When designers think about passive components, they think about the production tolerances of inductors and capacitors, which are generally ± 20% or ± 10%. This is true in theory, but not in practice. This article introduces some of the parameters that capacitors and inductors are susceptible to and that system designers must know, and discusses how to select external components for the smallest but most efficient portable power system solution.
When designers think of passive components, they think of the manufacturing tolerances of inductors and capacitors, which are typically ±20% or ±10%. This is true in theory, but not in practice. Applying a DC bias voltage to a ceramic capacitor or a current to an inductor at a certain frequency changes the characteristics of these components, hence the term "active passives."
For example, a 10μF, 0603, 6.3V capacitor measures 4μF at -30°C with a DC bias of 1.8V. A 3.3 μH inductor measures 0.8 μH in a real-world application at 85°C.
In addition, component manufacturers are becoming more aggressive and are likely to continue to introduce some very good parts to remain competitive in the size-to-value war. This is similar to various real-life situations. For example, a car rated at 30 MPG (miles per gallon) by the EPA (U.S. Environmental Protection Agency) may only get 20 mpg in actual driving. This means that the owner must go to the gas station more often than expected.
This example can be extended to portable power systems. Every component used in each module of the system has a direct impact on system performance. Key performance indicators of portable power systems include battery life, solution size, and ease of use of system resources. For example, in a portable power system, charging the device too frequently will make the so-called "portable" meaningless.
System designers have already taken the first step in achieving these key performance indicators by selecting a switching regulator to power different system blocks. The next step is to ensure that the selected switching regulator operates at maximum efficiency. The key performance indicators of a switching regulator are efficiency, accuracy, and output voltage tolerance (including transient response, voltage ripple, solution size, etc.). To meet these performance indicators, the switch IC must work in harmony with external components.
The external components of a switching regulator generally include an inductor, an input capacitor, and an output capacitor. Just as the success of any game depends on the team's cooperation, the external components and switches must also work together and coordinate to meet the expected performance indicators of the DC-DC converter solution.
When designing a switching regulator, a series of compensations are optimized for the inductor value and the input and output capacitor values. The output current capability of the component also depends on many factors, one of which is the inductor value.
This article introduces some of the parameters that are easily affected by capacitors and inductors, discusses what system designers must know, and explains when to select external components for the smallest but most efficient solution for portable power systems.
Selecting capacitors
Let's look at ceramic capacitors first. This type of capacitor is ideal for portable applications due to its size, cost, and performance advantages. It is also very suitable for high-frequency applications due to its low equivalent series resistance (ESR) and equivalent impedance at the switching frequency. Low ESR minimizes output voltage ripple, and low impedance produces excellent filtering characteristics. However, the temperature coefficient of Y5V-type dielectric capacitors is very poor, and it may drop by 80% at 85°C. It is generally not recommended for portable applications, so this section focuses on X5R/X7R capacitors.
Figure 1 shows the history of case size changes for 10μF, 6.3V, X5R ceramic capacitors. The main benefit of a smaller case size is that it saves switch footprint and reduces the height of the overall solution. Currently, mainstream mobile phone manufacturers have a maximum height limit of 1.2mm for components used in their phones. As phone models become smaller, this limit will be further reduced. Today's ceramic capacitors are able to meet these requirements very well.
So, is there anything more that system designers need to know beyond ceramic capacitors? Absolutely! For example, the DC bias effect must be considered in addition to selecting the capacitance value of a ceramic capacitor and its case size. Incorrect capacitor selection can wreak havoc on system stability. DC bias effects are commonly seen in ferroelectric dielectric (Class 2) capacitors, such as X5R, X7R, and Y5V class capacitors.
The basic calculation formula for ceramic capacitors is as follows:
C = K × [(S × n) / t]
Here, C = capacitance, K = dielectric constant, n = number of dielectric layers, S = electrode area, t = dielectric layer thickness
Factors that affect DC bias are K, dielectric thickness, voltage rating scale factor, and grain size of the material. The electric field across the capacitor "polarizes" the internal molecular structure, causing a temporary change in the K constant, unfortunately, a decrease. The smaller the case size of the capacitor, the greater the percentage drop in capacitance due to DC bias. For a given case size, the greater the DC bias voltage, the greater the percentage drop in capacitance. System designers must be very cautious when substituting 0603 capacitors for 0805 capacitors to save space - unless the converter has been tested with the intended type of capacitor. The specification sheet recommends 0603 capacitors.
Figure 2 shows the effect of DC bias on several different capacitors over the ambient temperature range of a typical portable application. Looking at the DC bias characteristics in the figure, we can see that the capacitance of a 10μF, 6.3V 0603 capacitor from manufacturer A is 5.75μF at 1.8V DC bias and -30°C. Note the difference between capacitors and capacitance. Capacitance is the actual value of the capacitor from the application's perspective. The same capacitor from manufacturer C has a capacitance of 3.5μF under the same conditions. In fact, the 4.7μF capacitor from manufacturer A is almost as good as the 10μF capacitor from manufacturer C. [page]
Therefore, remember to ask the manufacturer for a curve of the capacitance value at the intended DC bias voltage of the application. For example, with a 2.5V output voltage, the system designer must look at the DC bias at 2.5V. The minimum capacitance value for best switch stability can be found in the switch's specification sheet. Differences between manufacturers must also be considered when dual sourcing capacitors for the portable power solution's bill of materials (BOM).
These decisions should not be left to the purchasing staff unless they can give good advice. Capacitor manufacturers often like to show separate curves, such as a curve of capacitance changing with temperature and another curve of capacitance changing with DC bias. However, they will not show both at the same time, but practical applications require both. You should remember to ask the manufacturer for a comprehensive curve for the most common voltages in the system.
For example, common voltages for baseband core microprocessors are 1.3 V, 1.5 V, and 1.8 V. I/O and hard disk drives use 1.8 V, 2.5 V, or 3.3 V. RF power amplifier supplies have output voltages ranging from 0.8 to 3.4 V.
When selecting the input capacitor, the input voltage range must be considered. For Li-Ion batteries, this range is 3 to 4.3V, and can be as high as 5.5V when plugged into a charger.
From a system perspective, the impedance/ESR vs. frequency curve is also important. A capacitor used for a 2MHz switch may not be suitable for a 5MHz switch. The resonant frequency of the capacitor is a key specification in switch design. When the switching frequency is close to the resonant frequency of the output capacitor, the output voltage ripple is minimized.
For example, the resonant frequency range of both 4.7μF and 10μF 0603 capacitors is 2 to 3MHz. However, the resonant frequency of the 1μF 0603 capacitor is around 6MHz, and that of the 1μF 0402 capacitor is nearly 10MHz. When the operating frequency is above the resonant frequency, the impedance is actually inductive. Without proper compensation, stability problems will occur and the ripple of the switch will increase. Last but not least, the production tolerances of ceramic capacitors are specified/tested at 1kHz frequency and 1Vrms or 0.5Vrms voltage, but the conditions of the actual application vary greatly. At lower rms voltages, the capacitor ratings are much smaller. For a typical switch, the ripple voltage range is 5 to 30mV.
When designers think about passive components, they think about the production tolerances of inductors and capacitors, which are generally ± 20% or ± 10%. This is true in theory, but not in practice. This article introduces some of the parameters that capacitors and inductors are susceptible to and that system designers must know, and discusses how to select external components for the smallest but most efficient portable power system solution.
Selecting an Inductor
When choosing an inductor for a portable power application, the three most important things to consider are size, size, and size again. Board real estate in mobile phones is at a premium, especially as features such as MP3 players, TVs, and videos are added to phones. The added functionality also increases the current draw from the battery. Therefore, modules that have traditionally been powered by linear regulators or connected directly to the battery require a more efficient solution. The first step toward a more efficient solution is to use a magnetic buck converter. As the name implies, an inductor is needed.
In addition to the size, the main specifications of the inductor are the inductance value at the switching frequency, the DC resistance (DCR) of the coil, the rated saturation current, the rated rms current, the AC resistance (ESR) and the Q factor. Depending on the application, the choice of inductor type - shielded or unshielded - is also very important.
Similar to the DC bias in capacitors, a 2.2μH inductor from manufacturer A may be completely different from one from manufacturer B. The relationship between inductance value and DC current over the relevant temperature range is a very important curve that must be obtained from the manufacturer. The rated saturation current (ISAT) can be found on this curve. ISAT is generally defined as the DC current at which the inductance value drops by 30% of the rated value. Some inductor manufacturers do not specify ISAT. They may only specify the DC current when the temperature is 40 ?C above the ambient temperature.
DCR causes conduction losses, affecting efficiency at higher output currents. ESR increases with operating frequency, affecting the dominant switching losses at lower output currents. ESR is proportional to the Q factor. A low ESR inductor will have a higher Q factor at the same frequency. Why should system designers consider ESR and Q factor when the inductor meets all other specifications?
When the switching frequency exceeds 2MHz, special attention must be paid to the AC loss of the inductor. The ISAT and DCR of inductors from different manufacturers listed in the specification sheet for comparison may have very different AC impedance at the switching frequency, resulting in significant efficiency differences at light loads. This is very important to improve the battery life in portable power systems because the system is in sleep, standby or low power mode most of the time.
Since inductor manufacturers rarely provide ESR and Q factor information, designers should actively ask them for it. The relationship between inductance and current given by the manufacturer is often limited to 25 ?C, so relevant data should be requested within the operating temperature range. The worst case is generally 85 ?C.
Figure 3 shows the relationship between the AC impedance and frequency of various inductors. Consider an example of a buck converter with the following specifications: FSW = 2MHz, VIN = 5.5V, L = 2.2 μH, VOUT = 1.5V, I = 0 to 600MA, ΔI = 289MA (calculated).
Referring to Figure 3, the DCR of a 2.2μH rated inductor at low frequency is 0.2Ω, and the ESR at 2MHz is 1Ω. The DC loss and AC loss caused by the inductor can be calculated using the following formula:
DC loss = I2 × DCR
AC loss = (dΔI2)/12×ESR
[page]
From the above formula, we can see that when the output current is high, low-frequency or DC losses dominate; when the output current is low, AC losses dominate. ΔI is the peak-to-peak ripple current of the converter, and its amplitude is the same when the output current is high and low in continuous conduction mode. From mathematical calculations, we can see that when I=600mA, 91% of the total inductor loss is DC loss; when I=50mA, 93% of the total inductor loss is AC loss.
Figures 4a (ESR) and 4b (Q) show the inductors of vendor A (low ESR, high Q) and vendor B (high ESR, low Q), and also show the efficiency curves of a 2MHz converter using these inductors (Figure 4c). Judging from these data, even though vendor A has a higher DCR, it can provide higher efficiency at light loads.
Depending on the application, you can choose between shielded or unshielded inductors. Generally speaking, shielded inductors are used in portable applications that must meet stringent EMI specifications.
Last but not least, there are two types of inductors based on how they are produced. The first is the traditional wire wound coil inductor and the other is the newer chip inductor. Chip inductors are becoming more and more popular due to their size and height advantages. Mounting speed during PCB assembly is also one of the advantages touted by chip (multilayer) inductor manufacturers. System designers must consider certain key specifications of chip inductors when selecting a switching solution. The relationship between inductance and DC current over temperature is a major parameter that differs significantly between coil inductors and chip inductors. Figure 5 shows a cross-sectional schematic of a wire wound coil inductor and a chip inductor.
As can be seen from Figure 6, in general, the inductance-DC current and temperature relationship curve of the coil inductor is very flat before the saturation current. After the saturation current, it drops sharply with the change of current. Typically, ISAT at 85 ?C is 10% to 20% lower than at 25 ?C.
At 25 °C, chip inductors have an initial inductance value that is higher than the rated value. Once the current increases, the chip inductance starts to decrease. Therefore, in most cases, the definition of rated ISAT does not apply to chip inductors. The rated rms current that specifies the temperature rise also determines the rated current of the chip inductor. Another characteristic of chip inductors is that the inductance value decreases with temperature, but not with DC current.
Regarding the actual inductor value, the system designer must carefully select the correct inductor and find the minimum inductance value according to the specification. Incorrect inductor selection can affect stability, cause sub-harmonic oscillations, and/or reduce the rated output current of the switch. As with ceramic capacitors, the designer should focus primarily on the inductance value in actual operating conditions rather than the rated inductance value.
How do you choose the current rating of an inductor for a magnetic buck converter? If the inductor is rated for IMS greater than the required output current, the easiest approach is to select an I SAT rating greater than or equal to the maximum current limit of the switch. However, as we saw with chip inductors, we must search for the minimum inductance value that meets the stability and output current requirements. Selecting a higher value chip inductor (such as 3.3 μH instead of 2.2 μH) to meet the inductance requirement is not feasible because the inductance drops more dramatically with higher values for the same case size.
In addition, there are various differences between chip inductor manufacturers. For example, manufacturer A may use low permeability materials to make the inductance value change gradually. However, this solution requires more dielectric layers. Therefore, A will have a higher DCR than manufacturer B, which uses high permeability materials and has a more dramatic drop-off, and B will have a lower DCR.
The purpose of this article is to provide some relevant information that can be used in actual situations, and also to introduce to system designers and component purchasing engineers the necessary data that should be requested from component manufacturers during the component selection process.
Previous article:Chip Inductors and Their Applications
Next article:Analysis of capacitor filtering problems in circuits
Recommended ReadingLatest update time:2024-11-16 20:48
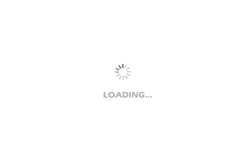
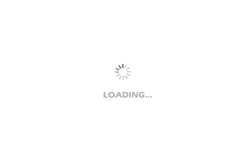
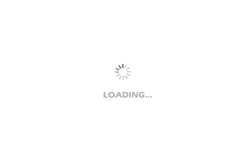
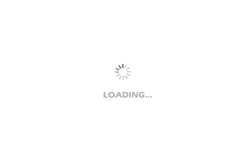
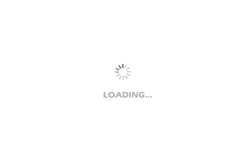
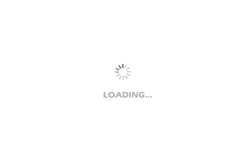
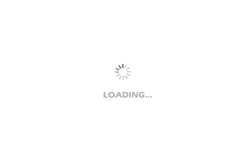
- MathWorks and NXP Collaborate to Launch Model-Based Design Toolbox for Battery Management Systems
- STMicroelectronics' advanced galvanically isolated gate driver STGAP3S provides flexible protection for IGBTs and SiC MOSFETs
- New diaphragm-free solid-state lithium battery technology is launched: the distance between the positive and negative electrodes is less than 0.000001 meters
- [“Source” Observe the Autumn Series] Application and testing of the next generation of semiconductor gallium oxide device photodetectors
- 采用自主设计封装,绝缘电阻显著提高!ROHM开发出更高电压xEV系统的SiC肖特基势垒二极管
- Will GaN replace SiC? PI's disruptive 1700V InnoMux2 is here to demonstrate
- From Isolation to the Third and a Half Generation: Understanding Naxinwei's Gate Driver IC in One Article
- The appeal of 48 V technology: importance, benefits and key factors in system-level applications
- Important breakthrough in recycling of used lithium-ion batteries
- Innolux's intelligent steer-by-wire solution makes cars smarter and safer
- 8051 MCU - Parity Check
- How to efficiently balance the sensitivity of tactile sensing interfaces
- What should I do if the servo motor shakes? What causes the servo motor to shake quickly?
- 【Brushless Motor】Analysis of three-phase BLDC motor and sharing of two popular development boards
- Midea Industrial Technology's subsidiaries Clou Electronics and Hekang New Energy jointly appeared at the Munich Battery Energy Storage Exhibition and Solar Energy Exhibition
- Guoxin Sichen | Application of ferroelectric memory PB85RS2MC in power battery management, with a capacity of 2M
- Analysis of common faults of frequency converter
- In a head-on competition with Qualcomm, what kind of cockpit products has Intel come up with?
- Dalian Rongke's all-vanadium liquid flow battery energy storage equipment industrialization project has entered the sprint stage before production
- Allegro MicroSystems Introduces Advanced Magnetic and Inductive Position Sensing Solutions at Electronica 2024
- Car key in the left hand, liveness detection radar in the right hand, UWB is imperative for cars!
- After a decade of rapid development, domestic CIS has entered the market
- Aegis Dagger Battery + Thor EM-i Super Hybrid, Geely New Energy has thrown out two "king bombs"
- A brief discussion on functional safety - fault, error, and failure
- In the smart car 2.0 cycle, these core industry chains are facing major opportunities!
- The United States and Japan are developing new batteries. CATL faces challenges? How should China's new energy battery industry respond?
- Murata launches high-precision 6-axis inertial sensor for automobiles
- Ford patents pre-charge alarm to help save costs and respond to emergencies
- New real-time microcontroller system from Texas Instruments enables smarter processing in automotive and industrial applications
- Timing diagram
- Can passive crystal oscillators of the same frequency be directly replaced? Is there anything I should pay attention to?
- LTC3108 Circuit Design
- EEWORLD University----STM32F7 online training (OLT)
- Share the issues that young electronic engineers are most concerned about. What are you concerned about?
- BK9521 wireless chip transmitter circuit
- EEWORLD University Hall----TI motor driver chip latest technical advantages and applications
- Open Source Hardware Badge Development Board
- 2021 National Electronic Design Competition Materials List
- 【ufun learning】Learning chapter 6: "Basic routine 5 - touch button control-PWM"