LED products have been gradually becoming the favorites in the field of optoelectronic display with their advantages of low consumption, long life and good weather resistance. Especially in the field of solid-state lighting in recent years, high-power LEDs have been increasingly favored by the industry.
LED products are divided into many varieties: dot matrix digital tube, lamp, SMD, top view, side view, high power, etc., but these varieties have one thing in common, that is, they all have a non-airtight package combination of resin and bracket. Therefore, they are all moisture-sensitive components, and moisture-sensitive components are exposed to the elevated temperature environment during reflow soldering. The moisture inside the surface mount device (SMD) trapped in the resin will produce enough steam pressure to damage or destroy the component. Common failure modes include separation of resin from the inside of the chip or lead frame (delamination), wire damage, chip damage, and internal cracks that do not extend to the surface of the component. In some extreme cases, cracks will extend to the surface of the component; the most serious case is the swelling and bursting of the component (called "popcorn" effect). IPC - The American Electronics Industry Association has formulated and published IPC-M-109, Moisture-Sensitive Component Standard and Guide Manual. It includes the following seven documents:
IPC/JEDEC J-STD-020 Moisture/Reflow Sensitivity Classification of Plastic Integrated Circuit (IC) SMDs
IPC/JEDEC J-STD-033 Standard for Handling, Packaging, Shipping and Use of Moisture/Reflow Sensitive SMDs
IPC/JEDEC J-STD-035 Acoustic Microscope Inspection Method for Non-hermetic Packaged Components
IPC-9501 Simulation Method for Assembly Process of Printed Wiring Boards (PWBs) for Evaluating Electronic Components (Pre-processed IC Components)
IPC-9502 PWB Assembly Soldering Process Guide for Electronic Components
IPC-9503 Moisture Sensitivity Classification of Non-IC Components
IPC-9504 Simulation Method for Assembly Process of Evaluating Non-IC Components (Pre-processed Non-IC Components)
Among them, IPC/JEDEC J-STD-020 defines the classification procedure for moisture-sensitive components, that is, non-hermetic packages made of moisture-permeable materials such as plastics and resins. The procedure includes exposure to reflow soldering temperatures followed by detailed visual inspection, scanning acoustic microscopy, cross-sectioning and electrical testing. IPC/JEDEC J-STD-020 also divides moisture-sensitive components into eight levels, namely:
Level 1 - ≤ 30°C / 85% RH Unlimited floor life
Level 2 - ≤ 30°C / 60% RH One year floor life
Level 2a - ≤ 30°C / 60% RH Four weeks floor life
Level 3 - ≤ 30°C / 60% RH 168 hours floor life
Level 4 - ≤ 30°C / 60% RH 72 hours floor life
Level 5 - ≤ 30°C / 60% RH 48 hours floor life
Level 5a - ≤ 30°C / 60% RH 24 hours floor life
Level 6 - ≤30°C / 60% RH 72 hours floor life (For Level 6, components must be baked before use and must be reflowed within the time limit specified on the moisture sensitivity notice label).
LEDs are generally classified into three levels: 2a, 3, and 4. SMD is classified into level 3, and top view and side view are classified into level 4. Therefore, the corresponding production process time must be controlled within the required range.
At present, it is a common problem in the industry that SMD products, including top view and side view, have dead lights during reflow soldering, and moisture control is also an effective way to solve this problem.
1. Shorten the product process time and strictly control the time the product is placed in the air after molding according to the grade requirements.
2. Perform baking and dehumidification treatment on hygroscopic raw materials before production. The baking time/temperature should be determined according to the characteristics of the material.
3. Control the temperature/humidity at the production site and place the semi-finished products in a moisture-proof cabinet.
4. Perform baking and dehumidification treatment on the products.
5. Vacuum pack the products.
6. Perform baking and dehumidification treatment on the products that are placed for a long time before use.
Among them, product packaging and baking, IPC/JEDEC J-STD-033 provides recommended methods for handling, packaging, shipping and baking moisture-sensitive components. The focus is on packaging and preventing moisture absorption - baking or dehumidification should be the final method used after excessive exposure occurs. Dry packaging involves sealing moisture-sensitive components in moisture-proof bags together with desiccant, humidity indicator cards and moisture-sensitive warning labels. The labels contain information about shelf life within a specific temperature and humidity range, exposure time after opening the bag, details about when baking is required, baking procedures, and the sealing date of the bag. Level 1. Drying before bagging is optional, bagging and desiccant are optional, labeling is not required, unless the component is classified to a reflow temperature of 235°C. Level 2. Drying before bagging is optional, bagging and desiccant are required, labeling is required. Level 2a ~ 5a. Drying before bagging is required, bagging and desiccant are required, labeling is required. Level 6. Drying before bagging is optional, bagging and desiccant are optional, labeling is required.
Of course, due to the packaging bag, we can use two methods to dry the product: desiccant or baking.
1. Dehumidify at room temperature. Use standard dry packaging methods or a drying oven that can maintain 25°C±5°C and humidity below 10%RH for 5 times the air exposure time to restore the original shop life.
2. Baking. There are some recommended baking methods for packaging before and after drying based on grade and packaging thickness. Pre-baking is used to prepare components for dry packaging, and post-baking is used to restore components after floor life. Please refer to and follow the recommended baking time/temperature in J-STD-033. Baking temperature may reduce the solderability of the pad by oxidizing the pad or causing excessive intermetallic growth; in addition, baking dehumidification is necessary if the product is packaged in tape and reel packaging, so the effect of baking on the sealing of the upper and lower tapes of the package must be considered.
IPC's pre-baking recommendations before dry packaging are:
1. Before packaging, package thickness is less than or equal to 1.4mm: for 2a ~5a levels, the baking time range is 8~28 hours at 125°C, or 4~14 hours at 150°C. Package thickness is less than or equal to 2.0mm: for 2a ~5a levels, the baking time range is 23~48 hours at 125°C, or 11~24 hours at 150°C.
2. After the floor life expires, package thickness is less than or equal to 1.4mm: for 2a ~5a levels, the baking time range is 4~14 hours at 125°C, or 5~9 days at 40°C. Package thickness is less than or equal to 2.0mm: for 2a ~5a levels, the baking time range is 18~48 hours at 125°C, or 21~68 days at 40°C.
3. The author also conducted several tests on tape-and-reel packaging products, and the baked SMD products were first placed at 30°C/80% RH for more than 336 hours.
Previous article:Comparison between LED and CCFL
Next article:Intelligent control technology characteristics and classification of LED landscape lighting
Recommended ReadingLatest update time:2024-11-16 19:44
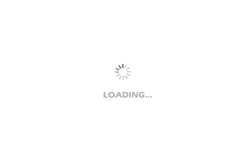
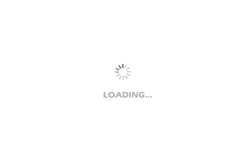
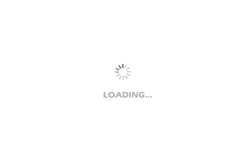
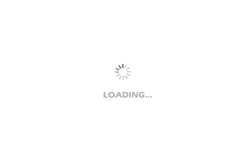
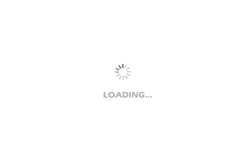
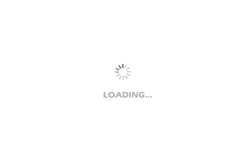
- Popular Resources
- Popular amplifiers
- MathWorks and NXP Collaborate to Launch Model-Based Design Toolbox for Battery Management Systems
- STMicroelectronics' advanced galvanically isolated gate driver STGAP3S provides flexible protection for IGBTs and SiC MOSFETs
- New diaphragm-free solid-state lithium battery technology is launched: the distance between the positive and negative electrodes is less than 0.000001 meters
- [“Source” Observe the Autumn Series] Application and testing of the next generation of semiconductor gallium oxide device photodetectors
- 采用自主设计封装,绝缘电阻显著提高!ROHM开发出更高电压xEV系统的SiC肖特基势垒二极管
- Will GaN replace SiC? PI's disruptive 1700V InnoMux2 is here to demonstrate
- From Isolation to the Third and a Half Generation: Understanding Naxinwei's Gate Driver IC in One Article
- The appeal of 48 V technology: importance, benefits and key factors in system-level applications
- Important breakthrough in recycling of used lithium-ion batteries
- Innolux's intelligent steer-by-wire solution makes cars smarter and safer
- 8051 MCU - Parity Check
- How to efficiently balance the sensitivity of tactile sensing interfaces
- What should I do if the servo motor shakes? What causes the servo motor to shake quickly?
- 【Brushless Motor】Analysis of three-phase BLDC motor and sharing of two popular development boards
- Midea Industrial Technology's subsidiaries Clou Electronics and Hekang New Energy jointly appeared at the Munich Battery Energy Storage Exhibition and Solar Energy Exhibition
- Guoxin Sichen | Application of ferroelectric memory PB85RS2MC in power battery management, with a capacity of 2M
- Analysis of common faults of frequency converter
- In a head-on competition with Qualcomm, what kind of cockpit products has Intel come up with?
- Dalian Rongke's all-vanadium liquid flow battery energy storage equipment industrialization project has entered the sprint stage before production
- Allegro MicroSystems Introduces Advanced Magnetic and Inductive Position Sensing Solutions at Electronica 2024
- Car key in the left hand, liveness detection radar in the right hand, UWB is imperative for cars!
- After a decade of rapid development, domestic CIS has entered the market
- Aegis Dagger Battery + Thor EM-i Super Hybrid, Geely New Energy has thrown out two "king bombs"
- A brief discussion on functional safety - fault, error, and failure
- In the smart car 2.0 cycle, these core industry chains are facing major opportunities!
- The United States and Japan are developing new batteries. CATL faces challenges? How should China's new energy battery industry respond?
- Murata launches high-precision 6-axis inertial sensor for automobiles
- Ford patents pre-charge alarm to help save costs and respond to emergencies
- New real-time microcontroller system from Texas Instruments enables smarter processing in automotive and industrial applications
- [McQueen Trial] The fourth post is delayed - Try the Arduino IDE development environment & timer interrupt
- [Zero-knowledge ESP8266 tutorial] Quick Start 8-Reading analog values
- Invitation | Visit the Avnet Artificial Intelligence Cloud Exhibition, read useful information online, and win gifts!
- In this circuit, why does the PMOS turn on as soon as it is powered on?
- !!! Help "Does anyone know how to solder SIM900A on the perf board?"
- Watch Shuige's video for a reward | How to save oscilloscope data and pictures to a remote PC
- LOTO virtual oscilloscope software function demonstration - FIR digital filtering
- How to compile the image for SINA33 development board
- CalcToolBox 2 based on micropython
- DIY handheld computer with ESP32 and Raspberry Pi