1. Common errors in schematic diagrams:
(1) ERC report pin has no access signal:
a. Define I/O properties for pins when creating a package;
b. Inconsistent grid properties were modified when creating or placing components, and the pins and lines were not connected;
c. When creating a component, the pin direction is reversed and the non-pin name end must be connected.
(2) Components run out of the drawing: Components are not created in the center of the component library drawing paper.
(3) The created project file network list can only be partially loaded into the PCB: global was not selected when generating the netlist.
(4) When using a multi-part component that you created yourself, never use annotate.
2. Common errors in PCB:
(1) Report NODE not found when loading from the network:
a. The components in the schematic diagram use packages that are not in the PCB library;
b. The components in the schematic diagram use packages with inconsistent names in the PCB library;
c. The components in the schematic diagram use packages with inconsistent pin numbers in the PCB library. For example, for a transistor, the pin numbers in the sch are e, b, c, while in the PCB they are 1, 2, 3.
(2) Printing cannot always fit on one page:
a. The origin is not created when creating the PCB library;
b. After moving and rotating the components several times, there are hidden characters outside the PCB boundary. Select Show all hidden characters, shrink the PCB, and then move the characters within the boundary.
(3) The DRC reporting network is divided into several parts:
It means that the network is not connected. Look at the report file and select CONNECTED COPPER to search.
In addition, I would like to remind my friends to use WIN2000 as much as possible to reduce the chance of blue screen; export files several times and make new DDB files to reduce file size and the chance of PROTEL freezing. If you are doing a more complex design, try not to use automatic wiring.
In PCB design, wiring is an important step to complete product design. It can be said that all the previous preparations are done for it. In the entire PCB, the design process of wiring is the most demanding, with the most delicate skills and the largest workload. PCB wiring includes single-sided wiring, double-sided wiring and multi-layer wiring. There are also two ways of wiring: automatic wiring and interactive wiring. Before automatic wiring, interactive wiring can be used to pre-wire the lines with stricter requirements. The edge lines of the input and output terminals should avoid being adjacent and parallel to avoid reflection interference. Ground wire isolation should be added when necessary. The wiring of two adjacent layers should be perpendicular to each other. Parallel wiring is prone to parasitic coupling.
The routing rate of automatic routing depends on a good layout. The routing rules can be preset, including the number of bends, the number of vias, the number of steps, etc. Generally, exploratory routing is performed first to quickly connect short lines, and then maze routing is performed. The global routing path optimization is first performed on the lines to be routed. It can disconnect the routed lines as needed. And try to re-route to improve the overall effect.
The through hole is not suitable for the current high-density PCB design, which wastes many precious wiring channels. To solve this contradiction, blind and buried via technologies have emerged. They not only complete the role of the through hole, but also save many wiring channels to make the wiring process more convenient, smoother and more complete. The design process of the PCB board is a complex and simple process. In order to master it well, it requires the majority of electronic engineering designers to experience it themselves to get the true meaning.
1. Power supply and ground wire processing
Even if the wiring in the entire PCB board is completed well, the interference caused by the lack of consideration of the power supply and ground wires will reduce the performance of the product and sometimes even affect the success rate of the product. Therefore, the wiring of the power and ground wires should be taken seriously to minimize the noise interference generated by the power and ground wires to ensure the quality of the product.
Every engineer who designs electronic products knows the cause of noise between the ground wire and the power line. Now we will only explain how to reduce and suppress noise:
It is well known that decoupling capacitors are added between the power supply and the ground line.
Try to widen the width of the power and ground wires. It is best if the ground wire is wider than the power wire. The relationship between them is: ground wire > power wire > signal wire. Usually the signal wire width is: 0.2-0.3mm, the thinnest width can reach 0.05-0.07mm, and the power wire is 1.2-2.5 mm
For digital circuit PCB, wide ground conductors can be used to form a loop, that is, to form a ground network (analog circuit ground cannot be used in this way).
Use a large copper layer as a ground wire, and connect all unused areas on the printed circuit board to the ground as a ground wire. Or make a multi-layer board, with the power supply and ground wire occupying one layer each.
[page]
2 Common ground processing for digital circuits and analog circuits
Nowadays, many PCBs are no longer single-function circuits (digital or analog circuits), but are a mixture of digital and analog circuits. Therefore, when wiring, it is necessary to consider the interference between them, especially the noise interference on the ground line.
The frequency of digital circuits is high, and the sensitivity of analog circuits is strong. For signal lines, high-frequency signal lines should be kept as far away from sensitive analog circuit devices as possible. For ground lines, the entire PCB has only one node to the outside world, so the problem of digital and analog common ground must be handled inside the PCB. In fact, the digital ground and analog ground are separated inside the board. They are not connected to each other, but at the interface where the PCB is connected to the outside world (such as plugs, etc.). There is a short circuit between the digital ground and the analog ground. Please note that there is only one connection point. There are also cases where the ground is not shared on the PCB, which is determined by the system design.
3. Signal lines are laid on the electrical (ground) layer
When wiring a multi-layer printed circuit board, there are not many unfinished wires in the signal layer. Adding more layers will cause waste and increase the workload of production, and the cost will increase accordingly. To solve this contradiction, you can consider wiring on the power (ground) layer. First, consider using the power layer, and then the ground layer. Because it is best to preserve the integrity of the ground layer.
4 Treatment of connecting legs in large area conductors
In large-area grounding (electricity), the legs of common components are connected to it. The treatment of the connecting legs needs to be comprehensively considered. In terms of electrical performance, it is better for the pads of the component legs to be fully connected to the copper surface, but there are some hidden dangers in the welding and assembly of components, such as: ① Welding requires a high-power heater. ② It is easy to cause cold solder joints. Therefore, taking into account both electrical performance and process requirements, a cross-shaped pad is made, which is called heat shield, commonly known as thermal pad. In this way, the possibility of cold solder joints caused by excessive heat dissipation in the cross section during welding can be greatly reduced. The treatment of the legs of the power (ground) layer of the multilayer board is the same.
5 The role of network system in wiring
In many CAD systems, wiring is determined by the network system. If the grid is too dense, the number of paths will increase, but the step size will be too small, and the amount of data in the drawing field will be too large, which will inevitably place higher requirements on the storage space of the equipment and also have a great impact on the computing speed of computer-related electronic products. Some paths are invalid, such as those occupied by the pads of the component legs or by the mounting holes and fixed holes. If the grid is too sparse, too few paths will have a great impact on the wiring rate. Therefore, a grid system with reasonable density is required to support the wiring process.
The distance between the legs of a standard component is 0.1 inch (2.54 mm), so the basis of the grid system is generally set at 0.1 inch (2.54 mm) or an integer multiple of less than 0.1 inch, such as 0.05 inch, 0.025 inch, 0.02 inch, etc.
6 Design Rule Check (DRC)
After the wiring design is completed, it is necessary to carefully check whether the wiring design conforms to the rules set by the designer. At the same time, it is also necessary to confirm whether the rules set meet the requirements of the printed circuit board production process. The general inspection includes the following aspects:
Whether the distance between wires, wires and component pads, wires and through holes, component pads and through holes, and through holes and through holes is reasonable and meets production requirements.
Are the widths of the power and ground lines appropriate? Are the power and ground lines tightly coupled (low wave impedance)? Is there any place in the PCB where the ground line can be widened?
Have the best measures been taken for key signal lines, such as keeping them as short as possible, adding protection lines, and clearly separating input and output lines?
Do the analog circuit and digital circuit parts have their own independent ground lines?
Whether the graphics added to the PCB later (such as icons, annotations) will cause signal short circuit.
Modify some unsatisfactory line shapes.
Are there any process lines on the PCB? Does the solder mask meet the requirements of the production process? Is the solder mask size appropriate? Is the character logo pressed on the device pad to avoid affecting the quality of the electrical equipment?
Whether the outer frame edge of the power ground layer in the multi-layer board is reduced. If the copper foil of the power ground layer is exposed outside the board, it is easy to cause a short circuit.
Overview The purpose of this document is to explain the process and some precautions of using PADS's printed circuit board design software PowerPCB for printed circuit board design, to provide design specifications for designers in a working group, and to facilitate communication and mutual inspection between designers.
Previous article:TI Technical Analysis: Digital Interface Series Articles - SPI Bus
Next article:TI engineers help you: IEEE 802.15.4 chip protocol selection
Recommended ReadingLatest update time:2024-11-16 21:57
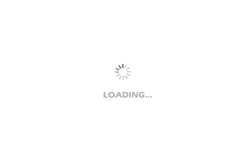
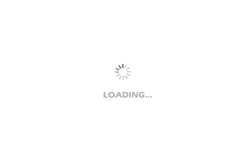
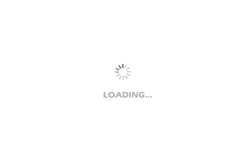
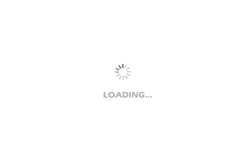
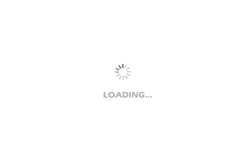
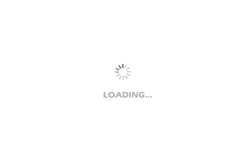
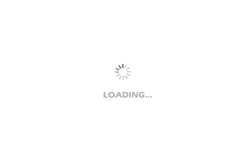
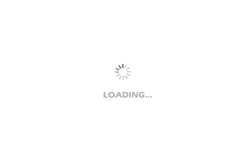
- MathWorks and NXP Collaborate to Launch Model-Based Design Toolbox for Battery Management Systems
- STMicroelectronics' advanced galvanically isolated gate driver STGAP3S provides flexible protection for IGBTs and SiC MOSFETs
- New diaphragm-free solid-state lithium battery technology is launched: the distance between the positive and negative electrodes is less than 0.000001 meters
- [“Source” Observe the Autumn Series] Application and testing of the next generation of semiconductor gallium oxide device photodetectors
- 采用自主设计封装,绝缘电阻显著提高!ROHM开发出更高电压xEV系统的SiC肖特基势垒二极管
- Will GaN replace SiC? PI's disruptive 1700V InnoMux2 is here to demonstrate
- From Isolation to the Third and a Half Generation: Understanding Naxinwei's Gate Driver IC in One Article
- The appeal of 48 V technology: importance, benefits and key factors in system-level applications
- Important breakthrough in recycling of used lithium-ion batteries
- Innolux's intelligent steer-by-wire solution makes cars smarter and safer
- 8051 MCU - Parity Check
- How to efficiently balance the sensitivity of tactile sensing interfaces
- What should I do if the servo motor shakes? What causes the servo motor to shake quickly?
- 【Brushless Motor】Analysis of three-phase BLDC motor and sharing of two popular development boards
- Midea Industrial Technology's subsidiaries Clou Electronics and Hekang New Energy jointly appeared at the Munich Battery Energy Storage Exhibition and Solar Energy Exhibition
- Guoxin Sichen | Application of ferroelectric memory PB85RS2MC in power battery management, with a capacity of 2M
- Analysis of common faults of frequency converter
- In a head-on competition with Qualcomm, what kind of cockpit products has Intel come up with?
- Dalian Rongke's all-vanadium liquid flow battery energy storage equipment industrialization project has entered the sprint stage before production
- Allegro MicroSystems Introduces Advanced Magnetic and Inductive Position Sensing Solutions at Electronica 2024
- Car key in the left hand, liveness detection radar in the right hand, UWB is imperative for cars!
- After a decade of rapid development, domestic CIS has entered the market
- Aegis Dagger Battery + Thor EM-i Super Hybrid, Geely New Energy has thrown out two "king bombs"
- A brief discussion on functional safety - fault, error, and failure
- In the smart car 2.0 cycle, these core industry chains are facing major opportunities!
- The United States and Japan are developing new batteries. CATL faces challenges? How should China's new energy battery industry respond?
- Murata launches high-precision 6-axis inertial sensor for automobiles
- Ford patents pre-charge alarm to help save costs and respond to emergencies
- New real-time microcontroller system from Texas Instruments enables smarter processing in automotive and industrial applications
- Digital EDA environment construction based on CentOS
- How to prevent bad phenomena of crystal oscillator
- How does a digital multimeter measure voltage, current, resistance, capacitance, diode, and transistor?
- Oscilloscope measuring the waveform of BYD Qin's three-phase drive motor
- C5000 compiles SUBC instruction to implement division
- Are you interested in CNC power supply?
- 122X32LCD screen printing CBG122032AL00 driver SED1520 screen data
- [Frequently Asked Questions about iMX6ULL Development] What are the requirements for the virtual machine when setting up the iMX6ULL development environment?
- Help with domestic chips that can replace stms105C6T6
- What is the function of this op amp circuit?