In recent years, the market demand for warp knitting machines has increased, and double-needle bed warp knitting machines, high-speed machines, biaxial and multi-axial warp knitting machines have all been selling well. In response to the system control requirements of warp knitting machines, Beijing Hollysys Automation Drive Technology Co., Ltd. has launched a warp knitting machine shuttle section traverse system. The entire system uses Hollysys PLC, which has a high cost performance ratio, as the controller. By using the PLC servo positioning function, rich internal data resources and powerful communication function, the control and drive are closely integrated, making the system control better, showing the advantages of Hollysys products in system integration.
The warp knitting machine is mainly composed of a weaving mechanism, a bar sliding mechanism, a warp feeding mechanism, a pulling and winding mechanism, and a transmission mechanism. The control system of the warp knitting machine mainly includes three parts: an electronic warp feeding system, an electronic jacquard system, and a shuttle sliding system. The main function of the electronic warp feeding system is to control the warp feeding speed and tension of various yarns to ensure constant warp feeding. The electronic warp feeding system can be divided into two types: single-speed or double-speed EBA and multi-speed EBC. It uses PLC, frequency converter, three-phase asynchronous motor, servo motor, encoder, etc. to form a closed-loop control to achieve constant speed operation of the main shaft and adjust the warp shaft speed, thereby achieving constant warp feeding. The electronic jacquard system is mainly used for pattern extraction, and then cooperates with the shuttle sliding to achieve pattern forming. It is mainly composed of an embedded system to realize the conversion of jacquard data and the action control of jacquard, and the execution action is realized by 3146 to 4096 solenoid valves. Due to the slow response speed of electromagnetic action, it is now slowly replaced by piezoelectric ceramics with fast action response. The shuttle sliding system mainly controls the movement of the shuttle. The shuttles of warp knitting machines usually have 56 or 40 shuttles, and the maximum number is 56. Each shuttle is controlled by a 900W servo. Due to the large number of control axes, decentralized control is adopted.
The shuttle traverse system developed by Hollysys is composed of PLC and servo motor, including control part, drive part and monitoring part.
The main controller of the control part needs to collect and process the lateral movement signal and coordinate the synchronous work of each sub-controller. The system adopts the G5 series PLC of Hollysys, which consists of a CPU module FM215-2BT02, two 16-point switch input modules FM221-1BH00, three 16-point switch output modules FM222-1BH00 and a 16-point relay output module FM221-1HF00. There are 28 sub-controllers in the system, and each group of sub-controllers controls two-axis shuttle servos. The sub-controller adopts the G3 series high-speed motion control CPU module LM3106A of Hollysys. The CPU module integrates 14-point input and 10-point transistor output, has an RS232 serial communication interface, and has two 100KHz high-speed pulse output functions. The sub-controller is connected to the host computer through the RS232/RS485 converter in 485 communication mode for monitoring.
The system has a total of 56 shuttles, which are controlled by 56 sets of 900W Senchuang AC servos from Hollysys. The servos operate according to the pattern data stored in the sub-controller that has been converted in advance by the weaving conversion program.
The upper monitoring is completed by an Advantech touch-screen tablet computer TPC-1261 equipped with monitoring software; at the same time, the computer also runs a weaving pattern conversion program to convert and download pattern data. The monitoring software uses Hollysys's configuration software to complete the operation status monitoring of the entire system, including the operation status of the servo, the communication status of the PLC and servo, the shuttle number of the pattern operation, etc.; complete the system parameter setting: mechanical parameters are mainly spindle parameters, and motion parameters are mainly pulse frequency, filter time, acceleration and deceleration time, etc. for PLC positioning control; in addition, it completes the process needle installation, fault handling, head control, user management, help and other functions.
2010/3/13 20:08:45
Previous article:Using PLC to solve the problem of synchronous control of distributed vehicle drives
Next article:Application of Delta PLC and touch screen in strip-rolling machine
Recommended ReadingLatest update time:2024-11-17 00:45
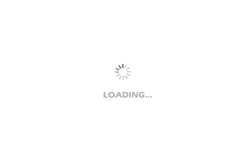
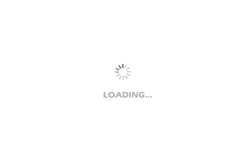
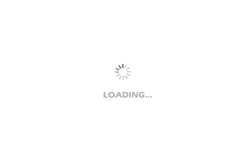
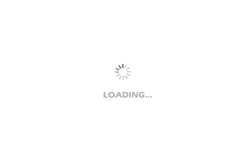
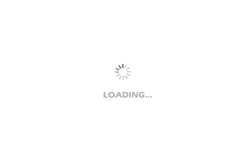
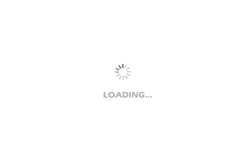
- Popular Resources
- Popular amplifiers
- Molex leverages SAP solutions to drive smart supply chain collaboration
- Pickering Launches New Future-Proof PXIe Single-Slot Controller for High-Performance Test and Measurement Applications
- CGD and Qorvo to jointly revolutionize motor control solutions
- Advanced gameplay, Harting takes your PCB board connection to a new level!
- Nidec Intelligent Motion is the first to launch an electric clutch ECU for two-wheeled vehicles
- Bosch and Tsinghua University renew cooperation agreement on artificial intelligence research to jointly promote the development of artificial intelligence in the industrial field
- GigaDevice unveils new MCU products, deeply unlocking industrial application scenarios with diversified products and solutions
- Advantech: Investing in Edge AI Innovation to Drive an Intelligent Future
- CGD and QORVO will revolutionize motor control solutions
- Innolux's intelligent steer-by-wire solution makes cars smarter and safer
- 8051 MCU - Parity Check
- How to efficiently balance the sensitivity of tactile sensing interfaces
- What should I do if the servo motor shakes? What causes the servo motor to shake quickly?
- 【Brushless Motor】Analysis of three-phase BLDC motor and sharing of two popular development boards
- Midea Industrial Technology's subsidiaries Clou Electronics and Hekang New Energy jointly appeared at the Munich Battery Energy Storage Exhibition and Solar Energy Exhibition
- Guoxin Sichen | Application of ferroelectric memory PB85RS2MC in power battery management, with a capacity of 2M
- Analysis of common faults of frequency converter
- In a head-on competition with Qualcomm, what kind of cockpit products has Intel come up with?
- Dalian Rongke's all-vanadium liquid flow battery energy storage equipment industrialization project has entered the sprint stage before production
- Allegro MicroSystems Introduces Advanced Magnetic and Inductive Position Sensing Solutions at Electronica 2024
- Car key in the left hand, liveness detection radar in the right hand, UWB is imperative for cars!
- After a decade of rapid development, domestic CIS has entered the market
- Aegis Dagger Battery + Thor EM-i Super Hybrid, Geely New Energy has thrown out two "king bombs"
- A brief discussion on functional safety - fault, error, and failure
- In the smart car 2.0 cycle, these core industry chains are facing major opportunities!
- The United States and Japan are developing new batteries. CATL faces challenges? How should China's new energy battery industry respond?
- Murata launches high-precision 6-axis inertial sensor for automobiles
- Ford patents pre-charge alarm to help save costs and respond to emergencies
- New real-time microcontroller system from Texas Instruments enables smarter processing in automotive and industrial applications
- Allwinner V853 NPU demo
- mini Protobuf library
- Statistics of domestic scientific laws
- ISM330DLC three-axis acceleration + three-axis angular velocity sensor package and code
- Altium Designer operation process and brief introduction
- DAC adjusts the output voltage of DCDC chip
- 3 levels and 4 misunderstandings of playing with microcontrollers
- Miniature Alphabet World Clock
- Make a simple lossless music player with STM32F103
- "New Concept Analog Circuit" Series 1, 2