-speed optocouplers should be selected to ensure that there will be no lag and distortion after signal coupling, which will affect the motor drive, and the driver board can meet the requirements of higher pulse frequency drive. In this design, two 6N137 high-speed optocouplers are selected to isolate CLK and CW, and their signal transmission rate can reach 10 MHz, and one TLP521 ordinary optocoupler is used to isolate the ENABLE signal. When applying, please note: the same-direction and reverse output connection of the optocoupler; the forward and backward power supplies of the optocoupler should be separate isolated power supplies, otherwise it cannot play the role of isolating interference.
1.3 Stepper Motor Main Circuit
As shown in Figure 2, the stepper motor main circuit mainly includes two parts: the drive circuit and the logic control circuit.
The power supply of the drive circuit adopts 28 V, and the voltage range is 4.5~40 V. Increasing the drive voltage can increase the output torque of the motor in the high-frequency range. The voltage selection should be determined according to the usage. VMB and VMA are the stepper motor drive power supply pins, and ceramic decoupling capacitors and electrolytic capacitors should be connected to stabilize the voltage. OUT_AP, OUT_AM, OUT_BP, and OUT_BM pins are the motor 2-phase output interfaces respectively. Since the freewheeling diode is integrated internally, these four output ports do not need external diodes like Toshiba's 8435 driver chip, which greatly reduces the wiring space of the circuit board. NFA and NFB are the maximum drive current definition pins for motor A and B phases respectively. The maximum current calculation formula is I OUT (A)=0.5(V)/R NF (Ω). If the maximum drive current of each phase of the motor is pre-defined as 2.5 A, take R NF =0.2 Ω, then PGNDA, PGNDB, and SGND are the motor A and B phase drive pin grounds and logic power grounds respectively.
The power supply of the logic control circuit is 5 V, VDD is the logic power supply pin, and decoupling capacitors and bypass capacitors should be connected to reduce interference noise; M0 and PROTECT are working status and overcurrent protection indicators; RESET is the chip reset pin, and low level is effective; the size of the capacitor connected to OSC determines the chopper frequency, and 100 to 1 000 pF is recommended, and the chopping frequency is 400 to 44 kHz; M2 and M1 are subdivision setting pins, and external dip switches can set different subdivision values, such as full step, half step, 1/8 subdivision, and 1/16 subdivision. Because stepper motors have the disadvantages of large vibration and noise when working at low frequencies, they need to be subdivided to solve.
Reference address:Design of stepper motor drive circuit based on TB6560
A stepper motor is an actuator that converts electrical pulses into angular displacement. After receiving a pulse signal, the driver drives the stepper motor to rotate a fixed angle in the set direction. First, the angular displacement is controlled by controlling the number of pulses to achieve accurate positioning; second, the speed and acceleration of the motor are controlled by controlling the pulse rate to achieve the purpose of speed control. At present, stepper motors have the characteristics of low inertia, high positioning accuracy, no cumulative error, and simple control. They are widely used in mechatronic products and are often used for positioning control and constant speed control. The commonly used chips for stepper motor drive circuits are L297 and L298 combination applications, 3977, 8435, etc. These chips generally have a single-phase drive current of about 2 A and cannot drive higher power motors, limiting their application range. This paper proposes a design scheme for a stepper motor drive circuit based on the stepper motor driver chip TB6560 launched by Toshiba in 2008.
1 Stepper motor drive circuit design
1.1 Introduction to TB6560 TB6560
is a low-power, highly integrated two-phase hybrid stepper motor driver chip launched by Toshiba. Its main features are: internal integrated dual full-bridge MOSFET driver; maximum withstand voltage of 40 V, single-phase output maximum current of 3.5 A (peak); full step, 1/2, 1/8, 1/16 subdivision modes; built-in temperature protection chip, automatically disconnect all outputs when the temperature is greater than 150°C; overcurrent protection; HZIP25 package. The TB6560 stepper motor drive circuit mainly includes three circuits: control signal isolation circuit, main circuit and automatic half-current circuit.
The subdivision control of the stepper motor is essentially to control the current in the excitation winding of the stepper motor so that the synthetic magnetic field inside the stepper motor is a uniform circular rotating magnetic field, thereby realizing the subdivision of the stepper motor step angle. In general, the amplitude of the synthetic magnetic field vector determines the size of the stepper motor rotation torque, and the angle between two adjacent synthetic magnetic field vectors determines the size of the step angle. DCY2 and DCY1 external dip switches set the current decay mode (0, 25%, 50%, 100%) to meet the needs of different stepper motors. Due to the influence of the motor's own conditions, power supply conditions, pulse frequency and other factors, stepper motors may generate high-frequency noise. This noise can be reduced or even eliminated by setting the current decay mode. Figure 3 shows the change of coil current when the decay mode is 0 and 50%, and it can be seen that the waveform has been significantly improved.
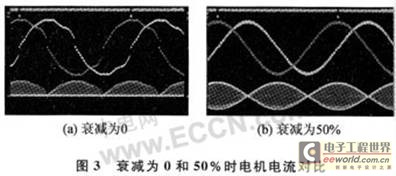
1.4 Stepper Motor Automatic Half-current Circuit
To reduce the heat generation of stepper motors, copper loss and iron loss must be reduced. Reducing copper loss means reducing resistance and current. It is required to select motors with small resistance and small rated current when selecting, but this often conflicts with the requirements of torque and high speed. For the selected motor, first of all, the automatic half-current control function and offline function of the driver should be fully utilized. The automatic half-current automatically reduces the current when the motor is in a static state, and the offline function cuts off the output motor current; secondly, the subdivision driver has less heat generation because the current waveform is close to sine and there are fewer harmonics. Reducing iron loss is related to the motor drive voltage. Although high-voltage driven motors will improve high-speed characteristics, they will also increase heat generation. Therefore, the appropriate drive voltage level should be selected, taking into account high speed, stability, heat generation, noise and other indicators.
In order to minimize the motor heat generation, the TQ2 and TQ1 pin levels of TB6560 need to be set to the maximum current output when the motor is working, and the current is halved or even smaller when the motor is not working, so it is called "automatic half-current circuit". After defining the maximum output current with NFA and NFB, the current ratio output is set through TQ2 and TQ1. When set to 00, 01, 10, and 11, the output current is 100%, 75%, 50%, and 25% of the maximum current respectively. Changing the drive current of the motor also changes the size of the motor output torque. The automatic half-current circuit design uses a retriggered monostable circuit chip 74CH123, and uses the motor drive pulse CLK as the trigger pulse of the monostable circuit. The reverse output of the monostable circuit is connected to the TQ2 pin. When the motor drive pulse continues, TQ2 keeps a low level and keeps a high level when there is no drive pulse. In the circuit of Figure 2, TQ1 is connected to 3 jumper caps. When jumper 1 is connected, TQ2 and TQ1 are always at the same high or low level, and the drive current switches between 25% and 100%; when jumper 2 is connected, TQ2 is always low, and the current switches between 50% and 100%; when jumper 3 is connected, the current switches between 25% and 75%. Different jumpers can be selected according to the working drive current.
2 Stepper motor step-out and overstep problems and solutions
The synchronous torque generated in the stepper motor cannot make the rotor speed follow the rotation speed of the stator magnetic field, thus causing step-out. The main reasons for step-out and solutions:
① The torque of the stepper motor is insufficient and the drag capacity is insufficient. When the drive pulse frequency reaches a certain critical value, it starts to lose step. Since the dynamic output torque of the stepper motor decreases with the increase of the continuous operation frequency, any operating frequency higher than this frequency will cause step-out.
There are three solutions: the electromagnetic torque generated by the stepper motor can be increased, and the drive current can be appropriately increased within the rated current range; when the torque is insufficient in the high-frequency range, the drive voltage of the drive circuit can be appropriately increased; using a stepper motor with large torque, etc. can also reduce the torque that the stepper motor needs to overcome, and the motor operating frequency can be appropriately reduced to increase the output torque of the motor.
② Stepper motor starts out of step. Due to the inertia of the stepper motor itself and the load it carries, this phenomenon will occur when the acceleration time is too short. A reasonable acceleration time should be set to allow the motor to rise smoothly from a low speed to a certain speed.
③ Resonance of the stepper motor is also a cause of out of step. When the stepper motor is in continuous operation, if the frequency of the control pulse is equal to the natural frequency of the stepper motor, resonance will occur. Within a control pulse cycle, the vibration has not been fully attenuated, and the next pulse has arrived, so the dynamic error is the largest near the resonance frequency and causes the stepper motor to lose step. Solution: Reduce the drive current of the stepper motor; use subdivision drive method and damping method.
When the rotor obtains too much energy during the stepping process, the average speed of the rotor will be higher than the average rotation speed of the stator magnetic field, which will increase the output torque generated by the stepper motor, thereby causing the stepper motor to overstep.
When the stepper motor oversteps, the drive current of the stepper motor can be reduced to reduce the output torque of the stepper motor or prolong the deceleration time.
3 Experimental results
During the design, the chip logic voltage should be lower than the drive voltage, otherwise the chip cannot work properly; when selecting NFA and NFB current sensing resistors, non-inductive resistors with a power of not less than 2 W should be selected; the printed circuit board wiring of the motor drive power supply and the drive output connection and ground should ensure that 3 A current can be passed stably; a fuse is added to the power inlet to protect the drive circuit to prevent the motor from burning the circuit board due to excessive current. The designed driver is applied to the drive of the three-axis stepper motor of the engraving machine X, Y, and Z. After testing, the engraved sample is shown in Figure 4. From the final result, the accuracy meets the target requirements.
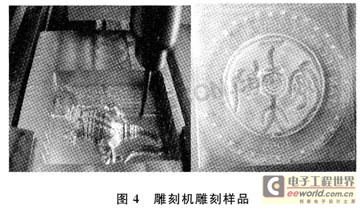
Conclusion
This paper proposes a design scheme for a stepper motor drive circuit based on TB6500, and provides a solution to the problem of stepping out of step and overstepping of the stepper motor. The experiment proves that the effect is good and the expected goal is achieved.
1.2 Stepper motor control signal isolation circuit
The stepper motor control signal isolation circuit is shown in Figure 1. There are three stepper motor control signals (CLK, CW, ENABLE), which control the motor's rotation angle and speed, the motor's forward and reverse direction, and enable, respectively. All of them must be isolated by optocouplers and connected to the chip. Optocouplers have two functions: first, to prevent the motor from interfering with and damaging the interface board circuit; second, to shape the control signal. For CLK and CW signals, medium-speed or high-speed optocouplers should be selected to ensure that there will be no lag and distortion after signal coupling, which will affect the motor drive, and the driver board can meet the requirements of higher pulse frequency drive. In this design, two 6N137 high-speed optocouplers are selected to isolate CLK and CW, and their signal transmission rate can reach 10 MHz, and one TLP521 ordinary optocoupler is used to isolate the ENABLE signal. When applying, please note: the same-direction and reverse output connection of the optocoupler; the forward and backward power supplies of the optocoupler should be separate isolated power supplies, otherwise it cannot play the role of isolating interference.
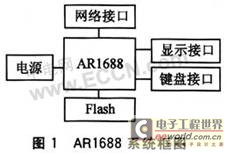
1.3 Stepper Motor Main Circuit
As shown in Figure 2, the stepper motor main circuit mainly includes two parts: the drive circuit and the logic control circuit.
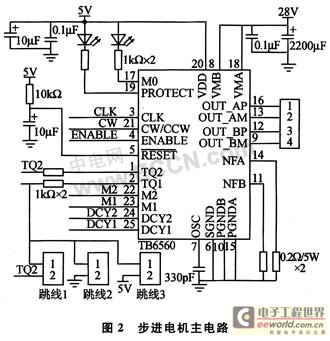
The power supply of the drive circuit adopts 28 V, and the voltage range is 4.5~40 V. Increasing the drive voltage can increase the output torque of the motor in the high-frequency range. The voltage selection should be determined according to the usage. VMB and VMA are the stepper motor drive power supply pins, and ceramic decoupling capacitors and electrolytic capacitors should be connected to stabilize the voltage. OUT_AP, OUT_AM, OUT_BP, and OUT_BM pins are the motor 2-phase output interfaces respectively. Since the freewheeling diode is integrated internally, these four output ports do not need external diodes like Toshiba's 8435 driver chip, which greatly reduces the wiring space of the circuit board. NFA and NFB are the maximum drive current definition pins for motor A and B phases respectively. The maximum current calculation formula is I OUT (A)=0.5(V)/R NF (Ω). If the maximum drive current of each phase of the motor is pre-defined as 2.5 A, take R NF =0.2 Ω, then PGNDA, PGNDB, and SGND are the motor A and B phase drive pin grounds and logic power grounds respectively.
The power supply of the logic control circuit is 5 V, VDD is the logic power supply pin, and decoupling capacitors and bypass capacitors should be connected to reduce interference noise; M0 and PROTECT are working status and overcurrent protection indicators; RESET is the chip reset pin, and low level is effective; the size of the capacitor connected to OSC determines the chopper frequency, and 100 to 1 000 pF is recommended, and the chopping frequency is 400 to 44 kHz; M2 and M1 are subdivision setting pins, and external dip switches can set different subdivision values, such as full step, half step, 1/8 subdivision, and 1/16 subdivision. Because stepper motors have the disadvantages of large vibration and noise when working at low frequencies, they need to be subdivided to solve.
Previous article:Stepper Motor Controller Circuit
Next article:Development of Vehicle License Plate Recognition System Based on NiosⅡ Soft-core
- Popular Resources
- Popular amplifiers
Latest Industrial Control Articles
- Molex leverages SAP solutions to drive smart supply chain collaboration
- Pickering Launches New Future-Proof PXIe Single-Slot Controller for High-Performance Test and Measurement Applications
- CGD and Qorvo to jointly revolutionize motor control solutions
- Advanced gameplay, Harting takes your PCB board connection to a new level!
- Nidec Intelligent Motion is the first to launch an electric clutch ECU for two-wheeled vehicles
- Bosch and Tsinghua University renew cooperation agreement on artificial intelligence research to jointly promote the development of artificial intelligence in the industrial field
- GigaDevice unveils new MCU products, deeply unlocking industrial application scenarios with diversified products and solutions
- Advantech: Investing in Edge AI Innovation to Drive an Intelligent Future
- CGD and QORVO will revolutionize motor control solutions
MoreSelected Circuit Diagrams
MorePopular Articles
- Innolux's intelligent steer-by-wire solution makes cars smarter and safer
- 8051 MCU - Parity Check
- How to efficiently balance the sensitivity of tactile sensing interfaces
- What should I do if the servo motor shakes? What causes the servo motor to shake quickly?
- 【Brushless Motor】Analysis of three-phase BLDC motor and sharing of two popular development boards
- Midea Industrial Technology's subsidiaries Clou Electronics and Hekang New Energy jointly appeared at the Munich Battery Energy Storage Exhibition and Solar Energy Exhibition
- Guoxin Sichen | Application of ferroelectric memory PB85RS2MC in power battery management, with a capacity of 2M
- Analysis of common faults of frequency converter
- In a head-on competition with Qualcomm, what kind of cockpit products has Intel come up with?
- Dalian Rongke's all-vanadium liquid flow battery energy storage equipment industrialization project has entered the sprint stage before production
MoreDaily News
- Allegro MicroSystems Introduces Advanced Magnetic and Inductive Position Sensing Solutions at Electronica 2024
- Car key in the left hand, liveness detection radar in the right hand, UWB is imperative for cars!
- After a decade of rapid development, domestic CIS has entered the market
- Aegis Dagger Battery + Thor EM-i Super Hybrid, Geely New Energy has thrown out two "king bombs"
- A brief discussion on functional safety - fault, error, and failure
- In the smart car 2.0 cycle, these core industry chains are facing major opportunities!
- The United States and Japan are developing new batteries. CATL faces challenges? How should China's new energy battery industry respond?
- Murata launches high-precision 6-axis inertial sensor for automobiles
- Ford patents pre-charge alarm to help save costs and respond to emergencies
- New real-time microcontroller system from Texas Instruments enables smarter processing in automotive and industrial applications
Guess you like
- Thank you + my son, my daughter, and my wife
- How to set breakpoints when debugging a program in keil4?
- 【Qinheng Trial】3. System clock and TIMER0
- Award-winning live broadcast: Market environment is uncertain, protecting IoT devices Infineon is very sure to start on time at 10:00 on July 30
- How to measure the internal resistance of the battery?
- Which one costs more: 200 MSP430s or 250 MSP430s?
- Free application: ST sensor kit SensorTile.box worth 350 yuan
- EEWorld Circuit Diagram Channel has a new version and is now online, come and experience it now!
- Reduction Operator Introduction
- WiFi 7 specs, features and release date