As an engineer, do you know how fast consumer electronic devices operate and how many tasks they can perform per second? The high speed operation of these devices has brought many pleasures, enabling intuitive touch phones and live video streaming, as well as many practical applications, such as driving high-speed data for networking and communication devices.
The increase in performance levels and speeds of electronic devices has brought many challenges to engineers. When designing these devices, safety is a key factor and requires special attention. Electromagnetic interference (EMI) from nearby devices is a major threat to user safety and reliable operation. Electromagnetic Interference I was watching a football game on my HDTV and was about to shoot when I suddenly received a call on my phone and the TV signal immediately went out. However, after hanging up the call, the TV signal came back. This is an example of electromagnetic interference. Every electrical signal is a combination of electric and magnetic fields. Any signal that is finite (or bounded) in the time domain is infinite (or unbounded) in the frequency domain, and vice versa. All electrical systems have signals that carry information, and therefore, they all have specific patterns. These patterns are defined by the communication protocols used by the receiver and transmitter, which can be located close to the chip on the same PCB or as far away as the earth and satellite. Signals with fixed patterns in the time domain have energy distributed over a wide range of frequencies. For example, Figure 1 shows a 125MHz clock signal in the time and frequency domains. In the time domain, this clock signal is periodic, and its energy is distributed over a wide range in the frequency domain. The markers at 125MHz, 375MHz, 625MHz, and 875MHz in the figure show four consecutive high energy points in the frequency domain. The peak energy is stored at the fundamental frequency of 125MHz, which is 10.55dB. In addition, 375MHz, 625MHz, and 875MHz are odd harmonics of the 125MHz clock signal. This energy is a key factor in electromagnetic interference, which can interfere with other systems operating nearby. A system with peak energy at a specific operating frequency is an example of an electromagnetic radiation source. In the example of a cell phone and TV, the radiation source is the cell phone. When watching a football game on an LCD HDTV, the set-top box is tuned to a sports channel in the 54 to 890MHz range. When the phone is in idle mode (i.e. not making a call or sending a text message), it does not transmit data and does not generate radiation. However, when the phone receives an incoming call, it begins communicating with the nearest base station. During the transmission, the phone uses more power and transmits in the GSM band (900MHz), which generates radiation in the adjacent set-top box frequency range (close to 890MHz). Due to this radiation, the set-top box cannot decode the broadcast TV signal. This does not happen in many homes because sufficient margins are taken into account in the operating frequencies and EMI protection of the TV and mobile phones. However, when supporting 4G transmission in the 800MHz range, mobile phone and TV designers will face more EMI challenges. This kind of damage does not pose a great threat when it occurs in consumer devices, but imagine what will happen when Wi-Fi signals interfere with the control operations of hazardous chemical plants? Many accidents in history have been caused by EMI, so the world's leading countries are regulating electronic designs from the perspective of EMI. In addition to EMI radiation, there is also conducted EMI from circuit board wiring, power supplies, capacitive or inductive coupling, which can interfere with system operation and functionality of other devices. Many international regulatory agencies (IEC, CISPR and EN) set the maximum radiation that a system can have, and also define the minimum EMI level that should not affect the system. International standards for EMI are defined based on applications and end equipment, such as: military, consumer, industrial and automotive. High-speed devices are devices driven by high-speed clocks. The main factor affecting EMI is the high-speed clock signal, which is periodic in the time domain. As shown in Figure 2, a 125MHz clock signal has peak energy and strong odd harmonic signals at the fundamental frequency (as shown in Figure 1). Figure 1: Clock signal in the time and frequency domains. Figure 2 shows a spectrum analysis of a 125MHz clock centered on the fundamental frequency. The peak indicates that the energy of the fundamental frequency is -5.29dBm. If the energy of the center frequency is reduced, the radiation caused by the clock signal will also decrease. In a system where the clock signal drives most of the on-board devices, EMI will increase significantly. Spread spectrum technology uses the same concept to improve the system's EMI resistance. Figure 2: Peak energy of a clock signal. Spread spectrum technology In spread spectrum technology, a high-frequency clock signal is modulated by a low frequency. The frequency of the modulating signal is usually 30~120kHz. Due to the modulation, the energy stored in the fundamental frequency will be distributed over a wider frequency range and the peak value will be reduced (as shown in Figure 3). If spread spectrum technology is not used, the peak value of a 125MHz clock signal is -5.29dB. After ±2% spreading, the peak value will be reduced to -13.37dB. Modulation curve, spreading type, and spreading percentage are all important parameters of spread spectrum technology. Figure 3: 125MHz clock after ±2% center spreading. Modulation curve: In simple terms, the modulation signal waveform represents the modulation curve. There are two familiar curves: Linear and Lexmark. Lexmark can reduce the peak value better than Linear. The shape of the Linear curve is similar to a triangle wave. Spread percentage: The peak-to-peak amplitude of the modulated signal represents the spread percentage. The spread percentage represents the deviation from the nominal signal frequency. Spread type: If the nominal signal frequency is at the center of the modulation curve, it is called center spread. If the signal frequency is at the top of the modulation curve, it is called downward spreading. The effectiveness of using spread spectrum technology to reduce peaks depends on the selected spread percentage and the spread curve. The following example shows the corresponding reduction in radiation due to the increase in spread percentage. Case Study In information technology equipment, the CY 25100 clock chip is used to drive FPGA and Ethernet chips (as shown in Figure 4). The reference clock output is 25MHz and has no spreading. The 125MHz signal is generated through an on-chip phase-locked loop and can be a spread spectrum clock . Figure 4: CY25100 application. Initially, the customer used the 125MHz clock output without spreading. According to EU requirements, the equipment needs to meet the EN 55022 standard limits. After testing the equipment prototype, it was found that there were 44dB radiation at multiple multiples of 125MHz, exceeding the 40dB limit of the EN 55022 standard. After some experiments with different spreading percentages, ±2% center spreading at 31.7kHz reduced the overall equipment radiation by 6dB, allowing the system to meet the EN 55022 requirements and provide a 2dB margin. To verify the effect of spread spectrum clocking in terms of EMI, the peak energy of a 125MHz clock was measured in a simple setup with minimal noise using a characterization board (i.e., only the CY 25100 device was on the board). Without spread spectrum, the measured peak value of the clock signal was -5.29dB. After ±2% spreading, the clock peak was reduced to 8dB. Table 1 shows the peak reduction for each spreading percentage. Table 1 : Peak measurements for different spreading percentages. When using spread spectrum clocking, there are significant improvements in EMI radiation. Furthermore, these improvements do not require the time and cost of a prototype or board redesign. Check parameters before using spread spectrum clocking
Jitter: Spreading a high frequency clock signal at a lower frequency increases the clock edge variation over the cycle. This results in higher jitter. The jitter of a spread spectrum clock needs to be measured and the clock receiver can be sure that the added jitter in the spread spectrum clock can be tolerated.
Parts Per Million (PPM) Error: The Parts Per Million (PPM) error parameter is used to measure the accuracy of the clock signal. Due to the percentage of spreading, the clock frequency will be different from the nominal frequency, so the PPM error will increase. For applications with very tight PPM error specifications, it is necessary to ensure that the PPM error is within limits after using spread spectrum.
Spreading a Known Phase-Locked Loop: Assuming an application where a single clock drives multiple clock receiving chips, a zero delay buffer can be used to meet the clock receiving load. If the originally generated clock signal has spread spectrum, it is necessary to verify that the zero delay buffer supports spreading by passing it through the clock receiving end to sufficiently reduce electromagnetic interference. If the zero delay buffer does not support spreading, the input spread will appear as an offset at the clock buffer output. This is called tracking skew and needs to be concerned if the application has tight skew specifications (for example: synchronization applications).
Selecting Spreading Parameters for Specific Applications
Increasing the spread percentage will reduce the peak energy accordingly, but the rate of peak reduction is not constant. As shown in Table 1, when the spread percentage is ±2%, the peak is reduced by 8.08dB ((-13.37)-(-5.29)dB). When the spread percentage is increased to ±2.5%, the peak is reduced by 8.82dB ((-14.11)-(-5.29)dB). Therefore, for further ±0.5% spread increments, less than 1dB of peak reduction can be observed.
Spreading Type (Downward Spreading/Center Spreading): This depends on the highest operating frequency of the clock receiver. If the clock receiver supports ± tolerance of the normal frequency, center spreading or downward spreading can be used. Center spreading can allow the nominal frequency to change in both directions, for example, 25MHz can be changed from 24.75MHz to 25.25MHz after ±1% spreading. Downward spreading only changes the nominal frequency downward, ensuring that the maximum frequency is always the nominal frequency. For example, a 25MHz spread of -1% will change from 24.75MHz to 25MHz. Downward spreading is the right choice when the normal frequency is the highest frequency.
Modulation frequency: Many clock generators support a wide range of modulation frequencies from about 30 to 120kHz. The most common range is between 30 and 60kHz. The modulation frequency can be any frequency in this range as long as these frequencies or their multiples do not interfere with the operation of other systems or devices or couple with them. Modulation
curve: The Lexmark curve can better reduce peaking than the Linear curve. If the clock generator supports the Lexmark curve, then choose it.
In complex system applications that contain multiple data, clock, and address buses that run at different speeds, use different power supplies, and support different communication protocols, using only a specific frequency spread spectrum clock is not enough to fully manage the electromagnetic interference of the system. Designers also need to pay special attention to board design issues (such as crosstalk and ground loops) because there are multiple noise sources. In such a complex system, there may be some protocols that are not optimized for functionality due to PPM requirements or jitter specifications. Spread spectrum clocking can help reduce the overall radiation caused by the clock, but other techniques will be needed to compensate for other data or clock signals that do not support spread spectrum. However, as shown in the case study above, having spread spectrum capability is always an advantage because it reduces the shielding and filtering required for many challenging EMI sources.
Reference address:Using Spread Spectrum Clocking to Reduce Electromagnetic Interference
The increase in performance levels and speeds of electronic devices has brought many challenges to engineers. When designing these devices, safety is a key factor and requires special attention. Electromagnetic interference (EMI) from nearby devices is a major threat to user safety and reliable operation. Electromagnetic Interference I was watching a football game on my HDTV and was about to shoot when I suddenly received a call on my phone and the TV signal immediately went out. However, after hanging up the call, the TV signal came back. This is an example of electromagnetic interference. Every electrical signal is a combination of electric and magnetic fields. Any signal that is finite (or bounded) in the time domain is infinite (or unbounded) in the frequency domain, and vice versa. All electrical systems have signals that carry information, and therefore, they all have specific patterns. These patterns are defined by the communication protocols used by the receiver and transmitter, which can be located close to the chip on the same PCB or as far away as the earth and satellite. Signals with fixed patterns in the time domain have energy distributed over a wide range of frequencies. For example, Figure 1 shows a 125MHz clock signal in the time and frequency domains. In the time domain, this clock signal is periodic, and its energy is distributed over a wide range in the frequency domain. The markers at 125MHz, 375MHz, 625MHz, and 875MHz in the figure show four consecutive high energy points in the frequency domain. The peak energy is stored at the fundamental frequency of 125MHz, which is 10.55dB. In addition, 375MHz, 625MHz, and 875MHz are odd harmonics of the 125MHz clock signal. This energy is a key factor in electromagnetic interference, which can interfere with other systems operating nearby. A system with peak energy at a specific operating frequency is an example of an electromagnetic radiation source. In the example of a cell phone and TV, the radiation source is the cell phone. When watching a football game on an LCD HDTV, the set-top box is tuned to a sports channel in the 54 to 890MHz range. When the phone is in idle mode (i.e. not making a call or sending a text message), it does not transmit data and does not generate radiation. However, when the phone receives an incoming call, it begins communicating with the nearest base station. During the transmission, the phone uses more power and transmits in the GSM band (900MHz), which generates radiation in the adjacent set-top box frequency range (close to 890MHz). Due to this radiation, the set-top box cannot decode the broadcast TV signal. This does not happen in many homes because sufficient margins are taken into account in the operating frequencies and EMI protection of the TV and mobile phones. However, when supporting 4G transmission in the 800MHz range, mobile phone and TV designers will face more EMI challenges. This kind of damage does not pose a great threat when it occurs in consumer devices, but imagine what will happen when Wi-Fi signals interfere with the control operations of hazardous chemical plants? Many accidents in history have been caused by EMI, so the world's leading countries are regulating electronic designs from the perspective of EMI. In addition to EMI radiation, there is also conducted EMI from circuit board wiring, power supplies, capacitive or inductive coupling, which can interfere with system operation and functionality of other devices. Many international regulatory agencies (IEC, CISPR and EN) set the maximum radiation that a system can have, and also define the minimum EMI level that should not affect the system. International standards for EMI are defined based on applications and end equipment, such as: military, consumer, industrial and automotive. High-speed devices are devices driven by high-speed clocks. The main factor affecting EMI is the high-speed clock signal, which is periodic in the time domain. As shown in Figure 2, a 125MHz clock signal has peak energy and strong odd harmonic signals at the fundamental frequency (as shown in Figure 1). Figure 1: Clock signal in the time and frequency domains. Figure 2 shows a spectrum analysis of a 125MHz clock centered on the fundamental frequency. The peak indicates that the energy of the fundamental frequency is -5.29dBm. If the energy of the center frequency is reduced, the radiation caused by the clock signal will also decrease. In a system where the clock signal drives most of the on-board devices, EMI will increase significantly. Spread spectrum technology uses the same concept to improve the system's EMI resistance. Figure 2: Peak energy of a clock signal. Spread spectrum technology In spread spectrum technology, a high-frequency clock signal is modulated by a low frequency. The frequency of the modulating signal is usually 30~120kHz. Due to the modulation, the energy stored in the fundamental frequency will be distributed over a wider frequency range and the peak value will be reduced (as shown in Figure 3). If spread spectrum technology is not used, the peak value of a 125MHz clock signal is -5.29dB. After ±2% spreading, the peak value will be reduced to -13.37dB. Modulation curve, spreading type, and spreading percentage are all important parameters of spread spectrum technology. Figure 3: 125MHz clock after ±2% center spreading. Modulation curve: In simple terms, the modulation signal waveform represents the modulation curve. There are two familiar curves: Linear and Lexmark. Lexmark can reduce the peak value better than Linear. The shape of the Linear curve is similar to a triangle wave. Spread percentage: The peak-to-peak amplitude of the modulated signal represents the spread percentage. The spread percentage represents the deviation from the nominal signal frequency. Spread type: If the nominal signal frequency is at the center of the modulation curve, it is called center spread. If the signal frequency is at the top of the modulation curve, it is called downward spreading. The effectiveness of using spread spectrum technology to reduce peaks depends on the selected spread percentage and the spread curve. The following example shows the corresponding reduction in radiation due to the increase in spread percentage. Case Study In information technology equipment, the CY 25100 clock chip is used to drive FPGA and Ethernet chips (as shown in Figure 4). The reference clock output is 25MHz and has no spreading. The 125MHz signal is generated through an on-chip phase-locked loop and can be a spread spectrum clock . Figure 4: CY25100 application. Initially, the customer used the 125MHz clock output without spreading. According to EU requirements, the equipment needs to meet the EN 55022 standard limits. After testing the equipment prototype, it was found that there were 44dB radiation at multiple multiples of 125MHz, exceeding the 40dB limit of the EN 55022 standard. After some experiments with different spreading percentages, ±2% center spreading at 31.7kHz reduced the overall equipment radiation by 6dB, allowing the system to meet the EN 55022 requirements and provide a 2dB margin. To verify the effect of spread spectrum clocking in terms of EMI, the peak energy of a 125MHz clock was measured in a simple setup with minimal noise using a characterization board (i.e., only the CY 25100 device was on the board). Without spread spectrum, the measured peak value of the clock signal was -5.29dB. After ±2% spreading, the clock peak was reduced to 8dB. Table 1 shows the peak reduction for each spreading percentage. Table 1 : Peak measurements for different spreading percentages. When using spread spectrum clocking, there are significant improvements in EMI radiation. Furthermore, these improvements do not require the time and cost of a prototype or board redesign. Check parameters before using spread spectrum clocking
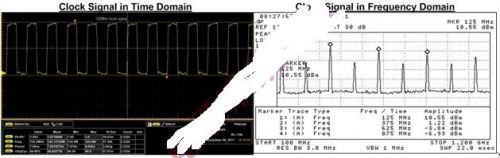

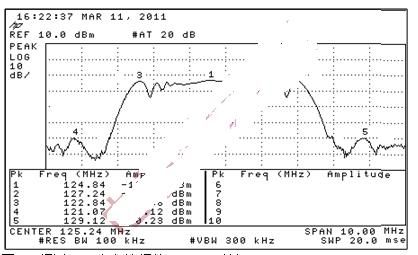
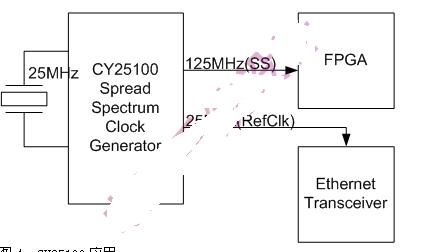
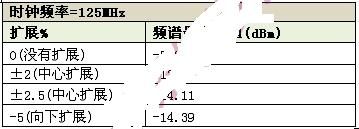
Jitter: Spreading a high frequency clock signal at a lower frequency increases the clock edge variation over the cycle. This results in higher jitter. The jitter of a spread spectrum clock needs to be measured and the clock receiver can be sure that the added jitter in the spread spectrum clock can be tolerated.
Parts Per Million (PPM) Error: The Parts Per Million (PPM) error parameter is used to measure the accuracy of the clock signal. Due to the percentage of spreading, the clock frequency will be different from the nominal frequency, so the PPM error will increase. For applications with very tight PPM error specifications, it is necessary to ensure that the PPM error is within limits after using spread spectrum.
Spreading a Known Phase-Locked Loop: Assuming an application where a single clock drives multiple clock receiving chips, a zero delay buffer can be used to meet the clock receiving load. If the originally generated clock signal has spread spectrum, it is necessary to verify that the zero delay buffer supports spreading by passing it through the clock receiving end to sufficiently reduce electromagnetic interference. If the zero delay buffer does not support spreading, the input spread will appear as an offset at the clock buffer output. This is called tracking skew and needs to be concerned if the application has tight skew specifications (for example: synchronization applications).
Selecting Spreading Parameters for Specific Applications
Increasing the spread percentage will reduce the peak energy accordingly, but the rate of peak reduction is not constant. As shown in Table 1, when the spread percentage is ±2%, the peak is reduced by 8.08dB ((-13.37)-(-5.29)dB). When the spread percentage is increased to ±2.5%, the peak is reduced by 8.82dB ((-14.11)-(-5.29)dB). Therefore, for further ±0.5% spread increments, less than 1dB of peak reduction can be observed.
Spreading Type (Downward Spreading/Center Spreading): This depends on the highest operating frequency of the clock receiver. If the clock receiver supports ± tolerance of the normal frequency, center spreading or downward spreading can be used. Center spreading can allow the nominal frequency to change in both directions, for example, 25MHz can be changed from 24.75MHz to 25.25MHz after ±1% spreading. Downward spreading only changes the nominal frequency downward, ensuring that the maximum frequency is always the nominal frequency. For example, a 25MHz spread of -1% will change from 24.75MHz to 25MHz. Downward spreading is the right choice when the normal frequency is the highest frequency.
Modulation frequency: Many clock generators support a wide range of modulation frequencies from about 30 to 120kHz. The most common range is between 30 and 60kHz. The modulation frequency can be any frequency in this range as long as these frequencies or their multiples do not interfere with the operation of other systems or devices or couple with them. Modulation
curve: The Lexmark curve can better reduce peaking than the Linear curve. If the clock generator supports the Lexmark curve, then choose it.
In complex system applications that contain multiple data, clock, and address buses that run at different speeds, use different power supplies, and support different communication protocols, using only a specific frequency spread spectrum clock is not enough to fully manage the electromagnetic interference of the system. Designers also need to pay special attention to board design issues (such as crosstalk and ground loops) because there are multiple noise sources. In such a complex system, there may be some protocols that are not optimized for functionality due to PPM requirements or jitter specifications. Spread spectrum clocking can help reduce the overall radiation caused by the clock, but other techniques will be needed to compensate for other data or clock signals that do not support spread spectrum. However, as shown in the case study above, having spread spectrum capability is always an advantage because it reduces the shielding and filtering required for many challenging EMI sources.
Previous article:Bringing sensorless BLDC motor control to low-cost applications
Next article:Using Spread Spectrum Clocking to Reduce Electromagnetic Interference
- Popular Resources
- Popular amplifiers
Latest Industrial Control Articles
- Molex leverages SAP solutions to drive smart supply chain collaboration
- Pickering Launches New Future-Proof PXIe Single-Slot Controller for High-Performance Test and Measurement Applications
- CGD and Qorvo to jointly revolutionize motor control solutions
- Advanced gameplay, Harting takes your PCB board connection to a new level!
- Nidec Intelligent Motion is the first to launch an electric clutch ECU for two-wheeled vehicles
- Bosch and Tsinghua University renew cooperation agreement on artificial intelligence research to jointly promote the development of artificial intelligence in the industrial field
- GigaDevice unveils new MCU products, deeply unlocking industrial application scenarios with diversified products and solutions
- Advantech: Investing in Edge AI Innovation to Drive an Intelligent Future
- CGD and QORVO will revolutionize motor control solutions
MoreSelected Circuit Diagrams
MorePopular Articles
- Innolux's intelligent steer-by-wire solution makes cars smarter and safer
- 8051 MCU - Parity Check
- How to efficiently balance the sensitivity of tactile sensing interfaces
- What should I do if the servo motor shakes? What causes the servo motor to shake quickly?
- 【Brushless Motor】Analysis of three-phase BLDC motor and sharing of two popular development boards
- Midea Industrial Technology's subsidiaries Clou Electronics and Hekang New Energy jointly appeared at the Munich Battery Energy Storage Exhibition and Solar Energy Exhibition
- Guoxin Sichen | Application of ferroelectric memory PB85RS2MC in power battery management, with a capacity of 2M
- Analysis of common faults of frequency converter
- In a head-on competition with Qualcomm, what kind of cockpit products has Intel come up with?
- Dalian Rongke's all-vanadium liquid flow battery energy storage equipment industrialization project has entered the sprint stage before production
MoreDaily News
- Allegro MicroSystems Introduces Advanced Magnetic and Inductive Position Sensing Solutions at Electronica 2024
- Car key in the left hand, liveness detection radar in the right hand, UWB is imperative for cars!
- After a decade of rapid development, domestic CIS has entered the market
- Aegis Dagger Battery + Thor EM-i Super Hybrid, Geely New Energy has thrown out two "king bombs"
- A brief discussion on functional safety - fault, error, and failure
- In the smart car 2.0 cycle, these core industry chains are facing major opportunities!
- The United States and Japan are developing new batteries. CATL faces challenges? How should China's new energy battery industry respond?
- Murata launches high-precision 6-axis inertial sensor for automobiles
- Ford patents pre-charge alarm to help save costs and respond to emergencies
- New real-time microcontroller system from Texas Instruments enables smarter processing in automotive and industrial applications
Guess you like
- ARM's strategic layout in the field of Internet of Things
- BearPi-HM Nano Development Board Review 1 Getting Started with Program Development
- I have some doubts about SensorTile.box
- A novice needs help. When drawing PCB manual wiring in AD13.4, why can't I see the trace of the wiring before the wiring is completed?
- What are the important techniques for PCB wiring?
- Naming of Cadence Allegro 17.2 built-in pads
- A precision rectification experiment
- Video: Talking about TI CC2650
- How stable is RT-Thread?
- How to improve the hardware and software architecture of embedded minimum systems?