In the cylinder head production workshop of DaimlerChrysler, the largest automobile manufacturer in Germany, the correctness of component assembly is checked by scanning QR codes with powerful and reliable vision sensors produced by Siemens. This technology ensures the traceability of components and has become an indispensable part of the quality management process.
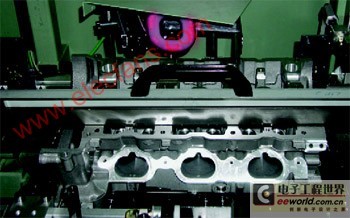
Pilot, testing and certification of Simatic VS130-2u vision sensor in other application areas
Every day, DaimlerChrysler's Bad Canstatt engine plant in Untertürkheim, Stuttgart, Germany, produces about 1,600 two-speed V6 and V8 diesel engines. Among them, detailed information on the production process of 3,200 cylinder heads is recorded in a product history file prepared for each vehicle. The cylinders are first marked with a QR code before processing to make their identity unique.
The code contains the part number, production year, production date, serial number in the relevant production series, and leaves space for adding notes.
The detection error rate is greatly reduced
Previously, DaimlerChrysler had been using cameras for code detection.
However, the error rate of camera scanning sometimes reached more than 10%, far exceeding the quality standards set by the company. In addition, in order to read the code, it was necessary to clean the residual oil on the surface of the cylinder head. As a result, the camera itself was also contaminated with oil, and the staff had to clean it every day. In order to solve these problems, the company's production planning department decided to use Siemens' Simatic VS130-2 vision sensor to replace the existing camera inspection system.
"We are surprised that since we used the VS130-2, the scanning error rate has been greatly reduced, and even the oil stains on the surface of the QR code do not need to be cleaned." Ralf Blesch, who is responsible for the production of cylinder heads in Bad Canstatt, said. "Through close cooperation with Siemens, we have successfully controlled the scanning error rate permanently between 0.1% and 0.5%. And we no longer need to clean the oil stains all the time, which saves us more energy and investment costs." Bernd Hofacker, who is responsible for production planning, added. Now, the camera head is only cleaned once a week with the machine as a whole. Since mid-2005, a total of 10 sets of VS130-2 machine vision sensors have been used in the Bad Canstatt cylinder head production workshop. The cylinder heads must be newly identified after passing through all processing centers. The specific method is to install the camera in the diagonal direction of the scanning surface. In order to ensure sufficient light, a circle of LED lights is installed on the camera.
Ralf Blesch explained: "In order to prevent occlusion and reflection caused by oil stains, we designed the lighting unit separately and adjusted it to the appropriate angle." At the same time, Siemens has improved the sensor according to the trial results of DaimlerChrysler. Now, the camera can select any part of the image to shoot, instead of only shooting the whole as before. This new technology has now become the standard configuration of VS130-2, which further reduces the scanning error rate of the system. Now, once an image error is detected, the system can determine whether it is caused by a label error or dirt.
Image capture and analysis in one system
The system can capture the entire static image with the automatic exposure setting through its own CCD chip. The correct recognition of each DMC point only requires five pixels, so the system is extremely flexible. By selecting different optical systems, the image point size and scanning distance can be defined, and a large range can be defined.
After scanning, VS130-2 can transmit the captured image to a separate analysis unit. In order to prevent oil contamination and protect the chip, the analysis unit is installed slightly higher than the sensor.
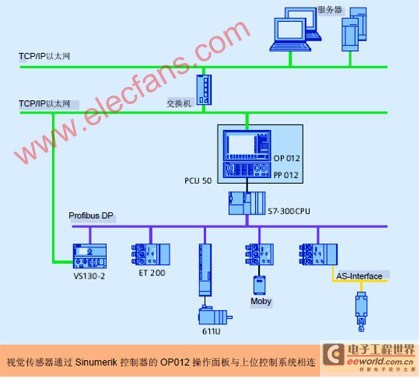
After the image is analyzed, the resulting data string will be transmitted via DP to the Sinumerik 840D machine controller or Simatic S7-300 in the machining center. The new system can be effortlessly integrated into the existing communication structure, and the analyzed image is displayed on the control panel of the production line in "real time". In addition, the system can also learn new codes by teaching. With VS130-2, users will no longer have to deal with complex production planning or parameterization work, but only need to configure the lighting and teach the algorithm, without having to make user settings in code.
Flexible access methods make the testing process open and transparent
The visual sensor can also be connected to the host system through the OP012 operation panel of the Sinumerik controller, which captures machine and operation data and enters it into the product history file. The system uses the Transline 2000 human-machine interface system developed by DaimlerChrysler and Siemens to communicate via Ethernet. The staff can access the stored fault images and camera live images through any connected terminal, and the access rights can be controlled by password.
Muller-Chrysler believes that another advantage of the system is that in the future the camera system as a standard open interface can be configured throughout the company via a WEB browser. Direct access to the image not only allows operators to monitor all functions directly from their desktop, but also speeds up the commissioning of DMC scanners as long as the position of the lighting unit can be monitored online and optimized as needed. In "Code Quality Access" mode, the system can also detect whether the label is working properly or whether there is a problem with the code itself.
Previous article:HybridKIT three-phase inverter system solution based on HybridPACK 2 IGBT module
Next article:Solution for Chinese Character Fire Floor Display Alarm System
- Popular Resources
- Popular amplifiers
- Molex leverages SAP solutions to drive smart supply chain collaboration
- Pickering Launches New Future-Proof PXIe Single-Slot Controller for High-Performance Test and Measurement Applications
- CGD and Qorvo to jointly revolutionize motor control solutions
- Advanced gameplay, Harting takes your PCB board connection to a new level!
- Nidec Intelligent Motion is the first to launch an electric clutch ECU for two-wheeled vehicles
- Bosch and Tsinghua University renew cooperation agreement on artificial intelligence research to jointly promote the development of artificial intelligence in the industrial field
- GigaDevice unveils new MCU products, deeply unlocking industrial application scenarios with diversified products and solutions
- Advantech: Investing in Edge AI Innovation to Drive an Intelligent Future
- CGD and QORVO will revolutionize motor control solutions
- Innolux's intelligent steer-by-wire solution makes cars smarter and safer
- 8051 MCU - Parity Check
- How to efficiently balance the sensitivity of tactile sensing interfaces
- What should I do if the servo motor shakes? What causes the servo motor to shake quickly?
- 【Brushless Motor】Analysis of three-phase BLDC motor and sharing of two popular development boards
- Midea Industrial Technology's subsidiaries Clou Electronics and Hekang New Energy jointly appeared at the Munich Battery Energy Storage Exhibition and Solar Energy Exhibition
- Guoxin Sichen | Application of ferroelectric memory PB85RS2MC in power battery management, with a capacity of 2M
- Analysis of common faults of frequency converter
- In a head-on competition with Qualcomm, what kind of cockpit products has Intel come up with?
- Dalian Rongke's all-vanadium liquid flow battery energy storage equipment industrialization project has entered the sprint stage before production
- Allegro MicroSystems Introduces Advanced Magnetic and Inductive Position Sensing Solutions at Electronica 2024
- Car key in the left hand, liveness detection radar in the right hand, UWB is imperative for cars!
- After a decade of rapid development, domestic CIS has entered the market
- Aegis Dagger Battery + Thor EM-i Super Hybrid, Geely New Energy has thrown out two "king bombs"
- A brief discussion on functional safety - fault, error, and failure
- In the smart car 2.0 cycle, these core industry chains are facing major opportunities!
- The United States and Japan are developing new batteries. CATL faces challenges? How should China's new energy battery industry respond?
- Murata launches high-precision 6-axis inertial sensor for automobiles
- Ford patents pre-charge alarm to help save costs and respond to emergencies
- New real-time microcontroller system from Texas Instruments enables smarter processing in automotive and industrial applications
- 【DSP】TMS320F28035 SCI routine (self-transmission and self-reception + query)
- The reverse withstand voltage peak of the secondary winding rectifier tube D10 reaches -142V. How can I adjust the RCD parameter value to reduce it?
- C6678 multi-core application cache test
- Simulation AWR Learning Website
- 15th Anniversary] EE DIY (Progress) -- Upper Computer UI Changes
- 【LoRa】Common Problems in LoRa Development
- [Synopsys IP Resources] Using ARC Processor IP to achieve efficient facial detection and recognition
- Welcome to discuss: Why are so many people optimistic about gallium nitride (GaN) devices?
- How can I include all the component libraries and package libraries used when copying the PROTEL99 project file to another computer?
- Summary of where and how DSP stores and writes data