SMBus Temperature Sensor IC
Commercially available SMBus temperature sensor ICs include sensors that measure the ambient temperature around the IC and devices that support one or more external sensors (i.e., some inexpensive triodes connected to diodes).
The SMBu communication interface provides a simple connection to the system microcontroller, and the measurement parameters of the temperature sensor can be configured through writable registers.
|
Figure 1: The relationship between temperature and fan speed set by the control circuit in this article. |
Many SMBus temperature sensors have one or two outputs that activate (typically go low) when the temperature exceeds a certain limit that is programmed into the IC register. Design engineers can expect typical sensor accuracy of 1 to 3°C and resolution as fine as 1/8°C.
Common drive voltages for most DC brushless fans are +5V and +12V dc . Fans running at full speed can produce annoying noise, so it's important to reduce the fan speed as much as possible. When running a DC fan at reduced voltage and as the fan ages, the fan starting voltage becomes a limiting factor as bearing wear causes the required starting voltage to increase.
The actual operating voltage range of fans varies widely. One manufacturer's fan rated for +5V may start with 2V dc , while another fan of the same size and specification may require 4Vdc to start. When the selected fan operates at a voltage lower than the manufacturer's rating, it is critical to characterize the fan and add some margin to account for wear and fan-to-fan differences.
|
Figure 2: Two transistors implement 5V fan drive. |
intelligent control
1. Two triodes realize 5V fan drive:
The circuit shown in Figure 2 is useful for +3.3V and +5V powered fan products. When the temperature falls below the two limit settings, the open-drain outputs Out1 and Out2 are set high, causing R1 and R2 to pull high the gates of the P-channel FETs Q1 and Q2, turning them off. When the temperature exceeds limit 1 in Figure 1, Out1 goes low, turning on Q1 and applying approximately 3V to the fan through Schottky diode D1. When Out2 goes low, Q2 turns on and applies 5V to the fan. D2 ensures that the 5V supply does not reverse the 3.3V supply through Q1.
This circuit is very efficient because the triode base draws no current, it acts as a switch, connecting the fan directly to the power rail. Choosing a P-channel FET with Ron < 0.75Ω @ V gs =3V keeps voltage drop and power consumption low. The low power consumption allows the fan to use a small-profile SOT-23 device to achieve a rated current of 400mA@5V.
2. Single transistor realizes 5V fan drive
|
Figure 3: A single transistor realizes 5V fan drive. |
The circuit shown in Figure 3 uses a PNP transistor to control the fan's three speeds: stop, medium speed, and high speed. When the temperature is lower than the two limit settings, both Out1 and Out2 become high. No current flows through the base of Q1, so it is off and the fan voltage is 0V.
When the temperature exceeds limit 1, Out1 is driven low and the resistor divider R1/R2 sets the voltage at the base of Q1 to 1.8V. Since the base voltage is V be , the emitter voltage will be 0.7V higher than V be , resulting in a fan voltage of 2.5V (50% of full scale voltage).
When Out2 goes low, it pulls the base of Q1 down to ground level, and the base current is limited by the maximum absorption capacity of the IC output, which is typically 6-8mA@V ol =0.4V. Due to the limited base current, the gain of Q1 should be greater than 100 to ensure minimum voltage drop and strong transistor driving capability. The voltage drop between the output device and Q1 limits the maximum fan voltage to 4.1V (82% of full-scale voltage).
3. Single transistor realizes 12V fan drive
The circuit shown in Figure 4 is slightly different from a single triode circuit and can drive a fan at low, medium, and high speeds. This arrangement allows the 12V fan to be controlled by an IC with a maximum output voltage of 5V.
|
Figure 4: A single transistor realizes 12V fan drive. |
When both outputs of the IC are high, low speed is set by resistors R1 and R3. The R1/R3 voltage divider sets the Q1 base voltage to 5.0V, providing approximately 6.3V to the fan (52% of full-scale voltage). Medium speed is achieved when Out1 goes low, sinking current through R2 to set the base voltage to 2.5V and the fan voltage to 8.8V (73% of full scale voltage). When Out2 goes low, the high-speed voltage reaches 11.1V (92% of full-scale voltage).
Summary of this article
The SMBus temperature sensor can be used to control the three speeds of the fan. The system design has high flexibility and low cost. Fan speeds can be set for silent operation by using the lower of the two fan speeds for normal and above-average power consumption scenarios. The top speed can be dedicated to operation in extreme temperature conditions, where cooling takes precedence over quiet operation.
Previous article:Design of remote monitoring system based on CDMA 1X
Next article:Method of using 555 timer to form a white LED voltage regulator
Recommended ReadingLatest update time:2024-11-16 23:38
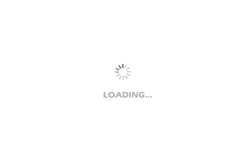
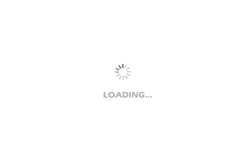
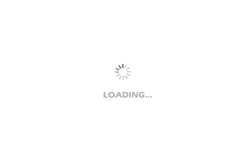
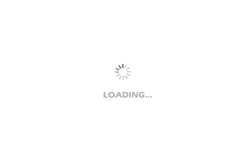
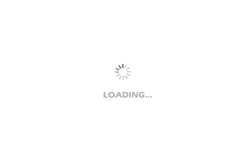
- Popular Resources
- Popular amplifiers
-
西门子S7-12001500 PLC SCL语言编程从入门到精通 (北岛李工)
-
New Energy Vehicle Detection and Diagnosis Experiment (Edited by Mao Caiyun, Zhou Xien, and Long Jiwen)
-
Virtualization Technology Practice Guide - High-efficiency and low-cost solutions for small and medium-sized enterprises (Wang Chunhai)
-
ESP32-S3 source code
- Molex leverages SAP solutions to drive smart supply chain collaboration
- Pickering Launches New Future-Proof PXIe Single-Slot Controller for High-Performance Test and Measurement Applications
- CGD and Qorvo to jointly revolutionize motor control solutions
- Advanced gameplay, Harting takes your PCB board connection to a new level!
- Nidec Intelligent Motion is the first to launch an electric clutch ECU for two-wheeled vehicles
- Bosch and Tsinghua University renew cooperation agreement on artificial intelligence research to jointly promote the development of artificial intelligence in the industrial field
- GigaDevice unveils new MCU products, deeply unlocking industrial application scenarios with diversified products and solutions
- Advantech: Investing in Edge AI Innovation to Drive an Intelligent Future
- CGD and QORVO will revolutionize motor control solutions
- Innolux's intelligent steer-by-wire solution makes cars smarter and safer
- 8051 MCU - Parity Check
- How to efficiently balance the sensitivity of tactile sensing interfaces
- What should I do if the servo motor shakes? What causes the servo motor to shake quickly?
- 【Brushless Motor】Analysis of three-phase BLDC motor and sharing of two popular development boards
- Midea Industrial Technology's subsidiaries Clou Electronics and Hekang New Energy jointly appeared at the Munich Battery Energy Storage Exhibition and Solar Energy Exhibition
- Guoxin Sichen | Application of ferroelectric memory PB85RS2MC in power battery management, with a capacity of 2M
- Analysis of common faults of frequency converter
- In a head-on competition with Qualcomm, what kind of cockpit products has Intel come up with?
- Dalian Rongke's all-vanadium liquid flow battery energy storage equipment industrialization project has entered the sprint stage before production
- Allegro MicroSystems Introduces Advanced Magnetic and Inductive Position Sensing Solutions at Electronica 2024
- Car key in the left hand, liveness detection radar in the right hand, UWB is imperative for cars!
- After a decade of rapid development, domestic CIS has entered the market
- Aegis Dagger Battery + Thor EM-i Super Hybrid, Geely New Energy has thrown out two "king bombs"
- A brief discussion on functional safety - fault, error, and failure
- In the smart car 2.0 cycle, these core industry chains are facing major opportunities!
- The United States and Japan are developing new batteries. CATL faces challenges? How should China's new energy battery industry respond?
- Murata launches high-precision 6-axis inertial sensor for automobiles
- Ford patents pre-charge alarm to help save costs and respond to emergencies
- New real-time microcontroller system from Texas Instruments enables smarter processing in automotive and industrial applications
- In low temperature environment, the battery level of the device is displayed as 90%, but when it is brought to normal temperature, the battery level drops rapidly until it shuts down. What is the principle behind this?
- Qorvo launches payload products into space to commemorate its 5th anniversary, speaking with strength!
- Temperature measurement in the electronics and semiconductor industries
- EEWORLD University ---- Linux driver strategy and framework
- Phase shifter classification and working principle (Part 1)
- 【RT-Thread Reading Notes】10. RT-Thread Learning Chapter 17 Reading Notes
- [TI recommended course] #Live replay: Application of TI millimeter wave sensors in smart home#
- EEWORLD University ---- Live playback: The most important component of the analog world - Signal chain and power supply: Amplifier special
- Help, how to calculate the voltage gain of an amplifier circuit?
- Xilinx XPE Power Estimation Software Setup Advisory