Central topics:
Basic relationship of PFC continuous operation mode of boost power circuit
Critical Continuous Boost Inductor Design
Usually, there are three operating modes of PFC in boost power circuit: continuous, critical continuous and discontinuous mode. The control method is that the input current tracks the input voltage. The continuous mode has peak current control, average current control and hysteresis control. This article introduces the basic relationship of PFC continuous operating mode of boost power circuit and critical continuous boost inductor design.
Basic relations of continuous mode
1. Determine the output voltage Uo
The input grid voltage generally has a certain variation range (Uin±Δ%). In order for the input current to track the input voltage well, the output voltage of the Boost level should be higher than the peak value of the highest input voltage. However, because the power withstand voltage is determined by the output voltage, the output voltage is generally 1.05~1.1 times the highest input peak voltage. For example, the input voltage is 220V, 50Hz AC, the variation range is 20% of the rated value (Δ=20), and the highest peak voltage is 220×1.2×1.414=373.45V. The output voltage can be selected from 390~410V.
2. Determine the maximum input current
The inductor should avoid saturation at maximum current. Maximum AC input current occurs when the input voltage is minimum and the output power is maximum.
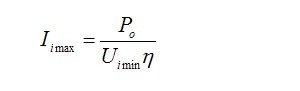
Where: Uimin – minimum input voltage; η-Boost stage efficiency, usually above 95%.
3. Determine the operating frequency
It is determined by factors such as power devices, efficiency and power level. For example, if the output power is 1.5kW, the power tube is MOSFET, and the switching frequency is 70~100kHz.
4. Determine the maximum duty cycle at the lowest input voltage peak
Because the relationship between the output Uo and input Uin of the continuous mode Boost converter is:
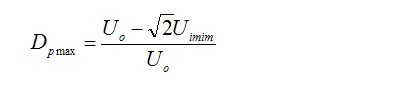
It can be seen from the above formula that if Uo is selected to be lower, the corresponding duty cycle at the highest input voltage peak is very small. Due to the switching time limitation of the power switch (otherwise the switching frequency is reduced), the input current may not be able to track the input voltage, resulting in an increase in the THD of the input current.
5. Calculate the required inductance
To ensure current continuity, the Boost inductor should be larger than
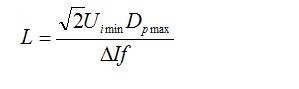
Among them: k=0.15~0.2.
6. Selecting the core size using the AP method
According to the law of electromagnetic induction, the effective cross-sectional area of the magnetic core

If the inductor is linear, we have

Because the DC component of the boost inductor is large, the core loss is less than the copper loss, and the saturation flux density limits the maximum value. To ensure that the core is not saturated at the maximum input current, there should be

Therefore, the area product

Where kw = 0.3~0.5 window filling factor, also known as window utilization factor. B < B/(1+k). Select the core accordingly.
Recommended related articles:
Design of parasitic inductance meter based on DDSApplication of LCR meter in impedance measurementAdvantages of coupled inductor SEPIC converterLecture 4: Single-stage isolated power factor correctionLED driverA brief discussion on static electricity and static electricity protection in the electronic manufacturing processCommon mode inductorCharacteristics of inductorCalculation of inductor Q valueCommon inductor calculation formulaWorking principle of PFC
When the output power is above 1kW, air-gap cores are generally used. The toroidal magnetic powder cores are expensive, difficult to process, and costly. However, the magnetic flux at the edge of the air-gap core near the air gap passes through the coil, causing additional losses, which should be noted in the process.
7. Calculate the number of turns

Critical Continuous Boost Inductor Design
1. Critical Continuous Features
The boost power switch is turned on at zero current, and the inductor current rises linearly. When the peak current reaches the reference current (sine wave) being tracked, the switch is turned off, and the inductor current drops linearly. When the inductor current drops to zero, the switch is turned on again. If the sine wave is completely tracked, according to the law of electromagnetic induction,
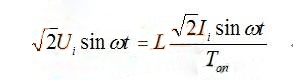
or

Where: Ui, Ii are the effective values of input voltage and current. When the input voltage and input power are constant, Ton is a constant. When the output power and inductance are constant, the conduction time Ton is inversely proportional to the square of the input voltage Ui.
2. Determine the output voltage
The on-time volt-seconds of the inductor should be equal to the off-time volt-seconds:
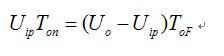
but

The switching cycle is

It can be seen that the output voltage Uo must be greater than the input voltage Uip. If the output voltage is close to the input voltage, the cut-off time is much longer than the on-time near the peak of the input voltage, and the switching cycle is very long, that is, the frequency is very low.
If we first determine that the on-time corresponding to the lowest input voltage (Uimin) is TonL, the on-time corresponding to the highest input voltage (Uimax) is
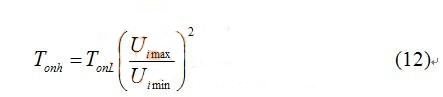
According to equations (11) and (12), the relationship between the switching period (frequency) and different voltage ratios can be obtained.
For example, assuming that the on-time is 10μs, 1.414Uimin/Uo=0.65, if the input voltage changes within the range of ±20%, the minimum input voltage is 220×0.8, and the output voltage is Uo =1.414×220×0.8/0.65=383V. The period is 10/0.35=28.57μs, and the frequency is 35kHz. At 15°, the period is 12μs, which is equivalent to a switching frequency of 83kHz. At the highest input voltage, the highest voltage on-time Tonh=(0.8/1.2)2×TonL=4.444μs is obtained from formula (12), and the switching period at the peak is T=Tonh/(1-1.414×1.2×220/383)=176μs, which is equivalent to a switching frequency of 5.66kHz.
If we. The output voltage is increased to 410V, the switching period is 25.45μs at the lowest input voltage and the switching frequency is 39.3kHz. At 15°, it is 11.864μs and the switching period is 84.5kHz. When the input voltage peak is the highest, the period is 49.2μs and the switching frequency is 20.3kHz. The frequency variation range is greatly reduced. Even at the zero crossing of the input voltage, the cut-off time approaches zero and the switching frequency is about 100kHz. The highest frequency is only 5 times the lowest frequency. At the output voltage of 383V, it is 18 times.
From the above calculations, we can see that increasing the output voltage will reduce the switching frequency variation range, which is beneficial to output filtering. However, the power tube and rectifier diode require higher voltage ratings, and the conduction loss and switching loss increase. Therefore, for 220V±20% AC input, the output voltage is generally selected to be around 410V. For 110V±20% AC input, the output voltage is selected to be 210V.
3. Maximum peak current
The maximum peak current in the inductor is 1 times the peak current

4. Determine the inductance
To avoid audio noise, the switching frequency should be above 20kHz within the input voltage range. From the above analysis, we can see that the switching frequency is lowest at the highest input voltage peak. Therefore, it is assumed that the switching period at the highest input voltage peak is 50μs. From formula (11), we can get

The minimum input voltage on-time is obtained from formula (12):

According to formula (8), we can get

5. Select the core
Because the on-time is inversely proportional to the square of the input voltage, the core size should be selected at the lowest voltage just enough to avoid saturation at the lowest input voltage peak.

Where: N is the number of turns of the inductor coil; Ae is the effective cross-sectional area of the magnetic core; Bm < Bs (100) is the maximum magnetic flux density. To reduce losses, 70% of the saturation magnetic induction is selected.
The cross-sectional area of the entire window copper

Substituting equation (17) into (16), we can get

Use AP method to select core size.
6. Calculate the number of coil turns
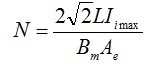
7. Coil wire cross-sectional area
Example: Input 220V±20%, output power 200W, critical continuous. Assume the efficiency is 0.95.
Solution: The maximum input current is
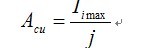
The peak current is
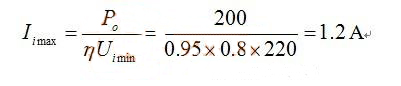
Assume the output voltage is 410V, and the minimum frequency is 20kHz when the input voltage is the highest. That is, the period is 50μs, so the conduction time is
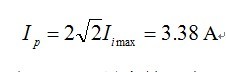
If magnetic powder core is used, choose Sendust core. LI2=1.48×3.382×10-3=16.9mJ, choose 77439. The effective magnetic permeability is 60, its inductance coefficient AL=135nH, and the number of turns required for inductance 1.48mH is N=105 turns.
The average magnetic path length of 77439 is l = 10.74 cm, and the magnetic field strength (Oe) is

From the figure, we can see that the magnetic permeability is 60, H=21Oe, and the magnetic permeability drops to 90%. In order to maintain a given inductance at a given peak current, the number of turns needs to be increased to N turns, and 111 turns are selected.
At this time, the magnetic field strength H = 111 × 21/105 = 22.2Oe, μ drops to 0.88, and the inductance

The design requirements are met. The switching frequency is increased by about 1% at the highest voltage. It should be noted that the average current is used here. The actual peak current is twice as large, and the maximum magnetic field strength is twice as large. From the figure, the magnetic permeability drops to 80%, and the magnetic field strength increases from zero to the maximum. The average magnetic permeability is (0.8+1)/2=0.9, which is close to 0.88.
Select the current density j=5A/mm2 and the wire size is
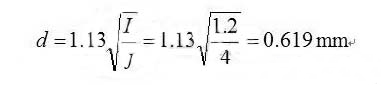
Select d=0.63mm, d'=0.70mm, and cross-sectional area Acu=0.312mm2.
Calculate the window utilization coefficient. Aw=4.27cm2, then
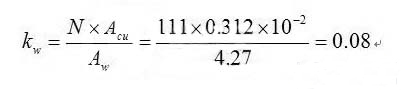
77439 Sendust powder core has an outer diameter of OD = 47.6 mm and an inner diameter of ID = 23.3 mm. Consider the first layer
Nm1=(π(ID-0.5d'-0.05)/1.05d')-1=96.9, actual 96 turns.
The second layer only needs 15 turns.
Previous article:Three-phase energy meter solution based on STM32 of CORTEX
Next article:Application of RFID Technology in Highway Toll Collection System
- Popular Resources
- Popular amplifiers
- Molex leverages SAP solutions to drive smart supply chain collaboration
- Pickering Launches New Future-Proof PXIe Single-Slot Controller for High-Performance Test and Measurement Applications
- CGD and Qorvo to jointly revolutionize motor control solutions
- Advanced gameplay, Harting takes your PCB board connection to a new level!
- Nidec Intelligent Motion is the first to launch an electric clutch ECU for two-wheeled vehicles
- Bosch and Tsinghua University renew cooperation agreement on artificial intelligence research to jointly promote the development of artificial intelligence in the industrial field
- GigaDevice unveils new MCU products, deeply unlocking industrial application scenarios with diversified products and solutions
- Advantech: Investing in Edge AI Innovation to Drive an Intelligent Future
- CGD and QORVO will revolutionize motor control solutions
- Innolux's intelligent steer-by-wire solution makes cars smarter and safer
- 8051 MCU - Parity Check
- How to efficiently balance the sensitivity of tactile sensing interfaces
- What should I do if the servo motor shakes? What causes the servo motor to shake quickly?
- 【Brushless Motor】Analysis of three-phase BLDC motor and sharing of two popular development boards
- Midea Industrial Technology's subsidiaries Clou Electronics and Hekang New Energy jointly appeared at the Munich Battery Energy Storage Exhibition and Solar Energy Exhibition
- Guoxin Sichen | Application of ferroelectric memory PB85RS2MC in power battery management, with a capacity of 2M
- Analysis of common faults of frequency converter
- In a head-on competition with Qualcomm, what kind of cockpit products has Intel come up with?
- Dalian Rongke's all-vanadium liquid flow battery energy storage equipment industrialization project has entered the sprint stage before production
- Allegro MicroSystems Introduces Advanced Magnetic and Inductive Position Sensing Solutions at Electronica 2024
- Car key in the left hand, liveness detection radar in the right hand, UWB is imperative for cars!
- After a decade of rapid development, domestic CIS has entered the market
- Aegis Dagger Battery + Thor EM-i Super Hybrid, Geely New Energy has thrown out two "king bombs"
- A brief discussion on functional safety - fault, error, and failure
- In the smart car 2.0 cycle, these core industry chains are facing major opportunities!
- The United States and Japan are developing new batteries. CATL faces challenges? How should China's new energy battery industry respond?
- Murata launches high-precision 6-axis inertial sensor for automobiles
- Ford patents pre-charge alarm to help save costs and respond to emergencies
- New real-time microcontroller system from Texas Instruments enables smarter processing in automotive and industrial applications
- Tms320VC5502 and isp1581 high-speed data acquisition solution
- 2019FPGA Employment Competition and Guidance
- What kind of activities do you hope the RF/Radio Frequency section will carry out? Please leave a message in the thread.
- Oscilloscope usage tips you don't know
- Free Trial | Keysight Accelerates Signal Integrity and Power Integrity Testing
- Learning PLC technology is super easy
- Advantages of modules
- EEWORLD University Hall----Live Replay: What to listen to when stuck in traffic? New generation of in-car audio systems and software-defined cars
- Beautiful Pico Quad Keyboard
- Summary of msp430 built-in functions